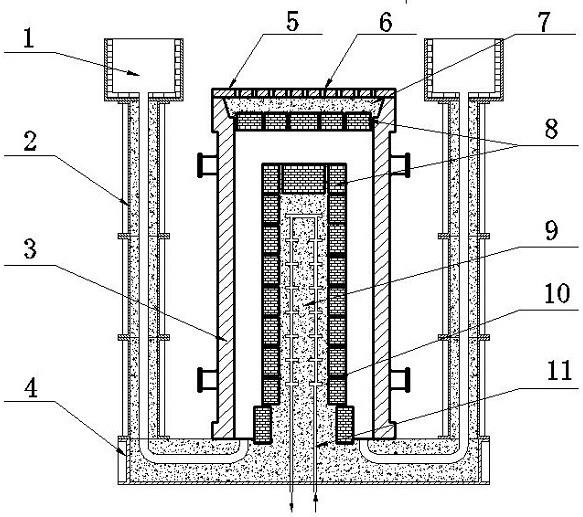
1.本实用新型涉及一种铸造百吨级乏燃料容器的模具,属于铸造领域。
背景技术:
2.核能的开发利用给人类带来了巨大的效用,中国近些年也正在积极发展核电项目,来提供清洁、安全、高效、可持续的电力能源保障,但随之产生的核废料会危害人类健康及环境安全,因此,科学处置核废料具有重大意义。在正常条件下,每台核电机组每年产生约25吨核废料,则我国核电厂每年共计产生约1000吨核废料。截至2017年底,我国核电厂已累计产生了7000多吨核废料,预计到2020年累计产生约9000吨,2030年累计产生约2万吨。基于我国核燃料后端目前的乏燃料运输能力和离堆贮存能力,我国将在2030年左右开始出现较大的乏燃料离堆贮存缺口。
3.而乏燃料贮运一体化金属容器是专门用于管理、贮存、运输乏燃料组件的容器,要求整体铸造成型,毛重130t,铁液量160t,壁厚达到500mm,需通过四项运输性事故条件的验证,包括贯穿试验、跌落试验、高温耐烧试验及水浸试验,各项性能指标要求严格,因此生产乏燃料贮运一体化球墨铸铁容器,需解决厚大断面球铁球化孕育及防衰退问题,保持铸件良好的性能要求。
4.公开号为cn110014123b的一种百吨级乏燃料贮运一体化金属容器的铸造方法,具体为百吨级乏燃料贮运一体化金属容器的造型工艺方法及铁砂组合铸型,尤其是为百吨级乏燃料贮运一体化金属容器的铸造方法及所用的铁砂组合铸型。铁模采用球墨铸铁铸造,外模由多部分和一个盖模组成,大坭芯为砂骨架加冷铁,冷铁嵌入型砂中,底部型砂采用呋喃树脂砂,造型完成后进行微震紧实,然后浇注,本工艺制定了专用工艺参数和工艺方法,使用浇注系统和过滤系统分离铁液中的一次氧化渣,并减少铁液与空气、铸型的化学反应,减少二次氧化渣,使铸件在凝固过程中石墨化膨胀充分抵消液态收缩和凝固收缩,消除缩孔和缩松。但是其仅靠大坭芯为砂骨架加冷铁结构来进行激冷降温,凝固时间仍然较长,易形成球化衰退,不利于石墨形态的保持;同时出气冒口的存在,使得铸型的刚性不足,在凝固过程中,石墨化膨胀,不利于形成致密的铸造组织。
技术实现要素:
5.本实用新型需要解决的技术问题是提供一种铸造百吨级乏燃料容器的模具,使得铁液在2小时凝固,解决了球墨铸铁容器凝固时石墨衰退问题,同时还使得制备的乏燃料贮运一体化金属容器组织均匀,致密性好,达到探伤及机械性能标准。
6.为解决上述技术问题,本实用新型所采用的技术方案是:
7.一种铸造百吨级乏燃料容器的模具,包括内部填充呋喃树脂砂的砂箱一种铸造百吨级乏燃料容器的模具,所述砂箱一种铸造百吨级乏燃料容器的模具的顶部固定设置有铸型和分立于铸型两侧、用于向铸型内部浇注铁液的双包双浇注系统;所述铸型包括固定于砂箱一种铸造百吨级乏燃料容器的模具上的金属型一种铸造百吨级乏燃料容器的模具和
设置于金属型一种铸造百吨级乏燃料容器的模具内部的内部呋喃树脂砂芯一种铸造百吨级乏燃料容器的模具,所述金属型一种铸造百吨级乏燃料容器的模具的顶部设置顶部呋喃树脂砂芯一种铸造百吨级乏燃料容器的模具;所述顶部呋喃树脂砂芯一种铸造百吨级乏燃料容器的模具的内侧与内部呋喃树脂砂芯一种铸造百吨级乏燃料容器的模具的外表面分别砌筑石墨冷铁一种铸造百吨级乏燃料容器的模具,相邻的石墨冷铁一种铸造百吨级乏燃料容器的模具之间保留有30~50mm的石墨冷铁间隙一种铸造百吨级乏燃料容器的模具,且石墨冷铁间隙一种铸造百吨级乏燃料容器的模具内部填充呋喃树脂砂;所述顶部呋喃树脂砂芯一种铸造百吨级乏燃料容器的模具的外侧设置铁板一种铸造百吨级乏燃料容器的模具,所述铁板一种铸造百吨级乏燃料容器的模具上均布铁板排气孔一种铸造百吨级乏燃料容器的模具。
8.本实用新型技术方案的进一步改进在于:所述内部呋喃树脂砂芯一种铸造百吨级乏燃料容器的模具的内部铺设循环水管道一种铸造百吨级乏燃料容器的模具,且循环水管道一种铸造百吨级乏燃料容器的模具延伸至砂箱一种铸造百吨级乏燃料容器的模具的外部与冷却塔连接。
9.本实用新型技术方案的进一步改进在于:所述双包双浇注系统包括两套浇口杯一种铸造百吨级乏燃料容器的模具和连接浇口杯一种铸造百吨级乏燃料容器的模具和铸型型腔口的浇道一种铸造百吨级乏燃料容器的模具,所述浇道一种铸造百吨级乏燃料容器的模具包括直浇道、横浇道和内浇道,且横浇道位于砂箱一种铸造百吨级乏燃料容器的模具的内部。
10.本实用新型技术方案的进一步改进在于:所述金属型一种铸造百吨级乏燃料容器的模具的厚度为200~300mm。
11.本实用新型技术方案的进一步改进在于:所述铁板一种铸造百吨级乏燃料容器的模具的厚度为100~200mm。
12.由于采用了上述技术方案,本实用新型取得的技术进步是:
13.本实用新型通过双包浇注,160t铁液在90~120s内浇注完毕,快速充型,提高型内铁液的均匀性;同时铸型采用外壁金属型、内部及上端石墨冷铁、树脂砂芯内部通水冷却的措施,能够保证型腔内铁液在2小时内快速均衡凝固(公开号为cn110014123b专利的凝固时间基本为7~9小时),解决了球墨铸铁容器凝固时石墨衰退问题。
14.本实用新型铸型的顶部设置石墨冷铁和呋喃树脂砂芯,且呋喃树脂砂芯的顶部设置开有铁板排气孔的铁板,铁液中的气体能够从石墨冷铁和呋喃树脂砂芯中逸出,相比于公开号为cn110014123b的专利,型腔内部的铁液达到一定压力后会从出气冒口逸出,本实用新型能够使得型腔内铁液的压力更大,得到组织更加致密的球墨铸铁铸件。
15.石墨冷铁采用高导热炭砖加工制作,石墨冷铁应保留30-50mm间隙并填入树脂砂,能够保证铸型的退让性,避免铸件收缩受阻。
16.本实用新型生产的百吨级乏燃料贮运一体化球墨铸铁容器,ut(超声波)探伤可达到专用探伤标准要求,解剖检测,铸件厚度内、外石墨形态、石墨等级无较大差别,组织均匀,性能良好。
附图说明
17.图1是本实用新型结构示意图;
18.其中,1、浇口杯,2、浇道,3、金属型,4、砂箱,5、铁板,6、铁板排气孔,7、顶部呋喃树脂砂芯,8、石墨冷铁,9、内部呋喃树脂砂芯,10、石墨冷铁间隙,11、循环水管道。
具体实施方式
19.下面结合实施例对本实用新型做进一步详细说明:
20.如图1所示,一种铸造百吨级乏燃料容器的模具,包括内部填充呋喃树脂砂的砂箱4,所述砂箱4的顶部固定设置有铸型和双包双浇注系统,双包双浇注系统分立于铸型两侧、用于向铸型内部浇注铁液,包括两套浇口杯1和连接浇口杯1和铸型型腔口的浇道2,所述浇道2包括直浇道、横浇道和内浇道,且横浇道位于砂箱4的内部。铁液通过双包双浇注系统同时浇注入铸型中,浇注时间为90~120s。
21.所述铸型包括固定于砂箱4上的金属型3和设置于金属型3内部的内部呋喃树脂砂芯9,所述金属型3的材质为球墨铸铁,厚度为200~300mm,且金属型3的顶部设置顶部呋喃树脂砂芯7;所述顶部呋喃树脂砂芯7的内侧与内部呋喃树脂砂芯9的外表面分别砌筑石墨冷铁8,石墨冷铁8采用高导热炭砖加工而成,相邻的石墨冷铁8之间保留有30~50mm的石墨冷铁间隙10,且石墨冷铁间隙10内部填充呋喃树脂砂;型腔内部铁液中的气体通过石墨冷铁和呋喃树脂砂向外逸出。
22.所述顶部呋喃树脂砂芯7的外侧设置铁板5,所述铁板5上均布铁板排气孔6。所述铁板5的厚度为100~200mm,保证一定的强度。铁液浇注时铁板5的顶部设置有座放压重,且座放压重的重量为浇注铁液的2~3倍,防止石墨膨胀时铸型膨胀。
23.内部呋喃树脂砂芯9的内部铺设循环水管道11,循环水管道11延伸至砂箱4的外部与冷却塔连接。铁液浇注完毕后向循环水管道11内通入15~30℃冷却水,通水时间12~24h,通水量5-10t/h。
24.具体包括以下步骤:
25.s1、准备砂箱4,使用呋喃树脂砂造型,将双包双浇注系统按照具体图纸要求摆放到位,将循环水管道11固定,使用呋喃树脂砂填满砂箱4,使用专用捣实工具捣实。
26.s2、待呋喃树脂砂硬化后,将内壁石墨冷铁8,按照图纸直径、高度要求,进行逐层砌筑,每层石墨冷铁间隙为30-50mm,内部及间隙填充呋喃树脂砂。
27.s3、金属型3使用煤气烘烤预热,在110-130℃时,金属型内壁喷涂专用涂料,涂料厚度控制1.5-2.5mm。
28.s4、顶部呋喃树脂砂芯7在专用芯盒内造型完成,按图纸要求在芯盒内部放置石墨冷铁,填入呋喃树脂砂,使用专用捣实工具捣实,在硬化12小时后起模。
29.s5、将上顶部呋喃树脂砂芯7底端面、内壁石墨冷铁8外壁喷涂专用涂料,厚度1.5-2.5mm。
30.s6、双包双浇注系统2选择合适直径耐材,填入呋喃树脂砂进行打制,选择合适规格浇口杯1使用耐材砌筑。
31.s7、按照装备图,将金属型3、顶部呋喃树脂砂芯7、铁板5、压重、双包双浇注系统2、浇口杯1逐项座放完毕,并将循环水系统接入冷却塔。
32.s8、根据熔炼、浇注工艺要求进行配料、冶炼得到铁液,铁液通过双包双浇注系统同时浇注入铸型中,浇注时间为90~120s。
33.s9、浇注完毕后,开启冷却水循环泵,进行降温冷却,控制水温15-30℃,通水时间12-24小时开箱,通水量5-10t/小时,得到乏燃料贮运一体化金属容器。