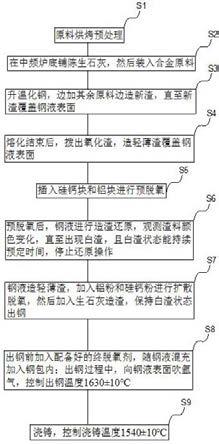
1.本发明涉及不锈钢技术领域,尤其涉及一种超级奥氏体不锈钢的冶炼工艺及铸管的制备工艺。
背景技术:
2.超级奥氏体不锈钢是一种合金含量(铬、钼、镍、氮等)显著高于普通奥氏体不锈钢的奥氏体合金,在海水、高浓度氯离子介质等极端恶劣的服役环境中具有优异的耐点蚀、耐缝隙腐蚀和耐应力腐蚀性能,被广泛应用于海水脱盐处理系统、纸浆漂白系统、湿法冶金设备等领域。
3.现有技术中,超级奥氏体不锈钢冶炼时大多采用预转炉或电炉冶炼与aod炉或vod炉精炼。工序较为繁琐,同时得到超级奥氏体不锈钢内部存在夹渣缺陷。
技术实现要素:
4.本发明为解决现有技术中超级奥氏体不锈钢冶炼时存在工序较为繁琐、夹渣缺陷的问题,提供一种超级奥氏体不锈钢的冶炼工艺及铸件的制备工艺,于中频炉内完成熔化和精炼过程,简化工序,同时通过渣料过程覆盖钢液表面,避免产生夹渣缺陷。
5.本发明采用的技术方案是:超级奥氏体不锈钢的冶炼工艺,所述冶炼工艺包括以下步骤:步骤s1,原料烘烤预处理;步骤s2,在中频炉底铺陈生石灰,然后装入合金原料;步骤s3,升温化钢,边加其余原料边造新渣,直至新渣覆盖钢液表面;步骤s4,熔化结束后,拨出氧化渣,造轻薄渣覆盖钢液表面;步骤s5,插入硅钙块和铝块进行预脱氧;步骤s6,预脱氧后,钢液进行造渣还原,观测渣料颜色变化,直至出现白渣,且白渣状态能持续预定时间,停止还原操作;步骤s7,钢液造轻薄渣,加入铝粉和硅钙粉进行扩散脱氧,然后加入生石灰造渣,保持白渣状态出钢;步骤s8,出钢前加入配备好的终脱氧剂,随钢液混充加入钢包内;出钢过程中,向钢液表面吹氩气,控制出钢温度1630
±
10℃;步骤s9,浇铸,控制浇铸温度1540
±
10℃。
6.进一步地,所述步骤s2中,生石灰用量为钢液总量的3
‰
。
7.进一步地,所述步骤s5中,控制钢液中铝含量小于0.01%,硅钙块按照0.5kg/t加入,控制块度≤50mm。
8.进一步地,所述步骤s8中,终脱氧剂为硅钙钡和硅钙块的混合物,硅钙钡按钢液总量的1~1.5kg/t加入,硅钙块按0.5kg/t加入。
9.进一步地,所述步骤s8中,出钢时,渣液应控制在钢液总量的10~15
‰
。
10.进一步地,所述步骤s8中,出钢时分批加入铈。
11.进一步地,铈的加入总重量为钢液总量0.8wt
‰
。
12.进一步地,所述步骤s9中,浇铸前,钢液静置3~5min。
13.基于同样的发明构思,本发明中还提供一种铸管的制备工艺,合金原料经前述超级奥氏体不锈钢的冶炼工艺后,离心浇铸,得到铸管。
14.进一步地,离心浇铸时采用以下步骤:步骤s91,型筒准备,并对型筒进行预处理;步骤s92,型筒喷涂,控制喷涂温度220~250℃,喷涂厚度1.5~2.0mm;步骤s93,浇铸前10min,向型筒内充入氩气或者二氧化碳;步骤s94,设置离心机工作参数;步骤s95,浇铸,并采用氩气保护,浇铸时型筒温度80~100℃。
15.本发明的有益效果是:1.本发明为解决现有技术中超级奥氏体不锈钢冶炼时存在工序较为繁琐、夹渣缺陷的问题,提供一种超级奥氏体不锈钢的冶炼工艺。该冶炼工艺中过包括装炉、化钢、预脱氧、还原、出钢造渣、终脱氧、出钢、浇铸等步骤。超级奥氏体不锈钢的冶炼过程均在中频炉内完成,省去了转炉精炼过程,简化了工序。同时也降低了转炉过程中由于增加了钢水与空气的接触时间导致夹渣缺陷的可能性。同时,通过一系列的造渣过程中,充分利用白渣的吸渣能力,充分吸出钢液中的杂质,进一步保证了超级奥氏体不锈钢的质量。
16.2. 本发明提供一种铸管的制备工艺,超级奥氏体不锈钢的冶炼于一个中频炉内完成熔炼和精炼过程,同时冶炼过程中通过多次渣料,利用泡沫化的渣料吸收钢液中的杂质,同时渣料覆盖在钢液表面,隔绝了空气,避免钢液二次氧化,避免最终的铸管产生夹渣缺陷,保证了产品的质量。
附图说明
17.为了更清楚地说明本技术实施例或现有技术中的技术方案,下面将对实施例或有现技术描述中所需要使用的附图作简单地介绍,显而易见地,下面描述中的附图仅仅是本技术的一些实施例,对于本领域普通技术人员来讲,在不付出创造性劳动的前提下,还可以根据这些附图获得其他的附图。
18.图1为实施例1中,冶炼工艺的流程图。
具体实施方式
19.下文的公开提供了许多不同的实施方式或例子用来实现本发明的不同结构。为了简化本发明的公开,下文中对特定例子的部件和设置进行描述。当然,它们仅仅为示例,并且目的不在于限制本发明。
20.下面结合附图对发明的实施例进行详细说明。
21.实施例1本实例中提供一种超级奥氏体不锈钢的冶炼工艺,该超级奥氏体不锈钢的成分如下表所示:
成分csimnpsnicrmocual
%≤0.020.6~0.81.5~1.8≤0.035≤0.0124.3~24.722.3~22.84.1~4.31.1~1.3≤0.02
该冶炼工艺包括以下步骤,如附图1中所示:步骤s1,原料烘烤预处理。
22.合金原料烘烤处理,烘烤温度600℃,保温4h;石灰、萤石、硅钙钡、硅钙块、铝粉等造渣脱氧剂烘烤处理,烘烤温度200℃,保温2h。
23.原料经烘烤后入炉,可以减小水分对冶炼的影响。
24.步骤s2,在中频炉底铺陈生石灰,然后装入合金原料。
25.其中,生石灰用量为钢液总量的3
‰
。
26.熔化期钢液要吸收气体,气体随钢液温度升高,溶解度越大,为减少钢液吸气量,炼钢前在炉底加入钢液总量3
‰
的生石灰打底,以减少钢液吸气。
27.步骤s3,升温化钢,边加其余原料边造新渣,直至新渣覆盖钢液表面。
28.一方面新渣会吸收钢液中的杂质,另一方面,新渣覆盖在钢液表面,可以隔绝空气,避免钢液被二次氧化。
29.步骤s4,熔化结束后,拨出氧化渣,造轻薄渣覆盖钢液表面。
30.步骤s5,插入硅钙块和铝块进行预脱氧。
31.其中,控制钢液中铝含量小于0.01%,硅钙块按照0.5kg/t加入,控制块度≤50mm。
32.步骤s6,预脱氧后,钢液进行造渣还原,观测渣料颜色变化,直至出现白渣,且白渣状态能持续预定时间比如10~15min,停止还原操作。
33.预脱氧后,进行造渣还原操作,根据渣样颜色判断,渣样依次呈黑色
→
棕色
→
绿色
→
黄色
→
淡黄色
→
白色,钢液在还原期可能随着合金加入熔化后产生的新渣及钢液内部夹杂物析出到渣液内,破坏已经造好的白渣渣系,所以造白渣不仅仅只是渣样呈白色即可,而是在还原期末,必须保持白渣状态,持续10-15min。渣的颜色变化是说明钢液脱氧好坏的关键,在现场无其他的手段无法在立即检出氧含量,以此过程来控制,可以简化控制手段,保证钢液质量。白渣状态的钢水,说明钢水脱氧已经很好,说明因此控制白渣出钢是最好的。
34.步骤s7,钢液造轻薄渣,加入铝粉和硅钙粉进行扩散脱氧,然后加入生石灰造渣,保持白渣状态出钢。
35.步骤s8,出钢前加入配备好的终脱氧剂,随钢液混充加入钢包内;出钢过程中,向钢液表面吹氩气,控制出钢温度1630
±
10℃,渣液应控制在钢液总量的10~15
‰
。
36.为了铸件的晶粒尺寸,可以在出钢时分批加入铈,铈的加入总重量为钢液总量0.8wt
‰
。通过加入稀土铈,可以细化晶粒,加速渣料上浮。
37.步骤s9,浇铸,控制浇铸温度1540
±
10℃。
38.为了使钢液排气,浇铸前,钢液静置3~5min。
39.本实施例中,超级奥氏体不锈钢的冶炼过程均在中频炉内完成,省去了转炉精炼过程,简化了工序。同时也降低了转炉过程中由于增加了钢水与空气的接触时间导致夹渣缺陷的可能性。同时,通过一系列的造渣过程中,充分利用白渣的吸渣能力,充分吸出钢液中的杂质,进一步保证了超级奥氏体不锈钢的质量。
40.实施例2铸管的制备工艺,其包括以下步骤:
步骤s1,原料烘烤预处理。
41.步骤s2,在中频炉底铺陈生石灰,生石灰用量为钢液总量的3
‰
,然后装入合金原料。
42.步骤s3,升温化钢,边加其余原料边造新渣,直至新渣覆盖钢液表面。
43.步骤s4,熔化结束后,拨出氧化渣,造轻薄渣覆盖钢液表面。
44.步骤s5,插入硅钙块和铝块进行预脱氧;控制钢液中铝含量小于0.01%,硅钙块按照0.5kg/t加入,控制块度≤50mm。
45.步骤s6,预脱氧后,钢液进行造渣还原,观测渣料颜色变化,直至出现白渣,且白渣状态能持续10~15min,停止还原操作。
46.步骤s7,钢液造轻薄渣,加入铝粉和硅钙粉进行扩散脱氧,然后加入生石灰造渣,保持白渣状态出钢。
47.步骤s8,出钢前加入配备好的终脱氧剂和铈,随钢液混充加入钢包内;出钢过程中,向钢液表面吹氩气,控制出钢温度1630
±
10℃,渣液应控制在钢液总量的10~15
‰
。终脱氧剂为硅钙钡和硅钙块的混合物,硅钙钡按钢液总量的1~1.5kg/t加入,硅钙块按0.5kg/t加入。铈的加入总重量为钢液总量0.8wt
‰
步骤s9,浇铸前,钢液静置3~5min,离心浇铸,控制浇铸温度1540
±
10℃。
48.离心浇铸时采用以下步骤:步骤s91,型筒准备,并对型筒进行预处理。
49.步骤s92,型筒喷涂,控制喷涂温度220~250℃,喷涂厚度1.5~2.0mm。
50.步骤s93,浇铸前10min,向型筒内充入氩气或者二氧化碳。
51.步骤s94,设置离心机工作参数,比如g值。
52.步骤s95,浇铸,并采用氩气保护,浇铸时型筒温度80~100℃。离心浇铸采用内径φ60mm浇道,钢包采用φ55mm口径的滑板及下水口,控制浇铸速度。
53.本实施例中铸管的制备工艺,超级奥氏体不锈钢的冶炼于一个中频炉内完成熔炼和精炼过程,同时冶炼过程中通过多次渣料,利用泡沫化的渣料吸收钢液中的杂质,同时渣料覆盖在钢液表面,隔绝了空气,避免钢液二次氧化,避免最终的铸管产生夹渣缺陷,保证了产品的质量。