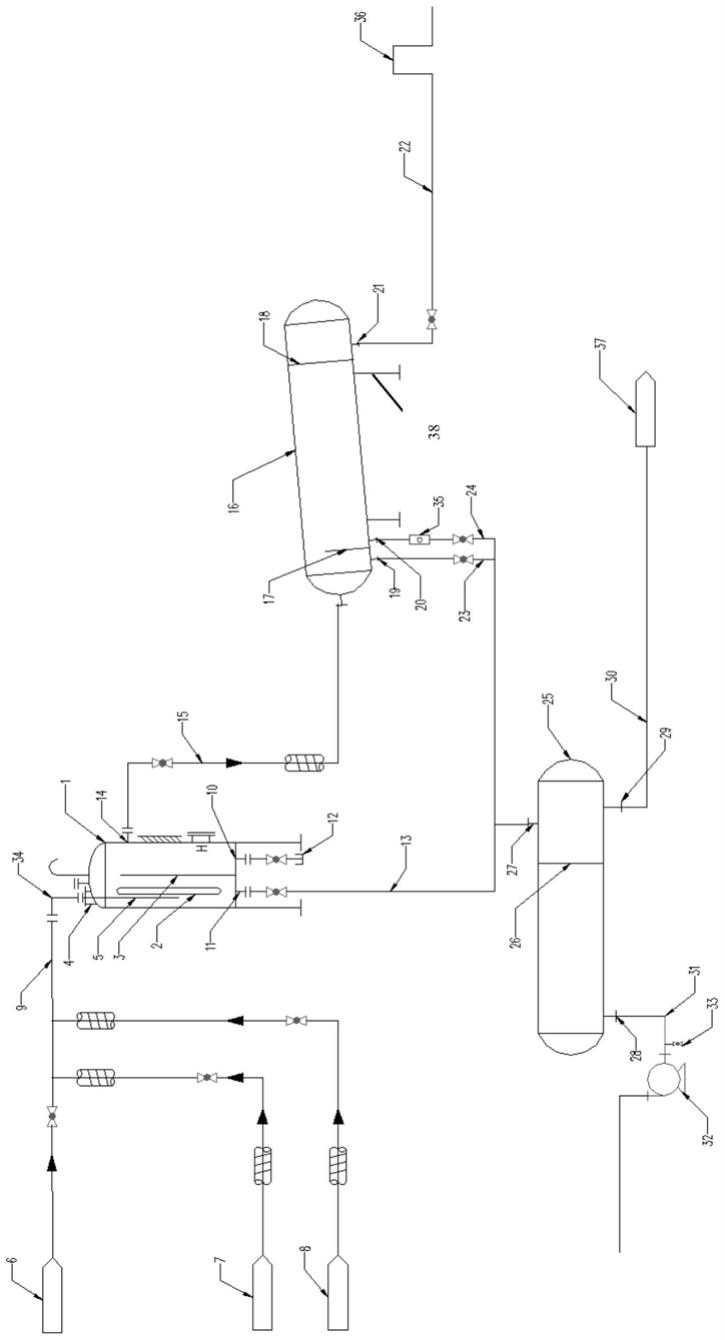
1.本实用新型涉及化工技术领域,特别是涉及一种顺酐生产中的废水用溶剂回收系统。
背景技术:
2.丁烷法生产顺酐的过程中反应器出来的气体只含有0.5%-2.5%(体积比)的顺酐,因此顺酐回收工艺在顺酐生产中占有重要地位。
3.有机溶剂吸收是目前顺酐吸收的主要方法。有机溶剂回收顺酐工艺采用的溶剂价格较高,因此,在工艺过程中必须设置有机溶剂的提纯精制部分,以使有机溶剂可以循环使用。目前,采用较多的溶剂是邻苯二甲酸二丁酯dbp。
4.溶剂与纯水混合,搅拌洗涤,进入离心机分离溶剂相和水相,溶剂相进入溶剂缓冲罐或溶剂倾析器进一步减少溶剂中的水含量,后进入吸收塔循环使用。水相中会带有少量油、醇、水过渡相等最后排入废水接受罐,这既造成物料的浪费,又增加污水处理系统的负担。
5.正丁烷法生产顺酐产生的废水主要来源于3部分:解析真空泵排出的废水,精制真空泵排除的废水和离心机轻相排出的含溶剂废水,废水ph=3~6.5,总有机物含量在1%~1.5%之间,是高浓度化工废水。
6.溶剂法顺酐生产中,当生产稳定时,溶剂回收后的废水中仍含有微量溶剂,这些微量溶剂并不再处理,直接排放到污水罐,最后排放至污水池;当生产不稳定时,溶剂回收后的废水含有大量油污,经过水槽沉降处理,废水溢流至污水罐,最后到污水池。现有技术方案在生产不稳定时才回收溶剂,水槽占地面积大,分离效果差;生产稳定时仍有少量溶剂未回收。溶剂是干净溶剂,直接排放造成浪费,且含有溶剂的废水达不到排放标准,需耗能处理。
7.探索一种顺酐溶剂回收装置,回收高价值的有机溶剂,降低顺酐生产的溶剂消耗是十分必要的;同时可以将废水中难以生化降解的有机物溶剂回收,提高顺酐废水的可生化降解性,减少处理废水的成本,降低对环境的污染,达到排放标准。
技术实现要素:
8.本实用新型的目的是针对现有技术中存在的顺酐生产过程中溶剂回收存在的弊端,而提供一种顺酐生产中的废水用溶剂回收系统。
9.为实现本实用新型的目的所采用的技术方案是:
10.顺酐生产中的废水用溶剂回收系统,包括溶剂沉降罐、倾析器和油相缓冲罐,其中:
11.所述溶剂沉降罐的顶部设有插入管道以连接废水接入管道,所述溶剂沉降罐由隔板分离形成左腔室和右腔室,所述左腔室和右腔室的顶部相连通,所述插入管道的出口位于所述左腔室的中部,所述左腔室的底部设有沉降溶剂出口,沉降溶剂出口通过溶剂输出
管路连接至所述油相缓冲罐的顶部入口,所述右腔室的底部设有检修放净口,所述右腔室的上部设有废水排出口,所述废水排出口通过溶剂回收后废水排出管路与所述倾析器的入口相连通;
12.所述倾析器的入口一端低另一端高,所述倾析器内靠近入口的一侧固定有隔油挡板,所述倾析器内另一侧固定有亲水超滤膜对流经所述倾析器内的液体进行过滤,所述倾析器的底部从低到高依次设有第一出口、第二出口和第三出口,所述第一出口、第二出口分别位于所述隔油挡板的两侧,且所述第二出口位于所述隔油挡板和亲水超滤膜之间,所述第二出口和第三出口分别位于所述亲水超滤膜的两侧,所述第三出口通过污水输出管路连接至污水池,所述第一出口、第二出口分别通过第一连接管路和第二连接管路连接至所述油相缓冲罐的顶部入口;
13.所述油相缓冲罐内设有憎水膜,所述憎水膜将所述油相缓冲罐分隔形成互相独立的油相腔室和水相腔室,所述顶部入口对应设置于所述水相腔室的顶部,所述水相腔室的底部设有水相出口;所述油相腔室的底部设有油相出口,所述油相出口连接循环回收管路,所述循环回收管路上设有循环泵和取样口。
14.在上述技术方案中,所述隔板的底部固定于所述溶剂沉降罐的底部内壁上,所述隔板的顶部与所述溶剂沉降罐的顶部内壁之间存在间隙,所述废水排出口的位置低于所述隔板的顶部边缘位置。
15.在上述技术方案中,连接滚筒离心机、精制真空泵和解析真空泵的废水出口分别通过管路连接至所述废水接入管道的入口上。
16.在上述技术方案中,所述水相出口通过连通管路连接至离心机前混合罐。
17.在上述技术方案中,所述溶剂沉降罐的顶部固定有支撑口,所述插入管道为可拆卸插入管道,所述可拆卸插入管道的顶部为水相进口,废水接入管道通过法兰连接于连接管上,所述连接管通过法兰连接于所述水相进口上,所述插入管道伸入至所述溶剂沉降罐内。
18.在上述技术方案中,所述检修放净口排出的液体通过管路输送至溶剂废水桶。
19.在上述技术方案中,所述左腔室对应的罐体侧壁上设有玻璃板液位计。
20.在上述技术方案中,所述第二连接管路上设有视镜。
21.在上述技术方案中,所述污水输出管路上设有向上弯折的凸起管段作为液封。
22.在上述技术方案中,所述憎水膜为疏水ptfe膜。
23.与现有技术相比,本实用新型的有益效果是:
24.1.本实用新型对顺酐生产中产生的废水反复进行水油分离,先进行粗分离,再对粗分离后的两相再次分离,使得溶剂最大限度的回收重复利用,降低了顺酐的生产成本。
25.2.本实用新型具有节能的有益效果,溶剂的废水分子量大,耗氧量多,处理溶剂需耗能,而本实用新型大大降低了废水的处理成本。
26.3.本实用新型的结构合理而紧凑,减少了设备的占地面积,工艺成熟,便于推广应用。
附图说明
27.图1所示为本实用新型的结构示意图。
28.图2所示为可拆卸插入管道的连接结构示意图。
29.图3是顺酐生产系统图。
30.图4是顺酐生产工艺流程图。
31.图中:1-溶剂沉降罐,2-玻璃板液位计,3-隔板,4-支撑口,5-插入管道,6-解析真空泵,7-精制真空泵,8-滚筒离心机,9-废水接入管道,10-检修放净口,11-沉降溶剂出口,12-溶剂废水桶,13-溶剂输出管路,14-废水排出口,15-溶剂回收后废水排出管路,16-倾析器,17-隔油挡板,18-亲水超滤膜,19-第一出口,20-第二出口,21-第三出口,22-污水输出管路,23-第一连接管路,24-第二连接管路,25-油相缓冲罐,26-憎水膜,27-顶部入口,28-油相出口,29-水相出口,30-连通管路,31-循环回收管路,32-循环泵,33-取样口,34-连接管,35-视镜,36-凸起管段,37-离心机前混合罐,38-支腿。
具体实施方式
32.以下结合附图和具体实施例对本实用新型作进一步详细说明。应当理解,此处所描述的具体实施例仅仅用以解释本实用新型,并不用于限定本实用新型。
33.实施例1
34.顺酐生产中的废水用溶剂回收系统,包括溶剂沉降罐1、倾析器16和油相缓冲罐25,其中:
35.所述溶剂沉降罐1的顶部设有插入管道5以连接废水接入管道9,所述溶剂沉降罐1由隔板3分离形成左腔室和右腔室,所述左腔室和右腔室的顶部相连通,所述插入管道5的出口位于所述左腔室的中部,所述左腔室的底部设有沉降溶剂出口11,沉降溶剂出口11通过溶剂输出管路13连接至所述油相缓冲罐25的顶部入口27,所述右腔室的底部设有检修放净口10,所述右腔室的上部设有废水排出口14,所述废水排出口14通过溶剂回收后废水排出管路15与所述倾析器16的入口相连通;
36.所述倾析器16的入口一端低另一端高,所述倾析器16内靠近入口的一侧固定有隔油挡板17(隔油挡板17的底部固定于所述倾析器16内底部,顶部与所述倾析器16的顶部保留间隙),所述倾析器16内另一侧固定有亲水超滤膜18对流经所述倾析器16内的液体进行过滤,所述倾析器16的底部从低到高依次设有第一出口19、第二出口20和第三出口21,所述第一出口19、第二出口20分别位于所述隔油挡板17的两侧,且所述第二出口20位于所述隔油挡板17和亲水超滤膜18之间,所述第二出口20和第三出口21分别位于所述亲水超滤膜18的两侧,所述第三出口21通过污水输出管路22连接至污水池,所述第一出口19、第二出口20分别通过第一连接管路23和第二连接管路24连接至所述油相缓冲罐25的顶部入口27;
37.所述油相缓冲罐25内设有憎水膜26,所述憎水膜26将所述油相缓冲罐25分隔形成互相独立的油相腔室和水相腔室,所述顶部入口27对应设置于所述水相腔室的顶部,所述水相腔室的底部设有水相出口29;所述油相腔室的底部设有油相出口28,所述油相出口28连接循环回收管路31,所述循环回收管路31上设有循环泵32和取样口33。
38.实施例2
39.作为优选的,所述隔板3的底部固定于所述溶剂沉降罐1的底部内壁上,所述隔板3的顶部与所述溶剂沉降罐1的顶部内壁之间存在间隙,所述废水排出口14的位置低于所述隔板3的顶部边缘位置。所述废水排出口14的位置比所述隔板3低约100mm.废水排出口14比
隔板3低可以再进行沉降。
40.作为优选的,连接滚筒离心机8、精制真空泵7和解析真空泵6的废水出口分别通过管路连接至所述废水接入管道9的入口上。对三路废水统一收集处理。
41.顺酐生产中产生的废水进入滚筒离心机8进行油水分离,滚筒离心机8分离出的含溶剂废水以及解析真空泵6排出的含溶剂废水,精制真空泵7排出的含溶剂废水通过废水接入管道9、插入管道5进入到溶剂沉降罐1内,溶剂密度大且带冲击力,沉降在溶剂沉降罐1的左腔室,大颗粒油类(粒径》150um)在左腔室不断富集,由沉降溶剂出口11排出,通过溶剂输出管路13进入到油相缓冲罐25内,废水则溢流至溶剂沉降罐1的右腔室,通过废水排出管路15进入到所述倾析器16;
42.溶剂输出管路13内溶液粒径大于150um,为大颗粒油类,废水排出管路15内为20~150um的分散油,在倾析器16内,再次进行油水分离,隔油挡板17与亲水超滤膜18之间为约20um的乳化油,经过亲水超滤膜18的过滤后,废水通过第三出口21、污水输出管路22输送至污水池做中和处理;经过隔油挡板17阻拦的油相通过第一出口19、第一连接管路23进入到油相缓冲罐25,经过亲水超滤膜18阻拦的油相通过第二出口20、第二连接管路24进入到油相缓冲罐25;
43.溶剂输出管路13、第一连接管路23和第二连接管路24均采用周期排放的方式。
44.在油相缓冲罐25内,憎水膜26对前期处理后的溶剂再次分离。
45.实施例3
46.所述水相出口29通过连通管路30连接至离心机前混合罐37。污水留在水相腔室,通过水相出口29打至溶剂预处理罐循环处理(进离心机前混合罐37),过滤得到的溶剂进入油相腔室通过油相出口28输出至循环回收管路31,然后通过取样口33取样检测,检测合格打至吸收器循环使用,检测不合格打至预混器循环使用。
47.作为优选的,所述溶剂沉降罐1的顶部固定有支撑口4,所述插入管道5为可拆卸插入管道,所述可拆卸插入管道的顶部为水相进口,废水接入管道9通过法兰连接于连接管34上,所述连接管34通过法兰连接于所述水相进口上,所述插入管道5伸入至所述溶剂沉降罐1内。
48.作为优选的,所述检修放净口10排出的液体通过管路输送至溶剂废水桶12。在检修时,通过检修放净口10放净溶剂沉降罐1内的物料。
49.作为优选的,所述左腔室对应的罐体侧壁上设有玻璃板液位计2,以观察到溶剂回收情况。
50.作为优选的,所述倾析器16由前低后高的支腿38固定支撑。
51.作为优选的,所述第二连接管路24上设有视镜35。视镜35用于观测第二连接管路24内的油相含量。
52.作为优选的,所述污水输出管路22上设有向上弯折的凸起管段36作为液封。
53.作为优选的,所述憎水膜26为疏水ptfe膜,疏水ptfe膜可有效的分离溶剂(邻苯二甲酸二丁酯dbp)和残留在溶剂中的废水。
54.为了易于说明,实施例中使用了诸如“上”、“下”、“左”、“右”等空间相对术语,用于说明图中示出的一个元件或特征相对于另一个元件或特征的关系。应该理解的是,除了图中示出的方位之外,空间术语意在于包括装置在使用或操作中的不同方位。例如,如果图中
的装置被倒置,被叙述为位于其他元件或特征“下”的元件将定位在其他元件或特征“上”。因此,示例性术语“下”可以包含上和下方位两者。装置可以以其他方式定位(旋转90度或位于其他方位),这里所用的空间相对说明可相应地解释。
55.而且,诸如“第一”和“第二”等之类的关系术语仅仅用来将一个与另一个具有相同名称的部件区分开来,而不一定要求或者暗示这些部件之间存在任何这种实际的关系或者顺序。
56.以上所述仅是本实用新型的优选实施方式,应当指出的是,对于本技术领域的普通技术人员来说,在不脱离本实用新型原理的前提下,还可以做出若干改进和润饰,这些改进和润饰也应视为本实用新型的保护范围。