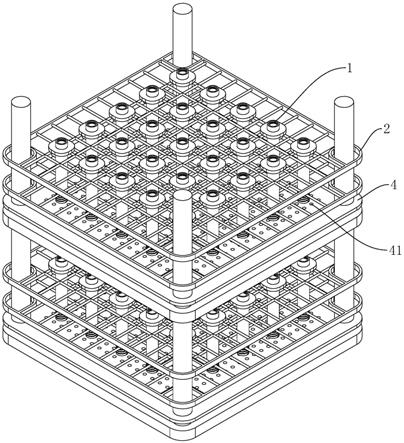
1.本技术涉及传动电机轴加工领域,更具体地说,它涉及传动电机轴热处理工艺。
背景技术:
2.电机轴是一种高转速、少支承的旋转体,在电机中,主要将电机的动力传递给与电机轴连接的配件,以达到驱动相关配件旋转的目的。电机轴的原材料主要为钢铁,电机轴在制作过程中,通常会进行热处理加工,其主要目的是使电机轴获得较高的强度和优良的韧性、塑性等,以确保电机轴具有优良的机械性能。
3.热处理加工一般包括淬火和回火,淬火后,电机轴的内应力增大,质脆,结合回火,以消除应力,从而增强电机轴的韧性、调整电机轴的强度,使电机轴的力学性能定型。淬火和回火的结合能够有效确保电机轴具有优良的机械性能,是目前大部分企业广泛使用的一种对电机轴加工的方式。
4.针对上述中的相关技术,发明人发现,电机轴经热处理加工后,电机轴的尺寸容易发生变形,尤其是电机轴端部的花键尺寸变形较为明显。为此,如何优化热处理加工步骤以改善电机轴尺寸变形是目前亟需解决的问题。
技术实现要素:
5.为了改善在热处理加工中电机轴花键发生尺寸变形的问题,本技术提供传动电机轴热处理工艺。
6.本技术提供的传动电机轴热处理工艺采用如下的技术方案:传动电机轴热处理工艺,包括以下步骤:装料;前清洗;预升温:升温至810-830℃,保持20-40min;渗碳淬火;后清洗;回火。
7.通过采用上述技术方案,渗碳淬火的温度一般在900-940℃左右,在渗碳淬火之前增加预升温的操作,使电机轴所处的环境的温度呈阶梯状升高,从而减缓电机轴的温度升高速度,降低电机轴在高温下产生的热应力,从而降低电机轴经热处理加工后发生变形的可能性。
8.优选的,装料后,进行预先热处理操作,具体为:升温至920-940℃,保持170-190min,冷却,然后再进行预升温。
9.通过采用上述技术方案,对电机轴进行预先热处理操作,能够细化金属组织晶粒,改善电机轴原材料成分偏析、带状组织等缺陷,以此提升原材料内部结构的均匀性,从而减少电机轴产生变形的可能性。
10.优选的,装料时,采用支撑板进行支撑电机轴,支撑板开设有若干过油孔。
11.优选的,过油孔的孔径为10-12mm,相邻过油孔之间的间距为28-32mm。
12.通过采用上述技术方案,利用支撑板对电机轴进行有效支撑,降低电机轴在自身重力下产生变形的可能性,同时,借助过油孔确保淬火油的流通量,从而在保证能够使电机轴淬硬的前提下,也能够降低电机轴产生变形的可能性。
13.优选的,渗碳淬火的具体操作为:s1、均热阶段,升温至890-910℃,不控制碳势,保持20-40min;s2、强渗阶段,保持温度为890-910℃,控制碳势为0.95%,保持110-130min;s3、扩散阶段,保持温度为890-910℃,控制碳势为0.75%,保持80-100min;s4、降温均热阶段,保持温度为790-810℃,控制碳势为0.75%,保持20-40min;s5、冷却阶段,保持油温120-140℃,油槽搅拌速度为20hz,保持20-40min。
14.通过采用上述技术方案,有助于渗碳介质产生的活性碳原子溶到电机轴的表层奥氏体中,并有助活性碳原子朝向电机轴的内部扩散,从而增强电机轴的强度、冲击韧性以及耐磨性等性能。同时利用热油对电机轴进行冷却,用于缓和电机轴的冷却速度,可降低电机轴在快速冷却过程中发生冷却不均匀、产生较大的应力,进而导致电机轴容易发生变形的现象。
15.优选的,回火操作中,温度为180-200℃,时间为110-130min。
16.通过采用上述技术方案,可以降低电机轴在淬火后产生的内应力和脆性,保持电机轴的高硬度和高强度。
17.优选的,前清洗中,采用清洗溶剂对电机轴进行真空浸泡清洗,清洗温度为110-130℃。
18.优选的,后清洗中,采用清洗溶剂对电机轴进行真空浸泡清洗,清洗温度为110-130℃。
19.通过采用上述技术方案, 一方面,降低电机轴表面残留的油渍对热处理质量的影响,另一方面,降低在后续回火操作中会产生大量烟气,进而会影响回火设备和工作人员健康的可能性。
20.综上所述,本技术具有以下有益效果:1、本技术通过增加预升温的操作,使得电机轴的温度升高速度得到减缓,降低了电机轴在高温下产生的热应力,从而降低了电机轴经热处理加工后发生变形的可能性。
21.2、本技术通过增加预先热处理的操作,使得电机轴原材料内部的成分偏析、带状组织得到改善,从而减少了电机轴产生变形的情况。
22.3、本技术通过改变装料方式,降低了电机轴因自身重力而产生变形的可能性。
附图说明
23.图1是利用支撑网支撑电机轴的装料示意图。
24.图2是利用支撑板支撑电机轴的装料示意图。
25.图3是对比例1中电机轴的金相照片。
26.图4是实施例5中电机轴的金相照片。
27.附图标记说明:1、电机轴;2、装料框;3、支撑网;4、支撑板;41、过油孔。
具体实施方式
28.以下结合附图和实施例对本技术作进一步详细说明。
29.电机轴端部的花键在热处理加工过程中发生变形主要是由于在处理过程中电机轴内部产生的热应力和组织应力的作用而产生的,除此之外,电机轴自身的重力以及电机轴自身的原材料成分也会影响电机轴端部的花键的变形。对此,申请人研究发现,在现有的工序增加预先热处理操作,可以有效改善电机轴原材料成分偏析等缺陷,可改善原材料内部结构的均匀性;在渗碳淬火工序之前增加预升温的操作,使温度呈阶梯状升高,可降低电机轴在高温下产生的热应力,进而改善电机轴端部花键发生变形的问题。
30.另外,传统的装料是采用支撑网进行支撑电机轴,通过改变装料方式,利用开孔的支撑板进行支撑电机轴,可降低电机轴自身重力造成花键变形的可能性。综合以上改善方案,可大大降低电机轴端部的花键发生变形的可能性,本技术正是基于上述发现做出的。
31.本技术中清洗电机轴的设备为hwbv真空浸泡清洗机,购买自江苏丰东制造;渗碳淬火使用的设备为ubg系列箱式多用炉,购买自江苏丰东制造,渗碳气氛类型为滴注式气氛,载气为甲醇,富化剂为丙烷;回火使用的设备为箱式回火炉,购买自江苏丰东制造;抛丸使用的设备为悬挂式抛丸机,购买自江苏丰东制造;清洗中使用的碳氢溶剂为本领域常规使用的清洗剂,本技术中使用的为d30溶剂油,购买自济南鑫飞御翔商贸。
32.本技术中用到的电机轴呈中空,一端具有内花键,热处理加工前花键上端的跨棒距为26.572mm,花键下端的跨棒距为26.532mm;另一端的内径为28mm,外径为32mm。
实施例
33.实施例1传动电机轴热处理工艺,包括以下步骤:装料,将电机轴装入装料框中,电机轴具有花键的一端朝上放置,如图1所示,采用支撑网对电机轴进行支撑;前清洗,采用碳氢溶剂对电机轴进行真空浸泡清洗,清洗温度为110℃;预升温,将清洗后的电机轴连同装料框放入炉中,升温至810℃,保持20min;渗碳淬火:s1、均热阶段,升温至890℃,不控制碳势,保持20min;s2、强渗阶段,保持温度为890℃,控制碳势为0.95%,保持110min;s3、扩散阶段,保持温度为890℃,控制碳势为0.75%,保持80min;s4、降温均热阶段,保持温度为790℃,控制碳势为0.75%,保持20min;s5、冷却阶段,保持油温120℃,油槽搅拌速度为20hz,保持20min;后清洗,采用碳氢溶剂对渗碳淬火后的电机轴进行真空浸泡清洗,清洗温度为110℃;回火,将电机轴连同装料框置于回火炉中,保持温度为180℃,时间为110min;检查,检测电机轴的表面硬度;抛丸,将电机轴置于抛丸机中,参照抛丸机的操作说明进行抛丸操作。
34.实施例2本实施例与实施例1的区别仅在于,预升温,将清洗后的电机轴连同装料框放入炉中,升温至820℃,保持30min。
35.实施例3本实施例与实施例1的区别仅在于,预升温,将清洗后的电机轴连同装料框放入炉中,升温至830℃,保持40min。
36.实施例4传动电机轴热处理工艺,包括以下步骤:装料,将电机轴装入装料框中,电机轴具有花键的一端朝上放置,如图1所示,采用支撑网对电机轴进行支撑;前清洗,采用碳氢溶剂对电机轴进行真空浸泡清洗,清洗温度为110℃;预先热处理,将电机轴连同装料框置于炉中,升温至920℃,保持170min,然后取出电机轴,冷却至室温,在其他实施方式中,也可将电机轴置于炉中的前室缓慢冷却90min;预升温,将电机轴连同装料框放入炉中,升温至810℃,保持20min;渗碳淬火:s1、均热阶段,升温至890℃,不控制碳势,保持20min;s2、强渗阶段,保持温度为890℃,控制碳势为0.95%,保持110min;s3、扩散阶段,保持温度为890℃,控制碳势为0.75%,保持80min;s4、降温均热阶段,保持温度为790℃,控制碳势为0.75%,保持20min;s5、冷却阶段,保持油温120℃,油槽搅拌速度为20hz,保持20min;后清洗,采用碳氢溶剂对渗碳淬火后的电机轴进行真空浸泡清洗,清洗温度为110℃;回火,将电机轴连同装料框置于回火炉中,保持温度为180℃,时间为110min;检查,检测电机轴的表面硬度;抛丸,将电机轴置于抛丸机中,参照抛丸机的操作说明进行抛丸操作。
37.实施例5本实施例与实施例4的区别仅在于,预先热处理,将电机轴连同装料框置于炉中,升温至930℃,保持180min,然后取出电机轴,冷却至室温。
38.实施例6本实施例与实施例4的区别仅在于,预先热处理,将电机轴连同装料框置于炉中,升温至940℃,保持190min,然后取出电机轴,冷却至室温。
39.实施例7本实施例与实施例4的区别仅在于,预先热处理,将电机轴连同装料框置于炉中,升温至970℃,保持180min,然后取出电机轴,冷却至室温。
40.实施例8传动电机轴热处理工艺,包括以下步骤:装料,将电机轴装入装料框中,电机轴具有花键的一端朝上放置,如图2所示,采用开设有过油孔的支撑板对电机轴进行支撑,支撑板上的过油孔均匀分布,过油孔的孔径为10mm,相邻过油孔之间的间距为30mm;前清洗,采用碳氢溶剂对电机轴进行真空浸泡清洗,清洗温度为110℃;预升温,将清洗后的电机轴连同装料框放入炉中,升温至810℃,保持20min;渗碳淬火:s1、均热阶段,升温至890℃,不控制碳势,保持20min;s2、强渗阶段,保持温度为890℃,控制碳势为0.95%,保持110min;
s3、扩散阶段,保持温度为890℃,控制碳势为0.75%,保持80min;s4、降温均热阶段,保持温度为790℃,控制碳势为0.75%,保持20min;s5、冷却阶段,保持油温120℃,油槽搅拌速度为20hz,保持20min;后清洗,采用碳氢溶剂对渗碳淬火后的电机轴进行真空浸泡清洗,清洗温度为110℃;回火,将电机轴连同装料框置于回火炉中,保持温度为180℃,时间为110min;检查,检测电机轴的表面硬度;抛丸,将电机轴置于抛丸机中,参照抛丸机的操作说明进行抛丸操作。
41.实施例9本实施例与实施例8的区别仅在于,过油孔的孔径为11mm,相邻过油孔之间的间距为30mm。
42.实施例10本实施例与实施例8的区别仅在于,过油孔的孔径为12mm,相邻过油孔之间的间距为30mm。
43.实施例11本实施例与实施例8的区别仅在于,过油孔的孔径为6mm,相邻过油孔之间的间距为30mm。
44.实施例12传动电机轴热处理工艺,包括以下步骤:装料,将电机轴装入装料框中,电机轴具有花键的一端朝上放置,如图1所示,采用支撑网对电机轴进行支撑;前清洗,采用碳氢溶剂对电机轴进行真空浸泡清洗,清洗温度为120℃;预升温,将清洗后的电机轴连同装料框放入炉中,升温至810℃,保持20min;渗碳淬火:s1、均热阶段,升温至900℃,不控制碳势,保持30min;s2、强渗阶段,保持温度为900℃,控制碳势为0.95%,保持120min;s3、扩散阶段,保持温度为900℃,控制碳势为0.75%,保持90min;s4、降温均热阶段,保持温度为800℃,控制碳势为0.75%,保持30min;s5、冷却阶段,保持油温130℃,油槽搅拌速度为20hz,保持30min;后清洗,采用碳氢溶剂对渗碳淬火后的电机轴进行真空浸泡清洗,清洗温度为120℃;回火,将电机轴连同装料框置于回火炉中,保持温度为190℃,时间为110min;检查,检测电机轴的表面硬度;抛丸,将电机轴置于抛丸机中,参照抛丸机的操作说明进行抛丸操作。
45.实施例13传动电机轴热处理工艺,包括以下步骤:装料,将电机轴装入装料框中,电机轴具有花键的一端朝上放置,如图1所示,采用支撑网对电机轴进行支撑;前清洗,采用碳氢溶剂对电机轴进行真空浸泡清洗,清洗温度为130℃;预升温,将清洗后的电机轴连同装料框放入炉中,升温至810℃,保持20min;
渗碳淬火:s1、均热阶段,升温至910℃,不控制碳势,保持40min;s2、强渗阶段,保持温度为910℃,控制碳势为0.95%,保持130min;s3、扩散阶段,保持温度为910℃,控制碳势为0.75%,保持100min;s4、降温均热阶段,保持温度为810℃,控制碳势为0.75%,保持40min;s5、冷却阶段,保持油温140℃,油槽搅拌速度为20hz,保持40min;后清洗,采用碳氢溶剂对渗碳淬火后的电机轴进行真空浸泡清洗,清洗温度为130℃;回火,将电机轴连同装料框置于回火炉中,保持温度为200℃,时间为130min;检查,检测电机轴的表面硬度;抛丸,将电机轴置于抛丸机中,参照抛丸机的操作说明进行抛丸操作。
46.实施例14传动电机轴热处理工艺,包括以下步骤:装料,将电机轴装入装料框中,电机轴具有花键的一端朝上放置,如图2所示,采用开设有过油孔的支撑板对电机轴进行支撑,支撑板上的过油孔均匀分布,过油孔的孔径为10mm,相邻过油孔之间的间距为30mm;前清洗,采用碳氢溶剂对电机轴进行真空浸泡清洗,清洗温度为110℃;预热处理,将电机轴连同装料框置于炉中,升温至930℃,保持180min,然后取出电机轴,冷却至室温,在其他实施方式中,也可将电机轴置于炉中的前室缓慢冷却90min;预升温,将电机轴连同装料框放入炉中,升温至820℃,保持30min;渗碳淬火:s1、均热阶段,升温至900℃,不控制碳势,保持30min;s2、强渗阶段,保持温度为900℃,控制碳势为0.95%,保持120min;s3、扩散阶段,保持温度为900℃,控制碳势为0.75%,保持90min;s4、降温冷却阶段,保持温度为800℃,控制碳势为0.75%,保持30min;s5、冷却阶段,利用邓文分级淬火油进行冷却,保持油温为130℃,油槽搅拌速度为20hz,保持30min;后清洗,采用碳氢溶剂对渗碳淬火后的电机轴进行真空浸泡清洗,清洗温度为120℃;回火,将电机轴连同装料框置于回火炉中,保持温度为190℃,时间为120min;检查,检测电机轴的表面硬度;抛丸,将电机轴置于抛丸机中,参照抛丸机的操作说明进行抛丸操作。
47.对比例对比例1传动电机轴热处理工艺,包括以下步骤:装料,将电机轴装入装料框中,电机轴具有花键的一端朝上放置,如图1所示,采用支撑网对电机轴进行支撑;前清洗,采用碳氢溶剂对电机轴进行真空浸泡清洗,清洗温度为110℃;渗碳淬火:将清洗后的电机轴连同装料框中置于炉中,然后进行渗碳淬火操作,具体如下:s1、均热阶段,升温至890℃,不控制碳势,保持20min;
s2、强渗阶段,保持温度为890℃,控制碳势为0.95%,保持110min;s3、扩散阶段,保持温度为890℃,控制碳势为0.75%,保持80min;s4、降温冷却阶段,保持油温为120℃,油槽搅拌速度为20hz,保持20min;后清洗,采用碳氢溶剂对渗碳淬火后的电机轴进行真空浸泡清洗,清洗温度为110℃;回火,将电机轴连同装料框置于回火炉中,保持温度为180℃,时间为110min;检查,检测电机轴的表面硬度;抛丸,将电机轴置于抛丸机中,参照抛丸机的操作说明进行抛丸操作。
48.性能检测试验试验一:针对实施例1至实施例3、实施例12至实施例13、对比例1中经过热处理加工后的电机轴,分别取10个试样,参照gb/t 9451-2005《钢件薄表面总硬化层深度或有效硬化层深度的测定》,利用上海恒一mh-6显微维氏硬度计测量各组试样表面的有效硬化层深度,并参照gb/t 4340.1-1999《金属维氏硬度试验 第1部分:试验方法》,利用上海恒一vh-5维氏硬度计测量试样的表面硬度,测量结果各组均取平均值。另外,参照gb/t 3478.1-2008《圆柱直齿渐开线花键》,分别测量各试样的花键上、下两端跨棒距的尺寸,若花键上端和下端的跨棒距尺寸均落入26.457-26.557mm范围内,则为合格,表明电机轴热处理过程中的花键尺寸变形得到控制。
49.表1 试验一的试验结果参照表1,与对比例1相比,实施例1至实施例3、实施例12和实施例13中电机轴端部的花键变形情况得到显著的改善,合格率可达到80%以上,且电机轴的有效硬化层深度及表面硬度相对较优,表明在渗碳淬火前增加预升温的操作,可以有效改善电机轴端部的花键经热处理加工后产生变形的可能性。
50.其中实施例12和实施例13中的电机轴的合格率不及实施例2和实施例3,表明渗碳淬火的工艺参数的改变对花键变形的控制起到的作用较小,主要影响电机轴的有效硬化层深度及表面硬度。
51.试验二:以实施例5和对比例1为例,分别取1个试样,参照gb/t 13298-2015《金属
显微组织检验方法》,利用蔡司金相显微镜axio observer 3m检测各组试样的金相组织。另外,针对实施例4至实施例7、对比例1中的经过热处理加工后的电机轴,分别取10个试样,参照gb/t 3478.1-2008《圆柱直齿渐开线花键》,分别测量各试样的花键上、下两端跨棒距的尺寸,若花键上端和下端的跨棒距尺寸均落入26.457-26.557mm范围内,则为合格,表明电机轴热处理过程中的花键尺寸变形得到控制。
52.表2 试验二的试验结果如图3所示,由对比例1中电机轴的金相照片中可以看出,珠光体和铁素体的分布具有带状倾向,而由图4中所示的实施例5中电机轴的金相照片中可以看出,珠光体和铁素体的分布呈等轴状分布。珠光体和铁素体的带状分布容易导致原材料的横向性能偏低,从而可降低原材料的冲击韧性和断面收缩率,容易致使零件在热处理加工过程中产生变形。结合实施例5和对比例1中的金相照片可知,本技术中增加的对电机轴进行预先热处理步骤可有效改善原材料内部成分偏析、带状组织等缺陷,从而提升原材料内部结构的均匀性,进而降低电机轴端部的花键产生变形的可能性。
53.试验三:针对实施例1、实施例8至实施例11中的经过热处理加工后的电机轴,分别取10个试样,沿电机轴中部的孔轴线切断电机轴以暴露出孔的内表面,并采用上述方法,检测电机轴内孔表面的有效硬化层深度和距内孔表面0.1mm位置处的硬度,各组结果均取平均值。参照gb/t 3478.1-2008《圆柱直齿渐开线花键》,分别测量各试样的花键上、下两端跨棒距的尺寸,若花键上端和下端的跨棒距尺寸均落入26.457-26.557mm范围内,则为合格,表明电机轴热处理过程中的花键尺寸变形得到控制。
54.表3 试验三的试验结果由表3可知,改变装料方式后,实施例8至实施例10中电机轴端部的花键变形尺寸得到控制,表明相对于利用支撑网进行支撑电机轴,支撑板更能够增强电机轴的受力方式
和受力面积,降低电机轴在高温下因自身重力而产生变形的可能性;同时,根据本技术公开的范围进行开设过油孔,可有效确保淬火油的流通量,有助于电机轴淬硬,进一步减少了电机轴的变形。
55.针对实施例14中的10个电机轴试样采用试验一的方法进行检测电机轴的合格率,测得合格率为100%,可见,在对电机轴热处理加工中,结合预先热处理、预升温和更改装料方式,能够更好的降低电机轴端部的花键产生变形的可能性,使得加工后的电机轴更符合企业的生产要求。
56.本具体实施例仅仅是对本技术的解释,其并不是对本技术的限制,本领域技术人员在阅读完本说明书后可以根据需要对本实施例做出没有创造性贡献的修改,但只要在本技术的权利要求范围内都受到专利法的保护。