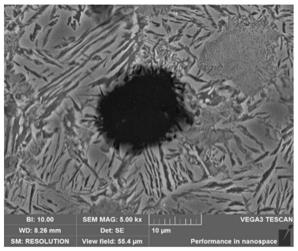
1.本发明属于模具制造技术领域,涉及一种铝型材加工用自润滑挤压模具材料,还涉及采用上述材料制造挤压模具的方法。
背景技术:
2.我国是全世界最大的铝合金生产国,年产各类铝合金近4000万吨,因此,近年来我国铝合金的加工工艺和加工装备也渐趋成熟。在众多的铝合金加工工艺中,铝合金压铸和挤压已成为铝合金最主要的加工方式。而在铝合金挤压加工过程中,挤压模具的磨损超差一直以来是困扰企业生产的一大难题。
3.在铝合金型材挤压生产过程中,铝合金棒料经加热后,在一定的挤压力作用下,被压入按照特定尺寸设计制造的挤压模具型腔,从而高效地完成铝合金型材的生产制造。然而,在铝型材挤压过程中,挤压模具型腔表面会与铝合金原材料在500℃左右发生高载滑动摩擦,加之高温下铝合金中的al元素对模具中mxoy的微区强还原反应会生成氧化铝产物,导致铝合金原材料与模具表面发生粘着,进一步使磨损加剧,从而使得挤压模具型腔尺寸短时间超差,过早报废。在实际生产过程中,为延长模具型腔磨损超差时间,往往需要两小时更换一套挤压模具,待卸下的挤压模具冷却至接近室温后,对其进行酸洗和二次表面渗氮等繁复的维护工序,为生产带来了极大的不便。
4.综上所述,针对性开发低摩擦自润滑挤压模具将会大幅度降低挤压模具型腔表面的磨损超差,延长模具使用寿命,降低模具维护成本。
技术实现要素:
5.本发明的目的是提供一种铝型材加工用自润滑挤压模具材料,解决了现有挤压模具在高载荷滑动摩擦过程中产生严重的型腔磨损,造成挤压模具型腔磨损超差时间短、生产成本高的问题。
6.本发明的另一目的是提供一种采用铝型材加工用自润滑挤压模具材料制造挤压模具的方法。
7.本发明所采用的技术方案是,一种铝型材加工用自润滑挤压模具材料,按照质量百分比由以下组分组成:c 2.5%~4.0%、si 2.2%~3.2%、mn 0.3%~1.3%、ni 1.0%~2.0%、cu 0.5%~1.5%、mg≤0.03%、p≤0.03%、s≤0.03%,余量为fe,上述组分的质量百分比之和为100%。
8.本发明所采用的另一技术方案是,一种采用铝型材加工用自润滑挤压模具材料制造挤压模具的方法,具体按照以下步骤实施:
9.步骤1,按照质量百分比称取以下组分:c 2.5%~4.0%、si 2.2%~3.2%、mn0.3%~1.3%、ni 1.0%~2.0%、cu 0.5%~1.5%、mg≤0.03%、p≤0.03%、s≤0.03%,余量为fe,上述组分的质量百分比之和为100%;
10.步骤2,将步骤1称取的材料在高温熔炼炉中进行熔炼至完全熔化,得到混合铁水;
11.步骤3,将步骤2得到的混合铁水通过转运包倒入预热好的连铸机配套保温炉中进行保温并加入硅铁球化剂和稀土孕育剂进行球化、孕育,得到生产铁水;
12.步骤4,将步骤3得到的生产铁水通过安装在连铸机上的结晶器进行激冷,经过激冷的生产铁水从表层开始凝壳,逐步向心部凝固,再通过引锭杆水平拉出形成铸态钢坯,得到自润滑挤压模具坯料;
13.步骤5,将步骤4得到的自润滑挤压模具坯料按挤压模具尺寸进行定尺,之后先通过cnc铣床和线切割对定尺后的坯料进行车外圆、铣型腔造型,得到挤压模具毛坯,将挤压模具毛坯放入加热炉中进行加热保温,随后取出再将挤压模具毛坯吊运至硝盐槽中保温,保温结束后取出,对挤压模具毛坯表面残留硝盐进行清洗,得到挤压模具;
14.步骤6,对步骤5得到的挤压模具分别进行硬度检验,合格后,再根据挤压模具图纸对模具型腔进行磨削、抛光加工,得到铝型材加工用自润滑挤压模具。
15.本发明的特征还在于,
16.步骤2中,熔炼温度为1320℃~1520℃。
17.步骤3中,连铸机配套保温炉的预热温度为630℃~830℃,保温时间为20min~35min。
18.步骤3中,硅铁球化剂的添加质量为步骤2中得到的混合铁水质量的1.4%~2.9%,稀土孕育剂的添加质量为步骤2中得到的混合铁水质量的1.4%~2.9%。
19.步骤4中,结晶器的尺寸较挤压模具最大外径大6~8mm。
20.步骤4中,生产铁水全截面凝固时间为6~14min,引锭杆的拉拔速度为2cm/min~5cm/min。
21.步骤5中,加热温度为800℃~950℃,保温时间为30min~90min。
22.步骤5中,硝盐槽的温度为220℃~390℃,保温时间为35min~120min。
23.步骤6中,硬度检验合格范围为hrc 48~50。
24.本发明的有益效果是,
25.(1)本发明制造的挤压模具利用基体中分布的500个/mm2且球化等级2级以上的游离态石墨来降低模具型腔与铝型材之间的摩擦磨损,有效延长了挤压模具型腔工作带磨损超差的时间,大幅降低生产成本;
26.(2)本发明制造的挤压模具经过热处理后,挤压模具工作带在型腔表面挤压应力作用下能使得组织中的过饱和奥氏体转换为马氏体,形成马氏体硬化层,可以避免现有挤压模具进行表面渗氮的工序,提高生产效率,降低生产成本。
附图说明
27.图1是本发明一种采用铝型材加工用自润滑挤压模具材料制造挤压模具的方法中得到的挤压模具的基体组织扫描电镜照片。
具体实施方式
28.下面结合附图和具体实施方式对本发明进行详细说明。
29.本发明提供一种铝型材加工用自润滑挤压模具材料,按照质量百分比由以下组分组成:c 2.5%~4.0%、si 2.2%~3.2%、mn 0.3%~1.3%、ni 1.0%~2.0%、cu 0.5%
~1.5%、mg≤0.03%、p≤0.03%、s≤0.03%,余量为fe,上述组分的质量百分比之和为100%。
30.本发明还提供一种采用铝型材加工用自润滑挤压模具材料制造挤压模具的方法,具体按照以下步骤实施:
31.步骤1,按照质量百分比称取以下组分:c 2.5%~4.0%、si 2.2%~3.2%、mn0.3%~1.3%、ni 1.0%~2.0%、cu 0.5%~1.5%、mg≤0.03%、p≤0.03%、s≤0.03%,余量为fe,上述组分的质量百分比之和为100%;
32.步骤2,将步骤1称取的材料在温度为1320℃~1520℃的高温熔炼炉中进行熔炼至完全熔化,得到混合铁水;
33.步骤3,将步骤2得到的混合铁水通过转运包倒入预热好的连铸机配套保温炉中进行保温并加入硅铁球化剂和稀土孕育剂进行球化、孕育,得到生产铁水;
34.其中,预热温度为630℃~830℃,保温时间为20min~35min;
35.硅铁球化剂的添加质量为步骤2中得到的混合铁水质量的1.4%~2.9%,稀土孕育剂的添加质量为步骤2中得到的混合铁水质量的1.4%~2.9%;
36.步骤4,将步骤3得到的生产铁水通过安装在连铸机上的结晶器进行激冷,结晶器的尺寸较挤压模具最大外径大6~8mm,经过激冷的生产铁水从表层开始凝壳,逐步向心部凝固,全截面凝固时间为6~14min,再通过引锭杆以2cm/min~5cm/min的速度水平拉出形成铸态钢坯,得到自润滑挤压模具坯料;
37.步骤5,将步骤4得到的自润滑挤压模具坯料按挤压模具尺寸进行定尺,之后先通过cnc铣床和线切割对定尺后的坯料进行车外圆、铣型腔造型,得到挤压模具毛坯,将挤压模具毛坯在温度为800℃~950℃下保温30min~90min,随后取出再将挤压模具毛坯吊运至温度为220℃~390℃的硝盐槽中保温35min~120min,保温结束后取出,对挤压模具毛坯表面残留硝盐进行清洗,得到挤压模具;
38.步骤6,对步骤5得到的挤压模具分别进行硬度检验,硬度检验合格范围为hrc48~50,合格后,再根据挤压模具图纸对模具型腔进行磨削、抛光加工,得到铝型材加工用自润滑挤压模具。
39.实施例1
40.本发明还提供一种采用铝型材加工用自润滑挤压模具材料制造挤压模具的方法,具体按照以下步骤实施:
41.步骤1,按照质量百分比称取以下组分:c 4.0%、si 2.2%、mn 1.3%、ni 2.0%、cu 1.5%、mg0.03%、p0.03%、s0.03%,余量为fe,上述组分的质量百分比之和为100%;
42.步骤2,将步骤1称取的材料在温度为1520℃的高温熔炼炉中进行熔炼至完全熔化,得到混合铁水;
43.步骤3,将步骤2得到的混合铁水通过转运包倒入预热好的连铸机配套保温炉中进行保温并加入硅铁球化剂和稀土孕育剂进行球化、孕育,得到生产铁水;
44.其中,预热温度为630℃,保温时间为35min;
45.硅铁球化剂的添加质量为步骤2中得到的混合铁水质量的1.4%,稀土孕育剂的添加质量为步骤2中得到的混合铁水质量的1.4%;
46.步骤4,将步骤3得到的生产铁水通过安装在连铸机上的结晶器进行激冷,结晶器
的尺寸较挤压模具最大外径大6mm,经过激冷的生产铁水从表层开始凝壳,逐步向心部凝固,全截面凝固时间为14min,再通过引锭杆以2cm/min的速度水平拉出形成铸态钢坯,得到自润滑挤压模具坯料;
47.步骤5,将步骤4得到的自润滑挤压模具坯料按挤压模具尺寸进行定尺,之后先通过cnc铣床和线切割对定尺后的坯料进行车外圆、铣型腔造型,得到挤压模具毛坯,将挤压模具毛坯在温度为950℃下保温30min,随后取出再将挤压模具毛坯吊运至温度为390℃的硝盐槽中保温35min,保温结束后取出,对挤压模具毛坯表面残留硝盐进行清洗,得到挤压模具;
48.步骤6,对步骤5得到的挤压模具分别进行硬度检验,硬度检验合格范围为hrc30~48,合格后,再根据挤压模具图纸对模具型腔进行磨削、抛光加工,得到铝型材加工用自润滑挤压模具。
49.图1为步骤5热处理后得到的挤压模具的基体组织扫描电镜照片,由此可以看出,挤压模具基体由铁素体、过饱和奥氏体和石墨组成,过饱和奥氏体在应力诱发下可转变为马氏体。
50.本发明基体中分布有500个/mm2且球化等级2级以上的游离态石墨,从而降低模具型腔与铝型材之间的摩擦磨损。
51.将步骤4所得到的自润滑挤压模具坯料与日本进口dc53模具钢进行的铝合金摩擦试验对比,将本发明自润滑挤压坯料与dc53模具钢与6063铝合金往复摩擦2万次后,本发明所得到的自润滑挤压模具坯料具有明显的低摩擦抑制粘铝的优点,粘铝量降低50%以上,不仅能够改善铝合金表面加工质量,还能够有效延长模具寿命。
52.实施例2
53.本发明还提供一种采用铝型材加工用自润滑挤压模具材料制造挤压模具的方法,具体按照以下步骤实施:
54.步骤1,按照质量百分比称取以下组分:c 2.5%、si 3.2%、mn 0.3%、ni 1.0%、cu 0.5%、mg 0.01%、p 0.01%、s0.01%,余量为fe,上述组分的质量百分比之和为100%;
55.步骤2,将步骤1称取的材料在温度为1320℃的高温熔炼炉中进行熔炼至完全熔化,得到混合铁水;
56.步骤3,将步骤2得到的混合铁水通过转运包倒入预热好的连铸机配套保温炉中进行保温并加入硅铁球化剂和稀土孕育剂进行球化、孕育,得到生产铁水;
57.其中,预热温度为830℃,保温时间为20min;
58.硅铁球化剂的添加质量为步骤2中得到的混合铁水质量的2.9%,稀土孕育剂的添加质量为步骤2中得到的混合铁水质量的2.9%;
59.步骤4,将步骤3得到的生产铁水通过安装在连铸机上的结晶器进行激冷,结晶器的尺寸较挤压模具最大外径大8mm,经过激冷的生产铁水从表层开始凝壳,逐步向心部凝固,全截面凝固时间为6min,再通过引锭杆以5cm/min的速度水平拉出形成铸态钢坯,得到自润滑挤压模具坯料;
60.步骤5,将步骤4得到的自润滑挤压模具坯料按挤压模具尺寸进行定尺,之后先通过cnc铣床和线切割对定尺后的坯料进行车外圆、铣型腔造型,得到挤压模具毛坯,将挤压模具毛坯在温度为800℃下保温90min,随后取出再将挤压模具毛坯吊运至温度为220℃的
硝盐槽中保温120min,保温结束后取出,对挤压模具毛坯表面残留硝盐进行清洗,得到挤压模具;
61.步骤6,对步骤5得到的挤压模具分别进行硬度检验,硬度检验合格范围为hrc48~50,合格后,再根据挤压模具图纸对模具型腔进行磨削、抛光加工,得到铝型材加工用自润滑挤压模具。
62.实施例3
63.本发明还提供一种采用铝型材加工用自润滑挤压模具材料制造挤压模具的方法,具体按照以下步骤实施:
64.步骤1,按照质量百分比称取以下组分:c 3.3%、si 2.8%、mn 1.8%、ni1.5%、cu 1%、mg0.02%、p0.02%、s0.02%,余量为fe,上述组分的质量百分比之和为100%;
65.步骤2,将步骤1称取的材料在温度为1400℃的高温熔炼炉中进行熔炼至完全熔化,得到混合铁水;
66.步骤3,将步骤2得到的混合铁水通过转运包倒入预热好的连铸机配套保温炉中进行保温并加入硅铁球化剂和稀土孕育剂进行球化、孕育,得到生产铁水;
67.其中,预热温度为720℃,保温时间为28min;
68.硅铁球化剂的添加质量为步骤2中得到的混合铁水质量的2%,稀土孕育剂的添加质量为步骤2中得到的混合铁水质量的2%;
69.步骤4,将步骤3得到的生产铁水通过安装在连铸机上的结晶器进行激冷,结晶器的尺寸较挤压模具最大外径大7mm,经过激冷的生产铁水从表层开始凝壳,逐步向心部凝固,全截面凝固时间为10min,再通过引锭杆以3.5cm/min的速度水平拉出形成铸态钢坯,得到自润滑挤压模具坯料;
70.步骤5,将步骤4得到的自润滑挤压模具坯料按挤压模具尺寸进行定尺,之后先通过cnc铣床和线切割对定尺后的坯料进行车外圆、铣型腔造型,得到挤压模具毛坯,将挤压模具毛坯在温度为870℃下保温60min,随后取出再将挤压模具毛坯吊运至温度为300℃的硝盐槽中保温75min,保温结束后取出,对挤压模具毛坯表面残留硝盐进行清洗,得到挤压模具;
71.步骤6,对步骤5得到的挤压模具分别进行硬度检验,硬度检验合格范围为hrc48~50,合格后,再根据挤压模具图纸对模具型腔进行磨削、抛光加工,得到铝型材加工用自润滑挤压模具。
72.实施例4
73.本发明还提供一种采用铝型材加工用自润滑挤压模具材料制造挤压模具的方法,具体按照以下步骤实施:
74.步骤1,按照质量百分比称取以下组分:c 4.0%、si 3.0%、mn 1.3%、ni 1.0%、cu 1.3%、mg0.01%、p0.02%,余量为fe,上述组分的质量百分比之和为100%;
75.步骤2,将步骤1称取的材料在温度为1500℃的高温熔炼炉中进行熔炼至完全熔化,得到混合铁水;
76.步骤3,将步骤2得到的混合铁水通过转运包倒入预热好的连铸机配套保温炉中进行保温并加入硅铁球化剂和稀土孕育剂进行球化、孕育,得到生产铁水;
77.其中,预热温度为800℃,保温时间为30min;
78.硅铁球化剂的添加质量为步骤2中得到的混合铁水质量的2.5%,稀土孕育剂的添加质量为步骤2中得到的混合铁水质量的2.5%;
79.步骤4,将步骤3得到的生产铁水通过安装在连铸机上的结晶器进行激冷,结晶器的尺寸较挤压模具最大外径大6mm,经过激冷的生产铁水从表层开始凝壳,逐步向心部凝固,全截面凝固时间为14min,再通过引锭杆以2cm/min的速度水平拉出形成铸态钢坯,得到自润滑挤压模具坯料;
80.步骤5,将步骤4得到的自润滑挤压模具坯料按挤压模具尺寸进行定尺,之后先通过cnc铣床和线切割对定尺后的坯料进行车外圆、铣型腔造型,得到挤压模具毛坯,将挤压模具毛坯在温度为900℃下保温70min,随后取出再将挤压模具毛坯吊运至温度为300℃的硝盐槽中保温60min,保温结束后取出,对挤压模具毛坯表面残留硝盐进行清洗,得到挤压模具;
81.步骤6,对步骤5得到的挤压模具分别进行硬度检验,硬度检验合格范围为hrc48~50,合格后,再根据挤压模具图纸对模具型腔进行磨削、抛光加工,得到铝型材加工用自润滑挤压模具。
82.实施例5
83.本发明还提供一种采用铝型材加工用自润滑挤压模具材料制造挤压模具的方法,具体按照以下步骤实施:
84.步骤1,按照质量百分比称取以下组分:c 2.8%、si 2.6%、mn 0.7%、ni 1.8%、cu 0.7%、p0.01%、s0.01%,余量为fe,上述组分的质量百分比之和为100%;
85.步骤2,将步骤1称取的材料在温度为1400℃的高温熔炼炉中进行熔炼至完全熔化,得到混合铁水;
86.步骤3,将步骤2得到的混合铁水通过转运包倒入预热好的连铸机配套保温炉中进行保温并加入硅铁球化剂和稀土孕育剂进行球化、孕育,得到生产铁水;
87.其中,预热温度为650℃,保温时间为30min;
88.硅铁球化剂的添加质量为步骤2中得到的混合铁水质量的1.8%,稀土孕育剂的添加质量为步骤2中得到的混合铁水质量的1.8%;
89.步骤4,将步骤3得到的生产铁水通过安装在连铸机上的结晶器进行激冷,结晶器的尺寸较挤压模具最大外径大7mm,经过激冷的生产铁水从表层开始凝壳,逐步向心部凝固,全截面凝固时间为10min,再通过引锭杆以4cm/min的速度水平拉出形成铸态钢坯,得到自润滑挤压模具坯料;
90.步骤5,将步骤4得到的自润滑挤压模具坯料按挤压模具尺寸进行定尺,之后先通过cnc铣床和线切割对定尺后的坯料进行车外圆、铣型腔造型,得到挤压模具毛坯,将挤压模具毛坯在温度为850℃下保温80min,随后取出再将挤压模具毛坯吊运至温度为250℃的硝盐槽中保温100min,保温结束后取出,对挤压模具毛坯表面残留硝盐进行清洗,得到挤压模具;
91.步骤6,对步骤5得到的挤压模具分别进行硬度检验,硬度检验合格范围为hrc48~50,合格后,再根据挤压模具图纸对模具型腔进行磨削、抛光加工,得到铝型材加工用自润滑挤压模具。