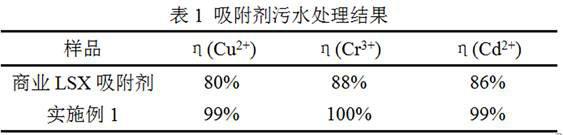
一种超低硅铝比的梯级孔lsx分子筛及其制备方法
技术领域
1.本发明属于分子筛制备技术领域,具体涉及一种超低硅铝比的梯级孔lsx分子筛及其制备方法。
背景技术:
2.x型分子筛骨架中相互连通的孔道和笼使其具有优异的离子交换、择形催化和吸附分离性能,因此被广泛应用于石油化工、精细化工和环境保护等多个领域。通常将硅铝比在1.0-1.1之间的x型分子筛称之为lsx分子筛,其骨架硅铝比更低因而具有更多的负电荷和高活性位点,故其阳离子交换量较大,电荷密度高且吸附能力强,具有更广泛的应用。但是,常规的lsx分子筛是典型的微孔材料,其在大分子催化和吸附反应中分别存在传质效率低、易结焦失活、活性位可接近性差和吸附容量低、扩散阻力大、传质效率低等问题,已不能满足工业应用的要求,因此迫切需要开发具有梯级孔道结构的分子筛催化、吸附材料。
3.众所周知使用模板法合成梯级孔分子筛已经相当成熟,然而模板剂的使用会带来很多负面的问题。其一,模板剂的价格昂贵,且自身合成过程操作复杂繁琐;其二,分子筛合成过程产生大量废水,由于其中含有大量对环境有害的模板剂,所以必须经过有效的处理才能达到排放标准;其三,在分子筛合成后期,一般采用高温焙烧的方法除去模板剂,而这一过程不仅需要消耗大量的能源,而且还会释放大量有害气体(如温室气体),此外,模板剂的脱除过程,还会引起分子筛骨架结构的坍塌,从而降低分子筛的可利用性。
4.目前已有较多学者使用各种原料合成lsx分子筛,但是仍然存在合成过程非绿色、高成本的问题,此外无模板剂合成梯级孔lsx分子筛的研究较少,且超低硅铝比梯级孔lsx分子筛的合成尚无涉及。
技术实现要素:
5.本发明的目的在于提供一种超低硅铝比的梯级孔lsx分子筛及其制备方法,实现了无模板法合成梯级孔lsx分子筛,缩短了梯级孔lsx分子筛合成路线,极大地降低了合成成本,制备过程更符合绿色化学的经济性,同时能够可控制备具有超低硅铝比(n(si/al)=1.0~1.02)的梯级孔lsx分子筛。
6.为实现上述目的,本发明采用如下技术方案:一种制备梯级孔lsx分子筛的方法:以天然黏土矿物为硅源和铝源,在不添加介孔模板剂的条件下,水热晶化可控制备出梯级孔lsx分子筛。
7.包括以下步骤:(1)矿物的活化:将天然黏土矿物与氢氧化钠溶液混合,活化,烘干,粉碎,得到活化后的天然硅铝矿物;(2)晶化:将活化后的天然硅铝矿物、去离子水、碱和补充硅源混合,搅拌形成均匀的凝胶,老化后密封静态晶化,自然冷却,离心,用去离子水洗涤至中性,干燥,得到所述的梯级孔lsx分子筛。
8.所述的天然黏土矿物为高岭土、累托土、蒙脱土、伊利石、叶腊石、铝土矿、膨润土中的至少一种。
9.步骤(1)中氢氧化钠溶液浓度为250-500g/l,天然黏土矿物与氢氧化钠的质量比为1:1-2;活化温度为150-300℃,时间1-6 h。
10.步骤(2)中原料投料摩尔比为sio2:al2o3:na2o:k2o:h2o=2.0-5.6:1:4-12:0-3:100-400。
11.步骤(2)中补充硅源为硅胶、白炭黑、正硅酸乙酯、硅酸钠中的至少一种。
12.步骤(2)中老化温度为25-60℃,时间为4-24 h。
13.步骤(2)中晶化温度为60-110℃,时间为2-12 h。
14.所述的梯级孔lsx分子筛的介孔孔径为3-20 nm,硅铝摩尔比为1.0-1.02,相对结晶度为80-98 %。
15.本发明的有益效果在于:(1)本发明可以在完全无模板剂、超低的硅铝比范围下利用天然矿物合成结晶度良好的介孔-微孔复合的梯级孔lsx分子筛,且其介孔分布集中,完全避免了有机模板剂的脱除对环境造成的污染,实现绿色合成高性能lsx分子筛的目的;(2)本发明将合成的梯级孔lsx分子筛应用于污水处理,取得了显著的效果:与市售的lsx分子筛相比,在相同的反应条件下,本发明所合成的梯级孔lsx分子筛污水中的重金属离子(cu
2+
、cr3+和cd
2+
)去除率高达99%~100%;(3)本发明将合成的梯级孔lsx分子筛应用于co2吸附,取得了显著的效果:与市售的lsx分子筛相比,在相同的反应条件下,本发明所合成的梯级孔lsx分子筛吸附量更高、吸附时间和寿命更长。
附图说明
16.图1为本发明实施1所制备的梯级孔lsx分子筛的x-射线衍射(xrd)谱图。
17.图2为本发明实施1所制备的梯级孔lsx分子筛的n
2-吸附脱附等温线。
18.图3为本发明实施1所制备的梯级孔lsx分子筛的bjh孔径分布图。
19.图4为本发明实施4所制备的梯级孔lsx分子筛的xrd谱图。
20.图5为本发明实施4所制备的梯级孔lsx分子筛的n
2-吸附脱附等温线。
21.图6为本发明实施4所制备的梯级孔lsx分子筛的bjh孔径分布图。
22.图7为本发明实施3所制备的梯级孔lsx分子筛与商业lsx分子筛的co2吸附曲线图。
23.图8为本发明实施3所制备的梯级孔lsx分子筛与商业lsx分子筛的co2吸附再生次数图。
具体实施方式
24.为了使本发明所述的内容更加便于理解,下面结合具体实施方式对本发明所述的技术方案做进一步的说明,但是本发明不仅限于此。
25.(1)矿物的活化:对低硅铝比矿物进行亚熔盐活化,配制浓度为250-500 g/l氢氧化钠水溶液,按低硅铝比矿物与氢氧化钠固体质量比为1:(1-2)的比例称取低硅铝比矿物,
将低硅铝比矿物与氢氧化钠水溶液一起加入反应釜中;将反应釜升温至150-300℃,并在常压敞开体系下反应1-6 h,烘干后粉碎得到活化后的低硅铝比矿物。
26.(2)晶化:将步骤(1)活化后的低硅铝比矿物、去离子水与氢氧化钠和硅胶在搅拌条件下混合形成均匀的凝胶,采用无机酸或无机碱调节体系的酸碱性,控制体系的摩尔比为sio2:al2o3:na2o:k2o:h2o=(2.0-5.6):1:(4-12):(0-3):(100-400);将混合后的凝胶在30-60℃下老化4-24 h,转移至聚四氟乙烯内衬的反应釜中60-110℃下晶化2-12 h密封静态晶化,待晶化结束后,将晶化得到的产物冷却,将产物进行离心分离,取沉淀并用去离子水洗涤至中性,干燥得梯级孔lsx分子筛。
27.本发明由天然矿物为全部铝源和部分硅源,补充硅源可以是硅胶、白炭黑、正硅酸乙酯、硅酸钠,无需模板剂,经水热晶化而获得梯级孔lsx分子筛。拓宽了以亚熔盐活化的天然矿物为原料合成梯级孔lsx分子筛的类型,且没有使用模板剂,降低了分子筛的合成成本,减少了污染排放。
28.本发明中所述的低硅铝比矿物是指硅铝摩尔比在10以下的天然矿物;因此,在本发明所述的方法中,低硅铝比的天然矿物除高岭土外,还可以选用蒙脱土、膨润土和伊利石。
29.实施例中所说的相对结晶度是根据astm d 5758-01标准,以所得产物与分子筛标样的xrd谱图中2θ角在6.09
°±
0.30
°
、9.96
°±
0.30
°
、11.70
°±
0.30
°
、15.40
°±
0.20
°
、23.27
°±
0.20
°
、26.62
°±
0.20
°
、30.28
°±
0.20
°
、30.92
°±
0.20
°
、31.96
°±
0.20
°
、33.56
°±
0.50
°
的十个特征峰面积之和的比值,以百分数表示,标样为以常规化学试剂为原料合成的lsx分子筛(南开大学催化剂厂生产,其硅铝摩尔比为2.36),将其结晶度定义为100 %。
30.各实施例中矿物、固体硅胶及无机化学试剂的选择:所用的高岭土、补充硅源、氢氧化钠和氢氧化钾固体均为市售产品。高岭土的主要成分为:sio2的含量为50.5 wt%,al2o3的含量为44.6 wt%;水玻璃的sio2的含量为27.68 wt%,na2o的含量8.95 wt%,h2o的含量为63.37 wt%、固体硅胶的sio2的含量为89.2 wt%,h2o的含量为9.9 wt%;氢氧化钠固体、氢氧化钾固体(北京化工厂出品,纯度为99 %)。
31.实施例1矿物的活化:称取35 g氢氧化钠固体溶解于150 ml去离子水中,加入25 g高岭土粉末并均匀混合,于220 ℃大气压下敞开体系反应4 h,将反应后的固体粉碎,得到活化的高岭土备用。
32.分子筛制备:称取4 g活化后的高岭土和2.86 g 氢氧化钠溶于50 g去离子水中,混合均匀后在搅拌的条件下加入0.71 g硅胶,最后再加入0.15 g晶种,在30 ℃下混合搅拌老化12 h;将该混合物倒入带聚四氟乙烯内衬的不锈钢晶化釜内,于90℃静止晶化4 h;晶化结束后,冷却、过滤得到滤饼,滤饼洗涤至中性,于100 ℃下干燥得到lsx分子筛,产物硅铝比为1.01。经xrd测定,合成产物的物相归属于lsx分子筛,相对结晶度定为98 %。
33.图1为本实施例的梯级孔lsx分子筛的xrd谱图,结果表明合成的梯级孔lsx分子筛的fau结构和结晶度保持良好。
34.图2为本实施例的梯级孔lsx分子筛的n2吸附-脱附等温线,结果表明本发明合成的梯级孔lsx分子筛表现出了iv型吸附等温线。在0《p/p0《0.40的低压区,吸附量随p/p0的增加而增大,这是由于n2在微孔区的填充;当相对压力p/p0大于0.40时,吸附-脱附等温线出现
明显的滞后环,属于n2在介孔中的毛细管凝聚现象,说明产物中存在介孔结构。
35.图3为本实施例的梯级孔lsx分子筛的bjh孔径分布图。根据吸附曲线计算得到的孔径分布曲线存在明显的介孔分布,说明本发明制备的梯级孔lsx分子筛具有介孔结构,介孔孔径分布在6 nm左右。
36.实施例2矿物的活化:称取37.5 g氢氧化钠固体溶解于150 ml去离子水中,加入25 g高岭土粉末并均匀混合,于200℃大气压下敞开体系反应5 h,将反应后的固体粉碎,得到活化的高岭土备用。
37.分子筛制备:称取4.00 g活化后的高岭土和2.60 g 氢氧化钠溶于48.52 g去离子水中,混合均匀后在搅拌的条件下加入2.28 g水玻璃,在30℃下混合搅拌老化12 h;将该混合物倒入带聚四氟乙烯内衬的不锈钢晶化釜内,于100℃静止晶化4 h;晶化结束后,冷却、过滤得到滤饼,滤饼洗涤至中性,于100℃下干燥得到lsx分子筛。经xrd测定,合成产物的物相归属于lsx分子筛,产物硅铝比为1.0,相对结晶度定为85 %,介孔孔径分布在10 nm左右。
38.实施例3矿物的活化:称取70 g氢氧化钠固体溶解于200 ml去离子水中,加入50 g高岭土粉末并均匀混合,于200℃大气压下敞开体系反应5 h,将反应后的固体粉碎,得到活化的高岭土备用。
39.分子筛制备:称取4.00 g活化后的高岭土和2.33 g 氢氧化钠溶于46.12 g去离子水中,混合均匀后在搅拌的条件下加入0.59 g硅胶,最后再加入0.13 g晶种,在30℃下混合搅拌老化14 h;将该混合物倒入带聚四氟乙烯内衬的不锈钢晶化釜内,于85℃静止晶化4.5 h;晶化结束后,冷却、过滤得到滤饼,滤饼洗涤至中性,于100℃下干燥得到lsx分子筛。经xrd测定,合成产物的物相归属于lsx分子筛,产物硅铝比为1.011,相对结晶度定为92 %,介孔孔径分布在4 nm左右。
40.实施例4本实施例提供一种梯级孔lsx分子筛,制备步骤同实施例1,仅调变部分参数,具体如下:分子筛制备:称取10.00 g高岭土、1.38 g 氢氧化钠和4.54 g氢氧化钾溶于38.91 g去离子水中,混合均匀后在搅拌的条件下加入0.31 g硅胶,最后再加入0.25 g晶种,在60℃下混合搅拌老化6 h;将该混合物倒入带聚四氟乙烯内衬的不锈钢晶化釜内,于75℃静止晶化2.5 h;晶化结束后,冷却、过滤得到滤饼,滤饼洗涤至中性,于100℃下干燥得到lsx分子筛。经xrd测定,合成产物的物相归属于lsx分子筛,产物硅铝比为1.02,相对结晶度为97 %,介孔孔径分布在15 nm左右。
41.实施例5本实施例提供一种梯级孔lsx分子筛,制备步骤同实施例2,仅调变部分参数,具体如下:分子筛制备:称取9.00 g高岭土、1.24 g 氢氧化钠和4.09 g氢氧化钾溶于36.46 g去离子水中,混合均匀后在搅拌的条件下加入0.39 g硅胶,最后再加入0.23 g晶种,在55℃下混合搅拌老化8 h;将该混合物倒入带聚四氟乙烯内衬的不锈钢晶化釜内,于70℃静止晶化2.5 h;晶化结束后,冷却、过滤得到滤饼,滤饼洗涤至中性,于100℃下干燥得到lsx分
子筛。经xrd测定,合成产物的物相归属于lsx分子筛,产物硅铝比为1.01,相对结晶度为86 %,介孔孔径分布在8 nm左右。
42.实施例6本实施例提供一种梯级孔lsx分子筛,制备步骤同实施例3,仅调变部分参数,具体如下:分子筛制备:称取9.00 g高岭土、2.25 g 氢氧化钠和3.13 g氢氧化钾溶于36.46 g去离子水中,混合搅拌均匀后,最后加入0.20 g晶种,在70℃下混合搅拌老化12 h;将该混合物倒入带聚四氟乙烯内衬的不锈钢晶化釜内,于100℃静止晶化5 h;晶化结束后,冷却、过滤得到滤饼,滤饼洗涤至中性,于100℃下干燥得到lsx分子筛。经xrd测定,合成产物的物相归属于lsx分子筛,产物硅铝比为1.015,相对结晶度为90 %,介孔孔径分布在18 nm左右。
43.实施例7将实施例1以天然矿物为原料制备的梯级孔lsx分子筛吸附剂应用于污水处理,取得了显著的效果:与市售的lsx分子筛相比,在相同的反应条件下,本发明所合成的梯级孔lsx分子筛污水中的重金属离子(cu
2+
、cr
3+
和cd
2+
)去除率高达99%~100%,具体的结果如表1。(η(cu
2+
、cd
3+
、cd
2+
)是指吸附剂对污水中的重金属离子的去除率)。
44.根据表1结果,实施例1以天然矿物为原料制备的梯级孔lsx分子筛吸附剂,具有优异的污水处理性能。
45.实施例8将实施例3以天然矿物为原料制备的梯级孔lsx分子筛吸附剂应用于吸附co2,取得了显著的效果:与市售的lsx分子筛相比,在相同的反应条件下,本发明所合成的梯级孔lsx分子筛co2吸附量大,且再生性能强,吸附效果更好,具体的结果如图7和图8。
46.以上实施例说明,本发明的高性能lsx分子筛的制备方法不仅使用天然矿物而且不需要使用任何模板剂,不仅大幅降低了分子筛的生产成本,而且极大提高了制备过程的绿色性,制备的lsx分子筛具有丰富的微-介孔复合的梯级孔道结构且硅铝比可控。
47.以上所述仅为本发明的较佳实施例,凡依本发明申请专利范围所做的均等变化与修饰,皆应属本发明的涵盖范围。