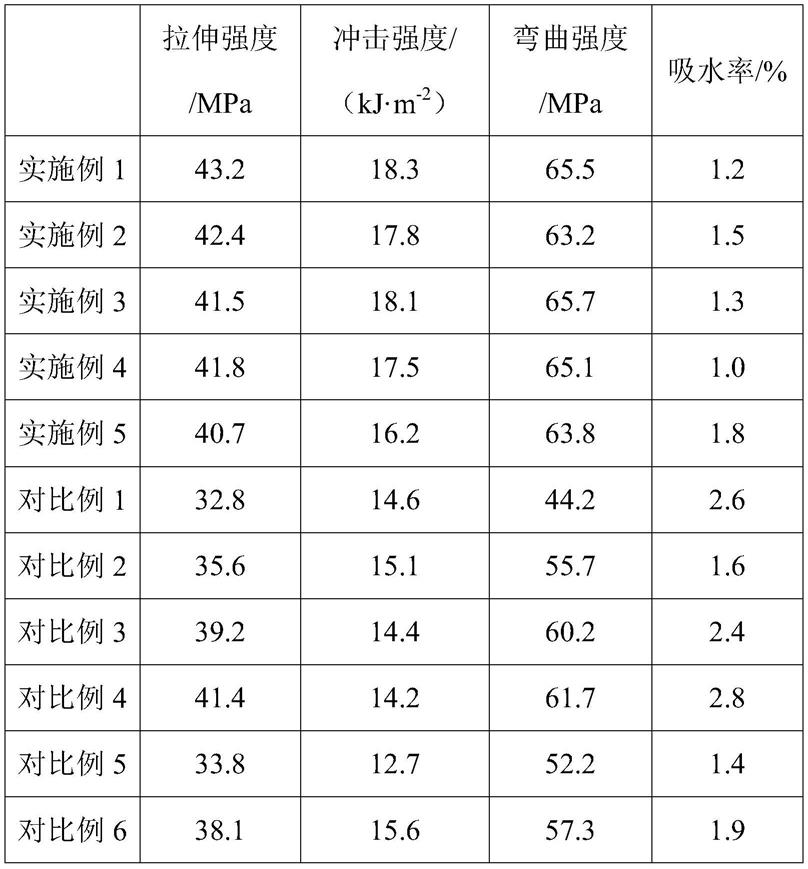
1.本发明涉及复合材料领域,具体为一种集装箱底板用竹塑复合材料及其制备方法。
背景技术:
2.集装箱作为一种装载货物进行运输,并便于用机械设备进行装卸搬运的工具,被广泛地应用各种领域,集装箱底板作为货物承载的载体,既可以用于固定货物,也可以防止货物在运输过程中与集装箱直接发生剐蹭、撞击,目前集装箱底板多为木材或竹材,虽然价格低廉,但是不耐腐蚀,在海运过程中易受水汽侵蚀腐烂,聚乳酸是可再生资源获得的生物基材料,它既可以像传统塑料一样进行热塑性加工,又可以生物降解,所制作的聚乳酸基竹塑复合材料废弃后的能自然降解,不会造成环境污染,但是目前的聚乳酸基竹塑复合材料力学性能较差,无法满足集装箱底板的使用需求。
技术实现要素:
3.发明目的:针对上述技术问题,本发明提供了一种集装箱底板用竹塑复合材料及其制备方法。
4.所采用的技术方案如下:
5.一种集装箱底板用竹塑复合材料,包括以下组成成分:
6.聚多巴胺改性竹粉、聚乳酸接枝马来酸酐/丙烯酸丁酯共聚物、乙烯/甲基丙烯酸甲酯共聚物、聚癸二酸甘油酯、增韧剂、马来酸酐接枝相容剂、聚乙烯蜡。
7.进一步地,包括以下重量份数的组成成分:
8.聚多巴胺改性竹粉40-60份、聚乳酸接枝马来酸酐/丙烯酸丁酯共聚物40-60份、乙烯/甲基丙烯酸甲酯共聚物5-10份、聚癸二酸甘油酯0.5-1份、增韧剂4-6份、马来酸酐接枝相容剂2-4份、聚乙烯蜡1-2份。
9.进一步地,所述聚多巴胺改性竹粉的制备方法如下:
10.将多巴胺盐酸盐加入tris-hcl缓冲液中,搅拌使其溶解,再将竹粉加入,继续搅拌10-30min,再将硫酸铜和过氧化氢加入,反应30-50min后滤出,用去离子水充分洗涤后干燥即可。
11.进一步地,所述竹粉经过硅烷偶联剂处理。
12.进一步地,所述硫酸铜和过氧化氢的加入量分别为0.75-0.85g/l、0.3-0.35g/l。
13.进一步地,所述增韧剂为聚烯烃弹性体和苯乙烯类热塑性弹性体。
14.进一步地,所述聚烯烃弹性体和苯乙烯类热塑性弹性体的质量比为1-3:1-3。
15.进一步地,所述聚乳酸接枝马来酸酐/丙烯酸丁酯共聚物的制备方法如下:
16.分别将聚乳酸、马来酸酐、丙烯酸丁酯用dmac溶解得到溶液a、溶液b和溶液c,向溶液a中加入过氧化物引发剂,80-85℃搅拌10-20min后,将溶液b和溶液c加入溶液a中,保温反应2-4h后恢复室温,将反应液倒入无水乙醇中,使产物析出,过滤,乙醇洗涤后烘干,再以
甲苯为溶剂,将产物在索氏抽提器中抽提20-25h,滤液倒入无水乙醇中,使纯化后的产物析出,过滤并干燥即可。
17.进一步地,所述聚乳酸、马来酸酐、丙烯酸丁酯的质量比为8-10:1:1-2。
18.本发明还提供了一种集装箱底板用竹塑复合材料的制备方法:
19.将聚多巴胺改性竹粉、聚乳酸接枝马来酸酐/丙烯酸丁酯共聚物、乙烯/甲基丙烯酸甲酯共聚物、聚癸二酸甘油酯、增韧剂、马来酸酐接枝相容剂、聚乙烯蜡混合均匀后,再转移至转矩流变仪中熔融共混,温度设置为180-200℃,转速为60-80r/min,熔融共混时间为10-30min,将熔融共混所得物料使用高速粉碎机粉碎成颗粒状,然后放入模具中使用平板硫化机热压,热压温度为180-200℃,压力为10-15mpa,热压时间为10-15min,最后于8-10mpa下冷压10-15min即可。
20.本发明的有益效果:
21.本发明提供了一种集装箱底板用竹塑复合材料,采用硫酸铜/过氧化氢氧化体系诱导多巴胺快速自聚沉积在竹粉表面,多巴胺的苯环和碳氢基团与其余组分间的大分子链产生物理缠绕等作用,改善了界面相容性,有效地提高复合材料的力学性能,马来酸酐作为极性单体,与聚乳酸接枝可赋予聚乳酸良好的极性,丙烯酸丁酯是一种柔性单体,接枝后可以改善聚乳酸的韧性,乙烯/甲基丙烯酸甲酯共聚物流动性能好,加入后可以改善加工性能,而且分子侧链中有着大量的甲基丙烯酸甲酯,也有一定的增容作用,聚癸二酸甘油酯加入后可以提升竹塑复合材料的韧性,经过测试,本发明竹塑复合材料具有极佳的力学性能,且由可降解材料制成,绿色环保,可以满足作为集装箱底板的使用需求。
具体实施方式
22.实施例中未注明具体条件者,按照常规条件或制造商建议的条件进行。所用试剂或仪器未注明生产厂商者,均为可以通过市售购买获得的常规产品。
23.实施例1:
24.一种集装箱底板用竹塑复合材料,包括以下组成成分:
25.聚多巴胺改性竹粉600g(自制)、聚乳酸接枝马来酸酐/丙烯酸丁酯共聚物500g(自制)、乙烯/甲基丙烯酸甲酯共聚物80g(美国杜邦)、聚癸二酸甘油酯8g(广州合美化工)、增韧剂40g、马来酸酐接枝相容剂poe-g-mah 20g(科艾斯)、聚乙烯蜡10g(科艾斯)。
26.其中,聚多巴胺改性竹粉的制备方法如下:
27.将乙醇与水按体积比95:5混合成溶液,再加入乙酸调节体系ph至4.5,再将2%的硅烷偶联剂kh-550加入,搅拌5min后将竹粉加入,超声振荡30min后滤出,水洗至中性后干燥待用,将多巴胺盐酸盐100g加入tris-hcl缓冲液(ph=8.5,0.05mol/l)中,搅拌使其溶解,再将硅烷偶联剂处理后的竹粉500g加入,继续搅拌30min,再将硫酸铜和过氧化氢加入,硫酸铜和过氧化氢的加入量分别为0.8g/l、0.35g/l,反应50min后滤出,用去离子水充分洗涤后干燥即可。
28.增韧剂为质量比为1:1的聚烯烃弹性体(陶氏)和苯乙烯类热塑性弹性体(陶氏)。
29.聚乳酸接枝马来酸酐/丙烯酸丁酯共聚物制备方法如下:
30.分别将聚乳酸、马来酸酐、丙烯酸丁酯用dmac溶解得到溶液a、溶液b和溶液c,向溶液a中加入总质量0.5%的过氧化苯甲酰做引发剂,85℃搅拌20min后,将溶液b和溶液c加入
溶液a中,聚乳酸、马来酸酐、丙烯酸丁酯的质量比为10:1:1,保温反应4h后恢复室温,将反应液倒入无水乙醇中,使产物析出,过滤,乙醇洗涤后烘干,再以甲苯为溶剂,将产物在索氏抽提器中抽提25h,滤液倒入无水乙醇中,使纯化后的产物析出,过滤并干燥即可。
31.上述集装箱底板用竹塑复合材料的制备方法:
32.将聚多巴胺改性竹粉、聚乳酸接枝马来酸酐/丙烯酸丁酯共聚物、乙烯/甲基丙烯酸甲酯共聚物、增韧剂、马来酸酐接枝相容剂、聚乙烯蜡混合均匀后,再转移至转矩流变仪中熔融共混,温度设置为200℃,转速为80r/min,熔融共混时间为30min,将熔融共混所得物料使用高速粉碎机粉碎成颗粒状,然后放入模具中使用平板硫化机热压,热压温度为200℃,压力为15mpa,热压时间为10min,最后于10mpa下冷压15min即可。
33.实施例2:
34.与实施例1基本相同,区别在于,一种集装箱底板用竹塑复合材料,包括以下组成成分:
35.聚多巴胺改性竹粉600g、聚乳酸接枝马来酸酐/丙烯酸丁酯共聚物600g、乙烯/甲基丙烯酸甲酯共聚物100g、聚癸二酸甘油酯10g、增韧剂60g、马来酸酐接枝相容剂poe-g-mah 40g、聚乙烯蜡20g。
36.实施例3:
37.与实施例1基本相同,区别在于,一种集装箱底板用竹塑复合材料,包括以下组成成分:
38.聚多巴胺改性竹粉400g、聚乳酸接枝马来酸酐/丙烯酸丁酯共聚物400g、乙烯/甲基丙烯酸甲酯共聚物50g、聚癸二酸甘油酯5g、增韧剂40g、马来酸酐接枝相容剂poe-g-mah 20g、聚乙烯蜡10g。
39.实施例4:
40.与实施例1基本相同,区别在于,一种集装箱底板用竹塑复合材料,包括以下组成成分:
41.聚多巴胺改性竹粉600g、聚乳酸接枝马来酸酐/丙烯酸丁酯共聚物400g、乙烯/甲基丙烯酸甲酯共聚物100g、聚癸二酸甘油酯5g、增韧剂60g、马来酸酐接枝相容剂poe-g-mah 20g、聚乙烯蜡20g。
42.实施例5:
43.与实施例1基本相同,区别在于,一种集装箱底板用竹塑复合材料,包括以下组成成分:
44.聚多巴胺改性竹粉400g、聚乳酸接枝马来酸酐/丙烯酸丁酯共聚物600g、乙烯/甲基丙烯酸甲酯共聚物50g、聚癸二酸甘油酯10g、增韧剂40g、马来酸酐接枝相容剂pp-g-mah 40g、聚乙烯蜡10g。
45.对比例1:
46.与实施例1基本相同,区别在于,区别在于,竹粉不经聚多巴胺改性处理。
47.对比例2:
48.与实施例1基本相同,区别在于,用等质量的聚乳酸代替聚乳酸接枝马来酸酐/丙烯酸丁酯共聚物。
49.对比例3:
50.与实施例1基本相同,区别在于,不加入乙烯/甲基丙烯酸甲酯共聚物。
51.对比例4:
52.与实施例1基本相同,区别在于,不加入聚癸二酸甘油酯。
53.对比例5:
54.与实施例1基本相同,区别在于,不加入增韧剂。
55.对比例6:
56.与实施例1基本相同,区别在于,竹粉不经过硅烷偶联剂处理。
57.性能测试:
58.将本发明实施例1-5及对比例1-6中所制备的竹塑复合材料作为试样进行性能检测,拉伸性能按gb/t1040.2-2006测试,弯曲强度按gb/t1449-2005测试,冲击强度按gb/t1843-2008测试;
59.吸水率的测定:取的竹塑复合材料试样(质量记为m1),试样尺寸为20
×
20
×
4mm,室温下浸泡于水中120h后取出,用吸水纸吸干其表面水分后再次称重(质量记为m2),按照下式来计算该竹塑复合材料的吸水率:
60.吸水率=[(m
2-m1)/m1]
×
100%
[0061]
测试结果如下表1所示:
[0062]
表1:
[0063][0064]
由上表1可知,本发明所制备的竹塑复合材料具有极佳的力学性能,且通过对比例1-6可知,本发明组分间具有极佳的协同性,可以满足作为集装箱底板的使用需求。
[0065]
以上实施例仅用以说明本发明的技术方案,而非对其限制;尽管参照前述实施例对本发明进行了详细的说明,本领域的普通技术人员应当理解:其依然可以对前述各实施例所记载的技术方案进行修改,或者对其中部分技术特征进行等同替换;而这些修改或者替换,并不使相应技术方案的本质脱离本发明各实施例技术方案的精神和范围。