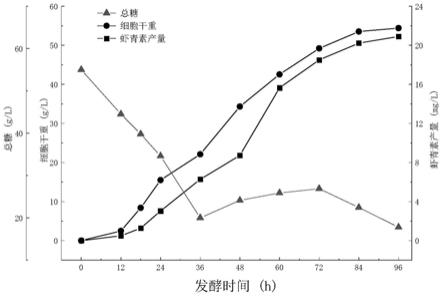
1.本发明属于农产品深加工技术领域,具体涉及一种培养产虾青素红法夫酵母的廉价培养基质及其制备方法和应用。
背景技术:
2.本发明背景技术中公开的信息仅仅旨在增加对本发明的总体背景的理解,而不必然被视为承认或以任何形式暗示该信息构成已经成为本领域一般技术人员所公知的现有技术。
3.虾青素(astaxanthin)又名变胞藻黄素,是萜烯类不饱和化合物,化学名为3,3'-二羟基-β,β'-胡萝卜素-4,4'-二酮,分子式为c
40h52
o4,相对分子量为596.86。虾青素由4个异戊二烯结构组成的长的共轭双键碳链和两端α-羟基酮的六元环构成,分子结构与β-胡萝卜素类似。虾青素广泛存在于生物界,特别是虾、蟹、鱼、藻体、酵母和鸟类的羽毛中含量较高,是海洋生物体内主要的类胡萝卜素之一。虾青素具有极强的抗氧化能力和淬灭单线态氧和捕捉自由基的能力,在已知的600多种天然类胡萝卜素中,虾青素是已知的最强的抗氧化剂,其效力是维生素e的500倍,β-胡萝卜素高38倍。此外,虾青素还具有包括抗炎、抗癌以及增强免疫系统等多种其它生物学特性。虾青素是一种脂溶性色素,能够直接存储在动物组织中,在禽类饲料中加入虾青素,可加深禽蛋的蛋黄颜色,提高其营养价值。
4.虾青素的生产方法大体上可以分为两大类,化学合成法和提取法。化学合成的虾青素为3种立体结构的混合物,抗氧化活性较低,fda已禁止化学合成的虾青素进入保健食品市场。提取法生产虾青素按照来源又可以分为3种:水产动物(如各种虾、蟹)、酵母(法夫酵母、酿酒酵母等)、微藻(如雨生红球藻)。从水产动物中提取虾青素过程复杂,提取成本高、污染严重等,限制了该方法的推广;雨生红球藻中虾青素含量高,利用雨生红球藻制备虾青素被认为是最具商业化前景的一种生产方法,但雨声红球藻生长条件要求苛刻、培养周期长、过程控制复杂、生产成本高;利用法夫氏酵母生产虾青素,细胞繁殖速度快,过程控制简单,但产量相对较低。为了降低法夫氏酵母生产虾青素的成本,采用廉价的原料进行法夫氏酵母高密度培养是一种不错的选择。
5.我国是世界上最大的甘薯生产国,年产量在1亿吨以上,利用生鲜甘薯生产甘薯淀粉及其衍生产品是我国甘薯最主要的深加工方式之一。甘薯淀粉生产是采用生鲜甘薯,分离淀粉后会产生大量甘薯渣和甘薯汁。目前甘薯汁作为生产废水进行处理排放。甘薯汁的固形物含量大约2-4%,含有甘薯中的大量营养物质,作为废水处理排放,不仅增加污水处理成本,还是资源的极大浪费。目前甘薯渣主要是作为饲料出售,附加值较低。甘薯渣中残留淀粉占干物的50-60%,另含有30-40%的膳食纤维。发明人此前研究开发的利用甘薯渣生产可溶性膳食纤维的工艺技术(cn 107095317 b),在提取膳食纤维前,需要通过液化、糖化将薯渣中的残留淀粉糖化后去除,分离的淀粉糖液可以用于食品加工配料或微生物培养碳源。
技术实现要素:
6.针对目前甘薯淀粉加工薯渣和甘薯汁低值化利用和虾青素生产成本高的问题,本发明的目的在于提供一种培养产虾青素红法夫酵母的廉价培养基质及其制备方法和应用。依托现有甘薯淀粉加工技术,利用淀粉生产过程中分离的甘薯渣和甘薯汁制备一种廉价的培养基质,用于产虾青素红法夫酵母的高密度培养,取得了有益的效果。
7.具体的,本发明的技术方案如下:
8.本发明的第一个方面,提供甘薯渣和甘薯汁在制备培养产虾青素红法夫酵母的培养基质中的应用。
9.本发明的第二个方面,提供一种用于培养产虾青素红法夫酵母的培养基质,所述培养基质为包含甘薯渣和甘薯汁成分物质的培养液,所述甘薯渣和甘薯汁可以是从甘薯淀粉加工过程中分离获得。
10.进一步的,所述培养基质还包含酵母浸粉。
11.本发明的第三个方面,提供上述用于培养产虾青素红法夫酵母的培养基质的制备方法,所述制备方法包括:
12.将甘薯渣和甘薯汁混合,加入中温淀粉酶进行液化糖化处理,过滤分离得薯渣和过滤清液,所述薯渣用水洗涤,洗涤水并入所述过滤清液得培养基质原液;调整培养基质原液的淀粉糖浓度至3-5%(优选4%)即得。
13.其中,所述甘薯渣和甘薯汁可以是从甘薯淀粉生产加工过程中分离获得。
14.更具体的,所述甘薯渣和甘薯汁的制备方法包括:向经预处理后的甘薯中加入水进行磨浆处理,磨浆后的物料经过滤筛分后得到甘薯渣和淀粉浆,所述淀粉浆再进行固液分离,分离淀粉后得甘薯汁。
15.本发明的第四个方面,提供上述培养基质在发酵培养产虾青素红法夫酵母中的应用。
16.本发明的第五个方面,提供一种产虾青素红法夫酵母的培养方法,所述培养方法包括:将产虾青素红法夫酵母接种至上述灭菌后的培养基质中进行发酵培养。
17.经试验证明,补料发酵可以大幅提升发酵液中菌体浓度和虾青素的产量。因此,本发明的又一具体实施方式中,所述发酵培养可采用补料发酵培养方式进行。
18.上述一个或多个技术方案的有益技术效果:
19.上述技术方案提供一种培养产虾青素红法夫酵母的廉价培养基质及其制备方法和应用,本发明依托现有甘薯淀粉加工技术,利用淀粉生产过程中分离的甘薯渣和甘薯汁制备一种廉价的培养基质,用于产虾青素红法夫酵母的高密度培养,经试验证明,采用上述廉价培养基质,红法夫酵母的菌体浓度和虾青素的产量优于现有一般合成培养基,因此具有良好的实际应用之价值。
附图说明
20.构成本发明的一部分的说明书附图用来提供对本发明的进一步理解,本发明的示意性实施例及其说明用于解释本发明,并不构成对本发明的不当限定。
21.图1为本发明实施例中碳源种类对红法夫酵母虾青素产量的影响;
22.图2为本发明实施例中氮源对红法夫酵母生长和虾青素产量的影响;
23.图3为本发明实施例中发酵罐分批发酵进程;
24.图4为本发明实施例中发酵罐分批补料发酵进程;
25.图5为本发明实施例中发酵罐分批连续补料发酵进程;
26.图6为本发明实施例中发酵罐对照组分批连续补料发酵进程。
具体实施方式
27.应该指出,以下详细说明都是例示性的,旨在对本发明提供进一步的说明。除非另有指明,本文使用的所有技术和科学术语具有与本发明所属技术领域的普通技术人员通常理解的相同含义。
28.需要注意的是,这里所使用的术语仅是为了描述具体实施方式,而非意图限制根据本发明的示例性实施方式。如在这里所使用的,除非上下文另外明确指出,否则单数形式也意图包括复数形式,此外,还应当理解的是,当在本说明书中使用术语“包含”和/或“包括”时,其指明存在特征、步骤、操作、器件、组件和/或它们的组合。
29.现结合具体实例对本发明作进一步的说明,以下实例仅是为了解释本发明,并不对其内容进行限定。如果实施例中未注明的实验具体条件,通常按照常规条件,或按照试剂公司所推荐的条件;下述实施例中所用的试剂、耗材等,如无特殊说明,均可从商业途径得到。
30.本发明的一个典型具体实施方式中,提供甘薯渣和甘薯汁在制备培养产虾青素红法夫酵母的培养基质中的应用。
31.本发明的又一具体实施方式中,提供一种用于培养产虾青素红法夫酵母的培养基质,所述培养基质为包含甘薯渣和甘薯汁成分物质的培养液,所述甘薯渣和甘薯汁可以是从甘薯淀粉加工过程中分离获得。
32.本发明的又一具体实施方式中,所述培养基质还包含酵母浸粉,所述酵母浸粉含量为不大于5g/l,进一步优选为不大于2g/l,如1g/l、2g/l。通过加入酵母浸粉,能显著提高培养的红法夫酵母菌体浓度和虾青素产量。
33.本发明的又一具体实施方式中,提供上述用于培养产虾青素红法夫酵母的培养基质的制备方法,所述制备方法包括:
34.将甘薯渣和甘薯汁混合,加入中温淀粉酶进行液化糖化处理,过滤分离得薯渣和过滤清液,所述薯渣用水洗涤,洗涤水并入所述过滤清液得培养基质原液;调整培养基质原液的淀粉糖浓度至3-5%(优选4%)即得。
35.所述中温淀粉酶添加量根据薯渣中的淀粉含量进行确定;液化过程选用中温淀粉酶,可以保存生鲜甘薯中的β-淀粉酶活性,使液化后的淀粉进一步糖化生成麦芽糖。
36.所述液化糖化处理具体条件包括:在80-90℃保温液化糖化5-30min,加热至沸腾后保持5-10min。
37.调整培养基质原液的淀粉糖浓度至3-5%,具体操作方法为:向淀粉糖浓度高的培养基质原液中加水稀释,向淀粉糖浓度低的培养基质原液中补加麦芽糖。
38.其中,所述甘薯渣和甘薯汁可以是从甘薯淀粉生产加工过程中分离获得;
39.更具体的,所述甘薯渣和甘薯汁的制备方法包括:向经预处理后的甘薯中加入水进行磨浆处理,磨浆后的物料经过滤筛分后得到甘薯渣和淀粉浆,所述淀粉浆分离淀粉后
得甘薯汁。
40.其中,甘薯的预处理方法包括:对甘薯进行清洗除杂;所述甘薯优选选用新鲜甘薯,但是对甘薯品种不做具体限定,因此可以是富含淀粉品种,也可以是富含β-胡萝卜素的鲜食品种。
41.甘薯磨浆加水量可根据原料甘薯含水量进行调整,一般为甘薯重量的1-3倍(即1kg甘薯,加1-3l饮用水)。
42.本发明的又一具体实施方式中,所述制备方法还包括:向所述培养培养基质中加入酵母浸粉;所述酵母浸粉添加量为不大于5g/l,进一步优选为不大于2g/l,如1g/l、2g/l。通过加入酵母浸粉,能显著提高培养的红法夫酵母菌体浓度和虾青素产量。
43.本发明的又一具体实施方式中,提供上述培养基质在发酵培养产虾青素红法夫酵母中的应用。
44.本发明的又一具体实施方式中,提供一种产虾青素红法夫酵母的培养方法,所述培养方法包括:将产虾青素红法夫酵母接种至上述灭菌后的培养基质中进行发酵培养。
45.经试验证明,补料发酵可以大幅提升发酵/液中菌体浓度和虾青素的产量。因此,本发明的又一具体实施方式中,所述发酵培养可采用补料发酵培养方式进行。其中,所述补料发酵培养方式可以为分批补料发酵或连续补料发酵;由于连续补料发酵过程更加平稳,基质利用率提高,96小时结束发酵,发酵液中残糖浓度低,菌体浓度和虾青素的产量都比分批补料有所提高,因此进一步优选为连续补料发酵。
46.以下通过实施例对本发明做进一步解释说明,但不构成对本发明的限制。应理解这些实施例仅用于说明本发明而不用于限制本发明的范围。下列实施例中为注明具体条件的试验方法,通常按照常规条件进行。
47.实施例
48.原料:淀粉加工用甘薯(干物含量38%),泗水利丰食品有限公司提供;富含β-胡萝卜素的甘薯,市场购买橙心甘薯(干物含量26%)。
49.产虾青素红法夫酵母培养基质的制备:
50.培养基质ⅰ:选取块茎完整、无虫害的淀粉加工用甘薯块茎,洗涤、除杂、切块,加入2.5倍清水磨浆,粉碎后物料经200目滤布过滤,分离薯渣,浆液2000rpm离心1min,分离淀粉,然后将离心清液和薯渣混合,按照薯渣中的淀粉含量加入适量中温α-淀粉酶,加热至80-85℃保温20min,继续加热至100℃,保温5min。过滤分离薯渣,薯渣加1倍水洗涤一次,洗涤水与过滤清液合并,混匀后测固形物含量为7.2%,淀粉糖含量为5.8%。
51.培养基质ⅱ:选取块茎完整、无虫害的富含β-胡萝卜素的甘薯块茎,洗涤、除杂、切块,加入2.0倍清水磨浆,粉碎后物料经200目滤布过滤,分离薯渣,浆液2000rpm离心1min,分离淀粉,然后将离心清液和薯渣混合,按照薯渣中的淀粉含量加入适量中温α-淀粉酶,加热至80-85℃保温5min,继续加热至100℃,保温5min。过滤分离薯渣,薯渣加1倍水洗涤一次,洗涤水与过滤清液合并,混匀后测固形物含量为6.1%,淀粉糖含量为4.5%。
52.培养基质ⅲ:选取块茎完整、无虫害的富含β-胡萝卜素的甘薯块茎,洗涤、除杂、切块,加入2.0倍清水磨浆,浆液不进行淀粉分离,按照料液中的淀粉含量加入适量中温α-淀粉酶,加热至80-85℃保温10min,继续加热至100℃,保温10min。过滤分离薯渣,薯渣加1倍水洗涤一次,洗涤水与过滤清液合并,混匀后测固形物含量为12.6%,淀粉糖含量为
10.8%。
53.培养基质ⅳ:取甘薯淀粉生产分离的薯渣(淀粉含量占干基65.6%)、甘薯汁(干物含量3.1%),按生产比例混合,然后按照薯渣中的淀粉含量加入适量中温α-淀粉酶,加热至80-85℃保温30min,继续加热至100℃,保温5min。过滤分离薯渣,薯渣加1倍水洗涤一次,洗涤水与过滤清液合并,混匀后测固形物含量为6.5%,淀粉糖含量为4.8%。
54.培养基质
ⅴ
:取甘薯淀粉生产分离的薯渣(淀粉含量占干基65.6%)、甘薯汁(干物含量3.1%),将薯渣和薯汁混合,然后按照薯渣中的淀粉含量加入适量中温α-淀粉酶,加热至80-85℃保温30min,继续加热至100℃,保温5min。过滤分离薯渣,薯渣加1倍水洗涤一次,洗涤水与过滤清液合并,将清液减压浓缩至可溶性固形物至60%,检测其中总淀粉糖含量为51.3%.
55.淀粉糖含量测定:取上述方法制备的培养基质20-50ml,浓缩液取2-5ml,加水至98ml,加入2ml浓盐酸,混匀,120℃水解30min,中和、定容250ml,然后用葡萄糖分析仪测定葡萄糖含量,按照葡萄糖含量计算淀粉糖含量。
56.产虾青素红法夫酵母培养:按上述方法制备的培养基质,根据需要调整淀粉糖浓度约4%(淀粉糖含量高的样品适当加水稀释,淀粉糖浓度低的适量补加麦芽糖),然后灭菌,冷却后接种红法夫酵母液体种子,进行培养。
57.菌种:产虾青素红法夫酵母菌株,上述菌种公众可以从山东省食品发酵工业研究设计院获得。
58.液体种子培养基(g/l):葡萄糖20,蛋白胨5,酵母粉5,自来水配制,ph自然。
59.发酵培养基(g/l):葡萄糖40,酵母粉2,硫酸铵0.5,磷酸二氢钠1.5,磷酸氢二钠1.5,硫酸镁0.2,自来水配制,ph自然。
60.培养方法:种子培养,保藏甘油管菌种活化1-2代,10%的接种量接种各种产虾青素酵母培养基质,
61.摇瓶培养:500ml三角瓶装液量50ml,接种量5-10%,25℃、200rpm培养72小时,测定细胞浓度,细胞干重,虾青素产量。
62.发酵罐发酵:发酵采用5l发酵罐培养,接种量5-10%,25℃,500rpm培养72小时,发酵过程中根据需求控制适当的温度和相对溶解氧浓度。培养至残留葡萄糖降至0.1g/l以下结束发酵。
63.虾青素产量(mg/l)测定:10ml发酵液离心收集菌体,水洗一次,收集菌体,加入所取发酵液2-3ml的3mol/l盐酸溶液,震荡均匀,浸泡25~35min,沸水浴10分钟,冰浴降温;离心去除盐酸溶液,细胞碎片沉淀水洗一次,然后加入3ml丙酮震荡浸提2次,离心收集上清液,476nm处测量吸光度,根据虾青素标准曲线计算样品中虾青素的含量,然后根据稀释倍数计算发酵液虾青素产量。
64.细胞干重测定:10ml发酵液离心收集菌体,水洗一次,收集菌体,干燥后称重。
65.实验结果
66.1碳源对红法夫酵母生长和虾青素产量的影响
67.分别用蔗糖、果糖、麦芽糖、甘油、果葡糖浆、麦芽糊精和可溶性淀粉替换葡萄糖添加到基础培养基中,不同碳源培养红法夫酵母产虾青素结果如图1所示。
68.由图1可以看出蔗糖对红法夫酵母生长和虾青素的合成最为有利,葡萄糖、麦芽
糖、果糖、果葡糖浆也都是比较合适的氮源。红法夫酵母不能直接利用淀粉。
69.2氮源对红法夫酵母生长和虾青素产量的影响
70.以40g/l葡萄糖为碳源,对氮源种类进行了实验。选用浓度为2g/l的牛肉膏、蛋白胨、尿素、玉米浆、酵母粉作为单一氮源,对菌体干重和虾青素含量进行测定,结果如图2所示。结果显示在相同浓度下,酵母粉对红法夫酵母的生长和虾青素的合成最为有利,玉米浆、牛肉膏、蛋白胨、尿素对红法夫酵母的生长影响相对较小,但虾青素产量比酵母浸粉明显降低。
71.3甘薯培养基质培养红法夫酵母结果
72.3.1摇瓶实验结果
73.上述用甘薯制备的各种培养基质,调整淀粉糖浓度至4%(淀粉糖含量高的样品适当加水稀释,淀粉糖浓度低的适量补加麦芽糖),添加或不添加酵母浸粉,用上述发酵培养基为对照进行红法夫酵母发酵生产虾青素试验,考察甘薯来源的培养基质对红法夫酵母发酵生产虾青素的影响。结果见表1。
74.表1培养基质对红法夫酵母发酵生产虾青素的影响
[0075][0076][0077]
试验结果显示,采用甘薯来源的培养基质,不添加酵母浸粉,细胞干重和虾青素产量略低于对照组,如果添加与对照培养基相同浓度的酵母浸粉(2g/l),菌体浓度和虾青素产量都明显优于对照培养基。基质ⅰ、ⅱ、ⅳ、
ⅴ
菌体量和虾青素产量区别不显著,基质ⅲ相较其他集中基质,细胞干重和虾青素产量都偏低。基质ⅲ制备过程中没有淀粉分离过程,基质中还原糖的比例明显高于其他4种基质,其他营养成分的比例相对降低。采用富含β-胡萝卜素的橙心甘薯制备甘薯培养基质(基质ⅱ)与淀粉加工用甘薯品种制备的培养基质(基质
ⅰ
)相比对红法夫酵母其虾青素产量没有观察到促进作用。
[0078]
3.2发酵罐批次发酵实验结果
[0079]
取培养基质ⅳ(淀粉糖浓度4.8%)添加2g/l酵母浸粉配制发酵培养基,10%的接种量,5l发酵罐培养,搅拌转速500rpm,通气比1:0.3,培养温度25℃。培养过程中定时取样测定细胞干重、虾青素产量和总糖浓度,结果如图3。采用发酵罐分批发酵,耗糖速度和细胞生长速度都比摇瓶培养要快,发酵结束时菌体量和虾青素产量都高于摇瓶培养。
[0080]
3.3发酵罐批次发酵分批补料发酵实验结果
[0081]
取培养基质ⅳ(调整淀粉糖浓度4.0%)添加2g/l酵母浸粉配制发酵培养基,10%的接种量,5l发酵罐培养,搅拌转速500rpm,通气比1:0.3,培养温度25℃。培养至36小时、48小时、60小时、72小时、84小时、96小时、120小时分别补加培养基质
ⅴ
50ml,同时培养过程中定时取样测定细胞干重、虾青素产量和总糖浓度,发酵进程如图4。结果表明,补料发酵可以大幅提升发酵液中菌体浓度和虾青素的产量。72小时以前,细胞浓度和虾青素产量增加较快,72小时后增长速度趋缓,虾青素产量96小时达到最高(18mg/l),96小时以后细胞浓度仍有所增加,但虾青素产量却有所下降。并且96小时以后耗糖几乎停滞,细胞干重略有增加,最高达到52.3g/l。
[0082]
3.4发酵罐批次发酵连续补料发酵实验结果
[0083]
取培养基质ⅳ(调整淀粉糖浓度4.0%)添加2g/l酵母浸粉配制发酵培养基,10%的接种量,5l发酵罐培养,搅拌转速500rpm,通气比1:0.3,培养温度25℃。培养至36小时采用连续流加培养基质
ⅴ
至72小时结束,总计补料200ml,同时培养过程中定时取样测定细胞干重、虾青素产量和总糖浓度,发酵进程如图5。结果表明,采用连续补料发酵过程更加平稳,基质利用率提高,96小时结束发酵,发酵液中残糖浓度低,菌体浓度和虾青素的产量都比分批补料有所提高(细胞干重达54.4g/l,虾青素产量达21.9mg/l),取得了非常好的效果。
[0084]
4葡萄糖为碳源连续补料发酵实验结果(连续补料发酵对照实验)
[0085]
发酵培养基(g/l):葡萄糖40,酵母浸粉2,硫酸铵0.5,磷酸二氢钠1.5,磷酸氢二钠1.5,硫酸镁0.2,自来水配制,ph自然。
[0086]
补料(g/l):葡萄糖500,酵母浸粉5。
[0087]
按上述配方配制发酵培养基,10%的接种量,5l发酵罐培养,搅拌转速500rpm,通气比1:0.3,培养温度25℃。培养至36小时采用连续流加方式补料至72小时结束,总计补料160ml,同时培养过程中定时取样测定细胞干重、虾青素产量和总糖浓度,发酵进程如图6。结果表明,采用对照培养基(葡萄糖为碳源)采用与甘薯基质相似的补料策略(连续补料),补料后葡萄糖消耗速率相对较慢,补料过程中料液中的糖浓度持续增加,96小时时发酵液残糖浓度仍然较高,菌体浓度和虾青素的产量都比甘薯基质差距显著(细胞干重23.5g/l,虾青素产量11.5mg/l)。
[0088]
上述实施例只为说明本发明的技术构思及特点,其目的在于让熟悉此项技术的人士能够了解本发明的内容并据以实施,并不能以此限制本发明的保护范围。凡根据本发明精神实质所作的等效变化或修饰,都应涵盖在本发明的保护范围之内。