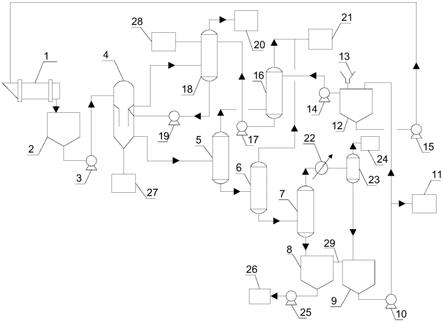
1.本实用新型涉及气化灰水处理技术领域,具体为一种内循环的气化灰水除硬装置。
背景技术:
2.气化煤中含有大量的金属离子及其氧化物,在气化炉中高温燃烧并激冷的过程中部分转化成固态的粗渣和细渣,剩余部分在气化灰水系统富集,灰水中钙、镁离子含量不断升高,整个气化装置水系统面临结垢和堵塞的问题,这是影响气化装置长周期稳定运行的主要因素。一般的灰水除硬流程是通过投加氢氧化钠或碳酸钠生成碳酸钙沉淀,除硬后的水再加酸回调ph,存在的主要问题有:1、除硬并回调ph后的水含有硫酸根等酸根离子,返回气化灰水系统会在装置内生成硫酸钙等硬垢;2、只处理气化外排灰水,循环灰水的结垢问题得不到解决;3、除硬产生的碳酸钙污泥难以处理,解决外排灰水硬度的同时引发新的问题;4、药剂成本高,运行成本高,无明显经济效益。
技术实现要素:
3.针对现有技术的不足,本实用新型提供了一种通过对气化灰水的多级处理以达到降低灰水除硬装置药剂使用量的特点,同时通过将十八酸钠储罐中的十八酸钠引入灰水回收单元中不仅能够降低灰水的硬度,且能够在气化炉中消耗除硬沉淀物并多产co、co2等工艺气体的内循环的气化灰水除硬装置。
4.为了达到上述目的,本实用新型所采用的技术方案是:
5.一种内循环的气化灰水除硬装置,包括气化炉,气化炉的一侧的煤浆进口与煤浆制备单元相连,气化炉的粗煤气出口通过水洗塔与工艺气变换系统相连,气化炉的底部与粗渣处理系统相连,气化炉的下部与高压闪蒸罐的进口相连,所述高压闪蒸罐底部的液相出口与低压闪蒸罐的进口相连,低压闪蒸罐的液相出口与真空闪蒸罐的进口相连,真空闪蒸罐的液相出口通过澄清槽以及底料泵与细渣处理系统相连;
6.所述真空闪蒸罐的顶部气相出口通过塔顶气经水冷凝器与真空闪蒸分离器相连,真空闪蒸分离器的顶部与不凝气体火炬装置相连通,真空闪蒸分离器的底部液相出口通过灰水槽与灰水回收单元相连;
7.所述灰水回收单元内包括用于对灰水除硬的十八酸钠储罐。
8.优选的,所述澄清槽的上部设有与灰水槽相连的澄清管道。
9.优选的,所述灰水回收单元包括与灰水槽相连的灰水泵,灰水泵通过管道分别与污水处理系统以及循环灰水部相连。
10.优选的,所述循环灰水部包括与灰水泵相连的灰水沉淀池,灰水沉淀池的顶部设有与其相连通的十八酸钠储罐,灰水沉淀池的底部沉淀物出口通过污泥泵与煤浆制备单元中的磨煤机相连,灰水沉淀池的下部液相出口通过灰水循环泵与热水塔相连,热水塔底部的液相出口通过热水泵与水洗塔的第一进口相连,水洗塔底部的液相出口与黑水泵与气化
炉的激冷水进口相连。
11.优选的,所述煤浆制备单元包括磨煤机,磨煤机的出口通过煤浆槽和煤浆泵与气化炉的燃烧室相连。
12.优选的,所述热水塔的进气口与高压闪蒸罐顶部的气相出口相连,热水塔的出气口与变换汽提塔的进口相连。
13.优选的,所述变换汽提塔的进口与低压闪蒸罐顶部的气相出口相连。
14.优选的,所述水洗塔的第一进口与变换高温凝液储罐相连。
15.按照上述安装制成的一种内循环的气化灰水除硬装置,通过设置高压闪蒸罐、低压闪蒸罐、真空闪蒸罐、澄清槽以及污水处理系统能够减少除硬药剂的使用量,进一步的通过将十八酸钠储罐中的十八酸钠引入灰水回收单元中,使除硬产水中游离的硬脂酸根离子在气化炉中完全热解,除硬沉淀物十八酸钙(硬脂酸钙)返回磨煤制浆系统回收其热值,并在气化炉燃烧室转变为co、co2等工艺气体,以达到降低循环灰水的硬度,避免出现结垢的现象,同时使气化炉消耗除硬沉淀物并多产工艺气体,将十八酸钠转化为可利用、有效益的工艺气,实现气化装置良性循环的优点。
附图说明
16.图1为本实用新型的结构示意图。
具体实施方式
17.为使本实用新型实施例的目的、技术方案和优点更加清楚,下面将结合本实用新型实施例中的附图,对本实用新型实施例中的技术方案进行清楚、完整地描述,显然,所描述的实施例是本实用新型一部分实施例,而不是全部的实施例。基于本实用新型中的实施例,本领域普通技术人员在没有作出创造性劳动前提下所获得的所有其他实施例,都属于本实用新型保护的范围。
18.参看图1:本实用新型为一种内循环的气化灰水除硬装置,包括气化炉4,气化炉4的一侧的煤浆进口与煤浆制备单元相连,气化炉4的粗煤气出口通过水洗塔18与工艺气变换系统20相连,气化炉4的底部与粗渣处理系统27相连,气化炉4的下部与高压闪蒸罐5的进口相连,所述高压闪蒸罐5底部的液相出口与低压闪蒸罐6的进口相连,低压闪蒸罐6的液相出口与真空闪蒸罐7的进口相连,真空闪蒸罐7的液相出口通过澄清槽8以及底料泵25与细渣处理系统26相连;所述真空闪蒸罐7的顶部气相出口通过塔顶气经水冷凝器22与真空闪蒸分离器23相连,真空闪蒸分离器23的顶部与不凝气体火炬装置24相连通,真空闪蒸分离器23的底部液相出口通过灰水槽9与灰水回收单元相连;所述灰水回收单元内包括用于对灰水除硬的十八酸钠储罐13。所述澄清槽8的上部设有与灰水槽9相连的澄清管道29。所述灰水回收单元包括与灰水槽9相连的灰水泵10,灰水泵10通过管道分别与污水处理系统11以及循环灰水部相连。所述循环灰水部包括与灰水泵10相连的灰水沉淀池12,灰水沉淀池12的顶部设有与其相连通的十八酸钠储罐13,灰水沉淀池12的底部沉淀物出口通过污泥泵15与煤浆制备单元中的磨煤机1相连,灰水沉淀池12的下部液相出口通过灰水循环泵14与热水塔16相连,热水塔16底部的液相出口通过热水泵17与水洗塔18的第一进口相连,水洗塔18底部的液相出口与黑水泵19与气化炉4的激冷水进口相连。所述煤浆制备单元包括磨
煤机1,磨煤机1的出口通过煤浆槽2和煤浆泵3与气化炉4的燃烧室相连。所述热水塔16的进气口与高压闪蒸罐5顶部的气相出口相连,热水塔16的出气口与变换汽提塔21的进口相连。所述变换汽提塔21的进口与低压闪蒸罐6顶部的气相出口相连。所述水洗塔18的第一进口与变换高温凝液储罐28相连。
19.一种内循环的气化灰水除硬装置的除硬工艺,包括如下步骤:步骤一:所述气化炉4中水煤浆燃烧产生的粗渣通过气化炉4的底部粗渣出口进入粗渣处理系统27中进行粗渣处理,气化炉4中产生的气化黑水依次在高压闪蒸罐5、低压闪蒸罐6和真空闪蒸罐7中减压闪蒸;所述气化炉4压力为:5.6-6.5mpag,所述气化炉4底部气化黑水温度为:237-242℃,流量为:175-202m3/h;所述高压闪蒸罐5闪蒸压力为:0.7-1.2mpag,所述低压闪蒸罐6的闪蒸压力为:0.15mpag-0.30mpag,所述真空闪蒸罐7的闪蒸压力为:-0.05mpag~-0.075mpag。步骤二:所述高压闪蒸罐5塔顶闪蒸汽进入热水塔16加热来自灰水循环泵14的灰水,所述热水塔16塔顶不凝气与来自低压闪蒸罐6的闪蒸汽一同送变换汽提塔21。所述灰水循环泵14出口灰水流量为:160-185m3/h,所述热水塔16塔顶压力为:0.65-0.90mpag。步骤三:所述热水塔16塔底液经热水泵17加压进入水洗塔18和变换高温凝液28共同洗涤来自气化炉4的粗煤气。所述热水泵17进口温度为:156-175℃,灰水流量为:185-212m3/h;所述水洗塔18塔顶工艺气进入变换系统20;所述水洗塔16塔底液经黑水泵19送入气化炉4激冷气化炉4燃烧室下来的粗煤气和残渣。所述黑水泵19出口压力为:7.0-7.8mpag,流量为:285-337m3/h。步骤四:所述真空闪蒸罐7塔顶气经水冷凝器22降温后再真空闪蒸分离器23中气液分离,真空闪蒸分离器23不凝气排入火炬24,凝液进入灰水槽9;所述水冷凝器22出口温度为:40-50℃;所述真空闪蒸罐7塔底黑水进入澄清槽8固液分离,上清液进入灰水槽9,澄清槽8底部渣浆经澄清槽底料泵25送入细渣处理系统26。步骤五:所述灰水槽9内灰水通过灰水泵10一部分进入污水处理系统11作为外排水,一部分进入灰水沉淀池12作为循环灰水。所述外排水流量为:55-85m3/h,所述循环灰水流量为:162-193m3/h。所述灰水泵10出口灰水温度为:65-80℃;所述灰水硬度为:800-1550mg/l;所述自动加药装置13向灰水沉淀池12加入粉状十八酸钠,所述十八酸钠单位时间加入量与灰水中钙、镁离子的摩尔比例为:1.0-1.2:1;所述灰水沉淀池12除硬后灰水硬度为:350-550mg/l。步骤六:所述灰水沉淀池12除硬后的灰水通过灰水循环泵14进入热水塔16复热升温;所述灰水沉淀池12底部沉淀物通过污泥泵15返回磨煤机1和气化煤混合制浆;所述污泥泵15流量为:2-8m3/h,污泥质量浓度为:0.5%-2%;所述磨煤机1合格的煤浆经过煤浆槽2和煤浆泵3进入气化炉4燃烧室。本实用新型通过减少除硬药剂的使用量,且使用粉剂十八酸钠作为除硬药剂,其能够使除硬产水中游离的硬脂酸根离子在气化炉中完全热解除硬沉淀物十八酸钙(硬脂酸钙)返回磨煤制浆系统回收其热值,并在气化炉燃烧室转变为co、co2等工艺气体。最终循环灰水和外排灰水硬度降低,气化炉消耗除硬沉淀物并多产工艺气体,将药剂成本转化为可利用、有效益的工艺气,实现气化装置良性循环;通过上述工艺能够使循环灰水硬度降低到350-550mg/l,每方灰水处理得到的沉淀物可在气化炉4内产生16-19nm3有效气(co+h2),最终多产有效气2592nm3/h-3667nm3/h,或节约气化煤1503kg/h-2126kg/h。
20.在本实用新型的描述中,需要说明的是,除非另有明确的规定和限定,术语“安装”、“相连”、“连接”应做广义理解,例如,可以是固定连接,也可以是可拆卸连接,或一体地连接;可以是机械连接,也可以是电连接;可以是直接相连,也可以通过中间媒介间接相连,
可以是两个元件内部的连通。对于本领域的普通技术人员而言,可以通过具体情况理解上述术语在本实用新型中的具体含义。
21.以上实施例仅用以说明本实用新型的技术方案,而非对其限制;尽管参照前述实施例对本实用新型进行了详细的说明,本领域的普通技术人员应当理解:其依然可以对前述各实施例所记载的技术方案进行修改,或者对其中部分技术特征进行等同替换;而这些修改或者替换,并不使相应技术方案的本质脱离本实用新型各实施例技术方案的精神和范围。