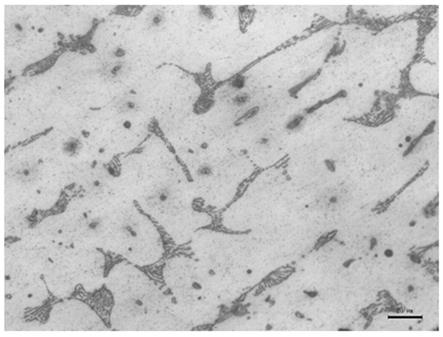
1.本发明创造属于铸造材料领域,具体涉及一种汽车涡轮增压器壳体铸钢材料。
背景技术:
2.随着环保排放要求的提高,对发动机燃料的燃烧程度需要更加充分,增压技术应运而生,而涡轮增压技术是既环保又节能的一种理想方法。涡轮增压器壳体是涡轮增压技术中的关键部件,工作温度逐步提高,部分已达到1000℃以上,在工作温度达到1000℃以上时,会缩短增压器壳体工作时间,产生裂纹而失效,造成增压器总成的不能正常运行,发动机功率降低。
3.目前涡轮增压器壳体基本为两类材料:高镍奥氏体球铁和一般奥氏体耐热钢。高镍奥氏体材料的缺点:含ni量高,达到34-36%。ni价格高,造成产品的成本高。材料的工作温度在950℃左右。如果超过此温度,产品会逐步失效,丧失其增压功能。一般奥氏体耐热钢材料的缺点:一般为保证奥氏体材料的单一相组织,ni量高,达到19-22%,ni价格高,造成产品的成本高,含nb在1.5-1.8%,nb价格高,造成产品成本高。含si量在2-2.5%,c量在0.3-0.4%,产品韧性差,伸长率指标低。
4.综上所述,能够找到既能满足使用条件,又能保证成本的铸造材料,这对于涡轮增压技术的规模化应用显得非常重要。
技术实现要素:
5.针对上述问题,本发明提出一种汽车涡轮增压器壳体铸钢材料,通过合理的设计各种元素的含量,控制材料的微观组织, 目的是可以满足产品工作温度的要求,并最大化的降低了生产成本,为规模化生产提供了条件。
6.本发明为实现其目的所采取的技术方案是:一种汽车涡轮增压器壳体铸钢材料,由以下重量百分比的组分组成:c:0.35-0.50%,si:1.0-1.8%,ni:9-10%,nb:0.6-1.1%,n:0.15-0.2%,余量为fe。
7.优选的,所述的一种汽车涡轮增压器壳体铸钢材料,由以下重量百分比的组分组成:c:0.44%,si:1.8%,ni:9.85%,nb:1.09%,n:0.16%,余量为fe。
8.优选的,所述的一种汽车涡轮增压器壳体铸钢材料,由以下重量百分比的组分组成:c:0.42%,si:1.71%,ni:9.7%,nb:1.01%,n:0.17%,余量为fe。
9.优选的,所述的一种汽车涡轮增压器壳体铸钢材料,由以下重量百分比的组分组成:c:0.43%,si:1.74%,ni:9.5%,nb:0.95%,n:0.15%,余量为fe。
10.优选的,所述的一种汽车涡轮增压器壳体铸钢材料,由以下重量百分比的组分组成:c:0.37%,si:1.31%,ni:10.00%,nb:0.9%,n:0.18%,余量为fe。
11.优选的,所述的一种汽车涡轮增压器壳体铸钢材料,由以下重量百分比的组分组成:c:0.38%,si:1.57%,ni:9.2%,nb:0.67%,n:0.19%,余量为fe。
12.本发明还提出一种汽车涡轮增压器壳体的制备工艺:其特征在于,包括以下步骤:
1)使用中频感应电炉作为熔化设备;2)需要的原材料包括废钢,电解镍,铌铁,微碳铬铁,氮化铬铁,硅铁,电解锰;3)备料:使用按重量百分比计的各原材料,废钢39.5-41.2%,电解镍9.1-10.1%,铌铁1.1-1.8%,微碳铬铁和氮化铬铁共45.1%,硅铁2.0%,电解锰1.0%,增碳剂0.4%,达到下列元素的控制范围c:0.35-0.50%,si:1.0-1.8%,ni:9-10%,nb:0.6-1.1%,n:0.15-0.2%,余量为fe;4)熔化步骤:熔化过程:第一步,在炉底加入增碳剂,氮化铬铁,废钢,后根据熔化的进度,依次加入铌铁,微碳铬铁,电解镍;第二步,升温到1560℃以上时,进行成分检查,硅锰元素除外,达到要求后;第三步,加入硅铁,电解锰,再次确认所有控制的化学成分在目标范围后,升温,待钢水温度达到产品工艺要求的出炉温度后停止供电,让钢水静置,扒除表面渣滓,最后出炉浇注产品;钢水等待时温度和时间要求:根据浇注涡轮增压器壳体的产品特性,一般在炉内钢水大于1600℃,等待的时间要小于60分钟,长时间的高温等待,会提高钢水的含气量,恶化微观组织,造成产品的功能失效;5)浇注过程:浇注设备为自动浇注机;根据产品的差异,程序设定浇注过程参数,如浇注重量和浇注时间;此方法优势为每型浇注重量控制波动小,一般在
±
1kg内;采用大流量,快流速,浇注状态稳定,基本无飞溅现象。
13.本发明技术的明显效果:本发明通过对元素c,si,ni,nb,n的有效控制的加入,在满足材料各种性能指标要求的前提下,极大的降低了生产成本,为涡轮增压器壳体提供一种稳定的制作材料。本发明ni含量在9-10%,极大地降低了生产成本,nb含量在0.6-1.1%,也极大地降低了生产成本,本发明节省了ni,nb的宝贵资源,更加环保,本发明通过有效的控制c,si元素含量,添加n元素,可以有效的保证产品组织的单一性,产品韧性指标明显提高,达到10%以上。基于以上特点,与现有技术相比本发明中的ni含量9-10%,降低了含量;nb含量0.6-1.1%,降低了含量;有效的控制了c,si含量,提高了材料的韧性指标,加入了n元素0.15-0.2%,氮元素是强奥氏体化元素,增加n元素含量有利于形成单一的奥氏体组织,抑制铁素体的形成。与nb形成第二相nbn,可以起到强化基体的作用。
14.本发明相比高镍奥氏体材料,本发明的效果是:1、ni降低到9-10%,相比高镍奥氏体材料,降低ni加入量在25%以上,按1kg的重量计算,可以少加入0.25kg的ni,需要补对应重量的fe 量,fe按3.3元/kg计算,目前按ni的价格110元/kg,可以降低26.7元/支产品,按年产100-200万只涡轮增压器规模考虑,可以降低2500万以上的费用,经济效益显著;nb补充到0.6-1.1%,相比高镍奥氏体材料,额外增加了加nb的费用,同样按1kg计算,增加0.009kg的nb,目前按nb的价格195元/kg计算,增加了费用1.76元/支产品,按年产100-200万只涡轮增压器规模考虑,增加了176万-350万费用;综上合计总节省成本最少在2000万/年以上。另外,本发明材料的工作温度可以满足最高温度到1050℃。
15.本发明相比一般奥氏体耐热钢材料,本发明的效果是:1、ni降低到9-10%,相比奥氏体耐热钢材料,降低ni加入量在10%以上,按1kg的重量计算,可以少加入0.1kg的ni,需要补对应重量的fe 量,fe按3.3元/kg计算,目前按ni的价格110元/kg,可以降低10.7元/支产品,按年产100-200万只涡轮增压器规模考虑,可以降低1000万以上的费用。2、nb降低到
0.6-1.1%,相比奥氏体耐热钢材料,降低nb加入量在0.6%以上 ,按同样按1kg计算,减少0.006kg的nb,需要补对应重量的fe 量,fe按3.3元/kg计算,目前按nb的价格195元/kg计算,减少了费用1.15元/支产品,按年产100-200万只涡轮增压器规模考虑,可以降低100万以上的费用,经济效益显著。3、相比奥氏体耐热钢材料,每年生产100-200万只涡轮增压器规模考虑,可以少加电解镍100吨以上,铌铁(60#)6吨左右,节省了国家宝贵矿产资源。4、有效控制了c和si元素,提高了材料的韧性指标。5、添加了n元素,氮元素是强奥氏体化元素,增加n元素含量有利于形成单一的奥氏体组织,抑制铁素体的形成。与nb形成第二相nbn,可以起到强化基体的作用。
16.本发明耐热性能分析:本发明的中心是在降低生产制作成本的前提下,形成奥氏体的基体组织,能满足材料的性能指标,提高高温强度,能持续满足1050℃以下的工作温度。
17.耐热性能的需要从两点进行说明,第一点是奥氏体化,减少出现其他基体组织。第二点是通过部分元素的合理搭配,形成的化合物会细化晶粒,在基体组织中,弥散分布的形态,对材料起到强化的作用。
18.ni元素是必不可少的奥氏体形成元素,本发明设定范围在9-10%。另外增加强奥氏体化元素n的含量,本发明设定的范围0.15-0.2%,为组织中奥氏体化奠定基础。
19.适当的加入nb元素,本发明的设定范围为0.6-1.1%,会形成高熔点的nb(c,n)化合物,合适的分布形态(短棒状,粒状等),起到提高材料强度的作用。过多的nb元素,会造成含nb化合物的数量增多,且尺寸长大(形成连续的网状,大的长条状),减弱强化作用,这对材料的高温性能是不利的。
20.综上所述,本发明材料中,特别是有效的控制降低了ni,nb贵重元素的加入,这两种元素是国家非常重要的资源,符合目前的环保理念。适当的提高c含量,可以有利于稳定形成奥氏体组织,并形成高温碳化物,提高高温强度,能持续满足1050℃以上的工作温度。降低si含量,可以适当的降低硬度,提高产品的韧性指标。ni降低到9-10%,极大地降低了成本,并能保证形成奥氏体基体组织。nb降低到0.6-1.1%,极大地降低了成本,并能保证形成足够的高温组织,保证强度。加入了0.15-0.2%的氮元素,氮元素是强奥氏体化元素,增加n元素含量有利于形成单一的奥氏体组织,抑制铁素体的形成。与nb形成第二相nbn,可以起到强化基体的作用。
附图说明
21.图1为本发明一种汽车涡轮增压器壳体铸钢材料的500倍金相组织照片;图2为现有技术中奥氏体耐热钢1的500倍金相组织照片;图3为现有技术中奥氏体耐热钢2的500倍金相组织照片。
具体实施方式
22.为更好地理解本发明,下面以具体实施例对本发明做进一步说明。
23.本发明提供一种汽车涡轮增压器壳体铸钢材料,由以下重量百分比的组分组成:c:0.35-0.5%,si:1.0-1.8%,ni:9-10%,nb:0.6-1.1%,n:0.15-0.2%,余量为fe。
24.实施例一,一种汽车涡轮增压器壳体铸钢材料,由以下重量百分比的组分组成:c:
0.44%,si:1.8%,ni:9.85%,nb:1.09%,n:0.16%,余量为fe。产品性能:抗拉强度573mpa,屈服强度375mpa,伸长率12.98%。
25.实施例二,一种汽车涡轮增压器壳体铸钢材料,由以下重量百分比的组分组成:c:0.42%,si:1.71%,ni:10%,nb:1.01%,n:0.17%,余量为fe。产品性能:抗拉强度620mpa,屈服强度411mpa,伸长率15%。
26.实施例三,一种汽车涡轮增压器壳体铸钢材料,由以下重量百分比的组分组成:c:0.43%,si:1.74%,ni:9.5%,nb:0.95%,n:0.15%,余量为fe。产品性能:抗拉强度591mpa,屈服强度384mpa,伸长率11.86%。
27.实施例四,一种汽车涡轮增压器壳体铸钢材料,由以下重量百分比的组分组成:c:0.37%,si:1.31%,ni:10.0%,nb:0.9%,n:0.18%,余量为fe。产品性能:抗拉强度560mpa,屈服强度389mpa,伸长率11.24%。
28.实施例五,一种汽车涡轮增压器壳体铸钢材料,由以下重量百分比的组分组成:c:0.38%,si:1.57%,ni:9.2 %,nb:0.67%,n:0.19%,余量为fe。产品性能:抗拉强度559mpa,屈服强度389mpa,伸长率13.94%。
29.实施例六,一种汽车涡轮增压器壳体铸钢材料,由以下重量百分比的组分组成:c:0.35%,si:1.0%,ni:10%,nb:0.6%,n:0.15%,余量为fe。
30.实施例七,一种汽车涡轮增压器壳体铸钢材料,由以下重量百分比的组分组成:c:0.5%,si:1.8%,ni:9%,nb:1.1%,n:0.2%,余量为fe。
31.本发明还提出一种汽车涡轮增压器壳体的制备工艺:包括以下内容:1)使用中频感应电炉作为熔化设备;2)需要的原材料包括废钢,电解镍,铌铁,微碳铬铁,氮化铬铁,硅铁,电解锰;3)备料:使用按重量百分比计的各原材料,废钢39.5-41.2%,电解镍9.1-10.1%,铌铁1.1-1.8%,微碳铬铁和氮化铬铁共45.1%,硅铁2.0%,电解锰1.0%,增碳剂0.4%,达到下列元素的控制范围c:0.35-0.50%,si:1.0-1.8%,ni:9-10%,nb:0.6-1.1%,n:0.15-0.2%,余量为fe;4)熔化步骤:熔化过程:第一步,在炉底加入增碳剂,氮化铬铁,废钢,后根据熔化的进度,依次加入铌铁,微碳铬铁,电解镍;第二步,升温到1560℃以上时,进行成分检查,硅锰元素除外,达到要求后;第三步,加入硅铁,电解锰,再次确认所有控制的化学成分在目标范围后,升温,待钢水温度达到产品工艺要求的出炉温度后停止供电,让钢水静置,扒除表面渣滓,最后出炉浇注产品;钢水等待时温度和时间要求:根据浇注涡轮增压器壳体的产品特性,一般在炉内钢水大于1600℃,等待的时间要小于60分钟,长时间的高温等待,会提高钢水的含气量,恶化微观组织,造成产品的功能失效;5)浇注过程:浇注设备为自动浇注机;根据产品的差异,程序设定浇注过程参数,如浇注重量和浇注时间;此方法优势为每型浇注重量控制波动小,一般在
±
1kg内;采用大流量,快流速,浇注状态稳定,基本无飞溅现象。
32.性能测试为对本发明充分公开,提供以下性能测试及其实验数据:
下表1为:根据本发明一种汽车涡轮增压器壳体铸钢材料各组分值的搭配,测试出的性能数据,以及与现有技术中高镍奥氏体,奥氏体耐热钢的性能数据比较,具体见下表1;性能测试还提供了本发明一种汽车涡轮增压器壳体铸钢材料的金相组织照片参看图1,以及现有技术中两种奥氏体耐热钢1、2的金相组织照片参看图2、3。通过金相照片对比,能够说明:图1中的碳化物数量变化不大,单个尺寸偏小,且呈粒状形态的碳化物数量要多于后两图,碳化物对材料的强化作用得到提升,这对材料的性能是有利的。