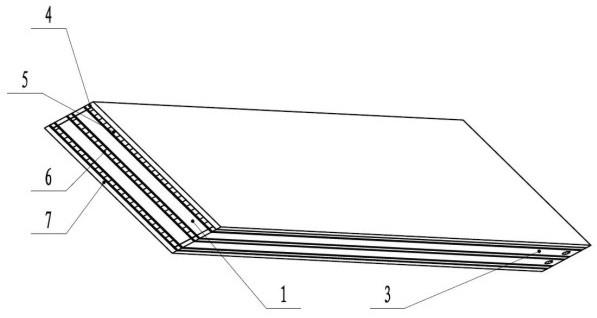
1.本实用新型涉及一种产氢装置。
背景技术:
2.在能源短缺和环境恶化两大困境的威胁下,可持续清洁能源的开发日益迫切,目前可替代的新能源包括可再生电力、生物质和氢能等,氢能源作为一种清洁能源,其主要优势在于,储量大、污染小、效率高、可持续发展等,因此氢能被认为是最理想的新能源,也是最有希望成为能源的终极解决方案。氢能源产业在用能方面以燃料电池为代表,氢燃料电池的能源效率高,安全性好,使用寿命长,产生的水清洁,越来越受到政府相关部门和行业的重视,目前急需一种能满足氢气燃料电池系统使用要求的产氢装置。
技术实现要素:
3.本实用新型的发明目的在于提供一种产氢装置,使得储氢有机液体中的氢气能安全、稳定、高效的分离出来,并方便的收集使用。
4.本实用新型采用的技术方案是:包括上/下两侧板、位于两侧板之间的由水平设置的隔板由下至上依次分隔成的2n+1层通道;其中,n>1;最上层通道及最下层通道为高温气体通道,相邻两层高温气体通道之间为储氢液体通道;储氢液体通道、高温气体通道交错堆叠排列;高温气体通道两侧设有气体通道封条;气体通道封条之间的高温气体通道由多个依次平行设置的气体通道导流分隔片分隔为多个气体小流道;液体通道入/出口设有液体导流封条;液体通道两侧设有液体通道封条;液体通道封条之间的液体通道由多个依次平行设置的液体通道导流分隔片分隔为多个液体小流道,其通道中液体流动方向与高温气体通道中气体的流动方向相反;其中一个液体通道封条上开有与液体通道连通的储氢液体入口孔,另一个液体通道封条上开有与液体通道连通的氢气出口孔。
5.所述液体通道导流分隔片、气体通道导流分隔片均为不锈钢制或铜质长条薄片。
6.所述液体通道导流分隔片、气体通道导流分隔片的厚度为0.10mm~0.20mm。
7.所述液体通道导流分隔片高度为9.5 mm~12.5mm,所述气体通道导流分隔片高度为3.5 mm~6.5mm。
8.所述n=2;两侧板之间有五层通道,包括三层高温气体通道和两层液体通道;各液体通道设置于相邻两高温气体通道之间。所述高温气体通道与液体通道流体流动方向为逆向流动。
9.所述液体通道封条、液体导流封条、气体通道封条、隔板、侧板均为不锈钢材质。
10.所述液体通道封条、液体通道导流分隔片、液体导流封条、高温气体通道封条、高温气体通道导流分隔片、隔板、侧板经高温真空钎焊而成。
11.所述高温气体通道导流分隔片按流体流动方向放置满整个高温气体通道空间,液体通道中液体通过液体通道封条端部的储氢液体入口孔进入液体通道,然后经液体通道导流分隔片与高温气体逆向流动,从另一侧液体通道封条端部的氢气出口孔排出。
12.本实用新型通过高温气体为储氢有机液体供热,将储氢有机液体中的氢气释放出来,产生氢气用于回烧和氢气燃料电池系统。其中高温气体通道介质为高温气体,液体通道介质为储氢有机液体,液体从液体通道封条端部的进口孔进入液体通道,然后经液体通道导流分隔片与高温气体逆向流动,从另一侧液体导流封条端部的出口孔流出,冷热流体通过逆流形式高效换热,将高温气体热量传递给储氢有机液体,释放出储氢有机液体中的氢气,满足氢气燃料电池系统的使用要求。
附图说明
13.图1是本实用新型的结构示意图。
14.图2是本实用新型面向高温气体通道方向示意图。
15.图3是本实用新型高温气体通道结构示意图。
16.图4是本实用新型面向液体通道方向示意图。
17.图5是本实用新型液体通道结构示意图。
18.图中,液体导流封条1,液体通道导流分隔片2,液体通道封条3,高温气体通道封条4,高温气体导流分隔片5,隔板6,侧板7,储氢液体入口孔8,氢气出口孔9。
具体实施方式
19.如图1所示,一种板翅式换热器芯体结构由液体通道和高温气体通道依次累积堆叠后,经高温真空钎焊而成。隔板6从下至上依次将位于两侧板7之间空间分隔成五层通道,最上层通道及最下层通道为高温气体通道,相邻两层高温气体通道之间为液体通道,最上层的高温气体通道和紧邻的下层液体通道呈逆向流动的型式。在高温气体通道侧,每层通道两边各放置一件高温气体通道封条4,在两封条之间放置高温气体导流分隔片5;在液体通道侧,液体通道四周放置有两件液体通道封条3、两件液体导流封条1,液体导流封条1之间的通道放置液体通道导流分隔片2,其通道中液体流动方向与高温气体通道中气体的流动方向相反。侧板7位于最外层通道上、下两侧,靠近侧板7的通道为高温气体通道。
20.图2、3中,每层高温气体通道两侧放置高温气体通道封条4各一件,两高温气体通道封条4中间流道部分放置高温气体通道导流分隔片5。
21.图4、5中,每层液体通道四周放置有两件液体通道封条3、两件液体导流封条1,液体导流封条1之间的通道放置液体通道导流分隔片2。其中一个液体通道封条3上开有与液体通道连通3的储氢液体入口孔8,另一个液体通道封条3上开有与液体通道连通的氢气出口孔9。
22.装配时,最底层放置侧板7,侧板7上层为高温气体通道,高温气体通道封条4、高温气体通道导流分隔片5的布置方式如图3所示;高温气体通道与液体通道之间放置一隔板6,隔板6上侧布置液体通道,其中液体通道封条3、液体通道导流分隔片2、液体导流封条1的布置方式如图5所示。液体通道上再放置另一隔板6,在隔板6上再布置高温气体通道。依次热、液体通道交替布置,直至放置完成所需要的层数后,在最上层的高温气体通道上放置侧板7,放置完毕后,用专用夹具压紧固定推入高温真空钎焊炉进行高温真空钎焊。本实用新型通过氢气催化燃烧技术为储氢有机液体供热,将储氢有机液体中的氢气释放出来,产生氢气用于回烧和氢气燃料电池系统。其中高温气体通道介质为高温气体,液体通道介质为储
氢有机液体,冷、热流体通过逆向流动形式,将高温气体热量传递给有机液体,释放出有机液体中的氢气,满足氢气燃料电池系统的使用要求。
技术特征:
1.一种产氢装置,其特征在于:包括上/下两侧板、位于两侧板之间的由水平设置的隔板由下至上依次分隔成的2n+1层通道;其中,n>1;最上层通道及最下层通道为高温气体通道,相邻两层高温气体通道之间为储氢液体通道;储氢液体通道、高温气体通道交错堆叠排列;高温气体通道两侧设有气体通道封条;气体通道封条之间的高温气体通道由多个依次平行设置的气体通道导流分隔片分隔为多个气体小流道;液体通道入/出口设有液体导流封条;液体通道两侧设有液体通道封条;液体通道封条之间的液体通道由多个依次平行设置的液体通道导流分隔片分隔为多个液体小流道,其通道中液体流动方向与高温气体通道中气体的流动方向相反;其中一个液体通道封条上开有与液体通道连通的储氢液体入口孔,另一个液体通道封条上开有与液体通道连通的氢气出口孔。2.根据权利要求1所述的一种板翅式换热器芯体结构,其特征在于:所述液体通道导流分隔片、气体通道导流分隔片均为不锈钢制或铜质长条薄片。3.根据权利要求2所述的一种板翅式换热器芯体结构,其特征在于:所述液体通道导流分隔片、气体通道导流分隔片的厚度为0.10mm~0.20mm。4.根据权利要求2所述的一种板翅式换热器芯体结构,其特征在于:所述液体通道导流分隔片高度为9.5 mm~12.5mm,所述气体通道导流分隔片高度为3.5 mm~6.5mm。5.根据权利要求1所述的一种不锈钢板翅式换热器芯体,其特征在于:所述n=2;两侧板之间有五层通道,包括三层高温气体通道和两层液体通道;各液体通道设置于相邻两高温气体通道之间。6.根据权利要求1所述的一种板翅式换热器芯体结构,其特征在于:所述液体通道封条、液体导流封条、气体通道封条、隔板、侧板均为不锈钢材质。
技术总结
一种产氢装置,包括上/下两侧板、位于两侧板之间的由水平设置的隔板由下至上依次分隔成的2n+1层通道;最上层及最下层通道为高温气体通道,相邻两层高温气体通道之间为储氢液体通道;储氢液体通道、高温气体通道交错堆叠排列;高温气体通道两侧设有气体通道封条;高温气体通道分隔为多个气体小流道;液体通道入/出口设有液体导流封条;液体通道两侧设有液体通道封条;液体通道分隔为多个液体小流道;其中一个液体通道封条上开有与液体通道连通的储氢液体入口孔,另一个液体通道封条上开有与液体通道连通的液体氢气出口孔。本实用新型通过高温气体为储氢有机液体供热,将储氢有机液体中的氢气释放出来,满足氢气燃料电池系统的使用要求。使用要求。使用要求。
技术研发人员:王学德 罗永明 马毅 云翔雨 周卓亚
受保护的技术使用者:襄阳航力机电技术发展有限公司
技术研发日:2021.09.16
技术公布日:2022/2/7