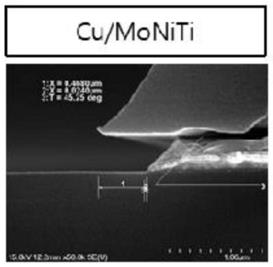
1.本发明涉及一种用于蚀刻金属膜的蚀刻剂组合物、使用所述蚀刻剂组合物的布线形成方法以及用于液晶显示装置的阵列基板的制造方法。
背景技术:
2.tft-lcd等液晶显示装置的像素电极使用铜膜、铜合金膜的单膜、或者铜膜和钼合金膜的多层膜等。像素电极一般是通过如下的一系列的光刻和蚀刻工艺来完成:通过溅射等方法层压在基板上,并在其上均匀涂上光刻胶,然后通过刻有图案的掩模进行光照射,然后通过显影形成所需图案的光刻胶后,再通过干法或湿法刻蚀将图案转印到光刻胶下面的金属膜上后,通过剥离工艺去除不需要的光刻胶。
3.以往用作金属布线膜材料的铬、钼、铝镍等具有高电阻,因此在大型tft-lcd中用作栅极和数据布线等时受到限制。
4.在这点上,与铝或铬相比电阻显着低且不存在太大环境问题的铜金属作为低电阻布线膜材料受到关注,但在铜膜的情况下,使用光刻胶图案作为掩模的选择性蚀刻存在问题,并且存在与玻璃基板或硅绝缘膜的附着力差的问题。
5.为了解决这个问题,提出了一种并用中间金属膜的技术,以增加铜膜与玻璃基板或硅绝缘膜之间的附着力并抑制铜扩散到硅膜中的技术,并且作为中间金属膜可以使用钛、钛合金、钼或钼合金等。
6.当用相同的蚀刻剂对包括铜膜和其他金属膜(例如钼合金膜等)的多层膜进行蚀刻时,可以简化制造工艺,但是一般而言,由于钼合金膜具有优异的耐化学性,因此存在难以进行湿法刻蚀的问题。
7.在这方面,韩国专利公开号10-2011-0118297公开了一种用于薄膜晶体管液晶显示装置的蚀刻组合物,其包括过氧化氢、氧化剂、磷酸盐、螯合剂、醛衍生物、铵化合物以及添加剂。然而,现有的蚀刻剂组合物在蚀刻过程中不可避免地会含有铝等杂质,且在蚀刻金属膜后会产生al和/或si析出物,特别是,铜合金和钼合金的金属膜层叠结构存在蚀刻特性不好的问题。
8.如果蚀刻设备中产生析出物,则会出现蚀刻过程中因开口缺陷等导致不良率增加而降低收率、因过滤器堵塞等导致过滤器更换周期缩短、需要去除析出物的设备的维护工作(pm)等问题,因此需要开发可以解决这些问题的蚀刻剂组合物。
9.[现有技术文献]
[0010]
[专利文献]
[0011]
(专利文献1)韩国专利公开号10-2011-0118297
技术实现要素:
[0012]
[技术问题]
[0013]
为了改善现有技术中存在的上述问题,本发明的目的在于提供一种蚀刻剂组合物、使用所述蚀刻剂组合物的布线形成方法以及用于液晶显示装置的阵列基板的制造方法,其在刻蚀时不产生析出物,金属膜的刻蚀速率控制得当,锥角特性优异,防止在三层膜蚀刻时出现尖端(tip)而获得优异的蚀刻轮廓。
[0014]
然而,本技术要解决的问题不限于上述问题,本领域技术人员通过以下描述将清楚地理解其他未提及的问题。
[0015]
[技术方案]
[0016]
为了实现上述目的,本发明提供了一种蚀刻剂组合物,其特征在于,包括:(a)过氧化氢;(b)氟化合物;(c)唑类化合物;(d)一个分子内具有氮原子和羧基的水溶性化合物;(e)磷酸盐化合物;以及(f)硫酸盐化合物,其中,所述(e)磷酸盐化合物和所述(f)硫酸盐化合物中的任一个包括铵盐,并且下述等式1的y值为16以上且200以下:
[0017]
[等式1]
[0018][0019]
此外,本发明还提供一种布线形成方法,其包括以下步骤:在基板上形成金属膜;在所述金属膜上形成光刻胶图案;以及以所述光刻胶图案为掩膜,用根据本发明的蚀刻剂组合物对所述金属膜进行蚀刻,其中,形成所述金属膜的步骤包括:层压一层以上的金属膜。
[0020]
此外,本发明还提供一种用于液晶显示装置的阵列基板的制造方法,所述制造方法包括以下步骤:(a)在基板上形成栅极布线;(b)在包括所述栅极布线的基板上形成栅极绝缘层;(c)在所述栅极绝缘层上形成半导体层;(d)在所述半导体层上形成源电极和漏电极;以及(e)形成与所述漏电极连接的像素电极,其中,所述步骤(e)包括:通过使用根据本发明的蚀刻剂组合物进行蚀刻来形成像素电极的工艺。
[0021]
[发明效果]
[0022]
本发明的蚀刻剂组合物不仅可以批量蚀刻铜膜或铜合金膜的单层膜,还可以批量蚀刻进一步包含钼或钼合金膜的多层膜,并且在多层膜中可以形成相对于上部铜金属膜具有优异直线度的锥形轮廓。
[0023]
此外,可以确保铜膜或铜/钼合金膜、钼合金膜/铜/钼合金膜的锥角和铜蚀刻速率优异,并且由于适当的铜蚀刻速率,因此可以防止在蚀刻钼合金膜/铜/钼合金膜等三层膜时出现尖端,并且提供蚀刻后不产生al和si析出物(颗粒)的效果。
[0024]
此外,即使在对玻璃基板上形成的金属膜进行蚀刻时,也可以抑制析出物的发生,从而抑制布线形成过程中开口缺陷的发生,并防止析出物在蚀刻装置内沉积,从而延长过滤器更换周期。
附图说明
[0025]
图1是用根据本技术的实施例1的蚀刻剂组合物蚀刻的cu/moniti双层膜的横截面sem照片。
[0026]
图2是用根据本技术的实施例1的蚀刻剂组合物蚀刻的moalti/cu/moalti三层膜的sem照片。
[0027]
图3是用根据本技术的比较例1的蚀刻剂组合物蚀刻的moalti/cu/moalti三层膜的横截面sem照片。
[0028]
图4是本技术的比较例2或比较例6的蚀刻剂组合物蚀刻金属膜时产生的al析出物的sem照片。
[0029]
图5是使用本技术的比较例1至5的蚀刻剂组合物蚀刻金属膜时产生的si析出物的sem照片。
具体实施方式
[0030]
本发明涉及一种用于蚀刻金属膜的蚀刻剂组合物、使用所述蚀刻剂组合物的布线形成方法以及用于液晶显示装置的阵列基板的制造方法。
[0031]
根据本发明的蚀刻剂组合物用于蚀刻由铜基金属膜、铜基金属膜/钼基金属膜组成的双层膜、以及由钼基金属膜/铜基金属膜/钼基金属膜组成的三层膜等,可以在多层膜质量中相对于上部铜基金属膜形成具有优异直线度的锥形轮廓,并且可以一起蚀刻上部铜基金属膜和钼基金属膜。此外,本发明的蚀刻剂组合物使蚀刻工艺中不可避免地产生的诸如铝和硅等的杂质的析出最少化,并解决了因出现析出物而导致开口缺陷(布线断开)、收率降低、过滤器堵塞等问题。
[0032]
本发明的蚀刻剂组合物在蚀刻铜基金属膜时可以实现蚀刻均匀性和直线度优异的锥度轮廓。由于本发明的蚀刻剂组合物在蚀刻过程中不产生残留物,因此不存在诸如电短路、布线缺陷和亮度降低等问题。因此,本发明的蚀刻剂组合物可以非常有用地用于制造液晶显示装置的阵列基板,该阵列基板实现大画面和高亮度的电路。
[0033]
在本说明书中,金属膜可以是指铜基金属膜、钼基金属膜、或者层压有两种或更多种这种膜的多层膜。
[0034]
在本说明书中,所述铜基金属薄膜包括铜作为膜的成分,所述铜基金属薄膜是指指纯铜、铜的氮化物、铜的氧化物或铜的合金,钼基金属膜包括钼作为膜的成分,并且是指纯钼、钼的氮化物、钼的氧化物或钼的合金。
[0035]
所述铜合金包括选自由纯铜、铜的氮化物、铜的氧化物组成的组中的一种、以及与选自由铝(al)、镁(mg)、钙(ca)、钛(ti)、银(ag)、铬(cr)、锰(mn)、铁(fe)、锆(zr)、铌(nb)、钼(mo)、钯(pd)、铪(hf)、钽(ta)和钨(w)组成的组中的一种以上金属的合金。
[0036]
此外,所述钼合金包括选自纯钼、钼的氮化物、钼的氧化物组成的组中的一种、以及与选自由铌(nb)、钨(w)、钛(ti)、镍(ni)和铝(al)组成的组中的一种以上金属的合金。例如,所述钼合金可包括但不限于moalti和moniti。
[0037]
《蚀刻剂组合物》
[0038]
本发明的蚀刻剂组合物是蚀刻金属膜而不产生析出物的组合物,并包括:(a)过氧化氢(h2o2);(b)氟化合物;(c)唑类化合物;(d)一个分子内具有氮原子和羧基的水溶性化合物;(e)磷酸盐化合物;以及(f)硫酸盐化合物,并且可以进一步包括(g)添加剂和/或(h)水。
[0039]
根据本发明的蚀刻剂组合物,相对于组合物的总重量,优选为,(a)过氧化氢的含量为5.0至25.0重量%;(b)氟化合物的含量为0.001至0.10重量%;(c)唑类化合物的含量为0.1至5.0重量%;(d)一个分子内具有氮原子和羧基的水溶性化合物的含量为0.1至5.0重量%;(e)磷酸盐化合物的含量为0.01至0.10重量%;并且(f)硫酸盐化合物的含量为0.1
至2.0重量%。
[0040]
此外,本发明的蚀刻剂组合物可以使用上述成分通过以往公知的方法制备,并且本发明的蚀刻剂组合物优选具有用于半导体加工的纯度。
[0041]
此外,本发明的蚀刻剂组合物的特征在于,等式1的y值为16以上且200以下,优选为20以上且200以下。当满足所述y值时,可以防止析出物的发生,并确保金属膜的优异的锥角(例如,35
°
至55
°
)以及铜蚀刻速率(例如,60至130埃/秒),并且可以防止开口缺陷和在多层蚀刻过程中尖端的出现。
[0042]
[等式1]
[0043][0044]
在上述等式1中,(d)水溶性化合物含量、(f)硫酸盐化合物含量、(b)氟化合物含量和(e)磷酸盐化合物含量是指相对于组合物的总重量所包含的含量,并且通过各自的重量(g)计算或通过相对于每种组合物的总重量的重量%计算。
[0045]
由于玻璃对氟敏感,因此当所述析出物中的硅(si)析出物蚀刻在含硅基板(例如,玻璃基板或硅绝缘膜等)上形成的金属膜时,所述基板和蚀刻剂组合物接触,从而由于与蚀刻剂组合物中包含的氟反应而产生si析出物。
[0046]
然而,满足所述y值范围的蚀刻剂组合物不会产生si析出物,从而防止了开口缺陷的发生并延长了过滤器更换周期。具体而言,当所述y值大于200时,不仅会产生si析出物,而且蚀刻速率太快而难以控制工艺,在多层蚀刻时出现尖端,并且即使在所述y值小于16的情况下,也存在蚀刻时产生si析出物的问题以及产生上部尖端的问题。
[0047]
此外,在根据本发明的蚀刻剂组合物中,所述磷酸盐化合物和所述硫酸盐化合物中的任一种可以包括铵盐,并且磷酸盐化合物和硫酸盐化合物都可以包括铵盐。
[0048]
在包含铝的金属膜的蚀刻工艺中,存在蚀刻剂组合物中含有的氟与铝反应而生成大量铝(al)析出物的问题。此外,即使金属膜不含铝,由于金属膜形成在以sio2和al2o3作为主要成分的玻璃基板上,因此玻璃基板也被氟蚀刻而产生al析出物。然而,当蚀刻剂组合物中的磷酸盐化合物和硫酸盐化合物中的任何一种含有铵盐时,铵盐与铝反应生成(nh4)3alf6,而由于铵盐在水中的溶解度高,(nh4)3alf6在室温下完全溶解在水中,因此可以防止铝析出物的发生,从而防止开口缺陷。
[0049]
(a)过氧化氢
[0050]
本发明的蚀刻剂组合物包括(a)过氧化氢(h2o2),作为影响铜基金属膜蚀刻的主要氧化剂,所述铜基金属膜可以包括在钼基金属膜上形成铜基金属膜的多层膜。
[0051]
相对于组合物的总重量,过氧化氢(h2o2)的含量可为5.0至25.0重量%,优选为10.0至23.0重量%。当过氧化氢的含量小于5重量%时,由于铜基金属膜和钼合金膜的蚀刻能力不足,因此无法进行充分的蚀刻,并且当过氧化氢的含量超过25重量%时,由于蚀刻速率增整体加,因此工艺控制变得困难,并且由于铜离子增加而可能大大降低热稳定性。
[0052]
(b)氟化合物
[0053]
本发明的蚀刻剂组合物中所含的氟化合物(b)是指能够在水中解离而产生氟(f)离子的化合物。氟化合物是一种影响钼基金属膜的蚀刻速率的辅助氧化剂,用于控制钼基
金属膜的蚀刻速率。此外,用于去除在同时蚀刻铜基金属膜和钼基金属膜的溶液中不可避免地产生的残留物。
[0054]
相对于组合物的总重量,氟化合物的含量可为0.001至0.1重量%,优选为0.01至0.08重量%。由于氟离子与铝离子或硅离子结合而产生沉淀,因此优选使氟化合物的含量最小化。当氟化合物的含量小于0.001重量%时,可能会产生蚀刻残留物,含钛金属膜可能难以蚀刻,钼合金/铜/钼合金在蚀刻过程中,上部/下部钼合金蚀刻速率慢,因此造成产能损失(capa.loss)。在氟化合物的含量超过0.1重量%时,存在玻璃基板的蚀刻速率变大的缺点。
[0055]
氟化合物是本领域中使用的材料,只要是能够在溶液中离解成氟离子或多原子氟离子的化合物就没有特别限制。例如,所述氟化合物优选为选自由hf、naf、nh4f、nh4bf4、nh4fhf、kf、khf2、alf3和hbf4组成的组中的一种或两种以上。
[0056]
(c)唑类化合物
[0057]
本发明的蚀刻剂组合物中包含的(c)唑类化合物控制铜基金属膜的蚀刻速率,减少图案的cd损失,从而提高工艺中的裕度。
[0058]
相对于组合物的总重量,唑类化合物的含量可为0.1至5重量%,优选为0.2至1.0重量%。当唑类化合物的含量小于0.1重量%时,铜的蚀刻速率过度增加,因此可能会出现cd损失过大,当唑类化合物的含量超过5重量%时,铜基金属膜的蚀刻速率和钼基金属膜的蚀刻速率过慢,因此导致工艺时间的损失,并且钼基金属膜的残留物残留的可能性增加。
[0059]
可以没有特别限制地使用唑类化合物,只要其是本领域中使用的材料。例如,唑类化合物优选为具有1至30个碳原子的唑类化合物,更优选为三唑化合物、氨基四唑化合物、咪唑化合物、吲哚化合物、嘌呤化合物、吡唑化合物、吡啶化合物、嘧啶化合物、吡咯化合物、吡咯烷化合物和吡咯啉化合物等可以分别单独使用或混合2种以上使用。
[0060]
(d)一个分子内具有氮原子和羧基的水溶性化合物
[0061]
本发明的蚀刻剂组合物中包含的(d)一个分子内具有氮原子和羧基的水溶性化合物防止了在蚀刻剂组合物的储存期间可能发生的过氧化氢的自分解反应,并且当大量基板被蚀刻时,可以防止蚀刻特性发生变化,也可以称为螯合剂。
[0062]
通常,对于使用过氧化氢的蚀刻剂组合物而言,在储存期间过氧化氢会自分解,因此储存期不长,并且存在容器可能会爆炸的危险。然而,当包含1分子内具有氮原子和羧基的水溶性化合物时,过氧化氢的分解速度降低近10倍,因此有利于确保保存期和稳定性。
[0063]
特别是,在铜基金属膜的情况下,当蚀刻剂组合物中残留大量铜离子时,会形成钝化膜并氧化成黑色,并且在此之后不再蚀刻的情况可能会很多,但是可以通过添加在一个分子内具有氮原子和羧基的水溶性化合物来防止这种现象。
[0064]
相对于组合物的总重量,一个分子内具有氮原子和羧基的水溶性化合物的含量为0.1至5.0重量%,优选为1.0至3.0重量%。当一个分子内具有氮原子和羧基的水溶性化合物的含量小于0.1重量%时,在蚀刻大量基板(约500张)之后形成钝化膜,因此难以获得足够的工艺裕度,并且当一分子内具有氮原子和羧基的水溶性化合物的含量超过0.5重量%时,钼基金属膜的蚀刻速度减慢。
[0065]
一个分子内具有氮原子和羧基的水溶性化合物例如为选自由丙氨酸、氨基丁酸、谷氨酸、甘氨酸、亚氨基二乙酸、次氮基三乙酸和肌氨酸组成的组中的一种或两种。
[0066]
(e)磷酸盐化合物
[0067]
(e)包含在本发明的蚀刻剂组合物中的磷酸盐化合物是使图案的锥形轮廓良好的成分。当本发明的蚀刻剂组合物中不包含磷酸盐化合物时,蚀刻轮廓会变差。
[0068]
在本发明的蚀刻剂组合物中,磷酸盐化合物可以包括铵盐,特别是当后述的硫酸盐化合物不包括铵盐时,所述磷酸盐化合物必须包括铵盐(铵离子)才能防止可以防止铝(al)析出物的产生。
[0069]
相对于组合物的总重量,所述磷酸盐化合物的含量可为0.10重量%或更少,优选为0.01至0.10重量%,更优选为0.01至0.08重量%。当磷酸化合物的含量小于0.01重量%时,蚀刻轮廓可能变差,当磷酸化合物的含量超过0.1重量%时,会出现铜基金属膜的锥角增大的问题,并且虽然铜基金属膜的蚀刻速率增大,但可能存在钼基金属膜的蚀刻速率变慢的问题。因此,当金属膜是由钼基金属膜/铜基金属膜/钼基金属膜形成的三层膜时,也会引起出现上部尖端的问题。
[0070]
磷酸盐化合物没有特别限制,只要其是选自磷酸中的一个或两个氢被碱金属、碱土金属、铵离子等取代的盐即可。例如,所述磷酸盐化合物优选为选自由磷酸一钠(sodium phosphate monobasic)、磷酸二钠(sodium phosphate dibasic)、磷酸一钾(potassium phosphate)、磷酸二钾(potassium phosphate dibasic)、磷酸一铵(ammonium phosphate monobasic)和磷酸二铵(ammonium phosphate dibasic)组成的组中的一种或两种以上,更优选为磷酸一铵或磷酸二铵。
[0071]
(f)硫酸盐化合物
[0072]
本发明的蚀刻剂组合物中所含的(f)硫酸盐化合物是使图案的锥度形状变得良好的成分,起到控制铜系金属膜的蚀刻速率的作用。当本发明的蚀刻剂组合物中不包含硫酸盐化合物时,由于蚀刻能力不足,因此可能无法进行充分的蚀刻。
[0073]
在本发明的蚀刻剂组合物中,硫酸盐化合物可以包括铵盐,特别是,当上述磷酸盐化合物不包括铵盐时,硫酸盐化合物必须包括铵盐(铵离子)才能防止出现铝(al)析出物。
[0074]
相对于组合物的总重量,硫酸盐化合物的含量可为0.1至2.0重量%,优选为0.3至1.5重量%,并且当满足上述范围时可具有合适的铜蚀刻速率。硫酸盐化合物含量越低,铜蚀刻速率越慢,双层蚀刻时锥角越小,硫酸盐化合物含量越高,铜蚀刻速率越快,双层蚀刻时锥角越大,具体而言,当硫酸盐化合物的含量低于0.1重量%时,可能无法进行充分的蚀刻,而当硫酸盐化合物的含量超过2重量%时,蚀刻速率整体变快,使得难以实现工艺控制。
[0075]
对硫酸盐化合物没有特别限制,只要其是选自硫酸中的一个或两个氢被碱金属、碱土金属、铵离子等取代的盐即可。例如,硫酸盐化合物选自由硫酸钠、硫酸氢钠、硫酸钾、硫酸氢钾和硫酸铵组成的组中的一种或两种,更优选为硫酸铵。
[0076]
(g)添加剂
[0077]
此外,除了本发明的蚀刻剂组合物除上述成分之外还可包括常规添加剂,所述添加剂可包括金属离子螯合剂、腐蚀抑制剂、表面活性剂和醋酸盐化合物等。此外,添加剂不限于此,为了进一步提高本发明的效果,可以选择本领域公知的各种其他添加剂而添加。
[0078]
具体地,本发明的蚀刻剂组合物可以包括多元醇型表面活性剂作为添加剂以提高蚀刻剂的稳定性。
[0079]
所述多元醇型表面活性剂用于通过降低表面张力来增加蚀刻的均匀性。此外,多
元醇类表面活性剂通过在蚀刻铜基金属膜后包围溶解在蚀刻剂中的铜离子来抑制铜离子的活性,从而抑制过氧化氢的分解反应。如果以这种方式降低铜离子的活性,则可以在使用蚀刻剂期间稳定地进行工艺。此外,相对于组合物的总重量,可以以0.001至5.0重量%包含多元醇型表面活性剂。
[0080]
多元醇类表面活性剂例如优选为选自由丙三醇、乙二醇、二甘醇、三甘醇和聚乙二醇组成的组中的一种或两种。
[0081]
此外,本发明的蚀刻剂组合物可以包含醋酸盐化合物作为添加剂以控制蚀刻速率。
[0082]
醋酸盐化合物通过提高ph来减缓铜膜的蚀刻速率,并且作为在蚀刻速率快时调节蚀刻速率的成分,相对于组合物的总重量,醋酸盐化合物的含量可以为0.1至2.0重量%。
[0083]
醋酸盐化合物例如优选为选自由乙酸乙酯、乙酸钠、乙酸甲酯、乙酸钾和乙酸铵组成的组中的一种或两种。
[0084]
(h)水
[0085]
本发明的蚀刻剂组合物还可以包括水,并且可以残留量而被包括。残留量是指使进一步包括本发明的必需成分和其它成分的总组合物的重量为100重量%的剩余量。例如,相对于组合物的总重量,本发明中的含量可以为65至94重量%。
[0086]
所述水没有特别限制,但优选为使用去离子水。此外,所述水更优选为使用电阻率值为18mω
·
cm以上的去离子水,该电阻率值表示水中离子的去除程度。
[0087]
《布线形成方法及用于液晶显示装置的阵列基板的制造方法》
[0088]
此外,本发明提供了使用根据本发明的蚀刻剂组合物的布线形成方法和/或用于液晶显示装置的阵列基板的制造方法。根据本发明的蚀刻剂组合物的布线形成方法和/或用于液晶显示装置的阵列基板的制造方法可以适用关于根据本发明的蚀刻剂组合物描述的所有内容,并且省略对重叠部分的详细描述,但是即使省略其描述也可以同样适用。
[0089]
根据本发明的布线形成方法包括以下步骤:在基板上形成金属膜;在所述金属膜上形成光刻胶图案;以及以所述光刻胶图案为掩膜,用根据本发明的蚀刻剂组合物对所述金属膜进行蚀刻,其中,形成所述金属膜的步骤包括:层压一层以上的金属膜。
[0090]
例如,双层布线形成方法包括以下步骤:(i)在基板上形成钼基金属膜;(ii)在所述钼基金属膜上形成铜基金属膜;(iii)选择性地在所述铜基金属膜上留下光反应材料;以及(iv)使用本发明的蚀刻剂组合物批量蚀刻所述铜基金属膜和钼基金属膜。
[0091]
此外,例如,三层膜的布线形成方法包括以下步骤:(i)在基板上形成第一钼基金属膜;(ii)在所述钼基金属膜上形成铜基金属膜;(iii)在所述铜基金属膜上形成第二钼基金属膜;(iv)在所述第二钼基金属膜上选择性地留下光反应材料;(v)使用本发明的蚀刻剂组合物批量蚀刻所述铜基金属膜、第一钼基金属膜和第二钼基金属膜。
[0092]
在本发明的布线形成方法中,所述光反应材料优选为常规的光刻胶材料,并且可以通过常规的曝光和显影工艺选择性地被留下。
[0093]
当蚀刻铜基金属膜时,本发明的蚀刻剂组合物可以实现蚀刻均匀性和直线度优异的锥度轮廓。本发明的蚀刻剂组合物在蚀刻过程中不产生残留物,因此不存在诸如电短路、布线缺陷和亮度降低等问题。因此,本发明的蚀刻剂组合物可以非常有用地用于制造液晶显示装置的阵列基板,该阵列基板实现大画面和高亮度的电路。
[0094]
此外,本发明的蚀刻剂组合物可以批量蚀刻由铜基金属膜制成的液晶显示装置的栅电极、栅极布线、源电极/漏电极和数据布线层。
[0095]
本发明的用于液晶显示装置阵列基板的制造方法包括以下步骤:(a)在基板上形成栅极布线;(b)在包括所述栅极布线的基板上形成栅极绝缘层;(c)在所述栅极绝缘层上形成半导体层;(d)在所述半导体层上形成源电极和漏电极;以及(e)形成与所述漏电极连接的像素电极,其中,所述步骤(e)包括:通过使用根据本发明的蚀刻剂组合物进行蚀刻来形成像素电极的工艺。
[0096]
所述用于液晶显示装置阵列基板可以为薄膜晶体管(tft)阵列基板。
[0097]
在下文中,将通过实施例更详细地描述本发明。然而,以下实施例用于更详细地说明本发明,并且本发明的范围不受以下实施例的限制。
[0098]
实施例和比较例:蚀刻剂组合物的制备
[0099]
根据下表1中所示的组成来制备实施例1至14以及比较例1至6的蚀刻剂组合物。
[0100]
此外,在下表1中,描述了根据实施例和比较例的蚀刻剂组合物通过以下等式1计算的y值:
[0101][0102]
[表1]
[0103]
[0104][0105]
在表1中,用于制备蚀刻剂组合物的材料如下。
[0106]
(a)过氧化氢(h2o2);
[0107]
(b)氟化合物:氟化氢铵;
[0108]
(c)唑类化合物:氨基四唑;
[0109]
(d)一个分子内具有氮原子和羧基的水溶性化合物(螯合剂):亚氨基二乙酸;
[0110]
(e)磷酸盐化合物:apm(磷酸一铵)、nhp(磷酸一钠);
[0111]
(f)硫酸盐化合物:as(硫酸铵)、pbs(硫酸氢钾)。
[0112]
试验例:评估蚀刻剂组合物的特性
[0113]
在玻璃基板(100mm
×
100mm,钠钙玻璃(soda lime glass)或大猩猩玻璃(gorilla glass))上沉积金属氧化物膜,在通过光刻工艺在所述膜上沉积铜膜或多层膜(cu/moniti双层膜或moalti/cu/moalti三层膜)以在基板上形成具有预定图案的光刻胶之后,分别使用实施例1至14以及比较例1至6的组合物执行蚀刻工艺。
[0114]
采用喷淋式蚀刻法的实验设备(型号名称:etcher(tft),semes公司),蚀刻过程中蚀刻剂组合物的温度约为33℃,但由于其他工艺条件和其他因素,因此可以根据需要改变适当的温度。
[0115]
蚀刻时间可根据蚀刻温度而变化,但通常进行约110秒。参照图1至图3,使用横截面sem(hitachi公司制造,型号名称s-4700)检查在蚀刻工艺中蚀刻的铜基金属膜的轮廓。
[0116]
(1)铜蚀刻速率评估
[0117]
在沉积有铜膜的基板上使用根据实施例和比较例的蚀刻剂组合物测量铜蚀刻速率,并将其结果示于下表2中。通过测量沉积厚度然后测量蚀刻时间来计算铜蚀刻速率。
[0118]
当铜蚀刻速率小于时,会出现产能问题,如果超过设备无法响应,因此当铜蚀刻速率满足60至时,判断为优异。
[0119]
《铜蚀刻速率评估标准》
[0120]
○
:60至/秒
[0121]
х:小于或大于
[0122]
(2)cu/moniti双层蚀刻评估-锥角
[0123]
在沉积有cu/moniti双层膜的基板上,使用根据实施例和比较例的蚀刻剂组合物批量蚀刻所述双层。在蚀刻之后,测量锥角,并将其结果示于下表2中。
[0124]
如果锥角小于35
°
,则在布线密集的区域由于光刻胶剥离(pr peeling)导致的开口发生率会增加,如果超过55,则由于在后续工艺中沉积绝缘膜时的阶梯覆盖变差,短缺陷也会增加,因此锥角为35
°
至55
°
时,判断为优异。
[0125]
《锥角评估标准》
[0126]
○
:35
°
到55
°
[0127]
х:小于35
°
或大于55
°
[0128]
(3)moalti/cu/moalti三层膜蚀刻评估-是否出现尖端
[0129]
使用根据实施例和比较例的蚀刻剂组合物在形成有moalti/cu/moalti三层膜的基板上批量蚀刻所述三层膜,并且在下表2中示出在蚀刻之后是否出现尖端。尖端是指三层膜中的中间层过刻蚀,上部膜部分凸出的现象,图2左边的sem图像为刻蚀后没有产生尖端的状态,图3是比较例如1的sem图像,可以确认在蚀刻后产生尖端的状态。
[0130]
(4)是否出现析出物的评估
[0131]
在蚀刻形成在玻璃基板(钠钙玻璃或大猩猩玻璃)上的cu/moniti膜和/或moalti/cu/moalti膜时,确认了是否出现铝(al)析出物(参见图4)和硅(si)析出物(参见图5),并将其结果示于下表3中。
[0132]
在玻璃基板中,钠钙玻璃是硬度低的玻璃,大猩猩玻璃是硬度高的玻璃。
[0133]
(5)开口缺陷发生的评估
[0134]
在用根据实施例和比较例的蚀刻剂组合物蚀刻金属膜以形成布线之后,在光学显微镜下确认开口缺陷的数量,并将其结果示于下表3。所述开口缺陷是由于析出物的出现而产生的现象,随着析出物量的增加,开口缺陷的数量也增加。
[0135]
(6)过滤器更换周期
[0136]
将14张5cm
×
5cm的基板在1l的根据实施例和比较例的蚀刻剂组合物中放置1天后,用过滤器过滤以测定施加到过滤器的析出物的量,并根据析出物的量评估过滤器更换周期并将其示于下表3中。
[0137]
随着析出物量增加,过滤器更换周期变短,并且由于一般情况下,即使没有析出物,工艺上过滤器的更换周期也是3个月,因此在没有析出物产生的情况下,过滤器更换周期设定为3个月。
[0138]
[表2]
[0139][0140][0141]
[表3]
[0142][0143][0144]
参考表2和表3,当使用实施例1至14的蚀刻剂组合物时,就优异的cu蚀刻速率和锥度而言蚀刻特性优异,并且在三层膜蚀刻中未出现尖端,并且没有出现析出物,由此也没有出现开口缺陷。
[0145]
具体而言,在实施例1至14的蚀刻剂组合物中,玻璃基板为大猩猩玻璃时,由于没有出现析出物,由此也没有出现开口缺陷,并且表现出优异的蚀刻特性。此外,图1和图2是用根据实施例1的蚀刻剂组合物蚀刻的双层膜或三层膜的sem照片,可以确认具有优良的蚀刻轮廓和直线度,并且在三层膜中没有出现尖端。然而,在实施例13和14的情况下,可以确认在玻璃硬度低的钠钙玻璃中产生si析出物,但是在使用玻璃硬度高的大猩猩玻璃的情况
下没有产生析出物。
[0146]
另一方面,当使用比较例1至6的蚀刻剂组合物时,会出现析出物和开口缺陷,从而显着缩短了过滤器更换周期。特别是,在y值在16至200的范围之外的比较例1至5的情况下,产生si析出物,并且在三层膜蚀刻期间出现上部尖端(参见图3),并且在y值超过200的比较例4和5中,在蚀刻形成在高硬度玻璃基板上的金属膜时没有产生沉淀物,但是出现了铜蚀刻速率过高的问题。此外,在磷酸盐化合物和/或硫酸盐化合物不含铵盐的比较例2和6中,产生了al析出物。进而,在比较例中,随着析出物的产生,开口缺陷的数量增加,并且由于析出物在蚀刻装置中累积,因此缩短了过滤器更换周期。