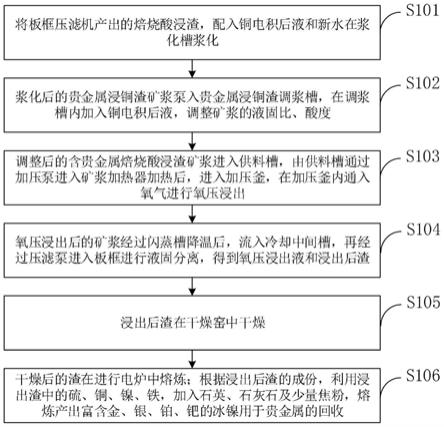
1.本发明属于焙烧酸浸渣综合回收技术领域,尤其涉及一种含贵金属焙烧酸浸渣的氧压浸出和贵金属富集方法。
背景技术:
2.目前,高冰镍湿法治炼铜镍产出的焙烧酸浸渣,由于成分较为复杂,常规工艺采用自然晾干后,拌入硫酸进行回转窑硫酸化焙烧-焙砂稀酸浸出-浸出液黄钠铁矾除铁工艺进行处理,铁渣堆放后返高冰镍冶炼,除铁后液返镍湿法冶炼-浸出渣熔炼回收贵金属。回转窑硫酸化焙烧无组织排放控制难度大,含酸和so2烟气治理难度大,工序多,能耗高。自然晾干需要较大的堆放仓库。返高冰镍治炼贵金属无法得到有效回收。
3.通过上述分析,现有技术存在的问题及缺陷为:
4.(1)回转窑硫酸化焙烧—稀酸浸出日处理量10t/d,无法满足生产需要。
5.(2)现有技术硫酸消耗量大,操作环境较差,烟气治理费用高。
6.(3)镍系统因体系平衡等原因,接收铜系统返回溶液能力有限,工艺产出的红渣,无法全部处理。
7.解决以上问题及缺陷的难度为:
8.以现有工艺难以解决存在的问题,需增加工序及配套设备提高处理量,但现场环境问题仍然无法解决。
9.解决以上问题及缺陷的意义为:
10.(1)提高红渣日处理量,提高直收率,降低生产成本。
11.(2)改善现场作业环境,走绿色发展之路。
12.(3)连续生产,远程操作,降低职工劳动强度,使过程连续化、自动化。
技术实现要素:
13.针对现有技术存在的问题,本发明提供了一种含贵金属焙烧酸浸渣的氧压浸出和贵金属富集方法。
14.本发明是这样实现的,一种含贵金属焙烧酸浸渣的氧压浸出和贵金属富集方法包括:
15.步骤一,将板框压滤机产出的焙烧酸浸渣,配入铜电积后液和新水在浆化槽浆化;
16.步骤二,浆化后的贵金属浸铜渣矿浆泵入贵金属浸铜渣调浆槽,在调浆槽内加入铜电积后液,调整矿浆的液固比、酸度;
17.步骤三,调整后的含贵金属焙烧酸浸渣矿浆进入供料槽,由供料槽通过加压泵进入矿浆加热器加热后,进入加压釜,在加压釜内通入氧气进行氧压浸出;
18.步骤四,氧压浸出后的矿浆经过闪蒸槽降温后,流入冷却中间槽,再经过压滤泵进入板框进行液固分离,得到氧压浸出液和浸出后渣;
19.步骤五,浸出后渣在干燥窑中干燥;
20.步骤六,干燥后的渣在进行电炉中熔炼;根据浸出后渣的成份,利用浸出渣中的硫、铜、镍、铁,加入石英、石灰石及少量焦粉,熔炼产出富含金、银、铂、钯的冰镍用于贵金属的回收。
21.进一步,步骤一中,所述焙烧酸浸渣为铜镍湿法冶金焙烧酸浸后产出的渣,含(%,g/t):cu10~14,ni15~22,fe5~9,s5~8,ba8~10,au10~20,ag1000~1500,pt8~10,pd8~10。
22.进一步,步骤二中,所述矿浆的液固比:l:s=5~8:1,酸度:h2so490~100g/l。
23.进一步,步骤三中,所述加热器加热到80~100℃;浸出温度:150~160℃,反应时间:2~3h,氧分压:0.15~0.3mpa。
24.进一步,步骤四中,氧压浸出液含(g/l):ni30~40,cu30~40,h2so4,fe2~3,h2so430~50,用于高冰镍浸出。
25.进一步,步骤四中,浸出后渣含(%):cu2~3,ni8~9,fe10~13,ba10~12,h2o15~18。
26.cu2~4,ni40~50,fe10~14,s20~22,ag1~3,au200~400g/t,pt100~150g/t,pd100~150g/t。
27.进一步,步骤五中,所述浸出后渣于180~200℃下干燥至含水5%~8%。
28.进一步,步骤六中,所述熔炼采用bao-feo-cao-sio2四元渣型。
29.进一步,步骤六中,所述电炉熔炼的控制条件为:熔炼温度为1350℃,配比为浸出后渣:石英:石灰石=6000:700~900:40~60。
30.进一步,步骤六中,所述富含金、银、铂、钯的冰镍的组分包含(%):cu2~4,ni40~50,fe10~14,s20~22,ag1~3,au200~400g/t,pt100~150g/t,pd100~150g/t。
31.结合上述的所有技术方案,本发明所具备的优点及积极效果为:
32.本发明提供的含贵金属焙烧酸浸渣的氧压浸出和贵金属富集方法,采用热压降镍技术可以将铜渣含镍大幅降低,降到1%以下,提高了镍系统镍直收率,改善了铜系统的冶金条件。
33.(1)红渣加压浸出系统可以将红渣处理量提高至7000t/a,完全满足实际需要,不再新增堆存红渣。
34.(2)有利于环保全湿法浸出工艺取代现有的硫酸化焙烧窑及烟气处理系统,改善了操作条件,对于阜冶工艺技术及装备水平的提高,推进绿色生产,意义重大。同时该项技术对采用高冰镍湿法浸出工艺的生产企业也有很好的借鉴和推广意义。
附图说明
35.为了更清楚地说明本技术实施例的技术方案,下面将对本技术实施例中所需要使用的附图做简单的介绍,显而易见地,下面所描述的附图仅仅是本技术的一些实施例,对于本领域普通技术人员来讲,在不付出创造性劳动的前提下还可以根据这些附图获得其他的附图。
36.图1是本发明实施例提供的含贵金属焙烧酸浸渣的氧压浸出和贵金属富集方法流程图。
37.图2是本发明实施例提供的含贵金属焙烧酸浸渣的氧压浸出和贵金属富集方法原
理图。
具体实施方式
38.为了使本发明的目的、技术方案及优点更加清楚明白,以下结合实施例,对本发明进行进一步详细说明。应当理解,此处所描述的具体实施例仅仅用以解释本发明,并不用于限定本发明。
39.针对现有技术存在的问题,本发明提供了一种含贵金属焙烧酸浸渣的氧压浸出和贵金属富集方法,下面结合附图对本发明作详细的描述。
40.s101,将板框压滤机产出的焙烧酸浸渣,配入铜电积后液和新水在浆化槽浆化;
41.s102,浆化后的贵金属浸铜渣矿浆泵入贵金属浸铜渣调浆槽,在调浆槽内加入铜电积后液,调整矿浆的液固比、酸度;
42.s103,调整后的含贵金属焙烧酸浸渣矿浆进入供料槽,由供料槽通过加压泵进入矿浆加热器加热后,进入加压釜,在加压釜内通入氧气进行氧压浸出;
43.s104,氧压浸出后的矿浆经过闪蒸槽降温后,流入冷却中间槽,再经过压滤泵进入板框进行液固分离,得到氧压浸出液和浸出后渣;
44.s105,浸出后渣在干燥窑中干燥;
45.s106,干燥后的渣在进行电炉中熔炼;根据浸出后渣的成份,利用浸出渣中的硫、铜、镍、铁,加入石英、石灰石及少量焦粉,熔炼产出富含金、银、铂、钯的冰镍用于贵金属的回收。
46.下面结合实施例对本发明进一步进行描述。
47.实施例1:
48.氧压浸出按以下步骤进行:
49.向浆化槽中7m3铜电积后液,打开搅拌,从焙烧浸出渣板框卸渣5t,其含量为(%):ni21,cu12,fe7.2,s6.3,ba8,au20,ag1000,pt10,pd10。
50.在浆化槽中浆化30min以上,之后打入调配槽中,按l/s=7:1,初始酸度h2so495g/l补加铜电积后液和新水。调浆完成后,打入供料槽。用加压泵经矿浆加热器泵入30m3衬钛4隔室加压釜中,通入氧气,搅拌浸出。浸出温度150℃,氧分压0.2mpa,加压泵流量3.5m3/h。
51.氧压浸出后的矿浆经过闪蒸槽降温后,流入冷却中间槽,再经过压滤泵进入板框进行液固分离,得到氧压浸出液和浸出后渣(贵渣)。氧压浸出液含(g/l):ni45,cu38,h2so4,fe2.54,h2so435,用于高冰镍浸出。浸出后渣含(%):cu2.85,ni8.41,fe11.2,ba10.5,h2o16;
52.实施例2:
53.浸出后渣(贵渣)熔炼冰镍富集贵金属按以下步骤进行:
54.压滤产出的浸出后渣(贵渣)在φ500
×
8000干燥窑中,于180℃下干燥至含水6%,用于熔炼含贵金属冰镍。
55.干燥后的浸出后渣(贵渣)和熔剂等,按浸出后渣:石英:石灰石=6000:700:50加入电炉中电炉熔炼,控制条件为:熔炼温度:1350℃,分批加入,分批排渣,熔炼时间16h。熔炼完成后,熔体倒入模具静置冷却,分离渣和冰镍。含贵金属的冰镍含(%):cu3.5,ni43,fe12,s21,ag2.2,au280g/t,pt106g/t,pd108g/t。
56.以上所述,仅为本发明的具体实施方式,但本发明的保护范围并不局限于此,任何熟悉本技术领域的技术人员在本发明揭露的技术范围内,凡在本发明的精神和原则之内所作的任何修改、等同替换和改进等,都应涵盖在本发明的保护范围之内。