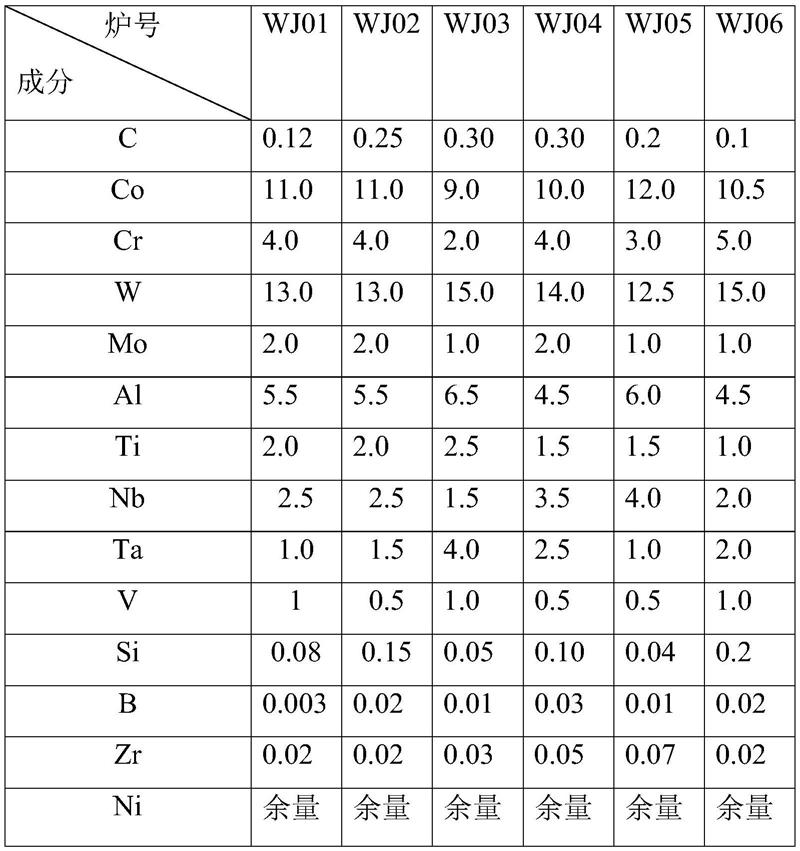
1.本发明是一种高性能铸造高温合金,属于金属材料加工技术领域。
背景技术:
2.随着等温锻造设备能力的提高,对等温锻造温度提出更高的要求。变形高温合金、粉末高温合金的等温锻造温度在实际生产过程中已经超过1050℃,为1070~1100℃。
3.美国使用tzm钼合金作为等温锻造模具材料,最高使用温度可达1200℃。但是tzm钼合金抗氧化性能较差,要求在全封闭真空等温锻造设备中进行,投资巨大。目前,我国的变形高温合金和粉末盘等温锻造在大气条件下进行。现有dm02合金(cn 2005100814011.3)在1050℃下性能较好,但在1100℃的高温强度不足。cn201710828424.7中提到的合金使用温度在1050℃以内,高于1050℃后合金的高温拉伸性能和抗氧化性能直线下降,不能满足等温锻造的需求。n3合金(《材料工程》2009年增刊18-21)使用温度在1050℃~1100℃,然而在批产过程中发现,该合金在1100℃的抗氧化性能较低,限制了在大气条件下作为等温锻造模具材料的使用寿命。
4.对于高温合金而言,服役温度每提高50℃,合金的使用寿命衰减为原来的一半。研究表明,二代单晶高温合金比一代单晶的服役温度提高了40℃。这说明突破服役温度至关重要。等温锻造模具使用过程中在高温的同时承受较大拉应力。另外,由于大气条件下使用,氧化皮的大量脱落导致模具型腔尺寸的变化,影响成型尺寸,导致产品报废。因此抗氧化性能至关重要。
5.n3合金在1100℃下高温抗拉强度可达到470mpa,但抗氧化性能较低,实验数据显示氧化剥落物较多,为抗氧化级别,不能达到完全抗氧化级别。
技术实现要素:
6.本发明正是针对上述现有技术状况而设计提供了一种高性能铸造高温合金,该合金在1100℃除了具有较高的抗拉强度外,抗氧化性能也得到较大改善,达到完全抗氧化级别,提高了使用寿命,能够成为1050℃到1100℃等温锻造用的模具材料。
7.本发明的目的是通过以下技术方案来实现的:
8.该种高性能铸造高温合金的化学成分及重量百分比为:c 0.1~0.3%,co 9~12%,cr 2.0~5.0%,w 12.5~15%,mo 1.0~3.0%,al 4.5~7.0%,ti 1.0~2.5%,nb 1.5~4.0%,ta 1.0~4.0%,v 0.5~1.0%,b 0.002~0.032%,zr 0.010~0.070%,si 0.05~0.2%,余量为ni。
9.本发明合金显微组织由奥氏体γ基体组成,加入w、mo、nb、ta进行固溶强化,其中w主要分布于枝晶干,而mo主要分布于枝晶间。al、ti、ta、co形成初生共晶γ’,起到提高塑形,协调变形的作用。nb、ta、ti可形成初生mc碳化物。b和zr元素可强化晶界,增加合金流动性,有利于铸造性能。v加入后主要分布于γ基体中,少量分布于γ’中,对晶格畸变产生影响,具有明显的固溶强化作用。此外,v的少量加入对于缺口敏感性的改善具有重要作用。si
作为微量元素添加,其重量百分数不大于0.2%。文献中对si元素的有害作用和有利影响均有报道,在本合金中,单独添加范围内的si元素并不能达到改善合金抗氧化性能的目的,而v和si需同时添加,且在此成分范围内才能达到良好的效果,这在以往的文献中并没有报道。
10.与现有技术相比,本发明合金具有抗拉强度高,延伸率好,抗氧化性能好的特点。在1100℃下高温拉伸性能可实现:高温抗拉强度rm≥470mpa,屈服强度ra≥340mpa,断后伸长率a≥7.0%。1100℃下抗氧化性能可实现:1100℃/100h平均氧化速率小于0.10g/m2.h,达到完全抗氧化级别。
具体实施方式
11.以下将结合实施例对本发明技术方案作进一步地详述:
12.该合金的实施例包括的化学成分及重量百分比参见表1所示。其中每一个炉号代表一个合金配比的实施例。
13.表1实施例合金成分范围
[0014][0015]
本发明所述的高性能铸造高温合金采用真空感应熔炼炉熔炼,该熔炼过程包括:熔化
‑‑‑
精炼
‑‑‑‑
浇铸成母合金。在熔化步骤中,碳、镍、钴、钨、钼在送电前直接加入坩埚
中,熔化结束后液面化清后精炼30~45分钟,过程中2~3次搅拌熔池,停电降温后加入铝、钛、硼、锆、钒、硅。完成后再次送电熔炼5~10分钟,停电降温。当温度降至浇注温度
±
10℃时开始浇注。母合金试棒经机加工后进行力学性能测试,测试标准为gb/t4338-2006。母合金中取板状试样进行抗氧化性能测试,依据标准为hb5258-2000。两项测试结果如表2所示。该结果表明,按照表1成分范围内的配比,合金1100℃的抗拉性能良好且抗氧化性能数据达到完全抗氧化级别。
[0016]
表2实施例合金1100℃力学性能
[0017][0018]
对比实施例
[0019]
采用真空感应熔炼炉熔炼成表3中wj07-wj17配比的母合金,母合金试棒经机加工后进行力学性能测试,测试标准为gb/t4338-2006。母合金中取板状试样进行抗氧化性能测试,依据标准为hb5258-2000。两项测试结果如表4所示。该结果表明,wj07为n3合金成分范围,该范围内的1100℃合金抗氧化性能低于本合金,wj08-wj09成分在本专利成分范围以外,此两炉合金性能低于专利成分范围内合金。wj10表示单独添加si元素不能达到提高性能的效果,wj11表示单独添加v元素也不能达到很好的效果。wj13-wj14表明添加hf元素效果不佳,wj15-wj16表明添加mn元素效果不佳,wj17表明同时添加hf和mn也不能起到提高合金高温抗拉性能和抗氧化性能的作用。
[0020]
表3对比实施例合金成分
[0021]
[0022][0023]
表4对比实施例合金1100℃性能数据
[0024]
[0025]
技术特征:
1.一种高性能铸造高温合金,其特征在于:该合金的化学成分及重量百分比为:c 0.1~0.3%,co 9~12%,cr 2.0~5.0%,w 12.5~15%,mo 1.0~3.0%,al 4.5~7.0%,ti 1.0~2.5%,nb 1.5~4.0%,ta 1.0~4.0%,v 0.5~1.0%,b 0.002~0.032%,zr 0.010~0.070%,si 0.05~0.2%,余量为ni。2.根据权利要求1所述的高性能铸造高温合金,其特征在于:该合金的化学成分及重量百分比为:c 0.12%,co 11.0%,cr 4.0%,w 13.0%,mo 2.0%,al 5.5%,ti 2.0%,nb 2.5%,ta 1.0%,v 1.0%,b 0.003%,zr 0.020%,si 0.08%,余量为ni。3.根据权利要求1所述的高性能铸造高温合金,其特征在于:该合金的化学成分及重量百分比为:c 0.25%,co 11.0%,cr 4.0%,w 13.0%,mo 2.0%,al 5.5%,ti 2.0%,nb 2.5%,ta 1.5%,v 0.5%,b 0.020%,zr 0.020%,si 0.15%,余量为ni。4.根据权利要求1所述的高性能铸造高温合金,其特征在于:该合金的化学成分及重量百分比为:c 0.30%,co 9.0%,cr 2.0%,w 15.0%,mo 1.0%,al 6.5%,ti 2.5%,nb 1.5%,ta 4.0%,v 1.0%,b 0.010%,zr 0.030%,si 0.05%,余量为ni。5.根据权利要求1所述的高性能铸造高温合金,其特征在于:该合金的化学成分及重量百分比为:c 0.30%,co 10.0%,cr 4.0%,w 14.0%,mo 2.0%,al 4.5%,ti 1.5%,nb 3.5%,ta 2.5%,v 0.5%,b 0.030%,zr 0.050%,si 0.10%,余量为ni。6.根据权利要求1所述的高性能铸造高温合金,其特征在于:该合金的化学成分及重量百分比为:c 0.20%,co 12.0%,cr 3.0%,w 12.5%,mo 1.0%,al 6.0%,ti 1.5%,nb 4.0%,ta 1.0%,v 0.5%,b 0.010%,zr 0.070%,si 0.04%,余量为ni。7.根据权利要求1所述的高性能铸造高温合金,其特征在于:该合金的化学成分及重量百分比为:c 0.10%,co 10.5%,cr 5.0%,w 15.0%,mo 1.0%,al 4.5%,ti 1.0%,nb 2.0%,ta 2.0%,v 1.0%,b 0.020%,zr 0.020%,si 0.20%,余量为ni。
技术总结
本发明是一种高性能铸造高温合金,其特征在于:该合金的化学成分及重量百分比为:C 0.1~0.3%,Co 9~12%,Cr 2.0~5.0%,W 12.5~15%,Mo 1.0~3.0%,Al 4.5~7.0%,Ti 1.0~2.5%,Nb 1.5~4.0%,Ta 1.0~4.0%,V 0.5~1.0%,B 0.002~0.032%,Zr 0.010~0.070%,Si 0.05~0.2%,余量为Ni。与现有技术相比,本发明合金具有抗拉强度高,延伸率好,抗氧化性能好的特点。在1100℃下高温拉伸性能可实现:高温抗拉强度Rm≥470MPa,屈服强度Ra≥340MPa,断后伸长率A≥7.0%。1100℃下抗氧化性能可实现:1100℃/100h平均氧化速率小于0.10g/m2.h,达到完全抗氧化级别。达到完全抗氧化级别。
技术研发人员:张华霞 冯微 赵会彬 孟宇
受保护的技术使用者:中国航发北京航空材料研究院
技术研发日:2021.11.10
技术公布日:2022/2/11