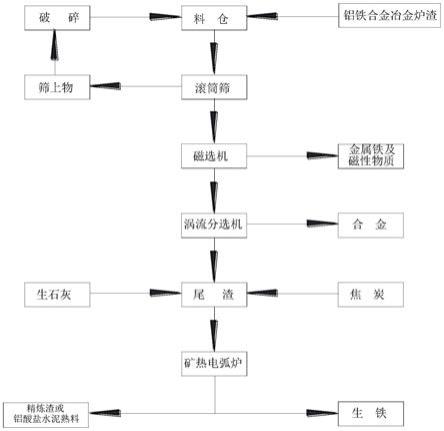
1.本发明涉及冶金炉渣资源化利用技术领域,尤其涉及一种用于炼钢的铝铁合金冶金炉渣的处理方法。
背景技术:
2.金属铝作为一种深脱氧剂在炼钢过程中被广泛使用,已经具有悠久的历史,其良好的脱氧性能已得到大家的认同。但由于铝熔点低、密度小,高温易氧化,在钢水表面产生铝漂浮和裹渣现象,因此难以加到钢水深部,在钢水中烧损大,利用率低,脱氧效果不稳定,控制钢中残铝量困难,一般平均收得率只有10~20%。同时,其脱氧产物al2o3夹杂物熔点高(2054℃),尺寸小,绝大部分夹杂物的尺寸小于50微米,在钢液内这种小尺寸的夹杂物不易上浮。尽管在精炼时采用了多种措施,但通常钢液中夹杂物含量仍较高,严重降低了钢材的使用性能,甚至使钢材报废。尤其是对于一些对夹杂物种类和含量要求十分严格的钢种,对夹杂物的控制尤为困难。同时钢中高熔点的al2o3也易在水口处形成结瘤,堵塞水口,影响连铸顺行。因此,如何在炼钢脱氧过程中提高铝的利用率和将钢液中的夹杂物含量降低到理想水平,始终是冶金工作者主要研究的工作内容。为解决纯铝脱氧存在的上述问题,经过不断研究和实践,把铝和铁制成合金,采用合金形式的脱氧剂进行脱氧取得成效。这是由于合金密度大,易在钢水中下沉,烧损氧化少,脱氧效果好,因此近年来代替纯铝广泛用于炼钢脱氧。利用铝铁合金脱氧,铝的收得率一般在50%以上,解决了纯铝脱氧利用率低的问题。但是这种单纯由铝和铁组成的合金没有解决脱氧产物al2o3夹杂物去除问题,因此人们经过不断探索,在铝铁合金的基础上加入了一定量的金属锰或金属钙、镁等与氧结合力强的金属制成铝锰铁、铝钙铁、铝镁钙铁等高效复合合金,实践证明这类复合合金除具有脱氧效果好、消耗低等特点外,还具有显著的去夹杂效果。使用复合合金脱氧生成的复合脱氧产物,易于上浮,去夹杂效果好。使用证明两种或两种以上的脱氧元素共同脱氧,效果优于单一元素脱氧。主要原理是两种或两种以上的脱氧元素可以增强彼此单独存在时的脱氧能力。锰、钙、镁在脱氧脱硫的同时,还有效改变夹杂物的形态,使三氧化二铝和二氧化硅等被转变成钙铝酸盐或钙硅酸盐,与硫化物一起形成复合型夹杂物,并由高熔点的链条形夹杂物转变成低熔点的球形夹杂物,利于夹杂物的上浮去除,提高了钢水纯净度,在解决了水口处结瘤堵塞的同时,也改善了钢材性能。
3.这类含铝量高的合金一般采用中频炉重熔法生产,根据品种的不同,原料主要有铝锭、金属钙、金属镁、金属锰、废钢等纯金属或合金。合金在生产时会产生一定量的炉渣,这些炉渣主要由10~20%合金,35~55%fe2o3·
feo、40~60%al2o3以及少量钙、镁、锰氧化物及其它氧化物组成。由于合金基本采用纯金属为原料,因此渣中除合金、fe2o3·
feo、al2o3外其它杂质极少。在现有传统工艺中,这些炉渣的处理办法一般是待这些炉渣冷却后,采用人工挑选和筛分的方法,回收其中的合金。由于这类合金多为脆性合金,在渣中大多数碎裂为细小颗粒,因此现有方法回收率极低,一般回收率只有渣中合金总量的30%左右,约占炉渣总量的5~8%,损失较大,劳动强度大,工作环境差。人工挑选后剩余炉渣一般采取
堆弃或填埋措施,这不但造成大量资源浪费,也造成了环境污染。
技术实现要素:
4.本发明所要解决的技术问题是提供一种用于炼钢的铝铁合金冶金炉渣的资源化处理方法,使资源得到充分利用,基本做到废渣零排放。
5.为实现上述目的,本发明采用以下技术方案实现:
6.一种用于炼钢的铝铁合金冶金炉渣的资源化处理方法,铝铁合金冶金炉渣经磁选分离出金属铁及磁性物质,再经分选机分离出合金,剩余尾渣配入生石灰、焦炭,在矿热炉中还原出金属铁,同时获得铝酸钙渣;具体步骤包括:
7.①
将铝铁合金冶金炉渣进行分级,通过滚筒筛将铝铁合金冶金炉渣筛分为0~10mm、10~30mm以及30mm以上三种粒度级别;
8.②
将30mm以上级别的铝铁合金冶金炉渣采用锤式破碎机破碎后,通过滚筒筛继续筛分为0~10mm、10~30mm粒度级别;
9.③
对同一粒度级别的铝铁合金冶金炉渣经过磁选机选出金属铁及磁性物质;
10.④
磁选后同一粒度级别的物料,进入涡流分选机分选出合金;
11.⑤
将分级分选后的全部尾渣配入焦碳和生石灰,将配合料搅拌均匀加入矿热电弧炉中,加热冶炼;
12.⑥
出炉时,将液态炉渣及液态铁放入铁水包内,静止等待1~3min,将炉渣倒入铸铁包内冷却、破碎,获得铝酸钙渣;将铁水包内的液态铁浇注在锭模内冷却成块状生铁。
13.步骤
④
中涡流分选机磁场强度≥5000gs。
14.步骤
⑤
中将分选后0~10mm粒度级别的尾渣压成20~50mm的块料。
15.步骤
⑤
中焦碳粒度为5~15mm,生石灰粒度20~100mm。
16.与现有的技术相比,本发明的有益效果是:
17.⑴
大幅提高了渣中合金的回收率和回收效率,机械化程度提高,节省人力。
18.⑵
处理方法简单、方便,工艺流程短,新的自然资源消耗较少,在各环节采取适当的除尘措施,则对环境没有二次污染,基本实现污染物零排放。
19.⑶
将固体废物加工制作成新产品,实现固体废物资源化处理,且基本没有新的固废产生,利于降本增效,实现经济效益的最大化。
20.⑷
在保护环境的同时,固废得到充分利用,节约自然资源和土地的占用,使废物中有用资源得到最大限度的回收与综合利用,极大促进了社会的可持续发展。
附图说明
21.图1为本发明的流程图。
具体实施方式
22.下面结合附图对本发明的具体实施方式进一步说明:
23.如图1,一种用于炼钢的铝铁合金冶金炉渣的资源化处理方法,包括以下具体步骤:
24.1.铝铁合金冶金炉渣分级:将铝铁合金冶金炉渣通过滚筒筛筛分为0~10mm、10~
30mm以及30mm以上三种粒度级别,30mm以上粒度级别的铝铁合金冶金炉渣经过破碎、筛分成0~10mm、10~30mm粒度级别;
25.2.0~10mm粒度级别铝铁合金冶金炉渣的分选
26.1)磁选:取0~10mm粒度级别铝铁合金冶金炉渣放入料仓内,开动磁选机,运转正常后,开启振动给料器,将料仓内的铝铁合金冶金炉渣均匀分布在运输带上,通过磁选机分离出金属铁及磁性物质;
27.2)将磁选过后的铝铁合金冶金炉渣通过运输带均匀送入涡流分选机中,调整皮带速度为1.2~1.4m/s,涡流分选机磁场强度≥5000gs,磁辊转速为1200~1400r/min,分隔板开口度为15~20mm,分选出炉渣中的合金,合金通过溜槽及皮带进入合金仓,尾渣通过溜槽及皮带进入尾渣仓,等待下一步处理;
28.3.10~30mm粒度级别铝铁合金冶金炉渣的分选
29.1)磁选:取10~30mm粒度级别铝铁合金冶金炉渣放入料仓内,开动磁选机,运转正常后,开启振动给料器,将料仓内的铝铁合金冶金炉渣均匀分布在运输带上,通过磁选机分离出金属铁及磁性物质;
30.2)将磁选过后的铝铁合金冶金炉渣通过运输带均匀送入涡流分选机中,调整皮带速度为1.4~1.6m/s,涡流分选机磁场强度≥5000gs,磁辊转速为1000~1200r/min,分隔板开口度为35~40mm,分选出炉渣中的合金,合金通过溜槽及皮带进入合金仓,尾渣通过溜槽及皮带进入尾渣仓,等待下一步处理;
31.普通涡流分选机一般用来分选铝、铜等有色金属,通常高电导率、低密度的金属材料所受斥力最大的分选效果好,而分别占比40~60%的铁和铝组成的合金,与金属铝比其密度大(是金属铝的1.5~2倍)导电率确大大低于铝。与铜比密度虽然比铜小,但其导电率确远不如铜,因此常规涡流分选机难以满足要求,因此本发明中采用高磁场强度的涡流分选机,经过计算和试验,磁场强度≥5000gs;并根据分选粒级不同,调整渣料输送皮带的速度和磁辊转速,以便于达到最佳分选效果。
32.4.将分级分选后的全部尾渣配入焦碳和生石灰,将配合料搅拌均匀加入矿热电弧炉中,加热冶炼;
33.5.出炉时,将液态炉渣及液态铁放入铁水包内,静止等待1~3min,将炉渣倒入铸铁模内冷却、破碎,获得铝酸钙渣(精炼渣或铝酸盐水泥熟料);将铁水包内的液态铁浇注在锭模内冷却成块状生铁。
34.实施例1
35.一种用于炼钢的铝铁合金冶金炉渣的资源化处理方法,具体包括:
36.1.分级:将铝铁合金冶金炉渣进行分级,通过滚筒筛将铝铁合金冶金炉渣筛分为0~10mm、10~30mm以及30mm以上三种粒度级别;将30mm以上级别的铝铁合金冶金炉渣采用锤式破碎机破碎后,通过滚筒筛继续筛分为0~10mm、10~30mm粒度级别;
37.2.0~10mm粒度级别铝铁合金冶金炉渣的分选
38.1)磁选:取0~10mm粒度级别铝铁合金冶金炉渣放入料仓内,开动磁选机,运转正常后,开启振动给料器,将料仓内的铝铁合金冶金炉渣均匀分布在运输带上,通过磁选机分离出金属铁及磁性物质;
39.2)将磁选过后的铝铁合金冶金炉渣通过运输带均匀送入涡流分选机中,调整皮带
速度为1.2~1.4m/s,涡流分选机磁场强度≥5000gs,磁辊转速为1200~1400r/min,分隔板开口度为15~20mm,分选出炉渣中的合金,合金通过溜槽及皮带进入合金仓,尾渣通过溜槽及皮带进入尾渣仓,等待下一步处理;
40.3.10~30mm粒度级别铝铁合金冶金炉渣的分选
41.1)磁选:取10~30mm粒度级别铝铁合金冶金炉渣放入料仓内,开动磁选机,运转正常后,开启振动给料器,将料仓内的铝铁合金冶金炉渣均匀分布在运输带上,通过磁选机分离出金属铁及磁性物质;
42.2)将磁选过后的铝铁合金冶金炉渣通过运输带均匀送入涡流分选机中,调整皮带速度为1.4~1.6m/s,涡流分选机磁场强度≥5000gs,磁辊转速为1000~1200r/min,分隔板开口度为35~40mm,分选出炉渣中的合金,合金通过溜槽及皮带进入合金仓,尾渣通过溜槽及皮带进入尾渣仓,等待下一步处理;
43.4.尾渣处理
44.1)经检验尾渣成分为:feo42%,al2o356%,其它为少量杂质。
45.2)将0~10mm粒度级别的尾渣压成20~50mm块状物料;
46.3)将压块后的尾渣和其余尾渣混合,加入生石灰和焦炭,尾渣、生石灰、焦炭按1:0.60:0.08的比例配料,混匀,生石灰:cao≥85%;生石灰粒度20~100mm,焦炭:c≥82%;焦炭粒度5~15mm。
47.4)将上述物料加入到镁质耐材作为炉衬的矿热电弧炉内,加热冶炼,完成氧化铁的还原;
48.5)出炉时将液态炉渣及液态铁一同放入铁水包内,静止等待1~3min,使得渣铁分离良好,将炉渣倒入铸铁模内冷却,破碎成10~40mm块状即可作为炼钢精炼剂使用。炼钢精炼剂的成分是:cao50.6%,al2o348.3%其它为少量不可避免的杂质;将铁水包内的液态铁浇注在锭模内冷却成块状生铁,可用于炼钢或铸造原料。
49.实施例2
50.一种用于炼钢的铝铁合金冶金炉渣的资源化处理方法,具体包括:
51.1.分级:将铝铁合金冶金炉渣进行分级,通过滚筒筛将铝铁合金冶金炉渣筛分为0~10mm、10~30mm以及30mm以上三种粒度级别;将30mm以上级别的铝铁合金冶金炉渣采用锤式破碎机破碎后,通过滚筒筛继续筛分为0~10mm、10~30mm粒度级别;
52.2.0~10mm粒度级别铝铁合金冶金炉渣的分选
53.1)磁选:取0~10mm粒度级别铝铁合金冶金炉渣放入料仓内,开动磁选机,运转正常后,开启振动给料器,将料仓内的铝铁合金冶金炉渣均匀分布在运输带上,通过磁选机分离出金属铁及磁性物质;
54.2)将磁选过后的铝铁合金冶金炉渣通过运输带均匀送入涡流分选机中,调整皮带速度为1.2~1.4m/s,涡流分选机磁场强度≥5000gs,磁辊转速为1200~1400r/min,分隔板开口度为15~20mm,分选出炉渣中的合金,合金通过溜槽及皮带进入合金仓,尾渣通过溜槽及皮带进入尾渣仓,等待下一步处理;
55.3.10~30mm粒度级别铝铁合金冶金炉渣的分选
56.1)磁选:取10~30mm粒度级别铝铁合金冶金炉渣放入料仓内,开动磁选机,运转正常后,开启振动给料器,将料仓内的铝铁合金冶金炉渣均匀分布在运输带上,通过磁选机分
离出金属铁及磁性物质;
57.2)将磁选过后的铝铁合金冶金炉渣通过运输带均匀送入涡流分选机中,调整皮带速度为1.4~1.6m/s,涡流分选机磁场强度≥5000gs,磁辊转速为1000~1200r/min,分隔板开口度为35~40mm,分选出炉渣中的合金,合金通过溜槽及皮带进入合金仓,尾渣通过溜槽及皮带进入尾渣仓,等待下一步处理;
58.4.尾渣处理
59.1)经检验尾渣成分为:feo48%,al2o351%,其它为少量杂质。
60.2)将0~10mm粒度级别的尾渣压成20~50mm块状物料;
61.3)将压块后的尾渣和其余尾渣混合,加入生石灰和焦炭,尾渣、生石灰、焦炭按1:0.50:0.10的比例配料,混匀,生石灰:cao≥85%;生石灰粒度20~100mm,焦炭:c≥82%;焦炭粒度5~15mm。
62.4)将上述物料加入到镁质耐材作为炉衬的矿热电弧炉内,加热冶炼,完成氧化铁的还原;
63.5)出炉时将液态炉渣及液态铁一同放入铁水包内,静止等待1~3min,使得渣铁分离良好,将炉渣倒入铸铁模内冷却,破碎成10~40mm块状即可作为炼钢精炼剂使用。炼钢精炼剂的成分是:cao50.3%,al2o347.5%其它为少量不可避免的杂质;将铁水包内的液态铁浇注在锭模内冷却成块状生铁,可用于炼钢或铸造原料。
64.实施例3
65.一种用于炼钢的铝铁合金冶金炉渣的资源化处理方法,具体包括:
66.1.分级:将铝铁合金冶金炉渣进行分级,通过滚筒筛将铝铁合金冶金炉渣筛分为0~10mm、10~30mm以及30mm以上三种粒度级别;将30mm以上级别的铝铁合金冶金炉渣采用锤式破碎机破碎后,通过滚筒筛继续筛分为0~10mm、10~30mm粒度级别;
67.2.0~10mm粒度级别铝铁合金冶金炉渣的分选
68.1)磁选:取0~10mm粒度级别铝铁合金冶金炉渣放入料仓内,开动磁选机,运转正常后,开启振动给料器,将料仓内的铝铁合金冶金炉渣均匀分布在运输带上,通过磁选机分离出金属铁及磁性物质;
69.2)将磁选过后的铝铁合金冶金炉渣通过运输带均匀送入涡流分选机中,调整皮带速度为1.2~1.4m/s,涡流分选机磁场强度≥5000gs,磁辊转速为1200~1400r/min,分隔板开口度为15~20mm,分选出炉渣中的合金,合金通过溜槽及皮带进入合金仓,尾渣通过溜槽及皮带进入尾渣仓,等待下一步处理;
70.3.10~30mm粒度级别铝铁合金冶金炉渣的分选
71.1)磁选:取10~30mm粒度级别铝铁合金冶金炉渣放入料仓内,开动磁选机,运转正常后,开启振动给料器,将料仓内的铝铁合金冶金炉渣均匀分布在运输带上,通过磁选机分离出金属铁及磁性物质;
72.2)将磁选过后的铝铁合金冶金炉渣通过运输带均匀送入涡流分选机中,调整皮带速度为1.4~1.6m/s,涡流分选机磁场强度≥5000gs,磁辊转速为1000~1200r/min,分隔板开口度为35~40mm,分选出炉渣中的合金,合金通过溜槽及皮带进入合金仓,尾渣通过溜槽及皮带进入尾渣仓,等待下一步处理;
73.4.尾渣处理
74.1)经检验尾渣成分为:feo31.8%,al2o367.1%,其它为少量杂质。
75.2)将0~10mm粒度级别的尾渣压成20~50mm块状物料;
76.3)将压块后的尾渣和其余尾渣混合,加入生石灰和焦炭,尾渣、生石灰、焦炭按1:0.8:0.07的比例配料,混匀,生石灰:cao≥85%;生石灰粒度20~100mm,焦炭:c≥82%;焦炭粒度5~15mm。
77.4)将上述物料加入到镁质耐材作为炉衬的矿热电弧炉内,加热冶炼,完成氧化铁的还原;
78.5)出炉时将液态炉渣及液态铁一同放入铁水包内,静止等待1~3min,使得渣铁分离良好,将炉渣倒入铸铁模内冷却,破碎成10~40mm块状即可作为炼钢精炼剂使用。炼钢精炼剂的成分是:cao54.6%,al2o344.5%其它为少量不可避免的杂质;将铁水包内的液态铁浇注在锭模内冷却成块状生铁,可用于炼钢或铸造原料。
79.实施例4
80.一种用于炼钢的铝铁合金冶金炉渣的资源化处理方法,具体包括:
81.1.分级:将铝铁合金冶金炉渣进行分级,通过滚筒筛将铝铁合金冶金炉渣筛分为0~10mm、10~30mm以及30mm以上三种粒度级别;将30mm以上级别的铝铁合金冶金炉渣采用锤式破碎机破碎后,通过滚筒筛继续筛分为0~10mm、10~30mm粒度级别;
82.2.0~10mm粒度级别铝铁合金冶金炉渣的分选
83.1)磁选:取0~10mm粒度级别铝铁合金冶金炉渣放入料仓内,开动磁选机,运转正常后,开启振动给料器,将料仓内的铝铁合金冶金炉渣均匀分布在运输带上,通过磁选机分离出金属铁及磁性物质;
84.2)将磁选过后的铝铁合金冶金炉渣通过运输带均匀送入涡流分选机中,调整皮带速度为1.2~1.4m/s,涡流分选机磁场强度≥5000gs,磁辊转速为1200~1400r/min,分隔板开口度为15~20mm,分选出炉渣中的合金,合金通过溜槽及皮带进入合金仓,尾渣通过溜槽及皮带进入尾渣仓,等待下一步处理;
85.3.10~30mm粒度级别铝铁合金冶金炉渣的分选
86.1)磁选:取10~30mm粒度级别铝铁合金冶金炉渣放入料仓内,开动磁选机,运转正常后,开启振动给料器,将料仓内的铝铁合金冶金炉渣均匀分布在运输带上,通过磁选机分离出金属铁及磁性物质;
87.2)将磁选过后的铝铁合金冶金炉渣通过运输带均匀送入涡流分选机中,调整皮带速度为1.4~1.6m/s,涡流分选机磁场强度≥5000gs,磁辊转速为1000~1200r/min,分隔板开口度为35~40mm,分选出炉渣中的合金,合金通过溜槽及皮带进入合金仓,尾渣通过溜槽及皮带进入尾渣仓,等待下一步处理;
88.4.尾渣处理
89.1)经检验尾渣主要成分:feo38%,al2o358%;
90.2)将0~10mm粒度级别的尾渣压成20~50mm块状物料;
91.3)将压块后的尾渣和其余尾渣混合,加入生石灰和焦炭,尾渣、生石灰、焦炭按1:0.40:0.08的比例配料,混匀,生石灰:cao≥85%;生石灰粒度20~100mm,焦炭:c≥82%;焦炭粒度5~15mm;
92.4)将上述物料加入到镁质耐材作为炉衬的矿热电弧炉内,加热冶炼,完成氧化铁
的还原;
93.5)出炉时将液态炉渣及液态铁一同放入铁水包内,静止等待1~3min,使得渣铁分离良好,将炉渣倒入铸铁模内冷却,破碎,获得铝酸盐水泥熟料;铝酸盐水泥熟料的成分是:cao35%,al2o362.6%,fe2o30.7%、sio20.15%其它为少量不可避免的杂质;将铁水包内的液态铁浇注在锭模内冷却成块状生铁,可用于炼钢或铸造原料。
94.实施例5
95.一种用于炼钢的铝铁合金冶金炉渣的资源化处理方法,具体包括:
96.1.分级:将铝铁合金冶金炉渣进行分级,通过滚筒筛将铝铁合金冶金炉渣筛分为0~10mm、10~30mm以及30mm以上三种粒度级别;将30mm以上级别的铝铁合金冶金炉渣采用锤式破碎机破碎后,通过滚筒筛继续筛分为0~10mm、10~30mm粒度级别;
97.2.0~10mm粒度级别铝铁合金冶金炉渣的分选
98.1)磁选:取0~10mm粒度级别铝铁合金冶金炉渣放入料仓内,开动磁选机,运转正常后,开启振动给料器,将料仓内的铝铁合金冶金炉渣均匀分布在运输带上,通过磁选机分离出金属铁及磁性物质;
99.2)将磁选过后的铝铁合金冶金炉渣通过运输带均匀送入涡流分选机中,调整皮带速度为1.2~1.4m/s,涡流分选机磁场强度≥5000gs,磁辊转速为1200~1400r/min,分隔板开口度为15~20mm,分选出炉渣中的合金,合金通过溜槽及皮带进入合金仓,尾渣通过溜槽及皮带进入尾渣仓,等待下一步处理;
100.3.10~30mm粒度级别铝铁合金冶金炉渣的分选
101.1)磁选:取10~30mm粒度级别铝铁合金冶金炉渣放入料仓内,开动磁选机,运转正常后,开启振动给料器,将料仓内的铝铁合金冶金炉渣均匀分布在运输带上,通过磁选机分离出金属铁及磁性物质;
102.2)将磁选过后的铝铁合金冶金炉渣通过运输带均匀送入涡流分选机中,调整皮带速度为1.4~1.6m/s,涡流分选机磁场强度≥5000gs,磁辊转速为1000~1200r/min,分隔板开口度为35~40mm,分选出炉渣中的合金,合金通过溜槽及皮带进入合金仓,尾渣通过溜槽及皮带进入尾渣仓,等待下一步处理;
103.4.尾渣处理
104.1)经检验尾渣主要成分:feo55.2%,al2o343.5%;
105.2)将0~10mm粒度级别的尾渣压成20~50mm块状物料;
106.3)将压块后的尾渣和其余尾渣混合,加入生石灰和焦炭,尾渣、生石灰、焦炭按1:0.22:0.12的比例配料,混匀,生石灰:cao≥85%;生石灰粒度20~100mm,焦炭:c≥82%;焦炭粒度5~15mm;
107.4)将上述物料加入到镁质耐材作为炉衬的矿热电弧炉内,加热冶炼,完成氧化铁的还原;
108.5)出炉时将将液态炉渣及液态铁一同放入铁水包内,静止等待1~3min,使得渣铁分离良好,将炉渣倒入铸铁模内冷却,破碎,获得铝酸盐水泥熟料;铝酸盐水泥熟料的成分是:cao28%,al2o370.8%,fe2o30.5%、sio20.13%其它为少量不可避免的杂质;将铁水包内的液态铁浇注在锭模内冷却成块状生铁,可用于炼钢或铸造原料。
109.实施例6
110.一种用于炼钢的铝铁合金冶金炉渣的资源化处理方法,具体包括:
111.1.分级:将铝铁合金冶金炉渣进行分级,通过滚筒筛将铝铁合金冶金炉渣筛分为0~10mm、10~30mm以及30mm以上三种粒度级别;将30mm以上级别的铝铁合金冶金炉渣采用锤式破碎机破碎后,通过滚筒筛继续筛分为0~10mm、10~30mm粒度级别;
112.2.0~10mm粒度级别铝铁合金冶金炉渣的分选
113.1)磁选:取0~10mm粒度级别铝铁合金冶金炉渣放入料仓内,开动磁选机,运转正常后,开启振动给料器,将料仓内的铝铁合金冶金炉渣均匀分布在运输带上,通过磁选机分离出金属铁及磁性物质;
114.2)将磁选过后的铝铁合金冶金炉渣通过运输带均匀送入涡流分选机中,调整皮带速度为1.2~1.4m/s,涡流分选机磁场强度≥5000gs,磁辊转速为1200~1400r/min,分隔板开口度为15~20mm,分选出炉渣中的合金,合金通过溜槽及皮带进入合金仓,尾渣通过溜槽及皮带进入尾渣仓,等待下一步处理;
115.3.10~30mm粒度级别铝铁合金冶金炉渣的分选
116.1)磁选:取10~30mm粒度级别铝铁合金冶金炉渣放入料仓内,开动磁选机,运转正常后,开启振动给料器,将料仓内的铝铁合金冶金炉渣均匀分布在运输带上,通过磁选机分离出金属铁及磁性物质;
117.2)将磁选过后的铝铁合金冶金炉渣通过运输带均匀送入涡流分选机中,调整皮带速度为1.4~1.6m/s,涡流分选机磁场强度≥5000gs,磁辊转速为1000~1200r/min,分隔板开口度为35~40mm,分选出炉渣中的合金,合金通过溜槽及皮带进入合金仓,尾渣通过溜槽及皮带进入尾渣仓,等待下一步处理;
118.4.尾渣处理
119.1)经检验尾渣主要成分:feo40.3%,al2o357.9%;
120.2)将0~10mm粒度级别的尾渣压成20~50mm块状物料;
121.3)将压块后的尾渣和其余尾渣混合,加入生石灰和焦炭,尾渣、生石灰、焦炭按1:0.55:0.08的比例配料,混匀,生石灰:cao≥85%;生石灰粒度20~100mm,焦炭:c≥82%;焦炭粒度5~15mm;
122.4)将上述物料加入到镁质耐材作为炉衬的矿热电弧炉内,加热冶炼,完成氧化铁的还原;
123.5)出炉时将液态炉渣及液态铁一同放入铁水包内,静止等待1~3min,使得渣铁分离良好,将炉渣倒入铸铁模内冷却,破碎成块状,获得铝酸盐水泥熟料。铝酸盐水泥熟料的成分是:cao 43.5%,al2o
3 55.6%,fe2o
3 2.2%、sio
2 1.25%其它为少量不可避免的杂质;将铁水包内的液态铁浇注在锭模内冷却成块状生铁,可用于炼钢或铸造原料。
124.采用磁选和高磁场强度涡流分选方法分选出铁及合金。剩余尾渣配入石灰、焦炭,在矿热电弧炉中还原出金属铁,同时生产高纯度铝酸钙渣,该渣即是一种重要的炼钢精炼剂,也是一种优质铝酸盐水泥熟料。
125.该炉渣处理方法合金回收率高,可达90%,不但可回收渣中绝大部分合金,而且使废渣得到充分利用,基本实现零排放,提高了资源利用率,节约了大量自然资源,同时也保护了环境。
126.该方法具有工艺简单,流程短、成本低等优点。与现有方法比大幅提高了渣中合金
的回收率和回收效率,机械化程度提高,节省人力物力。将固体废物加工制作成新产品,实现固体废物资源化处理,基本没有新的固废产生,新的自然资源消耗较少,利于降本增效,实现经济效益的最大化。在保护环境的同时,使废物得到最大限度的回收与综合利用,利于社会的可持续发展。
127.对于本技术领域的普通技术人员来说,在不脱离本发明原理的前提下,还可以对本发明进行改进与修饰,这些改进和修饰也落入本发明权利要求的保护范围内。以上所述,仅为本发明较佳的具体实施方式,但本发明的保护范围并不局限于此,任何熟悉本技术领域的技术人员在本发明揭露的技术范围内,根据本发明的技术方案及其构思加以等同替换或改变,都应涵盖在本发明的保护范围之内。