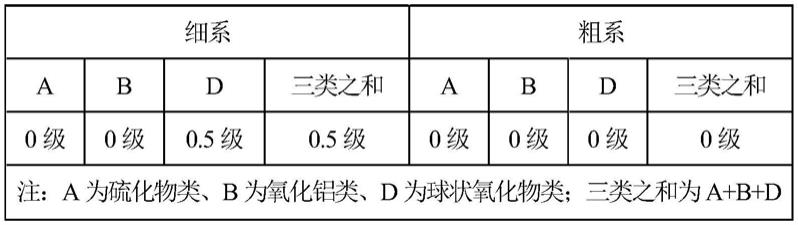
一种90mpa氢压机膜片用高强度耐氢脆板材的制备方法
技术领域
1.本发明涉及氢能装备关键材料部件领域,具体地说是一种90mpa氢压机膜片用高强度耐氢脆板材的制备方法。
背景技术:
2.90mpa氢气隔膜压缩机(以下称氢压机)是70mpa加氢站建设所不可或缺的关键装备,其稳定性、可靠性和使用效率对整个加氢站至关重要。膜片是氢压机中的关键部件,不但起到隔离润滑油和压缩氢气的作用,而且在液压油传递的压力作用下做往复运动,从而达到增压的目的。应予指出的是,服役过程中,膜片面临高压、氢气,以及交变载荷和温度循环的复杂苛刻工况条件,易于产生氢致开裂,导致膜片失效破坏,是妨碍高压氢压机研发和工程应用的瓶颈问题。目前国内运行的30mpa示范加氢站中使用的氢压机设计压力为35mpa,其临氢气侧膜片材料较多使用316l不锈钢。工程实践发现,随着服役氢压升高至52mpa,临氢气侧316l膜片的服役寿命显著降低(寿命甚至不足35mpa加氢机的1/5~1/10);当服役氢压进一步升高至90mpa(70mpa加氢站用氢压机设计压力为90mpa)后,316l膜片的服役寿命甚至会降至不足35mpa加氢机寿命的1/10~1/20,究其原因在于膜片所用316l板材综合性能的不足(较低的高温强度和耐疲劳性能)。应看到的是,我国未来建设的加氢站正在向着70mpa压力级的方向发展,这对加氢站关键装备和部件提出了更高的要求。不言而喻,开发具有更为优异综合性能的耐氢脆奥氏体合金板材,满足90mpa及更高压力级别氢压机的设计和使用要求,需求十分迫切。
技术实现要素:
3.针对氢能装备关键材料部件需求,本发明的目的在于提供一种90mpa氢压机膜片用高强度耐氢脆板材的制备方法,以满足90mpa氢压机对高性能临氢膜片设计和使用的迫切要求。
4.本发明的技术方案是:
5.一种90mpa氢压机膜片用高强度耐氢脆板材的制备方法,板材宽度不小于800mm、厚度在0.4~0.6mm、长度不小于1000mm,板材表面粗糙度ra≤0.8μm、不平度不大于10mm/m,厚度精度
±
0.05mm;按重量百分比计,板材的主要成分范围如下:
6.ni:29.50~31.50,cr:14.00~16.00,mo:0.90~1.50,v:0.10~0.40,ti:1.80~2.40,al:0.60~0.80,b:0.001~0.0030,fe及不可避免的残余元素:余量;不可避免的残余元素包括:碳、硫、磷,碳含量控制在≤0.020,硫含量控制在≤0.005,磷含量控制在≤0.007;
7.所述的90mpa氢压机膜片用高强度耐氢脆板材的制备方法,该板材的制备具体过程如下:
8.(1)以磷含量低于0.007wt.%优质工业纯铁、电解镍、金属铬、金属钼及其它中间合金:硅铁、硼铁、钛铁和铝铁为原料,采用热稳定性高的坩埚进行真空感应熔炼,在1530~
1570℃精炼处理10~15分钟,随后依次加入硅铁、钛铁、铝铁、硼铁和脱硫剂,再进行5~15分钟精炼脱硫,在1480~1520℃浇铸铸锭;
9.(2)真空自耗冶炼;
10.(3)合金锻造;开坯锻造温度1050~1150℃,终锻温度880~1000℃,获得锻坯;在锻至最终规格前允许回炉再加热,在1050~1150℃下保温1~4h;
11.(4)合金热轧制;锻坯在1050~1150℃保温2~4h后进行热轧制,开坯轧制温度1050~1150℃,终轧温度850~950℃,获得4~6mm厚的热轧板材;在轧至最终规格前允许回炉再加热,在1050~1150℃下保温0.5~3h;
12.(5)合金冷轧制或精轧制;室温冷轧制每次退火间变形量30~70%、中间采用1020~1060℃保温15~60min去应力退火,获得0.4~0.6mm厚的冷轧板材,其晶粒度不低于6级;
13.(6)板材固溶处理;板材固溶处理温度控制在970~990℃、保温时间20~60min,空冷;
14.(7)板材小变形冷轧制;板材冷轧制变形量为10~15%;
15.(8)板材退火处理;板材退火处理制度为:980~1000℃保温0.5~1h;
16.(9)板材时效处理;板材时效处理制度为:730~750℃保温7~9h,炉冷。
17.所述的90mpa氢压机膜片用高强度耐氢脆板材的制备方法,板材中∑3n晶界比例不低于60%,n=1、2或3,∑≤29晶界比例不低于65%。
18.所述的90mpa氢压机膜片用高强度耐氢脆板材的制备方法,板材的室温力学性能满足:屈服强度(rp0.2)不低于600mpa,抗拉强度(rm)不低于950mpa,延伸率(a)不低于25%。
19.所述的90mpa氢压机膜片用高强度耐氢脆板材的制备方法,板材的250℃高温力学性能满足:屈服强度(rp0.2)不低于600mpa,抗拉强度(rm)不低于950mpa,延伸率(a)不低于23%。
20.所述的90mpa氢压机膜片用高强度耐氢脆板材的制备方法,300℃、10mpa、高纯氢(体积纯度≥99.999%)、72h的充氢处理后,板材的室温力学性能满足:屈服强度(rp0.2)不低于600mpa,抗拉强度(rm)不低于950mpa以上,延伸率(a)不低于20%。
21.所述的90mpa氢压机膜片用高强度耐氢脆板材的制备方法,板材在50%置信度下的疲劳极限不低于270mpa。
22.所述的90mpa氢压机膜片用高强度耐氢脆板材的制备方法,时效处理后板材中的非金属夹杂物满足如下要求:细系(m),a≤0.5级,b≤0.5级,d≤1.5级,三类之和≤2.5级;粗系(m),a≤0.5级,b≤0.5级,d≤1.0级,三类之和≤1.5级;其中,a为硫化物类、b为氧化铝类、d为球状氧化物类,三类之和为a+b+d。
23.所述的90mpa氢压机膜片用高强度耐氢脆板材的制备方法,板材固溶处理在真空或气体保护气淬热处理炉中进行,气淬介质为氩气;板材的退火处理在气体保护热处理炉中进行,保护气氛为氩气。
24.所述的90mpa氢压机膜片用高强度耐氢脆板材的制备方法,板材时效处理采用真空或还原性气体保护热处理炉。
25.本发明的设计思想为:
26.首先,在铁铬镍奥氏体合金的基础上,通过ti、al合金化在单相奥氏体合金中引入
纳米尺寸的γ
′‑
ni3(al,ti)强化相,获得高的室温和250℃高温强度,其室温和250℃屈服强度(rp0.2)都可达600mpa以上,同时兼有良好的塑性(室温延伸率高于25%,250℃延伸率高于23%)。其次,一方面通过采用真空感应加真空自耗冶炼制备,控制碳、硫和磷杂质元素含量和非金属夹杂物水平,降低板材合金中的强氢陷阱数量和尺寸,降低氢致裂纹萌生几率;另一方面,通过形变+热处理的晶界调控方法,降低合金中自由晶界数量、提升特殊晶界(低∑3n(n=1,2,3)重合位置点阵晶界)比例,显著提升板材的耐氢致沿晶界裂纹萌生与扩展阻力,从而使板材获得优异的耐氢脆能力。第三,通过降低非金属夹杂物水平和晶界调控处理,减少专用板材合金中的强氢陷阱数量(亦是疲劳裂纹源),可同时提升板材的疲劳极限和耐氢脆能力。
27.本发明的优点及有益效果是:
28.1、本发明的90mpa氢压机膜片用高强度耐氢脆板材,碳、硫和磷杂质元素和非金属夹杂物含量低、低∑重合位置点阵晶界比例高,具有优异的室温和250℃高温力学性能,抗氢脆性能优异,可在90mpa级的氢压机复杂苛刻工况下使用。
29.2、本发明板材的宽度不小于800mm、厚度在0.4~0.6mm、长度不小于1000mm,板材表面粗糙度ra≤0.8μm、不平度应不大于10mm/m,厚度精度
±
0.05mm。
30.3、本发明板材的∑3n特殊晶界比例不低于60%,∑≤29晶界比例度不低于65%。
31.4、本发明板材的室温力学性能满足:屈服强度(rp0.2)不低于600mpa,抗拉强度(rm)不低于950mpa,延伸率(a)不低于25%。
32.5、本发明板材的250℃高温力学性能满足:屈服强度(rp0.2)不低于600mpa,抗拉强度(rm)不低于950mpa,延伸率(a)不低于23%。
33.6、本发明板材在300℃、10mpa、高纯氢(体积纯度≥99.999%)、72h的充氢处理后的室温力学性能满足:屈服强度(rp0.2)不低于600mpa,抗拉强度(rm)不低于950mpa以上,延伸率(a)不低于20%。
34.7、本发明膜板材在50%置信度下的疲劳极限不低于270mpa,同时兼有良好的塑性、耐氢脆能力和耐疲劳性能,可在90mpa级氢气隔膜压缩机中作为临氢膜片使用。
附图说明
35.图1是板材晶界结构ebsd图。
36.图2是板材特殊晶界统计结果图;图中,横坐标代表晶界类型,纵坐标fraction代表特殊晶界比例(%)。
具体实施方式
37.在具体实施过程中,本发明基于纳米尺寸γ
′‑
ni3(al,ti)强化相的引入和晶界调控来保证板材的高强度和耐氢脆能力,通过真空感应熔炼
→
钢模铸造
→
真空自耗冶炼
→
锻造
→
热轧制
→
冷轧制
→
固溶处理
→
小变形冷轧
→
退火处理
→
时效处理的方法制备板材。本发明专用板材的宽度不小于800mm、厚度在0.4~0.6mm、长度不小于1000mm,板材表面粗糙度ra≤0.8μm、不平度不大于10mm/m,厚度精度
±
0.05mm。
38.下面,通过实施例对本发明进一步详细阐述。
39.实施例1:规格为1800mm
×
830mm
×
0.6mm的板材
40.采用铝镁尖晶石坩埚,在1.0吨真空感应炉上熔炼合金,熔炼过程中进行一次精炼和一次精炼脱硫处理,随后浇铸铸锭;铸锭经表面打磨处理后进行自耗冶炼,自耗冶炼铸锭经打磨处理后经锻造
→
热轧制
→
冷/精轧制
→
固溶
→
小变形冷轧
→
退火处理
→
时效处理制备成规格为1800mm
×
830mm
×
0.6mm的板材,其化学成分见表1,制备过程为:
41.1、以磷含量低于0.007wt.%工业纯铁(本实施例为0.006wt.%)、电解镍、金属铬、金属钼及其它中间合金(如:硅铁、钛铁、铝铁、硼铁和钒铁)为原料,熔炼前将fe、ni、cr和mo装入坩埚中,将硅铁、钛铁、铝铁、硼铁、钒铁和钙质脱硫剂装入料斗。
42.2、采用铝镁尖晶石坩埚进行真空感应熔炼,在1530~1570℃精炼处理10~15分钟(本实施例为1540℃精炼10分钟),随后依次加入硅铁、钛铁、铝铁、硼铁、钒铁和脱硫剂(本实施例添加顺序为硅铁、钛铁、铝铁、硼铁、钒铁和钙质脱硫剂),再次进行5~15分钟精炼(本实施例为10分钟),利用坩埚的较好热稳定性和脱硫剂进行脱碳、脱硫处理,在1480~1520℃浇铸铸锭(本实施例为1520℃)。
43.3、所述铸锭进行真空自耗冶炼,自耗铸锭规格为φ200~350mm(本实施例为φ315mm)。
44.4、所述自耗铸锭,在1050~1150℃保温4~12h后进行合金锻造(本实施例为1140℃保温时间为6h),开坯锻造温度1050~1150℃(本实施例为1120℃),终锻温度880~1000℃(本实施例终锻温度为900℃),获得锻坯;在锻至最终规格前允许回炉再加热,在加热温度1050~1150℃下保温1~4h(本实施例回炉加热四次,在1120℃保温时间为1.5h),锻造板坯截面规格为850
×
60mm。
45.5、所述锻造板坯在1050~1150℃保温2~4h(本实施例为1130℃保温时间为2h)后进行轧制,开坯轧制温度1050~1150℃(本实施例为1120℃),终轧温度850~950℃(本实施例终轧温度为860℃),在轧至最终规格前允许回炉再加热,在1050~1150℃下保温0.5~3h(本实施例回炉加热三次,在1120℃保温时间为0.5h),最终热轧板截面规格为850
×
4.0mm。
46.6、所述热轧板进行室温冷轧制,每次退火间变形量30~70%(本实施例为40~50%)、中间采用1020~1060℃(本实施例为1050℃)保温15~60min(本实施例为30min)去应力退火,获得0.4~0.6mm(本实施例为0.6mm)厚的冷轧板材。
47.7、取步骤6中所述冷轧板材,垂直于板材轧制方向截取金相试样,按标准的金相试验方法制备试样,按gb/t 9394《金属平均晶粒度测定方法》规定进行晶粒度评定,评定结果显示合金板材平均晶粒度为8.0级。
48.8、取步骤7中所述冷轧板材,进行固溶处理,固溶处理温度控制在970~990℃(本实施例为980℃)、保温时间20~60min(本实施例为40min),空冷。
49.9、取步骤8所述经过固溶处理的板材,进行变形量为10~15%(本实施例为13%)的冷轧制,最终板材厚度为0.52mm。
50.10、取步骤9中所述板材,进行980~1000℃(本实施例为1000℃)保温0.5~1h(本实施例为1h)的退火处理。
51.11、取步骤10中所述板材,进行730~750℃(本实施例为740℃)保温7~9h(本实施例为8h)后炉冷的时效处理。
52.12、取步骤11中经时效处理后的板材进行尺寸和表面质量检测,结果显示,板材宽度不小于800mm(本实施例为830mm)、厚度在0.4~0.6mm(本实施例为0.6mm)、长度不小于
1000mm(本实施例为1800mm),表面粗糙度ra≤0.8μm(本实施例为ra=0.6μm),不平度应不大于10mm/m(本实施例为6mm/m),厚度精度
±
0.05mm(本实施例为-0.02~+0.04mm)。
53.12、取步骤5中的热轧板材,沿轧制方向纵截面截取金相试样,按标准的金相试验方法制备试样,按gb/t 10561《钢中非金属夹杂物显微评定方法》进行夹杂物评定,结果见表2。
54.13、取步骤11中经时效处理板材,加工相应规格试样,进行板材合金晶界的ebsd分析,结果显示板材合金中∑3n特殊晶界比例为74.9%,∑≤29晶界比例度为76.5%,板材合金晶界结构ebsd图示于图1,特殊晶界比例统计结果见图2。
55.14、取步骤11中经时效处理板材,加工板状拉伸试样,按gb/t 228.1《金属材料拉伸试验低1部分室温试验方法》进行室温力学性能检测,结果见表3。
56.15、取步骤11中经时效处理板材,加工拉伸试样,按gb/t 4338《金属材料高温拉伸试验方法》进行250℃力学性能检测,结果见表4。
57.16、取步骤11中经时效处理板材加工拉伸试样,随后进行300℃、10mpa、高纯氢(体积纯度≥99.999%)、72h的充氢处理,按gb/t 228.1进行力学性能检测,结果见表5。
58.17、取步骤11中经时效处理板材加工疲劳试样,参考gb/t 3075-2008《金属材料疲劳试验轴向力控制方法》和gb/t 24176-2009《金属材料疲劳试验数据统计方案与分析方法》进行疲劳性能测试,结果表明其50%置信度下的疲劳极限为284mpa。
59.表1板材合金的化学成分,质量分数,%
60.元素cspnibmoaltivfe含量0.0140.0040.00630.40.00221.300.682.280.26余
61.表2板材合金的非金属夹杂物
[0062][0063]
表3板材的室温力学性能
[0064]
编号rp
0.2
/mparm/mpaa/%1687102529.02679101530.03681102030.5
[0065]
表4板材的250℃高温力学性能
[0066]
编号rp
0.2
/mparm/mpaa/%164298725.0264299325.5364698825.0
[0067]
表5热充氢后板材的室温力学性能
[0068]
编号rp
0.2
/mparm/mpaa/%1688103523.52689102924.03689103223.5
[0069]
实验结果表明,所制备的规格为1800mm
×
830mm
×
0.6mm的板材,其表面粗糙度ra≤0.7μm、不平度应不大于6mm/m;板材中仅有0.5级的细系d类非金属夹杂物存在;板材合金中∑3n特殊晶界比例高于74.0%,∑≤29晶界比例度高于76.0%;板材室温力学性能为:屈服强度(rp
0.2
)高于675mpa、抗拉强度(rm)高于1010mpa,延伸率高于28%;板材250℃力学性能为:屈服强度(rp
0.2
)高于640mpa、抗拉强度(rm)高于985mpa,延伸率高于24.5%;在300℃、10mpa的高纯氢环境中放置72h后,板材屈服强度(rp
0.2
)高于685mpa、抗拉强度(rm)高于1025mpa,延伸率高于23%;板材在50%置信度下的疲劳极限高于280mpa。
[0070]
实施例2:规格为1200mm
×
800mm
×
0.6mm的板材
[0071]
与实施例1不同之处在于,所制备的板材长度为1200mm、宽度为800mm。
[0072]
采用cao坩埚,在500kg真空感应炉上熔炼合金,以磷含量未0.006wt.%工业纯铁、电解镍、金属铬、金属钼及其它中间合金(如:硅铁、钛铁、铝铁、硼铁和钒铁)为原料熔炼合金。熔炼过程中,首先在1550℃精炼处理10分钟,随后依次加入硅铁、钛铁、铝铁、硼铁、钒铁和钙质脱硫剂进行10分钟精炼,利用cao坩埚的热稳定性和脱硫剂进行脱碳、脱硫处理,在1510℃浇铸铸锭。将铸锭进行真空自耗冶炼,自耗铸锭规格为φ220mm,化学成分见表6。在1150℃保温4h后进行合金锻造,开坯锻造温度为1120℃,终锻温度为900℃,在锻至最终规格前回炉再加热二次,再热温度1120℃、保温时间为1.5h,锻造板坯截面规格为820
×
60mm。在1130℃保温时间为2h后进行轧制,开坯轧制温度为1120℃,终轧温度为860℃,在轧至最终规格前回炉再加热三次,再热温度1120℃、保温时间为0.5h,最终热轧板截面规格为820
×
4.0mm。经过变形量为40~50%+1050℃保温30min的去应力退火处理的多道次冷轧退火加工,制备出厚度为0.6mm的冷轧板材,将冷轧板材进行980℃保温40min空冷的固溶处理,随后进行13%的冷轧制,获得厚度为0.52mm的板材。将板材进行1000℃保温1h的退火处理后,再进行740℃保温8h后炉冷的时效处理。板材表面质量检测结果显示,表面粗糙度ra=0.6μm、不平度为6mm/m。板材合金中∑3n特殊晶界比例为72.6%,∑≤29晶界比例度为75.1%,其非金属夹杂物评定结果见表7,室温力学性能见表8,250℃力学性能见表9,300℃、10mpa、高纯氢(体积纯度≥99.999%)、72h的充氢处理后的力学性能见表10。参考gb/t 3075-2008《金属材料疲劳试验轴向力控制方法》和gb/t 24176-2009《金属材料疲劳试验数据统计方案与分析方法》进行疲劳性能测试,结果显示板材50%置信度下的疲劳极限为292mpa。
[0073]
表6板材合金的化学成分,质量分数,%
[0074]
元素cspnibmoaltivfe含量0.0120.0040.00630.80.00201.350.702.250.28余
[0075]
表7板材合金的非金属夹杂物
[0076][0077]
表8板材的室温力学性能
[0078]
编号rp
0.2
/mparm/mpaa/%1678102030..52685102230.53679101830.0
[0079]
表9板材的250℃高温力学性能
[0080]
编号rp
0.2
/mparm/mpaa/%164498526.0263597925.5363298125.0
[0081]
表10热充氢后板材的室温力学性能
[0082]
编号rp
0.2
/mparm/mpaa/%1688103523.52688103324.03692103523.5
[0083]
实验结果表明,所制备的规格为1200mm
×
800mm
×
0.6mm的板材,其表面粗糙度ra≤0.6μm、不平度不超过6mm/m。板材中仅有0.5级的细系d类非金属夹杂物存在;板材中∑3n特殊晶界比例高于72%,∑≤29晶界比例度高于75%;板材室温力学性能为:屈服强度(rp
0.2
)高于675mpa、抗拉强度(rm)高于1015mpa,延伸率高于29%;板材250℃力学性能为:屈服强度(rp
0.2
)高于630mpa、抗拉强度(rm)高于975mpa,延伸率高于24.5%;在300℃、10mpa的高纯氢环境中放置72h后,屈服强度(rp
0.2
)高于685mpa、抗拉强度(rm)高于1030mpa,延伸率高于23%;板材50%置信度下的疲劳极限高于290mpa。