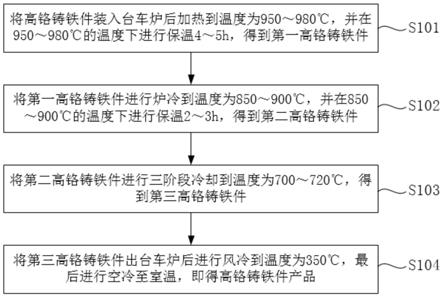
1.本发明实施例涉及铸铁件热处理技术领域,尤其涉及一种高铬铸铁件的热处理方法。
背景技术:
2.高铬铸铁具有较高的铬含量、良好的硬度、耐磨性以及抗氧化性,被广泛应用于生产各种磨料磨损、高温磨损和腐蚀磨损的工况设备,例如流体压力执行机构的灰渣泵、渣浆泵和泥浆泵。叶轮作为渣浆泵、灰渣泵和泥浆泵的主要部件,其在作业中因承担泥浆、砂石等的冲蚀作用,导致其很容易发生磨损失效,因而需要使用高铬铸铁为原料生产叶轮以延长其使用寿命。
3.高铬铸铁的材料热传导速率比较差,如果在正火冷却时按照硬化标准920~980℃进行保温,以及在保温后直接进行空冷,很容易导致叶轮内、外部的温度降低不一致,特别是叶轮外部的温度很快降低至ms点时内部温度仍然保持在很高的水平,从而造成叶轮外部马氏体转变完成后内部才开始转变,外部需要承受内部组织转变引起的体积膨胀产生的拉应力,当该拉应力超过高铬铸铁材料的抗拉强度时,即会产生开裂问题,造成重大的生产成本损失。鉴于此,公布号为cn 112813243 a公开了一种疏浚行业大型高铬铸铁件叶轮产品热处理工艺以解决叶轮内、外部降温不均衡的问题,具体是将高铬叶轮进行六阶段加热到温度为淬火温度900~980℃后,根据壁厚不同在淬火温度保温6~12h,然后进行针对叶轮厚大区域加风的空冷以降温至550℃,并在550℃的温度下进行保温和均温,以及再分四个阶段进行缓冷,每阶段按设定冷却曲线进行,不同阶段冷却时间2~4h不等,待降温至120℃后再次空冷至常温。
4.但是,以上所述的热处理工艺存在以下缺点:一是高铬铸铁叶轮在550℃的炉内均温后进行四个阶段的缓冷,不同阶段的冷却时间为2~4h不等,冷却速度过于缓慢,热处理效率低且叶轮在550~350℃的温度区间范围内产生上贝氏体组织,从而造成叶轮产品的硬度降低,脆性增大,后期使用过程容易出现开裂的风险;二是降温过程的工艺操作繁琐,不便于工人控制;三是针对厚大区域吹风强制冷却的操作不易控制,需要特殊设备予以实现,增加了生产成本。
技术实现要素:
5.本发明实施例的目的在于提供一种高铬铸铁件的热处理方法,用以解决现有热处理工艺造成的高铬铸铁叶轮产品硬度降低、脆性增大、易发生开裂、成品率低以及降温工艺操作繁琐且设备功能要求高的技术问题。
6.为了实现上述目的,本发明实施例的技术方案是:
7.本发明实施例提供了一种高铬铸铁件的热处理方法,包括以下步骤:
8.将高铬铸铁件装入台车炉后加热到温度为950~980℃,并在950~980℃的温度下进行保温4~5h,得到第一高铬铸铁件;
9.将所述第一高铬铸铁件进行炉冷到温度为850~900℃,并在850~900℃的温度下进行保温2~3h,得到第二高铬铸铁件;
10.将所述第二高铬铸铁件进行三阶段冷却到温度为700~720℃,得到第三高铬铸铁件,其中,所述三阶段冷却过程依次为:开启台车炉门至其开度的1/4进行第一阶段冷却到温度为790~810℃,时间为20min;开启台车炉门至其开度的1/3进行第二阶段冷却到温度为710~750℃,时间为20min;开启台车炉门至其开度的2/3进行第三阶段冷却到温度为700~720℃,时间为10min;以及
11.将所述第三高铬铸铁件出台车炉后进行风冷到温度为350℃,最后进行空冷至室温,即得高铬铸铁件产品。
12.在本发明实施例的优选实施方式中,所述加热到温度为950~980℃包括五阶段升温过程,所述五阶段升温过程依次为:
13.以30~40℃/h的升温速度加热到温度为200~260℃后保温2~3h;以30~40℃/h的升温速度加热到温度为350~400℃后保温2~3h;以50~60℃/h的升温速度加热到温度为600~680℃后保温3~4h;以50~60℃/h的升温速度加热到温度为800~850℃后保温3~4h;以65~75℃/h的升温速度加热到温度为950~980℃。
14.在本发明实施例的优选实施方式中,所述炉冷过程中的降温速度为65~75℃/h
15.在本发明实施例的优选实施方式中,所述风冷过程中的降温速度为55~75℃/h。
16.在本发明实施例的优选实施方式中,所述空冷至室温后还包括回火过程,所述回火过程依次为:
17.将所述高铬铸铁件产品以30~40℃/h的升温速度加热到温度为160~180℃后保温4~6h;以50~60℃/h的升温速度加热到温度为250~280℃后保温6~10h;以及最后空冷至室温。
18.在本发明实施例的优选实施方式中,所述高铬铸铁件的硬度≥55hrc,上下偏差≤4hrc。
19.在本发明实施例的优选实施方式中,所述大型高铬铸铁件的表面残余应力为-300~-100mpa。
20.在本发明实施例的优选实施方式中,所述高铬铸铁件的冲蚀率≤0.153mg/g。
21.在本发明实施例的优选实施方式中,所述高铬铸铁件为大型高铬铸铁叶轮。
22.在本发明实施例的优选实施方式中,所述大型高铬铸铁叶轮随炉试样规格尺寸为150mm
×
120mm
×
120mm。
23.与现有技术相比,本发明实施例的优点或有益效果至少包括:
24.本发明实施例提供的高铬铸铁件的热处理方法,其包括将高铬铸铁件加热到950~980℃的温度时进行保温4~5h;炉冷到850~900℃的温度时进行保温2~3h;以及依次进行三阶段冷却到温度为700~720℃、风冷到温度为350℃和空冷到室温。因此,本发明实施例一方面将高铬铸铁件在950~980℃的温度下保温4~5h后,炉冷到850~900℃的温度进行保温2~3h,随后通过三阶段冷却到温度为700~720℃,不仅可以明显地缓解较大过渡冷,从而防止高铬铸铁件在较高温区冷却中发生开裂,而且较高温区的冷却过程均在台车炉内进行,便于工人控制且简化了操作程序。另一方面在三阶段冷却到700~720℃的温度后进行风冷到温度为350℃,不仅能够降低高铬铸铁件发生珠光体转变,从而更有利于高铬
铸铁件发生马氏体转变,而且明显缩短了冷却时间,加快了冷却过程,实现了生产效率的提高。另外,本发明实施例的冷却过程中不再需要针对厚大区域进行吹风强制冷却,因而不必购买专用正火风冷设备,具有易于实现,且设备要求低、成本低的优点。
25.金相组织检测结果表明,本发明实施例提供的热处理方法不仅有利于将共晶奥氏体转变为针状的马氏体,而且有利于析出尺寸细小的二次碳化物颗粒以及较少的残余奥氏体;产品性能检测结果表明,本发明实施例热处理后的大型高铬铸铁叶轮的硬度>55hrc以上,且硬度分布均匀,上下偏差≤4hrc,没有发生开裂现象;冲蚀率≤0.153mg/g,在具有较高耐磨性的同时产品的成品率达到100%。
附图说明
26.为了更清楚地说明本发明的技术方案,下面将对实施例描述中所需要使用的附图作简单地介绍。显而易见地,下面描述中的附图仅是本技术中记载的一些实施例,对于本领域普通技术人员来讲,在不付出创造性劳动的前提下,还可以根据这些附图获得其他的附图。
27.图1为本发明实施例提供的高铬铸铁件的热处理方法的工艺流程图;
28.图2为本发明实施例提供的大型高铬铸铁叶轮产品的金相组织图;
29.图3为本发明实施例提供的大型高铬铸铁叶轮产品在冲蚀速率为100m/s下的冲蚀率柱状图。
具体实施方式
30.下面将结合本发明实施例,对本发明实施例中的技术方案进行清楚、完整地描述。显然,以下所描述的实施例只是本技术一部分实施例,而不是全部的实施例。基于本技术中的实施例,本领域普通技术人员在没有做出创造性劳动前提下所获得的所有其他实施例,都属于本发明实施例保护的范围。
31.本实施例提供一种高铬铸铁件的热处理方法,解决了现有热处理工艺造成的高铬铸铁叶轮产品硬度降低、脆性增大、易发生开裂、成品率低以及降温工艺操作繁琐且设备功能要求高的技术问题。请参照图1至图3。其中,图1为本实施例提供的高铬铸铁件的热处理方法的工艺流程图;图2为本实施例提供的大型高铬铸铁叶轮产品的金相组织图;图3为本实施例提供的大型高铬铸铁叶轮产品在冲蚀速率为100m/s下的冲蚀率柱状图。
32.如图1所示,该高铬铸铁件的热处理方法包括以下步骤。
33.s101:将高铬铸铁件装入台车炉后加热到温度为950~980℃,并在950~980℃的温度下进行保温4~5h,得到第一高铬铸铁件;
34.s102:将所述第一高铬铸铁件进行炉冷到温度为850~900℃,并在850~900℃的温度下进行保温2~3h,得到第二高铬铸铁件;
35.s103:将所述第二高铬铸铁件进行三阶段冷却到温度为700~720℃,得到第三高铬铸铁件,其中,所述三阶段冷却过程依次为:开启台车炉门至其开度的1/4进行第一阶段冷却到温度为790~810℃,时间为20min;开启台车炉门至其开度的1/3进行第二阶段冷却到温度为710~750℃,时间为20min;开启台车炉门至其开度的2/3进行第三阶段冷却到温度为700~720℃,时间为10min;
36.s104:将所述第三高铬铸铁件出台车炉后进行风冷到温度为350℃,最后进行空冷至室温,即得高铬铸铁件产品。
37.本领域技术人员应当理解,本发明实施例所述的三阶段冷却中,所述第三阶段冷却到的最高温度应当低于所述第二阶段冷却到的最低温度,同时本发明实施例中所述的温度均是在高铬铸铁件的同一部位测得的数值。
38.需要说明的是,本发明实施例的高铬铸铁件的热处理方法的机理是:高铬铸铁件的标准硬化处理温度为920~980℃,因而在这一温度区间进行保温2~6h后的高铬铸铁件的组织由奥氏体+部分未熔融共晶m7c3组成。而为了使高铬铸铁件获得较高的硬度,在冷却时需要相对较快的降温速度以期在冷却相变后获得较多的弥散的二次碳化物和马氏体,但过大的过冷度会造成高铬铸铁件不同部位的冷却程度不一致,当相变发生不同时会产生较大的内应力,最终导致高铬铸铁件产品开裂倾向性增大。同时,高铬铸铁材料的相变点accm接近810~830℃,ar1接近690~710℃,arm接近710~730℃,ms接近150~170℃,msf接近0℃甚至以下。但是,发明人在大型高铬铸铁件的热处理研究中发现,当高铬铸铁件在950~980℃的温度下保温4~5h后,通过炉冷到温度为850~900℃并保温2~3h,能够明显缓解较大过冷度,同时在炉冷过程中通过控制降温速度为65~75℃/h,能够使高铬铸铁件产品的各部位温度更一致,而且在850~900℃至arm临界温度区间时适当增加冷却速度并分三个阶段进行冷却到温度为700~720℃,以及在ar1以下进行风冷到温度为350℃后空冷至室温,能够促使内应拉力分布更均匀,从而实现大型高铬铸铁件产品硬度的增加和脆性的降低。另外,在风冷到温度为350℃以后进行空冷,放缓了冷却速度,从而防止低温下冷却速度过快而产生较大的组织转变应力,防止了开裂。
39.需要说明的是,本发明实施例中的三阶段冷却的具体过程包括:第一高铬铸铁件在850~900℃的温度下保温2~3h后,开启台车炉门至其开度的1/4并松开侧密封装置,同时台车开出距离为150~200mm,冷却时间为20min后测量危险截面处温度为790~810℃,即完成第一阶段冷却;开启台车炉门至其开度的1/3并松开侧密封装置,冷却时间为20min后测量危险截面处温度为710~750℃,即完成第二阶段冷却;开启台车炉门至其开度的2/3并松开侧密封装置,冷却时间为20min后测量危险截面处温度为700-720℃,即完成第三阶段降温。
40.当然,本领域技术人员应当理解,本发明实施例依次所述开启炉门至其相应开度只是根据本实施例中涉及的随炉规格尺寸(150mm
×
120mm
×
120mm)优选的一种选择方式,并不是针对所有随炉规格尺寸的特定限制,凡是能够在相应时间内实现相应的降温需求的炉门开启开度均可,本实施例对此不作限定。另外,本实施例对台车炉的具体型号不作特别限定,以满足相应的降温需求为准。
41.基于以上描述可知,本发明实施例提供的高铬铸铁件的热处理方法通过在950~980℃的温度下保温4~5h后炉冷到850~900℃的温度进行保温2~3h,并在850~900℃至arm临界温度区间内采用适当增加冷却速度的三阶段冷却方式,以及在ar1以下进行风冷至温度为350℃后空冷至室温,不仅明显缓解了过快冷却造成的较大过渡冷,而且使高铬铸铁件产品各部位温度的一致性更好,从而实现了高铬铸铁件产品硬度的增加和脆性的降低。同时,本发明实施例炉冷及保温后进行的三阶段的冷却所用时间最多为65min,相比于现有技术的四阶段长时间缓冷明显加快了降温程序,大幅提高了生产效率,而且本发明实施例
的三阶段降温过程及其以前的所有降温过程均在台车炉内进行,只需要简单配合炉门开启开度的设定即可,大大简化了降温工艺的操作程序且便于工人控制。另外,本实施例提供高铬铸铁件的热处理方法在整个降温程序中不再需要针对厚大区域进行吹风强制冷却,因而不必购买专用正火风冷设备,具有易于实现,且设备要求低、成本低的优点。
42.在本实施例中,所述将高铬铸铁件加热到温度为950~980℃包括五阶段升温过程,所述五阶段升温过程依次是:
43.以30~40℃/h的升温速度加热到温度为200~260℃,保温2~3h;
44.以30~40℃/h的升温速度加热到温度为350~400℃,保温2~3h;
45.以50~60℃/h的升温速度加热到温度为600~680℃,保温3~4h;
46.以50~60℃/h的升温速度加热到温度为800~850℃,保温3~4h;
47.以65~75℃/h的升温速度加热到温度为950~980℃。
48.需要说明的是,高铬铸铁材料的热传导速率较为缓慢,过快升温容易造成大型高铬铸铁件内、外部温度不均匀,导致奥氏体化不完全。因此,本实施例采用五阶段升温的升温方式,使各个相变阶段的大型高铬铸铁件内、外部的温度相一致,减少了开裂的倾向性。
49.在本实施例中,所述炉冷过程中的降温速度为65~75℃/h,不仅能够缓解过快冷却造成的较大过渡冷,而且能够使高铬铸铁件产品各部位的温度更均匀一致,从而实现了大型高铬铸铁件产品硬度的增加和脆性的降低。
50.在本实施例中,所述风冷过程中的降温速度为55~75℃/h,以防止过快降温造成的过渡冷和过慢降温造成的大型高铬铸铁件产品的硬度降低,脆性增大以及后期使用过程容易出现开裂的问题。具体地,本实施例在三阶段降温至温度为700~720℃后进行风冷并控制风冷降温速度为55~75℃/h,不仅避免过快降温造成的大型高铬铸铁件产品内、外部降温程度不一致的问题,而且能够解决过慢降温造成的大型高铬铸铁件产品的硬度降低,脆性增大以及后期使用过程容易出现开裂的问题。
51.在本实施例中,所述空冷至室温后还包括回火过程,所述回火过程依次是:
52.将所述高铬铸铁件产品以30~40℃/h的升温速度加热到温度为160~180℃后保温4~6h;以50~60℃/h的升温速度加热到温度为250~280℃后保温6~10h;以及最后空冷至室温。
53.需要说明的是,本实施例在正火冷却程序完成后还进行回火控制,促使残余奥氏体分解为过饱和的α+ε碳化物。
54.下面将结合具体实施例对本发明实施例的技术方案作详细阐述。
55.实施例1
56.本实施例1提供一种高铬铸铁件的热处理方法,其中,所述高铬铸铁件为中钢集团西安重机有限公司生产的大型高铬铸铁叶轮,重量≥12吨,危险截面尺寸为60~170mm不等。
57.具体地,该热处理方法包括以下步骤:
58.取高铬铸造叶轮及其浇筑后的本体切割随炉试样(尺寸规格为150mm
×
120mm
×
120mm),检查无探伤缺陷后,装炉支垫平稳后进入台车炉,试样放置于叶轮上端,随后加热到温度为950~980℃,并在950~980℃的温度下保温4~5h,得到第一大型高铬铸铁叶轮。其中,加热过程分为五个阶段,依次是在升温速度为30~40℃/h下加热到温度为350~400
℃后保温2~3h;在升温速度为50~60℃/h下加热到温度为600~680℃后保温3~4h;在升温速度为50~60℃/h下加热到温度为800~850℃后保温3~4h;以及在升温速度为65~75℃/h下加热到温度为950~980℃。
59.将所述第一大型高铬铸铁叶轮以65~75℃/h的降温速度炉冷到温度为850~900℃,并在850~900℃的温度下保温2~3h,停止升温,得到第二大型高铬铸铁叶轮。
60.将所述第二大型高铬铸铁叶轮进行三阶段冷却,得到第三大型高铬铸铁叶轮,其中,三阶段冷却过程依次为:
61.首先,开启台车炉的1/4炉门并松开侧密封装置,台车开出距离为150~200mm,以使大型高铬铸铁叶轮在20min的时间区间降低至790~810℃;
62.其次,开启台车炉的炉门至开度的1/3处并松开侧密封装置,以使大型高铬铸铁叶轮继续在20min的时间区间降低至710~750℃;
63.最后,开启台车炉的炉门至开度的2/3处并松开侧密封装置,以使高铬铸铁叶轮继续在10min降温,测量其温度约700~720℃后拉出台车。
64.本实施例分别检测了大型高铬铸铁叶轮下侧(标记
①
)、内腔右侧(标记
②
)、内腔左侧(标记
③
)和上侧(标记
④
)处在所述三阶段冷却过程中的温度,详见表1所述。
65.表1~高铬铸铁叶轮在三阶段降温程序的温度分布
[0066][0067]
通过表1可以看出,本实施例在800~850℃的温度下保温3~4h后分三个阶段进行冷却,明显使大型高铬铸铁叶轮各部位的温度更均匀,从而能够降低温变应力,有效防止大型高铬铸铁叶轮在早期发生开裂。
[0068]
将所述大型高铬铸铁叶轮从台车炉中拉出,在风机配合下以降温速度为55~75℃/h下进行风冷到温度为350℃;
[0069]
出炉空冷至室温,即完成正火冷却过程;
[0070]
将冷却到室温的大型高铬铸造叶轮装炉,随炉进行升温回火,所述升温回火依次是:首先在升温速度为30~40℃/h下加热到温度为160~180℃,保温4~6h,然后在升温速度为50~60℃/h下升温250~280℃,保温6~10h,最后出炉空冷至室温。
[0071]
检查硬度、探伤、组织和冲蚀试验合格,即得大型高铬铸造叶轮产品。
[0072]
为了验证本实施例提供的热处理方法的实际效果,本发明实施例人研究了热处理后大型高铬铸造叶轮产品的各项性能。
[0073]
1.本实施例研究了该大型高铬铸造叶轮产品的硬度指数,结果详见下表2。
[0074]
表2~大型高铬铸造叶轮产品的硬度分布图
[0075][0076]
通过表2可以看出,本实施例提供的热处理方法生产的大型高铬铸造叶轮产品的硬度达到hrc55以上,而且各部位的硬度分布比较均匀,上下偏差不大于4hrc。
[0077]
2.本实施例研究了该大型高铬铸造叶轮产品的金相组织,如图2所示。其中,图2示出了该大型高铬铸造叶轮产品在1000倍目镜下显微组织。
[0078]
通过图2可以看出,该大型高铬铸造叶轮产品中高度共晶的网状碳化物已经断网,析出了尺寸较为细小的二次碳化物颗粒,共晶奥氏体转变为针状的马氏体和较少的残余奥氏体。
[0079]
3.本实施例研究了该大型高铬铸造叶轮产品各部位的应力指数,结果详见下表3。
[0080]
表3~应力检测测试结果
[0081][0082]
通过表3可以看出,本实施例提供的热处理方法生产的大型高铬铸造叶轮产品的应力分布较为均匀。
[0083]
3.本实施例研究了大型高铬铸造叶轮产品的抗冲蚀性能,结果详见表4和图3。其中,图3示出了冲蚀速率为100m/s下的冲蚀率。
[0084]
表3~冲蚀速率为100m/s固体颗粒直径为120μm下的冲蚀率
[0085][0086]
通过表3和图3可以看出,本实施例提供的热处理方法生产的大型高铬铸造叶轮产品的在冲蚀角度为90
°
时,冲蚀率最高为0.153mg/g,在冲蚀角度为60
°
时,冲蚀率最低为0.099mg/g,在冲蚀角度为30
°
时,冲蚀率为0.127mg/g。因此,本实施例提供的热处理方法生产的大型高铬铸造叶轮产品的抗冲蚀性能良好,冲蚀率≤0.153mg/g。
[0087]
综合以上描述可知,本发明实施例提供的高铬铸铁件的热处理方法通过在950~
980℃的温度下保温后再炉冷到温度为850~900℃保温2~3h,以及在第二次保温后依次进行三阶段的控制降温速度的降温(第一阶段降温到790~810℃,时间20min;第二阶段降温到710~750℃,时间为20min;第三阶段降温到700~720℃,时间为10min)、风冷至温度为350℃和空冷至室温,不仅能够大幅缓解较大过渡冷并解决高铬铸铁件产品各部分的温度均匀一致的问题,而且明显加快了降温程序,实现时间成本的降低,同时三阶段降温程序及其以前的所有降温程序均在炉内进行,简化了降温工艺的操作程序以便于工人控制。另外,整个降温程序中不再需要针对厚大区域进行吹风强制冷却,因而不必购买专用正火风冷设备,具有易于实现,且设备要求低、成本低的优点。特别重要的是,本发明实施例提供的高铬铸铁件的热处理方法能够在较快降温的前提下,既实现了大型高铬铸铁件产品的硬度达到55hrc以上且硬度分布均匀,上下偏差不大于4hrc,没有发生开裂现象;又实现了大型高铬铸铁件产品的冲蚀率≤0.153mg/g,以及实现大型高铬铸铁件产品的成品率达到100%。
[0088]
对于本领域技术人员而言,显然本发明实施例不限于上述示范性实施例的细节,而且在不背离本发明实施例的精神或基本特征的情况下,能够以其他的具体形式实现本发明实施例。因此,无论从哪一点来看,均应将实施例看作是示范性的,而且是非限制性的,本发明实施例的范围由所附权利要求而不是上述说明限定,因此旨在将落在权利要求的等同要件的含义和范围内的所有变化囊括在本发明实施例内。