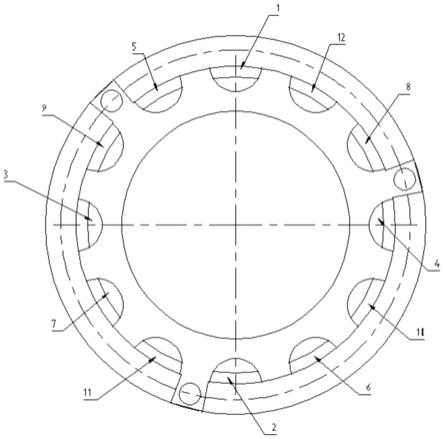
1.本发明涉及一种应用于异种材料超薄结构激光焊接的方法及装置,属于焊接技术领域。
背景技术:
2.激光焊接技术是近些年在材料连接领域快速发展的一种高能束焊接方法,该方法能够在大气环境中实现零件的高效、高可靠连接,目前在中厚零件的应用中较为广泛。国内汽车行业较多的开展了激光焊接工艺在薄板类零件制造中的应用研究,并实现了工业应用,但是在超薄板(厚度0.2mm)的焊接过程中,采用传统的连续激光及脉冲激光焊接易出现卷边、焊瘤等缺陷,尤其针对航天工业中常用的调压器、隔膜组件等薄壁膜片类零件,焊接后气密性不能满足产品使用要求,产品合格率低。
技术实现要素:
3.本发明要解决的技术问题是:克服现有技术的不足,提供了一种应用于异种材料超薄结构激光焊接的方法及装置,首先将连接环和保护工装连接,形成一端开放的腔体,向腔体内部通入保护气,形成保护腔,然后采用具有阵列结构的工装将超薄膜片与支撑环进行压紧装配,利用脉冲激光分段焊接方法将膜片和支撑环进行定位;然后拆除压紧工装,进行大离焦量下的整周焊接。本发明能够显著降低厚度0.2mm以内膜片类超薄零件在厚度差异较大且为异种材料焊接过程出现的卷边、烧穿和气密性不足等问题,显著降低薄膜零件对装配间隙的要求,提高了产品一次合格率。
4.本发明目的通过以下技术方案予以实现:
5.一种应用于异种材料超薄结构激光焊接装置,包括压板、底部工装;
6.底部工装为开口腔体结构,用于容置第一被焊接物;第二被焊接物与第一被焊接物紧贴放置;压板与底部工装连接后,将第二被焊接物与第一被焊接物固定;
7.压板上设有阵列式缺口,通过阵列式缺口,能够暴露第二被焊接物与第一被焊接物之间的局部焊缝;阵列式缺口均匀分布;
8.底部工装上设有管路接口,用于向底部工装的腔体内通入焊接保护气。
9.本发明一实施例中,阵列式缺口将第二被焊接物与第一被焊接物之间的所有焊缝平均分割。
10.本发明一实施例中,压板与底部工装连接后,压板的平面度优于0.1mm。
11.采用上述应用于异种材料超薄结构激光焊接装置的焊接方法,包括如下步骤:
12.将第一被焊接物放置在底部工装内,向底部工装内通入焊接保护气;
13.采用压板将第二被焊接物与第一被焊接物进行压紧装配,并将压板与底部工装连接;
14.利用脉冲激光分段焊接方法将第二被焊接物和第一被焊接物进行定位焊接;
15.拆除压板后,对第二被焊接物和第一被焊接物进行整周焊接;
16.其中第二被焊接物为膜片类,厚度不超过0.2mm。
17.本发明一实施例中,第二被焊接物和第一被焊接物为异种材料。
18.本发明一实施例中,焊接保护气的密度应大于空气密度。
19.本发明一实施例中,定位方式为分段定位,每段长度为5~10mm,定位顺序为对称定位;
20.本发明一实施例中,整周焊接时,脉冲焊接焊点的重叠率不小于50%,激光离焦量为+2~+10。
21.本发明一实施例中,进行定位焊接时,开启激光器引导光,采用表面聚焦的方法,在视频摄像头上寻找焊缝中心点,然后向压环方向偏移预定量,依次找正多段位置,最后进行焊接。
22.本发明一实施例中,整周焊接时,采用散焦方法进行焊接,离焦量为+6;定位焊接时,采用表面聚焦的方法进行焊接,离焦量为0。
23.本发明相比于现有技术具有如下有益效果:
24.(1)本发明向支撑环和底部工装连接后形成的腔体通入保护气,使得膜片零件在保护气氛中,避免了由于焊缝底部氧化形成的开裂、气孔等缺陷;
25.(2)本发明采用分段对称定位方式,使得薄膜类零件的受力状态得到改善,降低了膜片在焊接受热后的应力开裂的风险;
26.(3)本发明焊接过程采用较大的重叠率和较大的离焦量,降低了焊点间重合不足引起的气密泄露。
27.(4)本发明方法和装置具有通用性,可可适应同类型产品,能够极大的提升产品合格率。
附图说明
28.图1为焊接装配示意图。
29.图2为焊接装配剖视示意图。
30.图3为典型膜片结构示意图(材料为弹性合金、铜合金等)。
31.图4为定位焊的功率—焊波形变化图。
32.图5为正式焊接的功率—焊波形变化图。
33.图6为光束摆动变化图。
34.附图标记:压板-1、膜片-2、支撑环-3、底部工装-4。
具体实施方式
35.为使本发明的目的、技术方案和优点更加清楚,下面将结合附图对本发明的实施方式作进一步详细描述。
36.异种材料超薄结构激光焊接的装置,包括压板和底部工装;
37.(1)压板具有阵列式缺口,能够将焊缝位置平均分割,缺数量为3-20个;
38.(2)底部保护工装具有通气接管,并与压环形成紧密配合可形成半开口式腔体。
39.异种材料超薄结构激光焊接的方法,如图1和2所示,包括下列步骤:
40.(1)待焊材料为支撑零件和薄壁膜片零件,并且该两种次零件为异种材料;
41.(2)支撑环和底部工装连接后形成腔体,首先向腔体内通入保护气,因保护气密度较大,通入的保护气可排除腔体内空气,形成保护气氛;
42.(3)将膜片、具有阵列缺口的压板和底部保护工装进行连接;
43.(4)采用脉冲激光焊接模式,沿阵列缺口依次分段对称定位膜片;
44.(5)关闭背面保护气体,取出压板,采用脉冲激光模式,沿原有焊接轨迹进行整周焊接,形成密封焊缝。
45.所述步骤(1)中薄壁膜片厚度小于0.2mm,典型异种材料包括不锈钢、钛合金、弹性合金等材料;如图3所示;
46.所述步骤(2)中保护气密度应大于空气密度,典型气体为氦气、氩气等;通气时间为1~10min;
47.所述步骤(3)中压板和底部保护工装的连接过程中应保证压板平面度由于0.1mm。
48.所述步骤(4)中的定位方式为分段定位,每段长度为5~10mm,定位顺序为对称定位;
49.所述步骤(5)中脉冲焊接焊点的重叠率应大于50%,激光离焦量为+2~+10。
50.实施例1:
51.异种材料超薄结构激光焊接的方法,包括下列步骤:
52.(1)将支撑环和底部工装连接后形成腔体,向腔体内通入保护气,气体流量2l/min-10l/min,排除腔体内空气,形成保护气氛;
53.(2)采用脉冲激光焊接模式,沿阵列缺口依次对称定位膜片,可依据材料特点和装配状态,激光中心点向支撑环类材料偏移;
54.(3)关闭背面保护气体,取出压板,采用脉冲激光模式,保证脉冲激光形成的焊点重叠率不小于50%,沿原有焊接轨迹进行整周焊接,形成密封焊缝。
55.实施例2:
56.(1)将压调器支撑环3,外径42mm,材料为1cr18ni9ti,厚度为6.4mm,支撑环侧面加工有深度0.18mm的凹槽,装入底部工装4中。
57.(2)向工装中通入保护气,本实施例采用氩气,气体流量为2l/min,保持通气2min。
58.(3)将膜片2,厚度0.18mm~0.2mm,外径39mm,材料为3j21弹性合金,依次装入,通过调整压板的3个固定螺栓,保证压板平面度优于0.05mm。
59.(4)开启激光器引导光,采用表面聚焦的方法(离焦量为0),在视频摄像头上寻找焊缝中心点,然后向压环方向偏移0.02mm,按以上步骤依次找正12段位置,关闭背面保护气体。
60.(5)分段定位焊接,每段长度5mm,对称定位12段,定位时采用间隔对称方法,定位点间隔90
°
,逆时针方向循环定位,即附图1中1-12顺序。定位时采用脉冲焊接方法,在5mm范围内,波形变化如图4示,激光峰值功率为240w,基值40w,占空比60%,在收弧阶段设置功率平台,预防收弧裂纹的产生。
61.(6)取出压板,采用散焦方法(离焦量+6),进行整周焊接。本实施例参数波形变化图见图5。焊接区的参数为:焊接速度2.5m/min,激光峰值功率550w,基值功率40w,占空比60%,激光频率60hz。在圆周焊缝的起收弧重叠区域,为防止异种金属焊接时冷却速度过大产生裂纹,增加焊后缓冷脉冲,脉冲峰值300w,基值功率40w,占空比60%,激光频率100hz,
起收弧重叠角度为45
°
。
62.(7)焊后同时开背面保护气,正反面保护气继续通5min。
63.(8)在以上2个实施例中,为降低超薄零件焊前装配的裕度,采用摆动焊模式,摆动轨迹为沿焊接方向的顺时针圆型,扫描幅度0.3mm,扫描频率700hz,光束摆动示意图见图6。
64.本发明说明书中未作详细描述的内容属本领域技术人员的公知技术。
65.本发明虽然已以较佳实施例公开如上,但其并不是用来限定本发明,任何本领域技术人员在不脱离本发明的精神和范围内,都可以利用上述揭示的方法和技术内容对本发明技术方案做出可能的变动和修改,因此,凡是未脱离本发明技术方案的内容,依据本发明的技术实质对以上实施例所作的任何简单修改、等同变化及修饰,均属于本发明技术方案的保护范围。