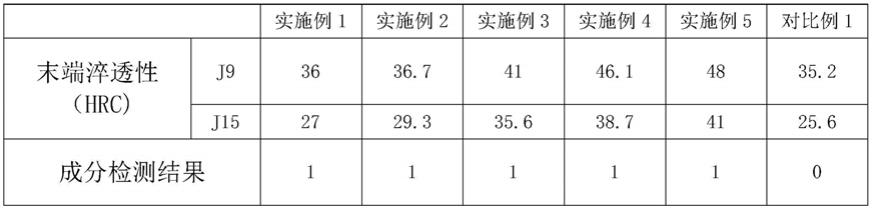
一种22crmoh保淬透性齿轮钢及其制备方法
技术领域
1.本技术涉及冶金制备制造技术领域,尤其是涉及一种22crmoh保淬透性齿轮钢及其制备方法。
背景技术:
2.保淬透性钢主要应用于汽车、工程机械及机械制造业的齿轮、齿轮轴等传动部件。齿轮钢是指可用于加工制造齿轮的钢材。
3.汽车行业的稳步发展,客户对齿轮钢的需求量日益增加,且对齿轮钢质量的要求也越来越严格,其中淬透性带的宽度是衡量保淬透性齿轮钢钢材质量的重要指标,因此在汽车齿轮钢的冶炼技术中,通过控制钢材淬透性带的宽度,来提高齿轮钢的性能。
4.针对上述中的相关技术,汽车齿轮在使用的过程中,不仅要承受较大的负荷,还要承受较大的冲击,因此齿轮的磨削量增加、咬合精度减小。
技术实现要素:
5.为了减小齿轮的磨削量,增加齿轮的咬合精度,本技术提供一种22crmoh保淬透性齿轮钢的制备方法。
6.第一方面,本技术提供的一种22crmoh保淬透性齿轮钢,采用如下的技术方案:一种22crmoh保淬透性齿轮钢,包括以下质量百分比的组分,c:0.20-0.21%,si:0.20-0.30%,mn:0.75-0.81%,cr:1.05-1.10%,mo:0.38-0.40%,其余为fe、杂质和其他合金元素;杂质含量满足p:≤0.020%,s:≤0.010%,cu:≤0.25%,ti:≤0.006%。
7.通过采用上述技术方案,22crmoh的化学成分在原有的基础上进行成分控制范围收窄,并在制备的过程中精确控制,得到的齿轮钢末端淬透性稳定,并且实现了窄淬透带的控制,因此齿轮钢离散度小,减小齿轮钢热处理后的变形量,进而减小齿轮的磨削量,提高齿轮的咬合精度。
8.由于齿轮钢末端淬透性稳定,使晶粒细小均匀,因此提高了齿轮钢的脆断抗力,提高机械的强度,进而减小齿轮出现裂纹的可能性,增加齿轮的疲劳寿命。
9.另外,由于齿轮钢末端淬透性稳定,因此齿轮钢的窄淬透性带,晶粒细小均匀、带状组织级别低,纯洁度高,进而提高了齿轮的纯净度和疲劳寿命。
10.综上所述,由于齿轮钢化学成分控制范围变窄,得到的齿轮钢末端淬透性稳定,使齿轮钢淬透性带窄,因此减小齿轮钢变形量,齿轮的磨削量减小,进而提高齿轮的咬合精度,且增加齿轮的疲劳寿命和纯净度。
11.可选的,所述其他合金元素包括al,al在齿轮钢中的含量为al:0.020-0.040%。
12.通过采用上述技术方案,通过控制齿轮钢中al的元素含量,进而控制齿轮钢成分均匀,使齿轮钢奥氏体晶粒细小且无混晶现象。
13.可选的,所述杂质含量还包括t[o]:≤20ppm,t[n]:≤70ppm。
[0014]
通过采用上述技术方案,通过控制齿轮钢中杂质的含量,减小杂质对齿轮钢性能
的影响。
[0015]
第二方面,本技术提供上述一种22crmoh保淬透性齿轮钢的制备方法,采用如下的技术方案:一种22crmoh保淬透性齿轮钢的制备方法,包括以下步骤:s1.转炉初炼:向转炉中加入铁水、废钢和生铁;采用底吹的方式供氧,全程吹氩;s2.钢包脱氧合金化:达到终点控制要求,周转包,底吹畅通,无渣出钢,加入脱氧剂、合金,并在放钢后期加入石灰渣洗;s3.lf精炼:lf炉中进行底吹氩气、通电造渣、调整成分、喂丝处理;s4.真空精炼:vd炉中进行底吹控制、真空控制和软吹处理;s5.连铸:大包采用氩封长水口,中包采用φ40mm的水口,结晶器保护渣用方坯低碳保护渣,并进行温度控制和浇注控制;s6.轧制;其中所述连铸过程中浇注过热度控制在15-20℃。
[0016]
通过采用上述技术方案,在齿轮钢生产过程中,调节每个制备步骤中的参数,调控齿轮钢化学成分范围,得到的齿轮钢成分范围稳定且窄,得到窄淬透性带齿轮钢。在制备过程中与原制备过程相比,降低连铸中的浇注过热度,可有效减小铸坯的成分偏析程度,降低齿轮钢淬透性带带宽,增加材料的组织均匀性,使带状组织控制级别低。
[0017]
可选的,步骤s1中所述转炉初炼的放钢终点控制为,高拉补吹c≥0.08,p≤0.015%,出钢温度≥1640℃;步骤s3中所述lf精炼的lf炉进站温度为≥1530℃,吊包温度1620-1630℃,液相线1510℃;步骤s4中所述vd炉进行抽真空保持15分钟以上的软吹搅拌。
[0018]
通过采用上述技术方案,在齿轮钢制备的过程中,由于通过控制转炉初炼的放钢终点、升高lf精炼温度和增加vd炉软吹搅拌时间,因此减小齿轮钢中s、p和cu等残余元素的含量,降低高倍夹杂,齿轮钢成分控制范围变窄,减小齿轮钢淬透性带带宽,进而增加了齿轮钢的纯净度。
[0019]
可选的,步骤s5中所述连铸采用全程保护浇注和等离子加热。
[0020]
通过采用上述技术方案,在连铸过程中,采用全程保护浇注,且用等离子加热控制浇注过热度,以此减小钢水二次氧化,提高钢材的洁净度,进而提高钢材的纯净度。
[0021]
可选的,步骤s2的所述脱氧剂为铝,每吨钢水加入所述铝的用量为1.0-1.5kg。
[0022]
通过采用上述技术方案,脱氧剂采用铝块,可有效的降低钢水中的氧含量,且在使用过程中不会引入其他杂质,因此提高了齿轮钢的疲劳寿命,同时保证了齿轮钢有较高的合格率。
[0023]
可选的,步骤s2中加入所述脱氧剂后,在步骤s3中进行所述喂丝处理,通过喂丝机向钢包中每秒为喂铁钙线1.31-2.18kg,进行软吹8-10min以上。
[0024]
通过采用上述技术方案,用脱氧剂铝块脱氧后,产生al2o3链状夹杂物。在钢水中加入一定量的钙后,对al2o3链状夹杂物进行了改性,改性后al2o3夹杂物的密度比钢水密度小,al2o3夹杂物在炼钢连铸温度下呈液态,就可以使大量的这类脱氧产物在进入中间包之前从钢液中上浮去除,不仅可以减轻中间包水口堵塞问题保证连铸顺利进行,而且可以增加钢材的纯净度,改善钢材的质量。
[0025]
可选的,步骤s3中,lf精炼过程中铝与氮的摩尔含量之间的比例是(2-3):1,钛与
氮的摩尔含量之间的比例是(1-2):1。
[0026]
通过采用上述技术方案,在制备齿轮钢的过程中,通过控制钢水中残余al、ti和n的比例,细化晶粒,并且控制成分均匀,使奥氏体晶粒细小且无混晶现象。
[0027]
奥氏体晶粒度使齿轮渗碳热处理晶粒长大趋势小,稳定齿轮钢末端淬透性,晶粒细小均匀,因此减小热处理后齿轮形变的可能性,进而提高齿轮的脆断抗力。
[0028]
综上所述,通过控制钢水中残余al、ti和n的比例,减小齿轮钢的奥氏体晶粒,稳定齿轮钢末端淬透性,增加齿轮的脆断抗力。
[0029]
综上所述,本技术包括以下至少一种有益技术效果:1.通过设计齿轮钢窄化学成分范围,由于齿轮钢化学成分控制范围窄,得到的齿轮钢末端淬透性稳定且窄,因此减小齿轮的磨削量,提高齿轮的咬合精度,且增加齿轮的疲劳寿命和纯净度;2.通过设计齿轮钢制备方法,在齿轮钢生产过程中,在齿轮钢生产过程中,调节每个制备步骤中的参数,调控齿轮钢化学成分范围,得到的齿轮钢成分范围稳定且窄,得到窄淬透性带齿轮钢;3.通过控制钢水中残余al、ti和n的比例,减小齿轮钢的奥氏体晶粒,稳定齿轮钢末端淬透性,增加齿轮的脆断抗力。
具体实施方式
[0030]
实施例1一种22crmoh保淬透性齿轮钢的制备方法,包括一下步骤:s1.转炉初炼:向转炉中加入铁水、废钢和生铁;进入转炉的铁水,采用底吹的方式供氧,氧压1.0mpa,全程吹氩8min;造渣碱度控制在3.0;放钢终点控制:高拉补吹,c控制在0.08%,p:0.015%,出钢温度1640℃;s2.钢包脱氧合金化:达到终点控制要求,正常周转包,干净、烘烤合格、底吹畅通,中修包、小修包周转3次方可投入使用,无渣出钢,每吨钢水中加入铝块1.5kg;按顺序依次在每吨钢水加入人造石墨1kg、硅锰13.45kg、硅铁1.21kg、低碳铬铁9.2kg、钼铁6.73kg,并在出钢过程中往钢包里加入石灰渣洗,每吨钢水中加入的石灰量为3kg;s3.lf精炼:lf炉进站温度为1530℃,吊包温度为1620℃,液相线温度为1510℃;lf炉中进行底吹氩气、通电造渣、调整成分、喂丝处理;底吹控制:在线底吹氩气:出钢过程吹ar流量100l/min,ar压力0.3mpa;造渣过程吹氩气:第一次通电过程流量为250l/min,第二次通电过程氩气流量50l/min,ar压力0.3mpa;软吹过程吹氩气:软吹11min,软吹过程中观察钢包内液面情况,控制好流量大小,以钢水不裸露为宜;通电造渣:化渣采用6级电压、电流25000a,送电加热造渣10min,测温、取样;再次通电采用4级电压,电流30000a,加入石灰,石灰的加入量分2批加入,第一批加入400kg,第二批加入200kg,再根据炉渣的流动性适当补加萤石;根据炉渣渣量,调整碱度,每吨钢水中总渣量为10
㎏
,碱度控制在3.0,白渣保持10min,feo:0.4%;渣面脱氧采用碳化硅、电石,每批加入量5kg,少加勤加,每吨钢水电石加入总量为0.99kg;调整成分:第一次通完电成分均匀后取样,化验结果出来后按目标成分进行调整,
调成份后适当提高底吹流量,严禁多次调整成分;喂丝处理:出战前成分、温度达到工艺要求后,通过喂丝机向钢包中每秒喂铁钙线1.31kg,周期为50min;s4.真空精炼:vd炉进站温度为1630℃,吊包温度为1575℃,液相线温度为1510℃;底吹控制:钢包进vd炉后,吹ar流量200l/min,压力0.4mpa,保证钢水不裸露,测温、取样;合盖真空脱气处理,氩气流量12nm3/h,压力0.6mpa;真空控制:真空度达到0.067kpa以下后保持15min,总真空时间控制在20min,真空处理前期氩气压力0.5mpa,真空处理后期氩气压力0.3mpa;软吹处理:待真空完毕后,吹氩弱搅拌15min后吊包,加碳化稻壳覆盖全渣面2袋,周期50min;s5.连铸:中包必须干净无杂物,开浇前进行氩气置换吹扫;大包采用氩封长水口,浸入水口采用φ40mm;结晶器保护渣用方坯低碳保护渣,要求干燥、洁净;温度控制:吊包温度1575℃,中包温度1540℃,液相线1510℃,等离子感应加热开启;浇注控制:铸坯规格:350mm
×
400mm;采用全保护浇注,拉速0.43m/min,开机/热换0.38m/min,结晶器水流量为185m3/h,二冷水比水量0.18l/
㎏
;结晶器电磁单向搅拌2hz、260a,末端电磁双向搅拌8hz、400a;等离子加热控制浇注过热度为20℃;中间包钢水液面高度300mm;上下炉连接转包浇钢时,中间包液面高度400mm;停浇时中间包液面高度250mm;采用全保护浇注,中包开浇后中包钢液到2/3高度时加入240kg中包覆盖剂,再加入70kg稻壳;连铸坯热装;s6.轧制,把轧钢棒材轧制成直径为40mm圆的棒材。
[0031]
实施例2s1.转炉初炼:向转炉中加入铁水、废钢和生铁;进入转炉的铁水,采用底吹的方式供氧,氧压1.1mpa,全程吹氩9min;造渣碱度控制在3.8;放钢终点控制:高拉补吹,c控制在0.09%,p:0.013%,出钢温度1650℃;s2.钢包脱氧合金化:达到终点控制要求,正常周转包,干净、烘烤合格、底吹畅通,中修包、小修包周转4次方可投入使用,无渣出钢,每吨钢水中加入铝块1.0kg;按顺序依次在每吨钢水加入人造石墨1kg、硅锰13.45kg、硅铁1.21kg、低碳铬铁9.2kg、钼铁6.73kg,并在出钢过程中往钢包里加入石灰渣洗,每吨钢水中加入的石灰量为3kg;s3.lf精炼:lf炉进站温度为1550℃,吊包温度为1630℃,液相线温度为1510℃;lf炉中进行底吹氩气、通电造渣、调整成分、喂丝处理;底吹控制:在线底吹氩气:出钢过程吹ar流量150l/min,ar压力0.4mpa;造渣过程吹氩气:第一次通电过程流量为350l/min,第二次通电过程氩气流量100l/min,ar压力0.4mpa;软吹过程吹氩气:软吹12min,软吹过程中观察钢包内液面情况,控制好流量大小,以钢水不裸露为宜;通电造渣:化渣采用6级电压、电流35000a,送电加热造渣10min,测温、取样;再次通电采用4级电压,电流35000a,加入石灰,石灰的加入量为加3批,第一批加入200kg,第二批加入360kg,第三批加入120kg,再根据炉渣的流动性适当补加萤石;根据炉渣渣量,调整碱度,每吨钢水中总渣量11
㎏
/吨钢,碱度控制在4.0,白渣保持11min以上,feo:0.35%;渣面脱氧采用碳化硅、电石,每批加入量10kg,少加勤加,每吨钢水电石加入总量为0.99kg;调
整成分:第一次通完电成分均匀后取样,化验结果出来后按目标成分进行调整,调成份后适当提高底吹流量,严禁多次调整成分;喂丝处理:出战前成分、温度达到工艺要求后,通过喂丝机向钢包中每秒喂铁钙线2.18kg,周期为50min;s4.真空精炼:vd炉进站温度为1620℃,吊包温度为1565℃,液相线温度为1510℃;底吹控制:钢包进vd炉后,吹ar流量100l/min,压力0.3mpa,保证钢水不裸露,测温、取样;合盖真空脱气处理,氩气流量7nm3/h,压力0.4mpa;真空控制:真空度达到0.067kpa以下后保持16min,总真空时间控制在22min,真空处理前期氩气压力0.4mpa,真空处理后期氩气压力0.2mpa;软吹处理:待真空完毕后,吹氩弱搅拌17min后吊包,加碳化稻壳覆盖全渣面3袋,周期50min;s5.连铸:中包必须干净无杂物,开浇前进行氩气置换吹扫;大包采用氩封长水口,浸入水口采用φ40mm;结晶器保护渣用方坯低碳保护渣,要求干燥、洁净;温度控制:吊包温度1565℃,中包温度1540℃,液相线1510℃,等离子感应加热开启;浇注控制:铸坯规格:350mm
×
400mm;采用全保护浇注,拉速0.43m/min,开机/热换0.38m/min,结晶器水流量为180m3/h,二冷水比水量0.18l/
㎏
;结晶器电磁单向搅拌2hz、260a,末端电磁双向搅拌8hz、400a;等离子加热控制浇注过热度为15℃;中间包钢水液面高度310mm;上下炉连接转包浇钢时,中间包液面高度410mm;停浇时中间包液面高度265mm;采用全保护浇注,中包开浇后中包钢液到2/3高度时加入240kg中包覆盖剂,再加入70kg稻壳;连铸坯热装;s6.轧制,把轧钢棒材轧制成直径为110mm圆的棒材。
[0032]
实施例3s1.转炉初炼:向转炉中加入铁水、废钢和生铁;进入转炉的铁,采用底吹的方式供氧,氧压1.2mpa,全程吹氩8.3min;造渣碱度控制在3.15;放钢终点控制:高拉补吹,c控制在0.1%,p:0.012%,出钢温度1665℃;s2.钢包脱氧合金化:达到终点控制要求,正常周转包,干净、烘烤合格、底吹畅通,中修包、小修包周转4次方可投入使用,无渣出钢,每吨钢水中加入铝块1.15kg;按顺序依次在每吨钢水加入人造石墨1kg、硅锰13.45kg、硅铁1.21kg、低碳铬铁9.2kg、钼铁6.73kg,并在出钢过程中往钢包里加入石灰渣洗,每吨钢水中加入的石灰量为3kg;s3.lf精炼:lf炉进站温度为1555℃,吊包温度为1628℃,液相线温度为1510℃;lf炉中进行底吹氩气、通电造渣、调整成分、喂丝处理;底吹控制:在线底吹氩气:出钢过程吹ar流量140l/min,ar压力0.375mpa;造渣过程吹氩气:第一次通电过程流量为315l/min,第二次通电过程氩气流量85l/min,ar压力0.385mpa;软吹过程吹氩气:软吹13min,软吹过程中观察钢包内液面情况,控制好流量大小,以钢水不裸露为宜;通电造渣:化渣采用6级电压、电流32000a,送电加热造渣10min,测温、取样;再次通电采用4级电压,电流34000a,加入石灰,石灰的加入量为加3批,第一批加入230kg,第二批加入400kg,第三批加入130kg,再根据炉渣的流动性适当补加萤石;根据炉渣渣量,调整碱度,每吨钢水中总渣量12
㎏
/吨钢,碱度控制在3.7,白渣保持12min以上,feo:0.30%;渣
面脱氧采用碳化硅、电石,每批加入量9kg,少加勤加,每吨钢水电石加入总量为1kg;调整成分:第一次通完电成分均匀后取样,化验结果出来后按目标成分进行调整,调成份后适当提高底吹流量,严禁多次调整成分;喂丝处理:出战前成分、温度达到工艺要求后,通过喂丝机向钢包中每秒喂铁钙线1.73kg,周期为50min;s4.真空精炼:vd炉进站温度为1623℃,吊包温度为1567℃,液相线温度为1510℃;底吹控制:钢包进vd炉后,吹ar流量110l/min,压力0.32mpa,保证钢水不裸露,测温、取样;合盖真空脱气处理,氩气流量8nm3/h,压力0.46mpa;真空控制:真空度达到0.067kpa以下后保持17min,总真空时间控制在23min,真空处理前期氩气压力0.43mpa,真空处理后期氩气压力0.23mpa;软吹处理:待真空完毕后,吹氩弱搅拌18min后吊包,加碳化稻壳覆盖全渣面3袋,周期50min;s5.连铸:中包必须干净无杂物,开浇前进行氩气置换吹扫;大包采用氩封长水口,浸入水口采用φ40mm;结晶器保护渣用方坯低碳保护渣,要求干燥、洁净;温度控制:吊包温度1567℃,中包温度1538℃,液相线1510℃,等离子感应加热开启;浇注控制:铸坯规格:350mm
×
400mm;采用全保护浇注,拉速0.43m/min,开机/热换0.38m/min,结晶器水流量为180m3/h,二冷水比水量0.18l/
㎏
;结晶器电磁单向搅拌2hz、260a,末端电磁双向搅拌8hz、400a;等离子加热控制浇注过热度为16.5℃;中间包钢水液面高度330mm;上下炉连接转包浇钢时,中间包液面高度420mm;停浇时中间包液面高度270mm;采用全保护浇注,中包开浇后中包钢液到2/3高度时加入240kg中包覆盖剂,再加入70kg稻壳;连铸坯热装;s6.轧制,把轧钢棒材轧制成直径为90mm圆的棒材。
[0033]
实施例4s1.转炉初炼:向转炉中加入铁水、废钢和生铁;进入转炉的铁水,采用底吹的方式供氧,氧压1.2mpa,全程吹氩8.8min;造渣碱度控制在3.7;放钢终点控制:高拉补吹,c控制在0.1%,p:0.012%,出钢温度1665℃;s2.钢包脱氧合金化:达到终点控制要求,正常周转包,干净、烘烤合格、底吹畅通,中修包、小修包周转4次方可投入使用,无渣出钢,每吨钢水中加入铝块1.15kg;按顺序依次在每吨钢水加入人造石墨1kg、硅锰13.45kg、硅铁1.21kg、低碳铬铁9.2kg、钼铁6.73kg,并在出钢过程中往钢包里加入石灰渣洗,每吨钢水中加入的石灰量为3kg;s3.lf精炼:lf炉进站温度为1555℃,吊包温度为1623℃,液相线温度为1510℃;lf炉中进行底吹氩气、通电造渣、调整成分、喂丝处理;底吹控制:在线底吹氩气:出钢过程吹ar流量119l/min,ar压力0.33mpa;造渣过程吹氩气:第一次通电过程流量为285l/min,第二次通电过程氩气流量68l/min,ar压力0.336mpa;软吹过程吹氩气:软吹13min,软吹过程中观察钢包内液面情况,控制好流量大小,以钢水不裸露为宜;通电造渣:化渣采用6级电压、电流27000a,送电加热造渣10min,测温、取样;再次通电采用4级电压,电流32000a,加入石灰,石灰的加入量为加3批,第一批加入230kg,第二批加入400kg,第三批加入130kg,再根据炉渣的流动性适当补加萤石;根据炉渣渣量,调整
碱度,每吨钢水中总渣量12
㎏
/吨钢,碱度控制在3.2,白渣保持12min以上,feo:0.30%;渣面脱氧采用碳化硅、电石,每批加入量6.5kg,少加勤加,每吨钢水电石加入总量为1kg;调整成分:第一次通完电成分均匀后取样,化验结果出来后按目标成分进行调整,调成份后适当提高底吹流量,严禁多次调整成分;喂丝处理:出战前成分、温度达到工艺要求后,通过喂丝机向钢包中每秒喂铁钙线1.73kg,周期为50min;s4.真空精炼:vd炉进站温度为1627℃,吊包温度为1573℃,液相线温度为1510℃;底吹控制:钢包进vd炉后,吹ar流量180l/min,压力0.375mpa,保证钢水不裸露,测温、取样;合盖真空脱气处理,氩气流量8nm3/h,压力0.55mpa;真空控制:真空度达到0.067kpa以下后保持17min,总真空时间控制在23min,真空处理前期氩气压力0.485mpa,真空处理后期氩气压力0.287mpa;软吹处理:待真空完毕后,吹氩弱搅拌18min后吊包,加碳化稻壳覆盖全渣面4袋,周期50min;s5.连铸:中包必须干净无杂物,开浇前进行氩气置换吹扫;大包采用氩封长水口,浸入水口采用φ40mm;结晶器保护渣用方坯低碳保护渣,要求干燥、洁净;温度控制:吊包温度1571℃;中包温度1533℃,液相线1510℃,等离子感应加热开启;浇注控制:铸坯规格:350mm
×
400mm;采用全保护浇注,拉速0.43m/min,开机/热换0.38m/min,结晶器水流量为180m3/h,二冷水比水量0.18l/
㎏
;结晶器电磁单向搅拌2hz、260a,末端电磁双向搅拌8hz、400a;等离子加热控制浇注过热度为17.5℃;中间包钢水液面高度330mm;上下炉连接转包浇钢时,中间包液面高度420mm;停浇时中间包液面高度270mm;采用全保护浇注,中包开浇后中包钢液到2/3高度时加入240kg中包覆盖剂,再加入70kg稻壳;连铸坯热装;s6.轧制,把轧钢棒材轧制成直径为50mm圆的棒材。
[0034]
实施例5s1.转炉初炼:向转炉中加入铁水、废钢和生铁;进入转炉的铁水,采用底吹的方式供氧,氧压1.2mpa,全程吹氩8.55min;造渣碱度控制在3.47;放钢终点控制:高拉补吹,c控制在0.1%,p:0.012%,出钢温度1665℃;s2.钢包脱氧合金化:达到终点控制要求,正常周转包,干净、烘烤合格、底吹畅通,中修包、小修包周转4次方可投入使用,无渣出钢,每吨钢水中加入铝块1.27kg;按顺序依次在每吨钢水加入人造石墨1kg、硅锰13.45kg、硅铁1.21kg、低碳铬铁9.2kg、钼铁6.73kg,并在出钢过程中往钢包里加入石灰渣洗,每吨钢水中加入的石灰量为3kg;s3.lf精炼:lf炉进站温度为1555℃,吊包温度为1626℃,液相线温度为1510℃;lf炉中进行底吹氩气、通电造渣、调整成分、喂丝处理;底吹控制:在线底吹氩气:出钢过程吹ar流量123l/min,ar压力0.35mpa;造渣过程吹氩气:第一次通电过程流量为298l/min,第二次通电过程氩气流量76l/min,ar压力0.355mpa;软吹过程吹氩气:软吹13min,软吹过程中观察钢包内液面情况,控制好流量大小,以钢水不裸露为宜;通电造渣:化渣采用6级电压、电流29000a,送电加热造渣10min,测温、取样;再次通电采用4级电压,电流33000a,加入石灰,石灰的加入量为加3批,第一批加入230kg,第二
批加入400kg,第三批加入130kg,再根据炉渣的流动性适当补加萤石;根据炉渣渣量,调整碱度,每吨钢水中总渣量12
㎏
,碱度控制在3.5,白渣保持12min以上,feo:0.30%;渣面脱氧采用碳化硅、电石,每批加入量7.6kg,少加勤加,每吨钢水电石加入总量为1kg;调整成分:第一次通完电成分均匀后取样,化验结果出来后按目标成分进行调整,调成份后适当提高底吹流量,严禁多次调整成分;喂丝处理:出战前成分、温度达到工艺要求后,通过喂丝机向钢包中每秒喂铁钙线1.73kg,周期为50min;s4.真空精炼:vd炉进站温度为1626℃,吊包温度为1571℃,液相线温度为1510℃;底吹控制:钢包进vd炉后,吹ar流量156l/min,压力0.35mpa,保证钢水不裸露,测温、取样;合盖真空脱气处理,氩气流量8.9nm3/h,压力0.51mpa;真空控制:真空度达到0.067kpa以下后保持17min,总真空时间控制在23min,真空处理前期氩气压力0.53mpa,真空处理后期氩气压力0.251mpa;软吹处理:待真空完毕后,吹氩弱搅拌18min后吊包,加碳化稻壳覆盖全渣面3袋,周期50min;s5.连铸:中包必须干净无杂物,开浇前进行氩气置换吹扫;大包采用氩封长水口,浸入水口采用φ40mm;结晶器保护渣用方坯低碳保护渣,要求干燥、洁净;温度控制:吊包温度1569℃;中包温度1535℃,液相线1510℃,等离子感应加热开启;浇注控制:铸坯规格:350mm
×
400mm;采用全保护浇注,拉速0.43m/min,开机/热换0.38m/min,结晶器水流量为182m3/h,二冷水比水量0.18l/
㎏
;结晶器电磁单向搅拌2hz、260a,末端电磁双向搅拌8hz、400a;等离子加热控制浇注过热度为17.5℃;中间包钢水液面高度330mm;上下炉连接转包浇钢时,中间包液面高度420mm;停浇时中间包液面高度270mm;采用全保护浇注,中包开浇后中包钢液到2/3高度时加入240kg中包覆盖剂,再加入70kg稻壳;连铸坯热装;s6.轧制,把轧钢棒材轧制成直径为73mm圆的棒材。
[0035]
对比例1采用现有的22crmoh齿轮钢,化学成分为,c:0.18%,si:0.31%,mn:0.70%,p:0.030%,s:0.015%,cr:1.15%,mo:0.36%,al:0.015%,ti:0.008%,b:0.0005%,v:0.007%,t[o]:21ppm,t[n]:75ppm,ni:0.3%,cu:0.3%,其余为fe和不可避免的杂质。
[0036]
性能检测参照gb/t5216-2014标准检测本技术实施例1-5和对比例1制备得到的齿轮钢末端淬透性、低倍组织、高倍组织和有害残余成分检测。
[0037]
对齿轮钢进行成分检测,其满足成分要求则记为1,不满足成分要求的记为0,成分要求为,c:0.20-0.21%,si:0.20-0.30%,mn:0.75-0.81%,p:≤0.020%,s:≤0.010%,cr:1.05-1.10%,mo:0.38-0.40%,al:0.020-0.040%,ti:≤0.006%,b:≤0.0003%,v:≤0.006%,t[o]:≤20ppm,t[n]:≤70ppm,ni:≤0.25%,cu:≤0.25%,其余为fe和不可避免的杂质。
[0038]
表1齿轮钢末端淬透性检测
从表1可以看出,本技术实施例1-5齿轮钢的淬透性优于对比例1,且实施例1-5齿轮钢的淬透性带窄且稳定。实施例1-5由上述制备方法制得的齿轮钢,符合成分要求。
[0039]
表2高倍组织检测表3低倍组织检测表4有害残余成分检测 实施例1实施例2实施例3实施例4实施例5对比例1p,%0.020.0190.0150.0110.0070.027s,%0.0150.0110.0130.0090.0050.02cu,%0.20.150.130.160.090.25从表2-4可以看出,与对比例1相比,本技术实施例1-5的齿轮钢夹杂物级别低,低倍组织良好,晶粒度高,晶粒细小,组织均匀,成分偏析偏析小,带状组织级别低,且齿轮钢有害成分掺杂少,因此制备的齿轮钢纯洁度高和疲劳寿命长。
[0040]
以上均为本技术的较佳实施例,并非依此限制本技术的保护范围,故:凡依本技术的结构、形状、原理所做的等效变化,均应涵盖于本技术的保护范围之内。