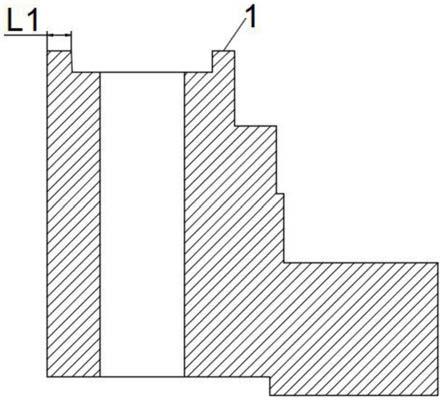
1.本发明涉及掘进机技术领域,具体地,涉及一种特大型掘进机主轴承套圈贴合面挡边的加工方法。
背景技术:
2.作为隧道掘进机核心部件之一的主驱动轴承为刀盘旋转提供扭矩同时,还承受推进系统的全部推力。现有技术中,掘进机主驱动轴承主要由轴承内套圈和三排滚动体组成,常见的掘进机轴承套圈由第一套圈和第二套圈组成,尺寸较大的还包括第三套圈,为了装配后更具有稳定性,一般在两套圈的贴合面设计一个内嵌式的浅槽来起到一个卡位固定的作用。
3.在加工大型掘进机主轴承套圈贴合面挡边的过程中,由于大型掘进机主轴承套圈贴合面挡边属于薄壁加工的范畴,且贴合面的套圈挡边高6mm,宽12mm,因此必须要有足够的硬度和韧性才能保证轴承的使用寿命。
4.目前针对大型掘进机主轴承套圈贴合面挡边的加工方法,采用的是先车加工后热处理的工艺方法,对高6mm宽12mm的薄壁件来进行表面感应淬火热处理,极易发生尖角效应和趋肤效应,从而出现裂纹、过热、金相组织粗大、硬化层过深等缺陷;且在车加工之后进行感应淬火热处理容易导致套圈的椭圆、滚道的椭圆、挡边的直线度存在变形。
技术实现要素:
5.本发明的目的在于针对现有技术中的不足,提供一种特大型掘进机主轴承套圈贴合面挡边的加工方法。
6.为实现上述目的,本发明提供了一种特大型掘进机主轴承套圈贴合面挡边的加工方法,包括以下步骤:
7.步骤一、粗加工:对主轴承套圈贴合面进行粗加工,并对主轴承套圈贴合面预留1.0mm-2.0mm的加工余量;
8.步骤二、表面处理:对主轴承套圈贴合面进行表面淬火处理;
9.步骤三、半精加工:对主轴承套圈贴合面半精加工形成贴合面挡边结构,并对主轴承套圈贴合面挡边预留0.5mm-1.0mm的加工余量;
10.步骤四、探伤处理:对主轴承套圈贴合面挡边进行探伤处理;
11.步骤五、精加工:对主轴承套圈贴合面挡边进行精加工,并对主轴承套圈贴合面挡边预留0.1mm-0.5mm的加工余量;
12.步骤六、精磨加工:对主轴承套圈贴合面挡边进行精磨加工。
13.可选的,所述步骤一中对主轴承套圈贴合面的预留加工余量设置为1.3mm-1.5mm。
14.可选的,所述步骤三中对主轴承套圈贴合面挡边的预留加工余量设置为0.6mm-0.8mm。
15.可选的,所述步骤四中对主轴承套圈贴合面挡边进行100%磁粉探伤处理。
16.可选的,所述步骤六中对主轴承套圈贴合面挡边的预留加工余量设置为0.3mm-0.5mm。
17.可选的,所述步骤二中对主轴承套圈贴合面进行表面淬火处理的具体步骤如下:
18.s2.1、加工前准备:根据主轴承套圈贴合面挡边的尺寸制作7字形的淬火感应器,并将感应器安装在淬火机床上;
19.s2.2、表面淬火:淬火机床通电,淬火感应器对主轴承套圈贴合面挡边进行加热淬火处理,使主轴承套圈贴合面挡边的组织由奥氏体变为马氏体。
20.可选的,所述步骤s2.2中淬火感应器对主轴承套圈贴合面挡边的加热温度设置为850℃-950℃。
21.可选的,所述感应器的横边尺寸大于等于主轴承套圈贴合面挡边的尺寸。
22.可选的,所述主轴承套圈贴合面挡边在表面淬火处理后的硬度为55hrc-62hrc,硬化层厚度大于等于4mm,淬火表面软带宽度小于等于50mm。
23.与现有技术相比,本发明具有以下有益效果:
24.本发明提供的一种特大型掘进机主轴承套圈贴合面挡边的加工方法,通过采用先对主轴承套圈贴合面进行粗加工和感应淬火后再加工出主轴承套圈贴合面挡边结构的加工工艺,以有效避免主轴承套圈贴合面挡边的尖角效应和趋肤效应,从而减小主轴承套圈贴合面挡边因表面处理而产生的变形问题。
25.除了上面所描述的目的、特征和优点之外,本发明还有其它的目的、特征和优点。下面将参照图,对本发明作进一步详细的说明。
附图说明
26.构成本技术的一部分的附图用来提供对本发明的进一步理解,本发明的示意性实施例及其说明用于解释本发明,并不构成对本发明的不当限定。在附图中:
27.图1是本发明实施例中主轴承套圈的截面示意图;
28.图2是本发明实施例中感应器的示意图。
29.其中:
30.1、主轴承套圈贴合面挡边,2、淬火感应器,l1、主轴承套圈贴合面挡边尺寸,l2、感应器横边尺寸。
具体实施方式
31.为使本发明的上述目的、特征和优点等能够更加明确易懂,下面结合附图对本发明的具体实施方式做详细的说明。需说明的是,本发明附图均采用简化的形式且均使用非精确比例,仅用以方便、清晰地辅助说明本发明实施;本发明中所提及的若干,并非限于附图实例中具体数量;本发明中所提及的
‘
前
’‘
中
’‘
后
’‘
左
’‘
右
’‘
上
’‘
下
’‘
顶部
’‘
底部
’‘
中部’等指示的方位或位置关系,均基于本发明附图所示的方位或位置关系,而不指示或暗示所指的装置或零部件必须具有特定的方位,亦不能理解为对本发明的限制。
32.本实施例:
33.一种特大型掘进机主轴承套圈贴合面挡边的加工方法,用于对主轴承套圈贴合面挡边1进行加工,包括以下步骤:
34.步骤一、粗加工:对主轴承套圈贴合面进行粗加工,并对主轴承套圈贴合面预留1.0mm-2.0mm的加工余量。此处优选:对主轴承套圈贴合面的预留加工余量优选设置为1.3mm-1.5mm,以便于表面处理时对主轴承套圈贴合面的淬火厚度能够精准控制。
35.步骤二、表面处理:对主轴承套圈贴合面进行表面淬火处理。此处优选:对主轴承套圈贴合面进行表面淬火处理的具体步骤如下:
36.s2.1、加工前准备:根据主轴承套圈贴合面挡边1的尺寸制作7字形的淬火感应器2,并将7字形淬火感应器2安装在淬火机床上;
37.s2.2、表面淬火:淬火机床通电,淬火感应器2开始对主轴承套圈贴合面挡边1进行加热,加热温度为850℃-950℃,使主轴承套圈贴合面挡边1的组织由奥氏体变为马氏体。此处可选:所述主轴承套圈贴合面挡边在表面淬火处理后的硬度为55hrc-62hrc,硬化层厚度大于等于4mm,淬火表面软带宽度小于等于50mm。
38.步骤三、半精加工:对主轴承套圈贴合面半精加工形成贴合面挡边1结构,并对主轴承套圈贴合面挡边1预留0.5mm-1.0mm的加工余量。此处优选:对主轴承套圈贴合面挡边的预留加工余量优选设置为0.6mm-0.8mm,以便保证后续对探伤处理的效果。
39.步骤四、探伤处理:对主轴承套圈贴合面挡边1进行100%磁粉探伤处理。
40.步骤五、精加工:对主轴承套圈贴合面挡边1进行精加工,并对主轴承套圈贴合面挡边1预留0.1mm-0.5mm的余量。此处优选:对主轴承套圈贴合面挡边的预留加工余量优选设置为0.3mm-0.5mm,以即能够减少精磨时的加工量,又能够实现精磨加工。
41.步骤六、精磨加工:对主轴承套圈贴合面挡边1进行精磨加工。
42.进一步的,为保证感应器对主轴承套圈贴合面挡边实现全面感应淬火,所述淬火感应器2的横边尺寸l2大于等于主轴承套圈贴合面挡边1的尺寸l1。
43.以上所述仅为本发明的优选实施例而已,并不用于限制本发明,对于本领域的技术人员来说,本发明可以有各种更改和变化。凡在本发明的精神和原则之内,所作的任何修改、等同替换、改进等,均应包含在本发明的保护范围之内。