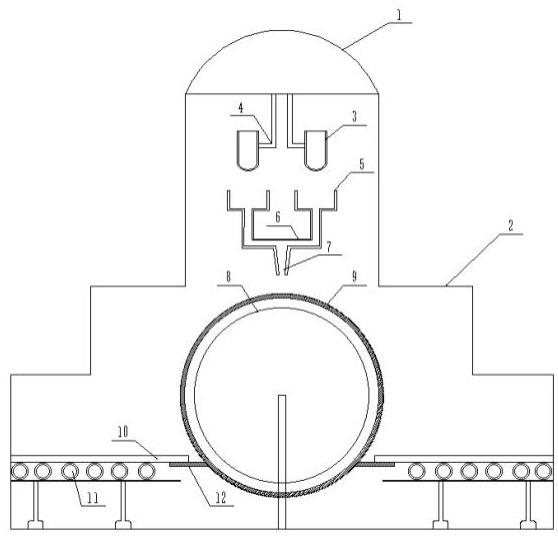
1.本发明涉及新材料技术领域,尤其涉及一种高磁感软磁材料非晶超薄带的制备装置。
背景技术:
2.纳米晶软磁合金是在非晶合金基础上发展起来的新型软磁材料,它由非晶基体及分布在该基体上的尺寸在10-15nm的体心立方结构纳米晶组成。其性能兼具传统晶态软磁材料高饱和磁感应强度和非晶态软磁材料低矫顽力、高磁导率和低损耗等优点,可以满足各类电气设备向高效节能、集成化方向发展的需求,且制备工艺简单,成本低廉,是重点支持和发展的新型绿色节能材料。
3.finemet合金具有高磁导率、低损耗等优异的综合软磁性能,并且可以在非真空条件下制备,研发不久就投入到工业应用中。但综合性能较好的fe
73.5
cu1nb3si
13.5
b9合金在最佳退火条件下的饱和磁感仅为1.24t,与高饱和磁感软磁材料相比,在相同工作条件下所需材料多,体积大,在一定程度上限制了其使用规模;nanoperm合金具有高饱和磁感和较为优异的综合软磁性能,由于含有zr等易氧化的贵金属元素,生产成本高,一直未能得到广泛应用;hitperm合金的特点是居里温度高,适合高温环境中使用,但其软磁性能与finemet合金和nanoperm合金相比较差。此外,该系列合金也需要在真空环境中制备,至今也未得到大规模应用。
4.因此,开发兼具高饱和磁感应强度、低损耗等优异软磁性能,同时制备工艺简单,原材料成本低廉的新型软磁材料是当前纳米晶软磁合金研究开发的热点与发展方向。通过制备技术改进、合金化元素配比优化及特殊的热处理工艺等手段,国内外科研工作者先后制备出fesibcu、fenbbcu、fenib等系列纳米晶软磁合金,其饱和磁感应强度达1.75-1.9t,已接近于取向硅钢。与传统软磁材料相比,这些合金在众多应用中具有明显的优势,但仍存在很多问题,如在制备过程中,目前通常采用单辊甩带快速冷却的方式制备非晶带材,如cn202010100414.7、cn201810341629.0、201710649674.8等专利中所提到的,但目前所用的单辊甩带装置往往比较传统,难以实现高速连续、高产能的生产,无法适应现代工业化生产的需求。
技术实现要素:
5.为了解决上述技术问题,本发明提供了一种高磁感软磁材料非晶超薄带的制备装置。
6.本发明完整的技术方案包括:一种高磁感软磁材料非晶超薄带的制备装置,所述制备装置包括熔炼室和快淬室,所述熔炼室对合金材料进行熔炼,所述快淬室位于熔炼室下方,快淬室设有合金带材快淬冷却辊,快淬冷却辊旁设有输送辊道,将凝固的合金带材输送出快淬室。
7.优选的,所述熔炼室中包括熔炼坩埚。
8.优选的,所述熔炼坩埚下方设有浇注系统。
9.优选的,所述浇注系统包括储液槽、浇道和浇口。
10.优选的,所述快淬室中设有快淬冷却辊,所述快淬冷却辊通过电机实现高速旋转。
11.优选的,所述快淬冷却辊旁设有输送系统。
12.优选的,所述输送系统前端设有退料挡块。
13.优选的,所述输送系统将超薄带材送至收集区。
14.本发明相对现有技术的优点为:1. 多个该倾转式熔炼坩埚设置,可以分别单独送料、次序熔炼、浇注、实现了纳米晶软磁合金材料的近连续式生产,提高了生产效率。
15.2. 浇口的纵截面设计使合金液进入浇口时静压力增大,充满整个型腔,提高了喷射速度,避免带材不连续情况的出现。
16.3. 快淬冷却辊可实现正反转,其左右两侧均设有输送辊道,用以输送凝固后的合金带材,使整个生产过程基本连续化完成,显著提高了产能。
17.4. 辊道上方铺设有表面光滑的输送板,避免划伤带材表面,提高了产品的表面质量。
附图说明
18.图1为本发明所用设备的结构示意图。
19.图2为本发明所用快冷辊的现场图。
20.图3为本发明控制系统界面图。
具体实施方式
21.下面将结合本技术实施方式中的附图,对本技术的实施方式中的技术方案进行清楚、完整的描述,显然,所描述的实施方式仅仅是作为例示,并非用于限制本技术。
22.本发明所公开的一种高磁感软磁材料非晶超薄带的制备装置,如图1所示,包括熔炼室1和快淬室2,所述熔炼室1内设有倾转式熔炼坩埚3,该坩埚可以通过转动与之相连的倾转臂4实现倾倒,尤其是,该倾转式熔炼坩埚3为多个,可以左右对称设置,也可以根据熔炼室的内部空间设置成3个或4个,并分别独立地与送料系统连接,该设计方式是为了实现纳米晶软磁合金材料的近连续式生产,以提高生产效率。
23.各倾转式熔炼坩埚3下方均设有对应的储液槽5,通过浇道6连接下方的浇口7,浇口7下方设有合金带材快淬冷却辊8,如图2所示,本发明的浇口7下方喷口处横截面设计为扁平的鸭嘴型,以提高其接触面积和冷却速度,其宽度小于下方的快淬冷却辊宽度,浇口7的纵截面呈上宽下窄的漏斗形,这样合金液进入浇口时,由于该形状该处的静压力增大,使喷口附近的合金液充满整个型腔,同时并提高了喷射速度,以避免出现带材不连续的情况。
24.快淬冷却辊8通过电机实现正转或反转,其左右两侧设有输送辊道,用以输送凝固后的合金带材,该辊道上方铺设有表面光滑的输送板10,下方通过托辊11驱动,以避免划伤带材表面,输送辊道前方各自设有退料挡块12,该退料挡块为可伸缩设计,输送辊道将带材输送到收集区进行热处理,该结构的设置是发现在实际生产中,仅在一侧存放带材,由于空间问题,能存放的带材有限,影响了生产效率。因此设计了能够正转和反转的快淬冷却辊8,
同时两侧均设置输送辊道,当一炉合金液浇注到冷却辊上凝固,通过一侧的输送辊输送到收集区,该炉合金生产完成后。浇注另一炉合金,并立刻反转电机,使下一炉的合金带材通过另一侧的输送辊送出。同时顶部的熔炼坩埚可以交替完成送料、熔炼、保温、倾倒的过程,使整个生产过程基本连续化完成,显著提高了产能。
25.下面对利用本发明的装置进行非晶超薄带材的具体制备过程进行介绍:(1)母合金锭制备:本发明非晶带材合金组分以原子比计,包括si:3.7%,b:6.8%,nb:2.8%,cu:1.1%,y:6.2%,余量为fe。是以finemet合金为基础,研究铁磁性元素fe及cu、nb等复合掺杂元素对合金纳米相组成及其交换耦合作用的影响,基于磁性价电子理论计算分析,提出高饱和磁感纳米晶合金成分设计原则,同时结合现场实际的熔炼温度控制和冷却工艺实际,对组分进行了微量调整,同时增加了可提高结晶化温度的钇元素。在提高了fe含量的同时,通过设计合适的nb和cu元素配比,抑制晶粒长大,获得均匀且显著细化的晶粒,从而增加了纳米晶材料的磁导率;矫顽力和损耗降低。
26.按照上述配比对各组分进行称量,将配好的fe、nb和y元素装入中频感应炉内进行熔炼,熔化后加入其余元素,继续熔炼并保温30分钟后冷却,得到母合金锭,将合金锭破碎后作为后续带材制备的原料。
27.(2)将破碎后的母合金材料通过送料系统分别送入坩埚中,进行熔炼。
28.(3)熔炼后,开启电机使快淬冷却辊高速旋转,同时使另一侧的退料挡块收回;转动倾转臂将合金液倾倒在储液槽中,并通过浇道由喷口喷射到快淬冷却辊表面,快速极冷形成非晶带,同时通过退料挡块进入输送辊道送到收集区。
29.(4)合金液浇注完成后,迅速将坩埚回正,送料系统送入新的母合金料进行熔炼;同时电机反转,使快淬冷却辊反方向高速旋转,同时一侧的退料挡块收回,另一侧的退料挡块伸出,转动倾转臂将另一炉合金液倾倒在储液槽中,重复上述过程,非晶带从另一侧的输送辊道运出。依次重复上述过程。
30.(5)到达收集区的非晶带材进行抓取并剪切,随后进行等温热处理,在真空条件下,于400-500℃保温10-50分钟,取出后进行水淬或空冷,得到退火后的纳米晶软磁合金带材。
31.尤其是,为适应不同宽度和厚度的带材需求,本发明步骤(2)中快淬冷却辊的转速通过控制系统控制为低速、中速和高速三个档位,如图3所示,每档的速度可以上下微调,具体为低速挡速度范围为340~360rpm,中速挡速度范围为400~420rpm,高速挡速度范围为480~500rpm。经过长期的大量实验,摸索出一套适合本发明合金组分和尺寸的转速控制方法,即转速r大致应符合下述条件,式中r为转速,单位为rpm,w为带材宽度,单位为mm,d为带材厚度,单位为μm,a为系数,取值范围为22~30,具体为在宽带材时取值可以为24.2,窄带材时取值可以为28.3。
32.本发明的送料系统、惰性气体保护、冷却系统以及热处理系统等均可采用现有技术中的成熟工艺,在此不再赘述。
33.本项目开发并生产出高饱和磁感应强度低损耗的新型铁基纳米晶合金,饱和磁感bs≥1.75t,工频损耗p1.5t/50hz≤0.3w/kg;工艺窗口宽、凝固过程可控,制备出的带材宽度为60~80mm,厚度为15~25μm,韧性好、可辊剪,该高性能纳米晶合金应用于定子铁芯制造上,使电机铁芯损耗比传统硅钢铁芯降低70-90%,整机效率比同款硅钢电机提升5-10%,在
无线充电、新能源汽车等高新技术领域有广泛的应用前景。非晶纳米晶软磁合金材料2019年全国使用量为12.5万吨,纳米晶超薄带市场需求量则在3500-500吨。目前正在研发推广应用的纳米晶高效电机,将带动非晶纳米晶带材数千亿元的市场,因此具有重要的经济价值和社会意义。
34.以上申请的仅为本技术的一些实施方式。对于本领域的普通技术人员来说,在不脱离本技术创造构思的前提下,还可以做出若干变型和改进,这些都属于本技术的保护范围。