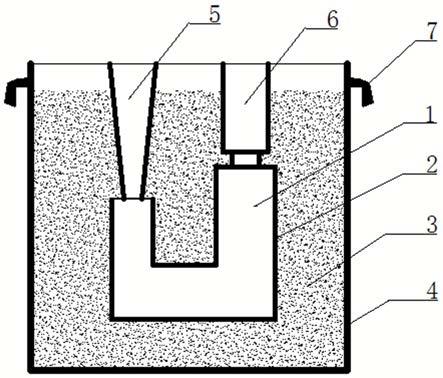
1.本发明涉及消失模铸造领域,特别是一种消失模采用高温陶瓷化涂料气化空壳无碳精密铸造方法。
背景技术:
2.消失模铸造是21世纪轻型化高效率的一项先进工艺技术,在中国已有4000多家消失模铸造企业,其中已有1500家以上采用干砂负压下富氧先烧空后浇注金属液的工艺,如公开号为cn101690976a公开的中国专利,名称为消失模铸造采用高性能涂层负压燃烧空壳浇注气流速冷消除碳缺陷法,此法比传统的实型浇注有了巨大的突破性和先进性,钢铁消失模铸件的增碳缺陷得到了比较好的控制,但由于烧空时间和铸件结构及大小不同的局限性,一般情况下还难以完全烧空型内的聚苯乙烯泡沫(expanded polystyrene,简称eps),烧空度多为80~90%范围,也就是说微增碳的威胁还存在,对于高要求的铸件,如兵器、军工、国防装备、高铁、航空、航天等装备的特殊铸件,尚不能满足需要,eps模样唯在700℃以上方可快速完全气化无碳残余。如果采用仿熔模空壳法,采用熔模铸造水玻璃类或硅溶胶类涂料,则工艺繁琐,生产周期长,涂层固化过程污染性大,能耗惊人,因为需在1000~1100℃下焙烧2小时以上才能保证壳型的透气性,而且这种涂料不易脱砂清理,所以推广应用不受欢迎,得不偿失,少慢差费。在全国4000多家消失模铸造厂中,相当多的厂平时都常常需要接受这样或那样的单件、小批甚至大批迫切需求的高质量严控制碳成分的铸件,特别是低碳钢、低碳合金钢铸件,可以说是100%的无奈,这是迫需解决的现实问题。
技术实现要素:
3.本发明的目的是针对上述现有技术的缺陷,提供一种消失模采用高温陶瓷化涂料气化空壳无碳精密铸造方法,这种方法比传统的熔模精密铸造方法工序简化,铸件成本大幅降低,生产过程少无污染,节能减排,铸件易清理。
4.实现本发明目的的技术方案如下:一种消失模采用高温陶瓷化涂料气化空壳无碳精密铸造方法,包括如下步骤:s1.涂料配制:采用桂林5号高温陶瓷化涂料与煅烧过的铝矾土耐火填料,按重量百分比的成分是桂林5号为8%~12%,铝矾土为88%~92%,混合均匀得到涂料粉状混合料,加入占此涂料粉状混合料重量的60%~80%的水,搅拌30分钟;s2.涂层烘干:上述配制好的涂料采用刷涂、浸涂或淋涂的方式涂敷于eps模样的表面,逐层烘干,烘干温度为50~55℃,每层烘时>4小时;涂层厚度为5~6mm或8~10mm;s3.装箱进炉:把eps模样置于铁桶或铁箱内,填充厚度为5~10cm的干砂,干砂粒度为2~5mm;s4.炉内气化:
eps模样气化温度控制为700~800℃,气化时间>40分钟,得到铸型;s5.出炉浇注:铸型出炉后浇注金属液,按铸造生产进行浇注。
5.进一步地,s1中,铝矾土耐火填料的配用,涂敷第一、第二层的涂料铝矾土耐火填料为200目规格,其al2o3含量≥75%。
6.进一步地,s1中,涂敷第三层起的涂料铝矾土耐火填料选用50~150目规格的涂料粉状混合料,其al2o3含量>60%。
7.本发明采用商品名为“桂林5号”的复合添加剂,即公开号为cn104525851a,名称为高温陶瓷化耐冲刷无粉尘污染的环保铸造涂料的中国专利公开的环保铸造涂料,按消失模生产常规配制与涂敷于eps模样表面,在50~55℃下逐层烘干,连续涂烘5~6层,涂料层干燥厚度为5~8mm,也可视不同情况象刮腻子那样刮涂3~4层,而后置于可控温度为700~800℃的气化炉内,至eps模样完全气化形成无碳壳型即可出炉浇注钢铁水。
8.本发明的特点、优点或效果:1.从生产实际出发,700~800℃是桂林5号涂料陶瓷化转变的最佳温度。在700℃条件下不能使涂层转变为陶瓷化的涂料不能用于本发明的消失模气化空壳铸造,本发明所用涂料是国家发明专利商品化产品桂林5号高温陶瓷化涂料;2.本发明选用的涂料之耐火填料是经煅烧的铝矾土,因铝矾土是中性耐火材料,适用性广,工艺性能和工作性能比较优越,成本适中,更重要的是其未经煅烧前的生料含10~16%的结晶水,煅烧后形成透气性极佳的微孔,而且经煅烧后其变形量极微,耐高温耐钢铁水冲刷性很强,有效防止了气化或浇注过程壳型变形或开裂,消除浇注反喷现象。煅烧的铝矾土耐火填料在本发明中选用的优越性是常见常用的如石英、石墨、宝珠砂、棕玉砂、莫来石、蓝晶石等所不具备的;3.桂林5号高温陶瓷化涂料添加剂的主要成分是包括工业淀粉在内的天然植物粉剂,在高温条件下完全炭化,在陶瓷化的涂层里产生许多透气微孔,这是石蜡熔模铸造传统或现行涂料(水玻璃或硅溶胶类)所不具备的,故本发明的壳型完全不需像传统熔模壳型那样,经1000~1100℃温度长时间的焙烧。
附图说明
9.图1为本发明实施例中消失模采用高温陶瓷化涂料气化空壳无碳精密铸造的模样装箱示意图。
10.图中,1.eps模样 2.涂层 3.干砂 4.箱体 5.浇口 6.冒口 7.吊勾。
具体实施方式
11.下面将结合附图和实施例,对本发明的技术方案进行完整地描述,显然,所描述的实施例仅仅是本发明一部分实施例,而不是全部的实施例。基于本发明中的实施例,本领域普通技术人员在没有做出创造性劳动前提下所获得的所有其他实施例,都属于本发明保护的范围。
12.实施例:一种消失模采用高温陶瓷化涂料气化空壳无碳精密铸造方法,包括如下步骤:
s1.涂料配制:采用桂林5号高温陶瓷化涂料与煅烧过的铝矾土耐火填料,按重量百分比的成分是桂林5号为10%,铝矾土为90%,混合均匀得到涂料粉状混合料,加入占此涂料粉状混合料重量的70%的水,搅拌30分钟;铝矾土耐火填料的配用,涂敷第一、第二层的涂料铝矾土耐火填料为200目规格,以提高铸件表面光洁度,其al2o3含量≥75%,以提高涂料的抗粘砂性能;涂敷第三层起的涂料铝矾土耐火填料选用50~150目规格的涂料粉状混合料,其al2o3含量>60%,以提高涂层的强度、透气性、抗裂、抗变形性;s2.涂层烘干:上述配制好的涂料采用刷涂、浸涂或淋涂的方式涂敷于eps模样的表面,逐层烘干,烘干温度为50~55℃,每层烘时>4小时;涂层厚度为5~6mm或8~10mm;s3.装箱进炉:如图1所示,涂层2厚度为5~6mm的eps模样1一般适用于铸件重量100kg以内的小件,为防止壳型受损或浇注金属液时壳型胀裂,宜把eps模样1置于铁质桶体或箱体4内填充粒度为2~5mm的干砂3,填充的厚度为5~10cm;涂层2厚度为8~10mm的eps模样1视铸件的不同结构和操作上不同的可靠性,可以直接进气化炉内气化,或装箱填充干砂3作保护进炉气化;设有浇口5与eps模样1的一端连通,设有冒口6与eps模样1的另一端连通;s4.炉内气化:eps模样中速气化温度为500℃左右,从生产周期、涂料层陶瓷化转变温度、减少电能损耗等因素综合考虑,气化温度控制为700~800℃为宜,气化完全的时间不能作教条性的规定,因铸件结构不同、炉子性能不同、炉内模样容量不同等因素而变,应以生产经验与实际检查相结合,一般情况下气化时间>40分钟,得到铸型;s5.出炉浇注:铸型出炉时处于700~800℃高温,宜通过箱体4上设有的吊勾7吊运至填有干砂的地坑内浇注金属液,按铸造生产进行浇注。
13.以上公开的本发明的优选实施例,只是帮助阐述本发明,不限制本发明仅为所述的具体实施方式。显然,根据本说明书的内容,可作很多的修改和变化。本说明书选取并具体描述这些实施例,是为了更好地解释本发明的原理和实际应用,从而使所属技术领域技术人员能很好地理解和利用本发明。