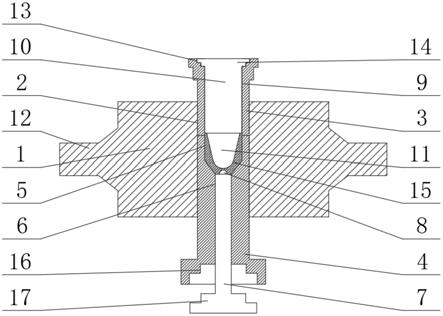
1.本实用新型属于射孔弹挤压模具技术领域,具体涉及一种石油射孔弹挤压模具。
背景技术:
2.聚能射孔弹是使用最广泛的射孔弹,也是射孔效率最高的射孔弹,常见有枪身聚能射孔弹结构主要有壳体、起爆药、主炸药和药形罩,弹壳多为钢壳,首要要求是承压能力,应确保形成理想形状的射流,主炸药是形成聚能射流的能量来源,为高能固体炸药,起爆药是与主炸药相同类型的炸药,但灵敏度更高,用于引爆主炸药,药形罩的作用是在主炸药爆炸后产生射流束,形成射孔孔道,射孔孔道的形态和质量主要由药形罩的材质和结构决定,射孔弹药形罩一般为锥形结构。
3.目前在射孔弹壳体制造领域,在对油气井实施全通径射孔施工时,射孔弹和弹架的碎片会留在井内,由于是全通径的射孔,要求射孔施工后射孔弹和弹架完全破碎成小颗粒碎屑,便于洗井液带出地面,使地下形成油气通径,这就要求全通径射孔施工,需采用粉末冶金制造射孔弹壳体,粉末冶金制造射孔弹壳体利用目雾化铁粉、天然鳞片石墨粉、铜粉、磷铁粉和工业用机油等,按照一定的比例调配完成后,注入射孔弹壳体的制造模具内,通过挤压最终压制成型,将压制烧结完成的弹壳放入弹壳精整模具对弹壳进行一次压制,将精整完成的弹壳推出即为粉末冶金射孔弹壳体,现有的石油射孔弹挤压模具通过把粉末冶金放入凹模内,通过压板带动凸模对凹模内的粉末冶金挤压,经过移动时间压制成型,存在不足之处有:成型后的射孔弹壳卡在在凹模内,需要使用特有的工具才能把射孔弹壳取出,造成取壳困难且浪费制造工期,存在模具使用不便的问题。
技术实现要素:
4.本实用新型的目的在于提供一种石油射孔弹挤压模具,以解决现有技术中存在模具使用不便的问题。
5.为实现上述目的,本实用新型提供如下技术方案:一种石油射孔弹挤压模具,包括固定座,所述固定座上端面设有铸模孔,所述铸模孔上端插设有上浮动模柱,所述铸模孔内下端插设有下固定模柱,所述上浮动模柱下端面与所述下固定模柱上端面接触连接,所述下固定模柱上端面设有锥形槽,所述锥形槽底端面设有穿孔,所述穿孔内下端插设有顶杆,所述顶杆上端面设置有弧形凸块,所述上浮动模柱上端面设有滑动孔,所述滑动孔内穿插有压杆,所述压杆下端面设置有锥形模块,所述锥形模块下端位于所述锥形槽内。
6.优选的,所述固定座两侧对应设置有安装耳座。
7.优选的,所述上浮动模柱上端外壁为梯形结构,所述上浮动模柱上端面设有第一梯形槽,所述压杆上端设置有梯形压板,所述梯形压板位于所述第一梯形槽内,所述顶杆上端面位于所述锥形槽内下端,所述锥形槽内位于所述顶杆上端与所述锥形模块下端之间固定连接有射孔弹壳。
8.优选的,所述下固定模柱为t字形结构,所述下固定模柱下端面设有第二梯形槽,
所述顶杆下端设置有底座。
9.与现有技术相比,本实用新型的有益效果是:
10.1.本实用新型首先把下固定模柱向上方调整,使下固定模柱的上端面与固定座的上端面在同一水平面,把顶杆向下方调整到预定的位置,把调配完成后的粉末冶金倒入锥形槽内,粉末冶金上端与固定座上端面平行,粉末冶金下端面位于顶杆上端,使锥形槽内的粉末冶金的量足够压制成射孔弹壳,此时控制上浮动模柱带动压杆向下方移动,在移动的过程中,上浮动模柱的下端面与下固定模柱的上端面紧密接触后,推动下固定模柱和顶杆在铸模孔内向下方移动,同时上浮动模柱的下端与下固定模柱的上端均位于铸模孔内,防止上浮动模柱与下固定模柱相互挤压发生偏移,导致射孔弹壳压制失败。
11.2.本实用新型再控制顶杆带动弧形凸块向上方移动,使顶杆上端面与锥形槽的下端面在同一水平面,再控制压杆带动锥形模块向下方移动,对锥形槽内的粉末冶金进行高压挤压,在对粉末冶金挤压的过程中,粉末冶金密度变大,同时粉末冶金发生收缩形变,挤压2s至10s后粉末冶金最终被挤压成型收缩成射孔弹壳,挤压成型后控制压杆带动锥形模块向上方移动,此时上浮动模柱同时向上方移动,脱离铸模孔,同时下固定模柱复位向上方移动,达到原始位置,控制顶杆向上方移动,带动压制成型后的射孔弹壳向上方移动,在移动的过程中当底座插入第二梯形槽内后,顶杆上端顶着射孔弹壳脱离铸模孔,位于固定座的上端,方便取下成型后的射孔弹壳,解决了模具使用不便的问题。
附图说明
12.图1为本实用新型的整体结构示意图;
13.图2为图1的剖切示意图;
14.图3为图2的射孔弹壳压制后示意图;
15.图4为图2的射孔弹壳压制前示意图。
16.图中:1、固定座;2、铸模孔;3、上浮动模柱;4、下固定模柱;5、锥形槽;6、穿孔;7、顶杆;8、弧形凸块;9、滑动孔;10、压杆;11、锥形模块;12、安装耳座;13、第一梯形槽;14、梯形压板;15、射孔弹壳;16、第二梯形槽;17、底座。
具体实施方式
17.下面将结合本实用新型实施例中的附图,对本实用新型实施例中的技术方案进行清楚、完整地描述。
18.如图1、图2、图3和图4所示,本实用新型实施例提供,一种石油射孔弹挤压模具,包括固定座1,固定座1上端面加工有铸模孔2,铸模孔2上端插入有上浮动模柱3,铸模孔2内壁与上浮动模柱3外壁滑动连接,铸模孔2的截面内壁直径与上浮动模柱3截面直径相同,铸模孔2内下端插入有下固定模柱4,铸模孔2内壁与下固定模柱4外壁滑动连接,铸模孔2内壁截面直径与下固定模柱4外壁截面直径相同,上浮动模柱3下端面与下固定模柱4上端面接触连接,下固定模柱4上端面加工有锥形槽5,锥形槽5底端面加工有穿孔6,穿孔6内下端插入有顶杆7,穿孔6内壁与顶杆7外壁滑动连接,穿孔6内壁截面直径与顶杆7外壁截面直径相同,顶杆7上端面焊接有弧形凸块8,上浮动模柱3上端面加工有滑动孔9,滑动孔9内穿插有压杆10,滑动孔9内壁锥形模块与压杆10外壁滑动连接,滑动孔9内壁截面直径与压杆10外
壁截面直径相同,压杆10下端面焊接有锥形模块11,锥形模块11底端面为弧形结构,11下端位于锥形槽5内,固定座1两侧对应焊接有安装耳座12,上浮动模柱3上端外壁为梯形结构,上浮动模柱3上端面加工有第一梯形槽13,压杆10上端焊接有梯形压板14,梯形压板14位于第一梯形槽13内,顶杆7上端面位于锥形槽5内下端,锥形槽5内位于顶杆7上端与锥形模块11下端之间固定连接有射孔弹壳15,下固定模柱4为t字形结构,下固定模柱4下端面加工有第二梯形槽16,顶杆7下端焊接有底座17,第二梯形槽16内壁截面直径大于底座17外壁截面直径。
19.本实施例的工作原理如下:首先把下固定模柱4向上方调整,使下固定模柱4的上端面与固定座1的上端面在同一水平面,把顶杆7向下方调整到预定的位置,把调配完成后的粉末冶金倒入锥形槽5内,粉末冶金上端与固定座1上端面平行,粉末冶金下端面位于顶杆7上端,使锥形槽5内的粉末冶金的量足够压制成射孔弹壳15,此时控制上浮动模柱3带动压杆10向下方移动,在移动的过程中,上浮动模柱3的下端面与下固定模柱4的上端面紧密接触后,推动下固定模柱4和顶杆7在铸模孔2内向下方移动,同时上浮动模柱3的下端与下固定模柱4的上端均位于铸模孔2内,防止上浮动模柱3与下固定模柱4相互挤压发生偏移,导致射孔弹壳15压制失败。再控制顶杆7带动弧形凸块8向上方移动,使顶杆7上端面与锥形槽5的下端面在同一水平面,再控制压杆10带动锥形模块11向下方移动,对锥形槽5内的粉末冶金进行高压挤压,在对粉末冶金挤压的过程中,粉末冶金密度变大,同时粉末冶金发生收缩形变,挤压2s至10s后粉末冶金最终被挤压成型收缩成射孔弹壳15,挤压成型后控制压杆10带动锥形模块11向上方移动,此时上浮动模柱3同时向上方移动,脱离铸模孔2,同时下固定模柱4复位向上方移动,达到原始位置,控制顶杆7向上方移动,带动压制成型后的射孔弹壳15向上方移动,在移动的过程中当底座17插入第二梯形槽16内后,顶杆7上端顶着射孔弹壳15脱离铸模孔2,位于固定座1的上端,方便取下成型后的射孔弹壳15,解决了模具使用不便的问题。
20.以上所述,仅为本实用新型的较佳实施例而已,并非用于限定本实用新型的保护范围。