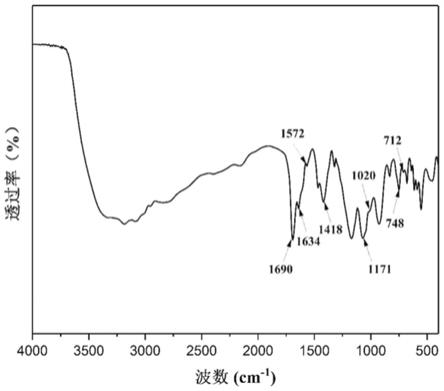
1.本发明涉及瓦斯或燃气阻火隔爆技术领域,具体涉及一种生物基阻火隔爆材料及其制备方法。
背景技术:
2.随着社会的快速发展,能源的需求量日益上涨,石油、天然气等能源在日常生活和工业生产中占据着重要地位,但其输送和使用过程中引发的燃烧爆炸事故近年来时有发生,因此针对燃气和可燃性粉尘的储运开展新型阻火隔爆材料的研究成为防治易燃易爆事故的重要手段。
3.阻火隔爆材料通常是填充于管道、罐体或阻爆装置内部,对爆炸冲击波和火焰的传播与发展起到抑制作用。多孔材料内部是由丝网编结而成的复杂孔道结构,火焰通过这些复杂孔道时会被撕裂成无数小的火焰团,导致火焰锋面不再连续,在湍流的扰动下,会因失去热平衡而熄灭,无数火焰团的熄灭会最终导致整个火焰锋面的熄灭,遏制火焰的传播,使爆炸冲击波衰减。
4.传统多孔阻火隔爆材料主要以网状铝合金、网状聚氨酯、泡沫陶瓷和硅酸铝棉材料为主,按照材料材质的不同可分为金属和非金属多孔材料。然而,金属材料成本高、易氧化,氧化后性能明显下降;非金属材料存在易燃、易产生静电、熔融物易黏附设备内壁和力学性能差等缺陷,以上问题极大地限制了多孔材料阻火隔爆的实际应用。
5.丝瓜络作为天然生物质材料,其具有质量轻、韧性强、绿色环保等特点,目前研究主要针对其药用价值和吸附能力;丝瓜络内部为纤维缠结而成的三维网状结构,可在爆炸中发挥火焰淬熄和吸波减振的作用,其中央骨架构成的孔道结构可使燃气有效通过,降低其阻塞率,因此对于阻火隔爆领域具有重要价值。但如何以丝瓜络为原料制得阻燃性能优异的生物基阻火隔爆材料是现有技术的难题。
技术实现要素:
6.本发明的目的在于克服上述技术不足,提供一种生物基阻火隔爆材料及其制备方法,解决现有技术中如何以丝瓜络为原料制得阻燃性能优异的生物基阻火隔爆材料的技术问题。
7.为达到上述技术目的,本发明的技术方案提供一种生物基阻火隔爆材料,由丝瓜络和阻燃剂混合制得;所述阻燃剂按照重量份数计算,包括山梨醇1-3份、水60-110份、氨基三亚甲基膦酸20-40份和烟酰胺10-20份。
8.此外,本发明还提出一种上述生物基阻火隔爆材料的制备方法,包括以下步骤:
9.s1、按照各组分配比,将山梨醇和水混合,之后加入氨基三亚甲基膦酸在100-130℃下反应,之后在100-130℃下继续加入烟酰胺反应得到阻燃剂;
10.s2、将丝瓜络浸泡于所述阻燃剂中得到所述生物基阻火隔爆材料。
11.进一步地,在步骤s1中,所述山梨醇和所述水混合的时间为5-10min。
12.进一步地,在步骤s1中,加入所述氨基三亚甲基膦酸在100-130℃下反应的时间为2-3h。
13.进一步地,在步骤s1中,在100-130℃下继续加入所述烟酰胺反应的时间为1-2h。
14.进一步地,在步骤s2中,将所述丝瓜络浸泡于所述阻燃剂中两次得到所述生物基阻火隔爆材料。
15.进一步地,在步骤s2中,将所述丝瓜络浸泡于所述阻燃剂中两次包括:将所述丝瓜络第一次浸泡于所述阻燃剂,之后进行第一次干燥,将干燥后的丝瓜络第二次浸泡于所述阻燃剂中,之后再次干燥得到所述生物基阻火隔爆材料。
16.进一步地,在步骤s2中,将所述丝瓜络第一次浸泡于所述阻燃剂中的时间为10-15min。
17.进一步地,在步骤s2中,所述第一次干燥的温度为50-60℃。
18.进一步地,在步骤s2中,所述第二次浸泡的时间为5-8min,所述再次干燥的温度为80-90℃。
19.与现有技术相比,本发明的有益效果包括:丝瓜络为天然纤维缠结构成的三维网状结构,其质量轻,韧性好,具有填充密度小、抗冲击能力强的特性;丝瓜络内部复杂的孔道结构具有良好的吸波减震和火焰淬熄效果,中间大骨架构成的孔道结构可减小管内流体阻塞率;阻燃剂由氨基三亚甲基膦酸、烟酰胺和山梨醇按照本发明提出的配比构成;氨基三亚甲基膦酸中磷含量较高,且能与山梨醇发生脱水缩合反应;山梨醇化学性质稳定、热稳定好,可作为生物质碳源;烟酰胺由于其富氮特性和含碳环结构,发挥发泡剂和碳源的作用;生物基膨胀型阻燃剂可实现对丝瓜络进行高效阻燃处理,弥补了丝瓜络阻燃性能的不足,开拓了丝瓜络在燃气阻火隔爆领域的应用,丝瓜络和阻燃剂混合得到的生物基阻火隔爆材料具有优异的阻燃性能。
附图说明
20.图1是本发明实施例1制得的阻燃剂的红外光谱图。
21.图2是本发明实施例2制得的生物基阻火隔爆材料的在
②
位置不同长度填充下的火焰传播图像。
22.图3是本发明实施例2制得的生物基阻火隔爆材料的在
②
位置不同长度填充下的火焰传播速率曲线图。
23.图4是本发明实施例1和对比例1制得的生物基阻火隔爆材料燃烧后的形貌对比图;其中左图为实施例1制得的生物基阻火隔爆材料,右图为对比例1制得的生物基阻火隔爆材料。
24.图5是本发明实施例2和对比例2制得的生物基阻火隔爆材料燃烧后的形貌对比图;其中左图为实施例2制得的生物基阻火隔爆材料,右图为对比例2制得的生物基阻火隔爆材料。
具体实施方式
25.本具体实施方式提供了一种生物基阻火隔爆材料,由丝瓜络和阻燃剂混合制得;所述阻燃剂按照重量份数计算,包括山梨醇1-3份、水60-110份、氨基三亚甲基膦酸20-40份
和烟酰胺10-20份。
26.本具体实施方式还提出一种生物基阻火隔爆材料的制备方法,其特征在于,包括以下步骤:
27.s1、按照各组分配比,将山梨醇和水混合5-10min,之后加入氨基三亚甲基膦酸在100-130℃下反应2-3h,之后在100-130℃下继续加入烟酰胺反应1-2h得到阻燃剂,将阻燃剂冷却备用,设置保存温度为25℃;
28.s2、将丝瓜络浸泡于所述阻燃剂中得到所述生物基阻火隔爆材料。
29.在某些优选的实施例中,将丝瓜络浸泡于所述阻燃剂中得到所述生物基阻火隔爆材料;进一步地,包括:将所述丝瓜络浸泡于所述阻燃剂中两次包括:将所述丝瓜络第一次浸泡于所述阻燃剂中10-15min,之后在50-60℃下进行第一次干燥5-7h,将干燥后的丝瓜络第二次浸泡于所述阻燃剂中5-8min,之后在80-90℃下再次干燥10-15h得到所述生物基阻火隔爆材料。
30.本发明提出的阻燃剂的制备方法是通过山梨醇与氨基三亚甲基膦酸之间发生脱水缩合反应形成中间产物,之后由中间产物中的p-o-与烟酰胺的nh
3+
通过离子反应形成阻燃剂。
31.反应过程如下:
[0032][0033]
为了使本发明的目的、技术方案及优点更加清楚明白,以下结合附图及实施例,对本发明进行进一步详细说明。应当理解,此处所描述的具体实施例仅仅用以解释本发明,并不用于限定本发明。
[0034]
实施例1
[0035]
本实施例提出一种生物基阻火隔爆材料,由丝瓜络和阻燃剂混合制得;所述阻燃
剂按照重量份数计算,包括山梨醇1份、去离子水65份、氨基三亚甲基膦酸22份和烟酰胺10份。
[0036]
本实施例还提出一种上述生物基阻火隔爆材料的制备方法,包括以下步骤:
[0037]
s1、按照各组分配比,将山梨醇和去离子水于烧瓶中,打开搅拌和冷凝装置,设置转速为800r/min混合5min,之后加入氨基三亚甲基膦酸在120℃下反应2h,之后在120℃下继续加入烟酰胺反应2h得到阻燃剂;
[0038]
s2、取粗细均匀的硬质丝瓜络,截至每段5cm,置于烘箱,设置温度65℃,时间13h;取烘箱烘干的丝瓜络置于容器,倒入阻燃剂,直至丝瓜络完全浸于阻燃剂中浸泡10min,浸泡结束后将其置于烘箱预烘,设置烘箱温度为60℃,时间为5h;取上述丝瓜络重新进行浸泡,设置浸泡时间5min,浸泡结束后将其置于80℃的烘箱干燥10h,得到生物基阻火隔爆材料。
[0039]
图1为本实施例制得的阻燃剂的红外光谱图,从图1可以看出1171cm-1
、748cm-1
和712cm-1
分别为氨基三亚甲基磷酸的p=o、n-c和p-c。1692cm-1
、1640cm-1
和1420cm-1
分别为烟酰胺的c=o、c=c和c=n。1572cm-1
为氨基三亚甲基膦酸与烟酰胺之间的离子相互作用而生成的-nh
3+
,1020cm-1
为山梨醇与氨基三亚甲基膦酸脱水缩合生成的p
–o–
c,该红外光谱图说明成功制备了阻燃剂。
[0040]
实施例2
[0041]
本实施例提出一种生物基阻火隔爆材料,由丝瓜络和阻燃剂混合制得;所述阻燃剂按照重量份数计算,包括山梨醇1份、去离子水65份、氨基三亚甲基膦酸25份和烟酰胺12份。
[0042]
本实施例还提出一种上述生物基阻火隔爆材料的制备方法,包括以下步骤:
[0043]
s1、按照各组分配比,将山梨醇和去离子水于烧瓶中,打开搅拌和冷凝装置,设置转速为500r/min混合10min,之后加入氨基三亚甲基膦酸在120℃下反应3h,之后在120℃下继续加入烟酰胺反应2h得到阻燃剂;
[0044]
s2、取粗细均匀的硬质丝瓜络,截至每段5cm,置于烘箱,设置温度65℃,时间13h;取烘箱烘干的丝瓜络置于容器,倒入阻燃剂,直至丝瓜络完全浸于阻燃剂中浸泡15min,浸泡结束后将其置于烘箱预烘,设置烘箱温度为60℃,时间为7h;取上述丝瓜络重新进行浸泡,设置浸泡时间8min,浸泡结束后将其置于80℃的烘箱干燥15h,得生物基阻火隔爆材料。
[0045]
实施例3
[0046]
本实施例提出一种生物基阻火隔爆材料,由丝瓜络和阻燃剂混合制得;所述阻燃剂按照重量份数计算,包括山梨醇3份、去离子水60份、氨基三亚甲基膦酸20份和烟酰胺15份。
[0047]
本实施例还提出一种上述生物基阻火隔爆材料的制备方法,包括以下步骤:
[0048]
s1、按照各组分配比,将山梨醇和去离子水于烧瓶中,打开搅拌和冷凝装置,设置转速为1000r/min混合8min,之后加入氨基三亚甲基膦酸在110℃下反应2.5h,之后在110℃下继续加入烟酰胺反应1h得到阻燃剂;
[0049]
s2、取粗细均匀的硬质丝瓜络,截至每段5cm,置于烘箱,设置温度65℃,时间13h;取烘箱烘干的丝瓜络置于容器,倒入阻燃剂,直至丝瓜络完全浸于阻燃剂中浸泡12min,浸泡结束后将其置于烘箱预烘,设置烘箱温度为50℃,时间为6h;取上述丝瓜络重新进行浸
泡,设置浸泡时间7min,浸泡结束后将其置于85℃的烘箱干燥12h,得生物基阻火隔爆材料。
[0050]
实施例4
[0051]
本实施例提出一种生物基阻火隔爆材料,由丝瓜络和阻燃剂混合制得;所述阻燃剂按照重量份数计算,包括山梨醇2份、去离子水110份、氨基三亚甲基膦酸40份和烟酰胺20份。
[0052]
本实施例还提出一种上述生物基阻火隔爆材料的制备方法,包括以下步骤:
[0053]
s1、按照各组分配比,将山梨醇和去离子水于烧瓶中,打开搅拌和冷凝装置,设置转速为900r/min混合9min,之后加入氨基三亚甲基膦酸在130℃下反应2h,之后在130℃下继续加入烟酰胺反应1.5h得到阻燃剂;
[0054]
s2、取粗细均匀的硬质丝瓜络,截至每段5cm,置于烘箱,设置温度65℃,时间13h;取烘箱烘干的丝瓜络置于容器,倒入阻燃剂,直至丝瓜络完全浸于阻燃剂中浸泡13min,浸泡结束后将其置于烘箱预烘,设置烘箱温度为55℃,时间为6.5h;取上述丝瓜络重新进行浸泡,设置浸泡时间6min,浸泡结束后将其置于90℃的烘箱干燥13h,得生物基阻火隔爆材料。
[0055]
对比例1
[0056]
本对比例的制备方法与实施例1的区别在于,阻燃剂的制备步骤不同,具体地,按照各组分配比,将山梨醇、氨基三亚甲基膦酸、烟酰胺和去离子水于烧瓶中,设置转速为800r/min,搅拌混合4h,25℃冷却保存得到阻燃剂;
[0057]
s2、取粗细均匀的硬质丝瓜络,截至每段5cm,置于烘箱,设置温度65℃,时间13h;取烘箱烘干的丝瓜络置于容器,倒入阻燃剂,直至丝瓜络完全浸于阻燃剂中浸泡10min,浸泡结束后将其置于烘箱预烘,设置烘箱温度为60℃,时间为5h;取上述丝瓜络重新进行浸泡,设置浸泡时间5min,浸泡结束后将其置于80℃的烘箱干燥10h,得生物基阻火隔爆材料。
[0058]
对比例2
[0059]
本对比例的制备方法与实施例2的区别在于,阻燃剂的制备步骤不同,具体地,按照各组分配比,将山梨醇、氨基三亚甲基膦酸、烟酰胺和去离子水于烧瓶中,设置转速为800r/min,搅拌混合5h,25℃冷却保存得到阻燃剂;
[0060]
s2、取粗细均匀的硬质丝瓜络,截至每段5cm,置于烘箱,设置温度65℃,时间13h;取烘箱烘干的丝瓜络置于容器,倒入阻燃剂,直至丝瓜络完全浸于阻燃剂中浸泡15min,浸泡结束后将其置于烘箱预烘,设置烘箱温度为60℃,时间为7h;取上述丝瓜络重新进行浸泡,设置浸泡时间8min,浸泡结束后将其置于80℃的烘箱干燥15h,得生物基阻火隔爆材料。
[0061]
对本发明实施例1-4的生物基阻火隔爆材料进行阻火隔爆测试,试平台由点火系统、配气系统、3节长2m内径60mm的圆管道和1节长0.5m方形管道(可视窗)组成,爆炸气体为9.5%甲烷-空气预混气体,将材料填充于管道中,设置填充位置为
①
位置(距离点火端1.9m),填充长度分别为5cm、10cm、15cm。具体压力测试结果如表1所示。
[0062]
表1实施例1-4的生物基阻火隔爆材料在
①
位置的隔爆试验压力数据
[0063][0064]
从表1可以看出随着填充长度的递增,抑制率也呈递增趋势,在填充长度15cm时,抑制率最高可达81.41%。
[0065]
对本发明的生物基阻火隔爆材料实施例1-2进行阻火隔爆测试,试平台由点火系统、配气系统、3节长2m内径60mm的圆管道和1节长0.5m宽50mm方形管道(可视窗)组成,爆炸气体为9.5%甲烷-空气预混气体,将材料填充于管道中,设置填充位置
②
(距离点火端4.4m),填充长度分别为5cm、10cm、15cm。具体压力测试结果如表2所示。
[0066]
表2实施例1-2的生物基阻火隔爆材料在
②
位置的隔爆试验压力数据
[0067][0068]
从表2可以看出随着填充长度的递增,抑制率也呈递增趋势,在填充长度15cm时,抑制率最高可达54.17%。
[0069]
结合图2和图3可以看出,生物基阻火隔爆材料随着填充长度的增长,火焰传播速度明显变慢,这也说明了本发明制得的生物基阻火隔爆材料具有较好的阻火作用。
[0070]
ul-94垂直燃烧测试
[0071]
将实施例1及对比例1制得的生物基阻火隔爆材料进行ul-94垂直燃烧测试,结果如图4所示。
[0072]
从图4可以看出,实施例1制得的生物基阻火隔爆材料只损毁了4cm,而对比例1的生物基阻火隔爆材料损毁了8.5cm,说明本发明制得的生物基阻火隔爆材料的阻燃效果明显优于对比例1。
[0073]
从图5可以看出,实施例2制得的生物基阻火隔爆材料只损毁了3.5cm,而对比例2的生物基阻火隔爆材料损毁了8.0cm,说明本发明制得的生物基阻火隔爆材料的阻燃效果明显优于对比例2。
[0074]
极限氧指数测试
[0075]
将丝瓜络原料、实施例1、实施例2、对比例1和对比例2制得的生物基阻火隔爆材料进行极限氧指数实验,结果如表3所示。
[0076]
表3实施例1-2及对比例1-2制得的生物基阻火隔爆材料的阻燃测试数据
[0077][0078]
从表3可以看出,本发明提出的生物基阻火隔爆材料具有较高的极限氧指数,可高达45%。
[0079]
以上所述本发明的具体实施方式,并不构成对本发明保护范围的限定。任何根据本发明的技术构思所做出的各种其他相应的改变与变形,均应包含在本发明权利要求的保护范围内。