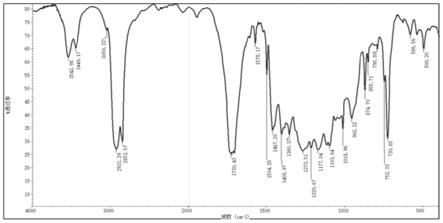
1.本发明涉及聚酯的化学再生技术领域,更具体的,涉及一种具有典型绿色低碳特点的闭环回收废旧聚酯制备再生聚酯的方法。
背景技术:
2.聚酯行业飞速发展的同时,废旧聚酯制品的处理问题接踵而来,社会中废弃聚酯制品的巨大存量不仅给生态环境带来了巨大的压力,同时造成了石化资源的严重浪费。因此,有大量的废旧聚酯需要被回收利用、再生利用。
3.对废旧聚酯的回收再利用方法主要分为两类:物理回收和化学回收。物理回收主要是利用聚酯的热塑性,将聚酯及其制品经过除杂、清洗、熔融再造粒,得到二次塑料或者纤维制品,虽然工艺简便,成本较低,但仅能实现聚酯的降级回收,且回收次数有限,达不到循环使用的目的。化学回收是指基于聚酯缩聚反应的可逆性及酯交换反应的亲核反应机理,通过小分子解聚剂对大分子链的进攻使聚酯解聚成聚合单体或中间体,经分离提纯后进行再聚合实现再生。将废弃聚酯通过化学回收的方法再生利用,能够有效利用资源、降低环境负荷。
4.现有的化学法回收利用废旧聚酯的方法中,主要有以下几方面的缺陷:(1)含有重金属类解聚催化剂的残留对于再生聚酯的性能有不利影响,如导致再生聚酯易分解、粘度低,且造成重金属含量超标;(2)废旧聚酯的解聚过程中温度高、解聚剂用量高,大多需要加压反应,解聚时间较长,反应装置的安全性要求高,能耗比较大,不符合当下绿色低碳的技术要求,同时易产生成分较复杂的副产物,影响解聚效率同时导致副产物处理的能耗及一系列环境影响;(3)再生聚酯难以应用于回收前相同或相似场景,即难以实现闭环回收,且目前化学回收后以pet以制备塑料瓶,纤维和织物为主,而工业化制备可降解塑料的回收很少有涉及,且目前可降解塑料的堆肥条件苛刻,在自然环境下难以完成有效的充分的降解,实现可降解材料的闭环循环回收是大势所趋。
5.中国专利申请cn107266664a公开了一种聚酯废料回收工艺,使用醋酸锌作为催化剂对pet废料进行解聚,但残留在解聚产物中的锌离子会因为其对羰基氧配位的催化机理会导致再聚合过程中热降解等副反应加速,使得分子量增长受限,再生聚酯的粘度低,品质差。中国专利申请cn102731310a公开了一种第一过渡系金属离子液体催化醇解pet的方法,但此类离子液体的催化剂中卤组元素含量很高,如果未能将催化剂从解聚产物中除去,则再聚合过程中会因为产生卤化氢而导致大分子的分解,严重影响再聚合制品的品质;并且该方法中催化剂添加量需要达到pet的10wt.%,醇解溶剂乙二醇的用量约为pet的4~10倍,催化剂和二元醇的用量大。
6.中国专利申请cn 104327260 a公开了一种生物可降解再生聚酯的制备方法,采用的解聚催化剂为可溶解于乙二醇的二元醇钛碱金属配位化合物,对废旧pet进行解聚,进而再共聚合得到再生聚酯。但一方面,该方法仅能回收废旧pet,而不涉及其他种类的废旧聚
酯,另一方面,该方法的醇溶解聚过程中解聚温度为160~240℃,解聚时间为0.5~5h,温度过高、时间过长,使得乙二醇极易环化脱水形成环化副产物,并且该方法的醇解剂用量大,过程复杂。
7.现有技术(孟辉.聚丁二酸丁二醇酯合成中工艺条件对酯化过程副产物四氢呋喃的影响[d].华东理工大学,2011.)报道了对于环化副产物的解决方案,例如通过通入氮气、降低反应温度等方法降低酯化过程中环化产物四氢呋喃的生成速率和产量。但对于解聚反应,在过低的反应温度、过短的反应时间下聚酯无法解聚。
[0008]
在绿色低碳循环的发展方针,以及国家碳达峰、碳中和的战略要求下,急需开发出一种典型绿色低碳特点的闭环回收废旧聚酯制备再生聚酯的方法。
技术实现要素:
[0009]
本发明为克服上述现有技术所述的废旧聚酯未闭环回收、副产物含量高的缺陷,提供一种绿色的闭环回收废旧聚酯制备再生聚酯的方法。
[0010]
为解决上述技术问题,本发明采用的技术方案是:
[0011]
一种具有典型绿色低碳特点的闭环回收废旧聚酯制备再生聚酯的方法,包括如下步骤:
[0012]
s1.废旧聚酯解聚:
[0013]
将废旧聚酯溶解于含有解聚催化剂和微波吸收剂的多元醇溶剂中,在常压、惰性气体氛围、微波条件下,进行解聚反应,得到解聚产物;
[0014]
所述解聚催化剂为钛酸纳米管、磷酸钛、二氧化钛、钛酸丁酯、乙二醇钛或丁二醇钛中的一种或几种;
[0015]
所述解聚反应的温度为150~170℃且温度波动≤2℃,解聚反应时间为6~35min;
[0016]
s2.解聚产物提纯:
[0017]
将步骤s1制得的解聚产物去除多元醇溶剂后,经过提纯去除副产物,得到解聚单体;
[0018]
s3.共酯化:
[0019]
将步骤s2制得的解聚单体,与二元酸、多元醇、聚合催化剂和扩链剂混合,在惰性气体氛围、微波条件下,进行聚合反应,得到酯化产物;
[0020]
s4.缩聚:
[0021]
将步骤s3的酯化物与催化剂和稳定剂混合,在抽真空的条件下进行缩聚反应,得到所述再生聚酯。
[0022]
本发明利用废旧聚酯解聚可合成一系列脂肪族-芳香族共聚酯作为再生聚酯,不仅有效实现了聚酯的化学回收,且该再生聚酯使用后可再次进行化学解聚、回收利用,实现闭环回收。
[0023]
在解聚过程中,本发明以钛酸纳米管、磷酸肽、二氧化钛、钛酸丁酯、乙二醇钛或丁二醇钛作为解聚催化剂,一方面其解聚效果优异,另一方面,该钛系催化剂对废旧聚酯进行解聚后,不需要进行分离,可直接作为再生聚酯共酯化的催化剂,且不会对制得的再生聚酯的性能造成不利影响。并且,本发明的催化体系不含可降解聚酯的限制元素,在再生聚酯的合成过程中把控原料,为后续的循环回收提供有力保障。
[0024]
发明人研究发现,废旧聚酯解聚反应在微波条件下进行,一方面微波能够使得待解聚的聚酯原料内外部同时受热,使得其受热均匀,解聚更彻底;另一方面,微波能够以极低的温度达到与传统加热方式同样的解聚效果,使得解聚反应可以高效、快速地进行,既保证了废旧聚酯的解聚程度,又极大地缩短了解聚时间、降低了反应温度,并减少了解聚过程中多元醇引起的环化产物的生成,提高了产率,减少了副产物处理对环境的污染。
[0025]
在步骤s1的解聚反应过程中,不仅要求解聚反应的温度范围满足150~170℃,还要求解聚反应温度恒定,即单次解聚反应的温度波动不超过
±
2℃。
[0026]
在温度恒定的情况下,能够减少副产物产生,同时保证极高的解聚率和反应效率。
[0027]
所述废旧聚酯为聚己二酸/对苯二甲酸丁二酯(pbat)、聚(癸二酸丁二醇-对苯二甲酸丁二醇)共聚酯(pbset)、聚对苯二甲酸乙二醇酯-1,4-环己烷二甲醇酯(petg)、聚对苯二甲酸乙二醇-1,4-环己烷二甲醇酯(pctg)、聚对苯二甲酸丁二酯(pbt)中或聚对苯二甲酸乙二酯(pet)中的一种或几种。
[0028]
所述废旧聚酯的来源可以为消费后回收塑料(post consumer recycled plastic,pcr)、工业回收塑料(post industry recycle plastic,pir)或海洋废塑料中的一种或几种。
[0029]
所述海洋废塑料可以为趋海塑料(oceanboundplastic,obp)和/或海洋内塑料(in-the-ocean plastics,iop)。
[0030]
所述废旧聚酯经除杂、清洗、破碎后可直接用于解聚。
[0031]
优选地,所述解聚催化剂为钛酸纳米管、磷酸钛或钛酸丁酯中的一种或几种。
[0032]
对于同样的废旧聚酯,使用钛酸纳米管、磷酸钛或钛酸丁酯作为解聚催化剂,解聚效率更优,解聚时间更短,从而进一步减少了环化产物的生成。
[0033]
优选地,所述解聚催化剂占废旧聚酯的0.05~0.15wt.%。
[0034]
优选地,步骤s1中所述废旧聚酯与多元醇的质量比为1:(0.6~3)。
[0035]
优选地,所述微波吸收剂为碳酸钠、氯化钠、活性炭或磷酸钠中一种或几种。
[0036]
更优选地,所述微波吸收剂为碳酸钠。
[0037]
优选地,步骤s1中所述微波吸收剂占废旧聚酯的0.01~1wt.%。
[0038]
发明人研究发现,碳酸钠既具有微波吸收作用,又具有一定的解聚催化作用。在使用碳酸钠作为微波吸收剂时,步骤s1的解聚效率得到进一步提升。
[0039]
优选地,步骤s1中所述微波条件为微波功率500~1000w,微波波长122mm。
[0040]
优选地,步骤s1中所述解聚反应的温度为155~165℃,时间为10~30min。
[0041]
更优选地,步骤s1中所述解聚反应的温度为160℃,时间为10min。
[0042]
在本技术的技术方案中,在微波条件下进行解聚反应的过程中,微波功率与解聚反应的温度并非直接对应的关系。
[0043]
优选地,步骤s2中所述去除多元醇溶剂为减压蒸馏和真空干燥。
[0044]
优选地,步骤s2中所述提纯为溶解重结晶过滤。
[0045]
步骤s3中所述聚合催化剂可以为聚酯类常用的聚合催化剂。
[0046]
优选地,步骤s3中所述聚合催化剂为钛酸丁酯、钛酸丙酯、钛磷化合物、钛硅化合物或钛酸乙酯中的一种或几种。
[0047]
优选地,步骤s1中所述多元醇溶剂和步骤s3中所述二元醇均为乙二醇、丙二醇、1,
4-丁二醇或戊二醇、丙三醇中一种或几种。
[0048]
优选地,步骤s3中所述二元酸为碳原子数为2~36的脂肪族二元酸。
[0049]
优选地,步骤s3中所述多元醇与二元酸的质量比为(0.2~1):1。
[0050]
优选地,步骤s1中所述多元醇溶剂和步骤s3中所述二元醇均为1,4丁二醇,步骤s3中所述二元酸为癸二酸和/或己二酸。
[0051]
使用生物质的1,4丁二醇、癸二酸作为原料进行共酯化时,制得的再生聚酯的生物质含量≥60%,充分实现了生物质和化学回收并举的绿色低碳循环理念。
[0052]
优选地,步骤s3中所述微波条件为500~1000w。
[0053]
优选地,步骤s3中所述聚合反应的温度为160~180℃,时间为30~90min。
[0054]
优选地,步骤s3中聚合催化剂占解聚单体、二元酸、二元醇和扩链剂质量之和的0.03~2wt.%。
[0055]
优选地,步骤s3中所述扩链剂为多元醇类扩链剂、异氰酸酯类扩链剂、酸酐类扩链剂或环氧化合物扩链剂中一种或几种。
[0056]
可选地,所述多元醇类扩链剂为乙二醇、丙三醇、季戊四醇、三羟甲基丙烷、木糖醇或山梨醇中的一种或几种。
[0057]
可选地,所述异氰酸酯类扩链剂为甲苯二异氰酸酯(tdi)、二苯基甲烷二异氰酸酯(mdi)、六亚甲基二异氰酸酯(hdi)或异氟尔酮二异氰酸酯中一种或几种。
[0058]
可选地,所述环氧化合物扩链剂可以为adr扩链剂。
[0059]
优选地,步骤s4中所述催化剂与步骤s3所述聚合催化剂一致。
[0060]
优选地,步骤s4中所述稳定剂为有机亚磷酸酯类稳定剂、磷酸酯类稳定剂、受阻酚类稳定剂中的一种或几种。
[0061]
可选地,所述有机亚磷酸酯类稳定剂可以为亚磷酸三甲酯、亚磷酸三乙酯或亚磷酸三苯酯中的一种或几种。
[0062]
可选地,所述磷酸酯类稳定剂可以为磷酸三苯酯、磷酸三甲酯或磷酸三乙酯中的一种或几种。
[0063]
可选地,所述受阻酚类稳定剂可以为3,5-二叔丁基-4-羟基苄基二乙基膦酸酯(抗氧剂1222)和/或抗氧剂1010。
[0064]
优选地,所述缩聚反应的温度为230~250℃,时间为3~5h,压力为20~100pa。
[0065]
与现有技术相比,本发明的有益效果是:
[0066]
本发明利用废旧聚酯解聚、再聚合,合成的再生聚酯仍是全生物降解聚酯,不仅有效实现了聚酯的化学回收,且该再生聚酯使用后可再次进行化学解聚、回收利用,实现闭环回收。
[0067]
在解聚过程中,本发明以特定的钛系催化剂作为解聚催化剂,在微波吸收剂的存在下,以较低温度、较短的时间对废旧聚酯进行解聚,且二元醇溶剂用量小,催化剂添加量低。获得了极高的解聚效率,同时副产物产率低,解聚催化剂不需要进行分离,可直接进行下一步骤的酯化,也不会对制得的再生聚酯的性能造成不利影响,有效实现了绿色化学回收。
[0068]
当使用生物质的1,4-丁二醇、癸二酸作为原料进行共酯化时,制得的再生聚酯的生物质含量≥60%,实现了生物质和化学回收并举的技术路线。根据生命周期评估(lca)的
测算结果,由于引入了生物质原料和废旧聚酯作为原料,相对现有化学回收路线的碳排放降低幅度超过60%以上,充分体现了技术路线和产品的低碳特征。
[0069]
来自于海洋垃圾的废旧pet瓶由于在自然环境中受到光、热、海水冲刷,生物和微生物附着等多方面因素的影响,出现了明显了性能劣化,其外观呈现为脆化,透明度下降等特征,其实质是聚酯降解后导致分子量下降,特性粘数降低。这些降解产物进入海洋后成为微塑料,由于大部分海洋废旧pet性能下降明显,打捞收集后常规的物理回收只能降级回收或者能量回收,不能有效体现资源回收再充分利用的原则。本发明不但可以通过回收海洋垃圾实现保护环境和降低微塑料污染的目的,而且还能将收集的废旧pet作为资源进行化学回收转化为高值次级产物充分利用,实现了环境保护和资源高质循环的双重目的。
附图说明
[0070]
图1为实施例1的解聚反应馏分和聚合反应馏分、对比例7的解聚反应馏分、四氢呋喃标准溶液的红外光谱图。
[0071]
图2为实施例1制得的解聚单体的红外光谱图。
[0072]
图3为实施例1制得的再生聚酯的红外光谱图。
[0073]
图4为实施例1制得的再生聚酯的核磁氢谱。
具体实施方式
[0074]
下面结合具体实施方式对本发明作进一步的说明。
[0075]
实施例及对比例中的原料均可通过市售得到;
[0076]
废旧聚酯:
[0077]
pet粒子,来自polindo pt;海洋废旧pet瓶片(特性粘度《0.5dl/g,重均分子量《16000g/mol),来自蓝丝带海洋保护协会;pctg,petg,来自广州市锐胜塑料有限公司;pbat、pbset,来自珠海万通化工限公司。
[0078]
解聚催化剂:
[0079]
钛酸纳米管,购自先丰纳米;磷酸钛,购自威海天创精细化工有限公司;钛酸丁酯,购自阿拉丁;醋酸锌,购自阿拉丁。
[0080]
微波吸收剂:
[0081]
碳酸钠,氯化钠购自麦克林;活性碳粉,市售,分析纯,平均粒径30μm,碳化硅,购自麦克林。
[0082]
稳定剂:
[0083]
亚磷酸三甲酯,磷酸三苯酯,购自阿拉丁。
[0084]
二元醇中:1,4-丁二醇(bdo),为生物基bdo,购自山东兰典生物科技股份有限公司;
[0085]
二元酸中:葵二酸,购自济南博奥化工有限公司。
[0086]
除非特别说明,本发明采用的试剂、方法和设备为本技术领域常规试剂、方法和设备。
[0087]
实施例1~5
[0088]
实施例1~5分别提供一种对废旧聚酯的闭环回收制备再生聚酯的方法,包括如下
步骤,具体的原料及反应条件见表1:
[0089]
s1.废旧聚酯解聚:
[0090]
将平均粒径≤2mm的废旧聚酯溶解于含有解聚催化剂和微波吸收剂的二元醇溶剂中,放置于500ml的玻璃反应釜中,再转移到微波化学合成仪(型号anks-sr8,青岛艾尼克斯微波自动化设备有限公司)中,在氮气氛围中、微波条件下,进行解聚反应,得到解聚产物;
[0091]
s2.解聚产物提纯:
[0092]
将步骤s1制得的解聚产物经减压蒸馏去除二元醇等溶剂后,经过提纯得到解聚单体;
[0093]
s3.共酯化:
[0094]
将步骤s2制得的解聚单体,与二元酸、二元醇、聚合催化剂和扩链剂混合,在惰性气体氛围、微波条件下,进行聚合反应,得到酯化产物;
[0095]
s4.缩聚:
[0096]
将步骤s3的酯化产物加入稳定剂和催化剂,在抽真空的条件下进行缩聚反应,得到所述再生聚酯。
[0097]
表1实施例1~5的原料及反应条件
[0098][0099][0100]
实施例6~10
[0101]
实施例6~10提供一种对废旧聚酯的闭环回收制备可生物降解聚酯的方法,除了
步骤s1中的解聚条件外,其他步骤同实施例1;
[0102]
实施例6的步骤s1中,解聚条件为温度恒定为150
±
2℃,时间35min;
[0103]
实施例7的步骤s1中,解聚条件为温度恒定为155
±
2℃,时间30min;
[0104]
实施例8的步骤s1中,解聚条件为温度恒定为165
±
2℃,时间10min;
[0105]
实施例9的步骤s1中,解聚条件为温度恒定为170
±
2℃,时间8min。
[0106]
实施例10的步骤s1中,解聚条件为温度恒定为160
±
1℃,时间10min。
[0107]
对比例1~6
[0108]
对比例1~6提供一种对废旧pet和petg共混物的闭环回收制备可生物降解聚酯的方法,步骤同实施例1,具体原料及反应条件如表2。
[0109]
表2对比例1~3的原料及反应条件
[0110]
[0111][0112]
对比例4~6
[0113]
对比例4~6提供一种对废旧pet和petg共混物的闭环回收制备可生物降解聚酯的方法,除了步骤s1中的解聚条件外,其他步骤、原料及反应条件同实施例1;
[0114]
对比例4的步骤s1中,解聚条件为温度恒定为140
±
2℃,时间90min;
[0115]
实施例5的步骤s1中,解聚条件为温度恒定为190
±
2℃,时间10min;
[0116]
实施例6的步骤s1中,解聚条件为温度160℃,波动范围为
±
5℃,时间10min。
[0117]
对比例7
[0118]
对比例7提供一种对废旧pet和petg共混物的闭环回收制备可生物降解聚酯的方法,步骤与中国专利申请cn 104327260 a实施例1相近,具体如下:
[0119]
s1.制备醇解催化剂丁二醇钛酸锂,包括以下步骤:
[0120]
a)将钛酸四乙酯在50℃和氮气保护条件下,与丁二醇均匀混合,钛酸四乙酯酯与丁二醇的摩尔比为1:100;b)加入氢氧化锂,氢氧化锂与钛酸四乙酯的摩尔比为2.05:1,持续搅拌至反应体系为均一透明的液体后,升高反应温度至180℃;c)反应过程中,回流丁二醇并排除反应生成的低沸点的乙醇和水,反应时间3小时,反应结束后在温度为190℃下,反应体系压力为0.5atm下,0.5min中内将体系内的丁二醇蒸发完全,将体系内的二元醇蒸发完全获得白色固体,对此固体利用乙醇-氯仿重结晶三次得到无色晶体,即制得丁二醇钛酸锂;
[0121]
s2.将以上制得的醇解催化剂丁二醇钛酸锂溶解于解聚剂丁二醇中,丁二醇钛酸锂的用量为丁二醇质量的1%,形成解聚溶液;
[0122]
s3.将解聚溶液与废旧pet粒子和petg共混物混合,并进行在惰性气体保护下的解聚反应,同时搅拌,搅拌速率为1500转/min,解聚剂丁二醇用量与pet和petg共混物的摩尔比为20:1,解聚反应温度为190℃,反应体系压力为1atm,反应时间为3h;
[0123]
s4.所得溶液中加入含有活性炭质量分数为0.5%的丁二醇分散液,活性炭丁二醇
分散液的加入量为解聚溶液质量的1.5倍,在温度为150℃下,常压回流搅拌脱色5h后,经过滤去除杂质及脱色用的活性炭,脱色及过滤过程反复进行2次;
[0124]
s5.将除杂脱色后的解聚物的丁二醇溶液在温度为190℃且压力为0.5atm条件下,将溶液中的丁二醇蒸发完全,获得提纯及脱色后的解聚产物;
[0125]
s6.己二酸一缩二丁二醇酯化物的制备:将1,6-己二酸,丁二醇,聚丁二醇4000三者以等物质量混合,并加入100ppm的丁二醇钛酸锂为催化剂,在反应温度为170℃,压力为1atm下进行酯化4h,同时及时馏出反应过程中生成的水,反应过程中以惰性气体进行保护,反应结束后获得己二酸一缩二丁二醇酯化物的制备;
[0126]
s7.按质量比为8:2混合步骤s5和步骤s6获得的产物,并加入100ppm丁二醇钛酸锂作为缩聚催化剂和50ppm磷酸三甲酯热稳定剂,并在220℃,压力1atm,惰性气体保护条件下搅拌混合;然后,将反应温度升高至250℃,继续反应120min,同时在此段时间,使体系内压力匀速降低至1kpa;然后,将反应温度升高至265℃,使体系内压力降低至20pa后,继续反应180min,即获得再生聚酯。
[0127]
性能测试
[0128]
对上述实施例及对比例制得的解聚产物和再生聚酯进行性能测试,具体方法如下:
[0129]
解聚单体和再生聚酯的定性:对解聚单体和再生聚酯分别进行红外光谱检测,测试条件为测定方法:透射、参比样品:kbr、检测器:dtgs、波数范围:400~4000cm-1
、分辨率:4cm-1
、扫描次数:32。
[0130]
四氢呋喃(thf)产率:蒸出的馏分称重,采用红外进行定性,用气相色谱-氢火焰检测器分析其中四氢呋喃和其它副产物的量;标样乙二醇、四氢呋喃、1,4-丁二醇、异丙醇为分析纯;色谱柱为美国agilent公司hp-ffap气相毛细管柱30m*0.32mm*0.25μm,以异丙醇为内标;进样器温度250℃,检测器温度300℃,载气为n2,流速30ml/min,h2流速30ml/min:空气流速300ml/min,进样0.5μl。
[0131]
pet解聚率=(1-未反应的废旧聚酯细颗粒重量/废旧聚酯投料量)*100%。
[0132]
再生聚酯的产率:再生聚酯产率=产物的实际重量/理论重量*100%。
[0133]
采用双冷凝系统收集对实施例1的解聚反应馏分、聚合反应馏分和对比例7的解聚反应馏分进行红外光谱测试,谱图见图1。可以看出,实施例1中解聚反应馏分主要是水和乙二醇、聚合反应馏分主要是水和丁二醇,而对比例7中的解聚反应馏分与四氢呋喃标准溶液相比,thf的特征峰非常明显,这表示其反应得到了较多thf副产物。
[0134]
对实施例1制得的解聚单体进行红外光谱测试,根据图2的红外光谱图可以确认,实施例1得到的解聚单体为聚对苯二甲酸丁二醇低聚物(bhbt)。
[0135]
对实施例1制得的再生聚酯进行红外光谱测试,根据图3的红外光谱图,在1730cm-1
处出现的羰基(-c=o)伸缩振动吸收峰,归属于pbset共聚酯中酯键上的羰基;1120cm-1
、1177cm-1
处为醚键(c-o-c)伸缩振动吸收峰。在3050cm-1
处出现的(-c-h)基团的伸缩振动与面外弯曲振动吸收峰,归属于苯环上的(-c-h)基团;图中1578cm-1
处新出现的吸收峰为苯环骨架的伸缩振动峰,752cm-1
处的强吸收峰是靠近苯环的c-h伸缩振动吸收峰,1467cm-1
处的吸收峰为pbset共聚酯中-ch
2-ch
2-的面内弯曲振动吸收峰;在2931cm-1
和1408cm-1
、1360cm-1
处分别为pbset共聚酯分子链上亚甲基(-ch
2-)的伸缩振动吸收峰和面内弯曲振动峰;在
3400~3630cm-1
处为分子间缔合的羟基(-oh)的伸缩振动吸收峰,归属于pbset共聚酯中的端羟基。可以确认,实施例1制得的再生聚酯为pbset。
[0136]
各实施例及对比例的测试结果见表3。
[0137]
表3实施例1~10及对比例1~4的测试结果
[0138][0139][0140][0141]
根据上表的测试结果可以看出,采用本发明的方法可以有效闭环回收废旧聚酯,解聚温度低、时间短、解聚效率高,且获得解聚单体产率高、副产物含量极低。
[0142]
而对比例1与实施例1相比,解聚过程中未使用微波,在相同的解聚温度和时间下解聚效率极低,几乎未解聚。对比例2仍未使用微波解聚,但提高了反应温度、延长了反应时间,虽然一定程度提高了解聚效率,但也使得解聚过程中产生了大量环化副产物,thf产率为5%。对比例3中,虽然在解聚过程中使用了微波条件,但由于解聚催化剂为醋酸锌,解聚效率差,且锌残留在反应体系内影响了再生聚酯的特性粘度,最终制得的再生聚酯产率为84%,特性粘度为1.251dl.g-1
。对比例4虽然在解聚过程中采用了微波条件,由于温度太低,导致解聚效率低,难以在短时间是废旧聚酯醇解。对比例5中,解聚温度为190
±
2℃,温度过高,使得thf产率达到4.2%。对比例6中解聚温度不恒定,波动高达5℃,使得废旧聚酯解聚率和再生聚酯的产率都较低。对比例7为模拟现有技术的方法制备再生聚酯,可以看出,使用该方法得到的副产物含量较高,thf产率达到7%,且再生聚酯的产率仅为83%。
[0143]
显然,本发明的上述实施例仅仅是为清楚地说明本发明所作的举例,而并非是对本发明的实施方式的限定。对于所属领域的普通技术人员来说,在上述说明的基础上还可
以做出其它不同形式的变化或变动。这里无需也无法对所有的实施方式予以穷举。凡在本发明的精神和原则之内所作的任何修改、等同替换和改进等,均应包含在本发明权利要求的保护范围之内。