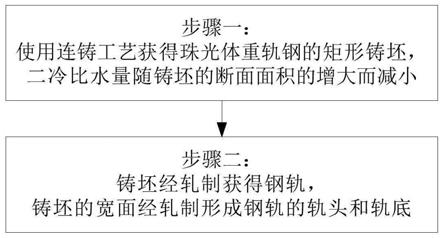
1.本公开属于钢铁冶金技术领域,特别涉及到一种促进非金属夹杂物弥散化分布的重轨生产方法以及使用该方法生产的珠光体重轨。
背景技术:
2.随着社会经济的迅猛发展,铁路运输正不断趋于高速化、重载化,钢轨各项技术质量指标控制要求不断提升。钢轨在与车轮接触的时候,承受着机车回环往复且多变的载荷,其纯净度对于钢轨疲劳寿命有着重要影响。由于钢中夹杂物对钢材基体组织连续性的阻碍作用,使得钢材在轧制加工、热处理以及使用过程中与夹杂物发生分离,导致缝隙产生,对钢材力学性能、抗腐蚀性等指标产生消极影响。由此,非金属夹杂可严重影响产品安全可靠性,进而对企业产品质量水平、质量控制合格率、生产效率及生产成本均造成不利影响。
3.现有技术注重对夹杂物本身及其均质性控制进行研究,并通过设计特定结构的浇注设备、使用前驱诱导粉、超声等措施在铸造阶段促进非金属夹杂物的弥散化分布,以改善钢轨的力学性能。然而,现有方法涉及原有设备的改造、原料和/或操作步骤的增多,使得生产成本有所增加。
4.由此可见,开发一种低成本、易于操作的重轨生产方法,以有效促进非金属夹杂物弥散化分布、改善钢轨力学性能成为钢铁冶金技术领亟待解决的问题。
5.公开内容
6.为了解决现有的技术问题,本公开提出了一种促进非金属夹杂物弥散化分布的重轨生产方法,该方法通过在连铸过程中优化二冷比水量、二冷宽窄面配水比,促进珠光体重轨钢中非金属夹杂物弥散化分布,改善钢轨力学性能。
7.依据本公开,提供一种促进非金属夹杂物弥散化分布的重轨生产方法,包含以下步骤:
8.步骤一,使用连铸工艺获得珠光体重轨钢的矩形铸坯,其中,连铸工艺的二次冷却过程中,二冷比水量随铸坯的断面面积的增大而减小,且铸坯宽窄面配水呈宽面少窄面多的趋势分配;以及
9.步骤二,铸坯经轧制获得钢轨,其中,铸坯的宽面经轧制形成钢轨的轨头和轨底。
10.依据本公开的一个实施例,二冷比水量按0.32~0.41l/kg
钢
投运。
11.依据本公开的一个实施例,二次冷却过程中,二冷宽窄面配水比如下:
12.第一区段1:(1.05~1.1);
13.第二区段1:(1.38~1.42);
14.第三区段1:(1.45~1.53);
15.第四区段1:(1.55~1.58);
16.第五区段1:1.55。
17.依据本公开的一个实施例,珠光体重轨钢包含:u75v重轨钢、u78crv重轨钢。
18.依据本公开的一个实施例,铸坯的断面面积包含以下规格:280mm
×
380mm、280mm
×
325mm、320mm
×
410mm。
19.依据本公开的一个实施例,连铸过程中浇铸过热度为20~35℃。
20.依据本公开的一个实施例,连铸过程中连铸拉速为0.65~0.80m/min。
21.依据本公开的一个实施例,连铸过程中拉矫位置坯壳温度为910~980℃。
22.依据本公开,提供一种重轨,重轨由上述重轨生产方法生产。
23.由于采用以上技术方案,本公开与现有技术相比具有如下优点:
24.1、依据本公开的重轨生产方法充分利用矩形坯宽窄面冷却传热效率差异,优化二冷配水,强化冷却,降低局部凝固时间,提升局部凝固速率,减小二次枝晶臂间距;
25.2、依据本公开的重轨生产方法强化连铸过程中铸坯的冷却凝固,改善溶质微观偏析,细化偏析析出的mns非金属夹杂物;
26.3、依据本公开的重轨生产方法通过大压缩比促进关键区域基体流变迁移,降低非金属夹杂物聚集,促进其弥散分布,改善夹杂评级质量及产品力学性能;
27.4、依据本公开的重轨生产方法仅涉及连铸工艺二次冷却工艺参数的调整以及轧制工序调配,无需改造设备、增加原料/操作步骤,以低成本获得高性能珠光体重轨钢。
附图说明
28.图1为依据本公开的促进非金属夹杂物弥散化分布的重轨生产方法的流程图;
29.图2为依据本公开的重轨生产方法中铸坯经轧制形成重轨的示意图;
30.图3为现有技术中铸坯经轧制形成重轨的示意图。
31.图中
32.100铸坯,110第一宽面,120第二宽面,130第一窄面,140第二窄面,200重轨,210轨头,220轨底。
具体实施方式
33.为了使本公开的目的、技术方案及优点更加清楚明白,下面结合实施例,对本公开进行进一步详细说明。应当理解,此处所描述的具体实施例仅用以解释本公开,并不用于限定本公开。
34.大断面重轨钢连铸坯在生成过程中由于其钢种成分本身及钢液凝固传热原理的因素,铸坯横断面局部区域凝固速率差异大,凝固过程产生的凝固组织及溶质元素浓度分布不均匀,进一步地产生严重晶间偏析,晶间溶质浓度极高,这为低温析出的mns等非金属夹杂提供了有利热力学条件。本公开通过强化连铸过程中铸坯的冷却凝固,改善溶质微观偏析,细化偏析析出的mns等非金属夹杂物;充分利用矩形坯宽窄面对应方向冷却凝固速率差异;通过大压缩比促进关键区域基体流变迁移,降低非金属夹杂物聚集,促进其弥散分布,改善夹杂评级质量及产品力学性能。
35.图1示出了依据本公开的促进非金属夹杂物弥散化分布的重轨生产方法的流程图。方法突破现有技术中铸坯断面面积越大,比水量越大的传统冷却给水方案,充分利用矩形铸坯宽窄面冷却传热效率差异、优化二冷配水强化冷却,有效促进了非金属夹杂物的弥散化分布,改善钢轨的力学性能。具体地,依据本公开的促进非金属夹杂物弥散化分布的重轨生产方法包含以下步骤:
36.步骤一,使用连铸工艺获得珠光体重轨钢的矩形铸坯,其中,连铸工艺的二次冷却过程中,二冷比水量随铸坯的断面面积的增大而减小。其中,珠光体重轨钢可包含u75v重轨钢、u78crv重轨钢等进行组织为珠光体的重轨钢;铸坯的断面面积可具有280mm
×
380mm、280mm
×
325mm、320mm
×
410mm等多种规格。
37.步骤二,铸坯经轧制获得钢轨,其中,铸坯的宽面经轧制形成钢轨的轨头和轨底。如图2所示,矩形铸坯100沿厚度方向的第一宽面110和第二宽面120经轧制后分别形成重轨200的轨头210和轨底220。
38.在本公开的实施例中,二冷比水量优选按0.32~0.41l/kg钢投运,比水量主要受浇铸断面差异影响,整体呈断面增大,比水量减小的趋势;(4)二冷宽窄面配水比按以下工艺实施:第一区段为1:(1.05~1.1)、第二区段为1:(1.38~1.42)、第三区段为1:(1.45~1.53)、第四区段为1:(1.55~1.58)、第五区段为1:1.55。轧制过程通过调整轧制工艺,使铸坯宽面轧制于轨头轨底侧,而窄面则位于轨腰两侧,进而该表铸坯至钢轨的基体流变与区域遗传。
39.依据本公开的促进非金属夹杂物弥散化分布的重轨生产方法所采用的连铸工艺中,其他工艺参数可依据具体工况进行设定。在本公开的实施例中,可设定以下工艺参数:浇铸过热度20~35℃、连铸拉速0.60~0.75m/min,拉矫位置坯壳温度910~980℃。
40.以下为依据本公开的重轨生产方法的具体实施例。
41.实施例1
42.本实施例中,使用连铸工艺获得u75v重轨钢的矩形铸坯,铸机断面为280mm
×
380mm。生产过程中采用以下参数:
[0043][0044]
随后,铸坯经轧制获得钢轨,其中,铸坯的宽面经轧制形成钢轨的轨头和轨底。
[0045]
上述工艺实施后,对重轨多点采样进行检测,结果显示:铸坯关键区域,即对应钢轨非金属夹杂检测面所处区域——距离铸坯表面40~70mm区域处二次枝晶臂间距由286~411μm降低至242~279μm,铸坯低倍质量良好,中心疏松、中心偏析均≤1.0级的比例由42%提高至72.2%;铸坯轧制成钢轨后,对钢轨进行非金属夹杂评级检测,a类非金属夹杂评级整体降低0.5~1.0级;采用aspex扫描检测单位面积内非金属夹杂颗粒数量密度为6.1颗/mm2,本发明技术较常规生产工艺降低23.7%。
[0046]
实施例2
[0047]
本实施例中,使用连铸工艺获得u75v重轨钢的矩形铸坯,铸机断面为280mm
×
325mm。生产过程中采用以下参数:
[0048][0049]
随后,铸坯经轧制获得钢轨,其中,铸坯的宽面经轧制形成钢轨的轨头和轨底。
[0050]
上述工艺实施后,对重轨多点采样进行检测,结果显示:铸坯关键区域二次枝晶臂间距由270~358μm降低至217~255μm,铸坯低倍质量良好,中心疏松、中心偏析均≤1.0级的比例由57%提高至87.3%;铸坯轧制成钢轨后,对钢轨进行非金属夹杂评级检测,a类非金属夹杂评级整体降低0.5~1.0级;采用aspex扫描检测单位面积内非金属夹杂颗粒数量密度为5.6颗/mm2,本发明技术较常规生产工艺降低32.3%。
[0051]
实施例3
[0052]
本实施例中,使用连铸工艺获得u78crv重轨钢的矩形铸坯,铸机断面为320mm
×
410mm。生产过程中采用以下参数:
[0053][0054]
随后,铸坯经轧制获得钢轨,其中,铸坯的宽面经轧制形成钢轨的轨头和轨底。
[0055]
上述工艺实施后,对重轨多点采样进行检测,结果显示:铸坯关键区域二次枝晶臂间距由354~450μm降低至282~326μm,铸坯低倍质量良好,中心疏松、中心偏析均≤1.0级的比例由41%提高至68.1%;铸坯轧制成钢轨后,对钢轨进行非金属夹杂评级检测,a类非金属夹杂评级整体降低0.5~1.0级;采用aspex扫描检测单位面积内非金属夹杂颗粒数量密度为6.3颗/mm2,本发明技术较常规生产工艺降低21.0%。
[0056]
对比例1
[0057]
对比例1中,使用连铸工艺获得u75v重轨钢的矩形铸坯,铸机断面为280mm
×
380mm。生产过程中二次冷却采用弱冷却,宽窄面配水整体呈宽面多窄面少的趋势,具体参数如下:
[0058][0059]
随后,铸坯经轧制获得钢轨,其中,铸坯的窄面经轧制形成钢轨的轨头和轨底,宽面经轧制形成轨腰。如图3所示,矩形铸坯100沿长度方向的第一长面130和第二窄面140经轧制后分别形成重轨200的两个侧面。
[0060]
上述工艺实施后,对重轨多点采样进行检测,结果显示:所得铸坯关键区域二次枝晶臂间距270~450μm,铸坯低倍中心疏松、中心偏析均≤1.0级的比例41%;铸坯轧制成钢轨后,对钢轨进行非金属夹杂评级检测,a类非金属夹杂评级整体2.0~3.0级;采用aspex扫描检测单位面积内非金属夹杂颗粒数量密度为7.1~8.8颗/mm2。
[0061]
对比例2
[0062]
对比例2中,使用连铸工艺获得u78crv重轨钢的矩形铸坯,铸机断面为320mm
×
410mm。生产过程中二次冷却采用弱冷却,宽窄面配水整体呈宽面多窄面少的趋势,具体参数如下:
[0063][0064]
随后,铸坯经轧制获得钢轨,其中,铸坯的窄面经轧制形成钢轨的轨头和轨底,宽面经轧制形成轨腰。如图3所示,矩形铸坯100沿长度方向的第一窄面130和第二窄面140经轧制后分别形成重轨200的两个侧面。
[0065]
上述工艺实施后,对重轨多点采样进行检测,结果显示:所得铸坯关键区域二次枝晶臂间距360~530μm,铸坯低倍中心疏松、中心偏析均≤1.0级的比例57%;铸坯轧制成钢轨后,对钢轨进行非金属夹杂评级检测,a类非金属夹杂评级整体2.0~3.0级;采用aspex扫描检测单位面积内非金属夹杂颗粒数量密度为8.7~9.8颗/mm2。
[0066]
综上所述,实施例1-3中采用本方法生产的大断面重轨钢相比于对比例1-2中采用的常规方法生产的重轨钢非金属夹杂物分布更加弥散化,单位面积夹杂物颗粒数降低,非金属夹杂物评级水平得到提升,为产品质量合格率提升提供了重要技术支撑,为钢轨力学性能改善提供积极影响。
[0067]
以上实施例仅表达了本公开的实施方式,其描述较为具体和详细,但并不能因此而理解为对本公开专利范围的限制。应当指出的是,对于本领域的普通技术人员来说,在不脱离本公开构思的前提下,还可以做出若干变形和改进,这些都属于本公开的保护范围。因此,本公开专利的保护范围应以所附权利要求为准。