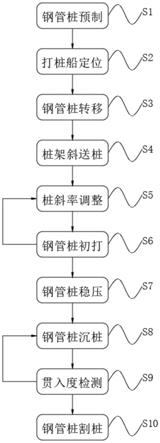
1.本发明涉及海上打桩施工技术领域,尤其涉及一种海上承台超长斜嵌岩桩的沉桩施工工艺。
背景技术:
2.在海上进行平台作业,需要将平台基础打入海水以下土层中。相比于陆地施工,海上桩基的土层上方存在海水压力作用,使土体的密实度较高,且其中存在较强的应力场,所以海上混凝土管桩沉桩更加困难。砂土表面粗糙,高应力场下会在预制桩沉桩过程中产生很大的摩擦阻力,故这种问题在砂土层中体现的更为明显。因此,海上桩基一般采用钢桩,相比混凝土管桩可以尽量较小沉桩摩阻力。并且海上平台群桩基础桩基施工多采用具有承载力高、稳定性好等优点的斜桩群。
3.现有的超长斜嵌岩桩桩身长度大幅加长,使得桩身难以控制和沉桩作业,并且超长斜嵌岩桩的贯入度难以保证,影响到桩体的斜率和贯入度的准确性。
技术实现要素:
4.有鉴于此,有必要提供一种海上承台超长斜嵌岩桩的沉桩施工工艺,用以解决超长桩体的斜率和贯入度不准确的问题。
5.本发明提供一种海上承台超长斜嵌岩桩的沉桩施工工艺,所述施工工艺包括依次进行的以下步骤:
6.打桩船定位:运用gps定位系统根据起重机的主臂伸长量确定抛锚点,准确定位桩基位点;
7.钢管桩转移:打桩船上的起重机将水平安置的钢管桩从运桩船上转移到打桩船上,并利用桩架竖直安置钢管桩;
8.桩斜率调整:通过调整桩架改变钢管桩的斜率,使得钢管桩的斜率与设计斜率一致;
9.钢管桩初打:首先利用gps定位系统微调打桩船的位置使得钢管桩位于预设桩基位点的正上方,然后立即进行插打作业,插打完成后立即对钢管桩进行测试复核,确保钢管桩的位置和斜率与设计相一致;
10.钢管桩沉桩:打桩锤按照一定锤击频次不断击打钢管桩,使得钢管桩插入海底深处;
11.贯入度检测:检测钢管桩灌入海底泥土中的深度,确保钢管桩插入深度与预设贯入度一致。
12.进一步的,在钢管桩初打步骤中,当钢管桩的位置和斜率与设计不一致时,则拔出钢管桩返回到桩斜率调整步骤,直到钢管桩的位置和斜率与设计一致时,才能进入到下一步骤。
13.进一步的,在贯入度检测步骤中,当钢管桩插入深度与预设贯入度不一致时,则回
到钢管桩沉桩步骤,继续击打钢管桩,直到钢管桩插入深度与预设贯入度一致。
14.进一步的,所述施工工艺还包括钢管桩割桩步骤,钢管桩采用场内模块化预制,利用运桩船将钢管桩分段运输到施工区域,进行多段装配成钢管桩桩体,钢管桩割桩步骤在打桩船定位步骤之前进行。
15.进一步的,所述施工工艺还包括桩架斜送桩步骤,桩架斜送桩步骤在钢管桩转移步骤和桩斜率调整步骤之间进行,控制桩架后倾,使得钢管桩与海面呈锐角设置,打桩锤将钢管桩击打至水面以下;在桩架斜送桩步骤,打桩锤套接在钢管桩的顶上供于传递锤击力的长替打,直到将钢管桩击打至水面以下。
16.进一步的,所述施工工艺还包括钢管桩稳压步骤,钢管桩稳压步骤在钢管桩初打步骤和钢管桩沉桩步骤之间进行,锁定桩架的斜度且保持打桩船的位置不变,确保在施工过程中,钢管桩的插入点和斜率稳定不变。
17.进一步的,所述施工工艺还包括钢管桩割桩步骤,钢管桩割桩步骤在贯入度检测步骤后进行,按照同一标高,对多个钢管桩进行同步式整体割桩。
18.进一步的,在桩斜率调整步骤中,首先利用起重机调节桩架整体的斜率与设计斜率相对一致,再通过调节桩架的水平拉压杆,微调钢管桩的斜率至设计斜率。
19.进一步的,在钢管桩沉桩步骤中,沉桩时间严格控制在20min-30min以内,以防钢管桩的斜率和位置受到海浪的剧烈影响而发生大幅改变。
20.进一步的,所述施工工艺重复进行,对多个钢管桩进行沉桩施工且使多桩呈圆形分布在作业海域。
21.与现有技术相比,本发明具有的有益效果为:
22.本发明的一种海上承台超长斜嵌岩桩的沉桩施工工艺,采用贯入度和斜率的检测反馈机制,在校核发现,贯入度和斜率达不到设计要求时,就返回到在先步骤,重新调整贯入度和斜率直到达到设计要求,斜率的复核机制可以确保钢管桩以设定的斜率打入到海底,满足对应的设计标准,方便对承载平台的安装。贯入度的复核机制可以满足对钢管桩的支撑强度要求,避免因贯入度不达标而造成钢管桩的位移。
附图说明
23.此处所说明的附图用来提供对本发明的进一步理解,构成本技术的一部分,本发明的示意性实施例及其说明用于解释本发明,并不构成对本发明的不当限定。在附图中:
24.图1为本发明提供的一种海上承台超长斜嵌岩桩的沉桩施工工艺的施工操作图;
具体实施方式
25.下面结合附图来具体描述本发明的优选实施例,其中,附图构成本技术一部分,并与本发明的实施例一起用于阐释本发明的原理,并非用于限定本发明的范围。
26.请参阅图1,本实施例中的一种海上承台超长斜嵌岩桩的沉桩施工工艺,所述施工工艺包括依次进行的以下步骤:
27.s1钢管桩预制,一般采用q235钢板作为原材料,通过专业的切割机进行切割,由大功率的卷板机卷曲制成螺旋状,并通过自动焊接机焊接成圆筒状,焊缝要求经过x光损伤检测,确保焊接的质量。在完成焊接施工后,还需要在圆筒的表面进行相应的防腐蚀和防锈处
理,确保圆筒外壁能够接受海水的侵蚀。同时在每个圆筒的上下两端设置对接结构形成钢管桩模块化预制段,利用运桩船将钢管桩模块化预制段运输到施工海域,在运输船上现场对钢管桩模块化预制段进行上下对接组装,形成单根的钢管桩桩体。
28.s2打桩船定位,运用gps定位系统来调整打桩船在施工海域的确切位置,根据起重机的主臂伸长量确定抛锚点,准确定位桩基位点,确保每一根钢管桩都从预先设定的切入。在具体实施过程中,由于海上没有参考点,只能用gps定位,多个gps仪安装在起重机的主臂和桩架上,共同确保钢管桩的定位准确。
29.s3钢管桩转移:利用gps定位系统,保证打桩船与运桩船始终保持两米左右的安全距离停靠,将两套索具上端分别挂在起重机的两个主钩头上,下端挂在钢管桩上下吊耳上,为使钢管桩立直,上端索具加一吊梁;双钩同时起吊,将钢管桩吊离运桩船甲板面一定高度后,转动起重机臂架,将桩吊至预定桩基位点的上方,然后起升钢管桩上端钩头,下降钢管桩下端钩头,直至将钢管桩竖立,并将钢管桩慢慢吊入桩架中并锁定,待钢管桩初步稳定后,下降上吊点的主钩头,将主钩头降至限位架顶部位置,将吊索具从主钩头上解除,同时解除下吊点的吊索具。
30.s4桩架斜送桩,首先利用起重机调节桩架,使得竖直的钢管桩与海面呈锐角倾斜,打桩锤套接在钢管桩的顶上,传递锤击力的给钢管桩,直到将钢管桩击打至水面以下为止。在具体实施过程中,多个钢管桩均与海面呈锐角倾斜设置,多个钢管桩呈环形分布,钢管桩的上端朝内侧倾斜设置,且共同作用于将要设置的海上承台。
31.s5桩斜率调整,通过起重机带动桩架运动初步调节钢管桩的斜率,驱使钢管桩的斜率与设计斜率接近。然后,在通过微调位于桩架上的水平拉压杆,使得钢管桩的斜率与设计斜率基本一致。
32.s6钢管桩初打,首先利用gps定位系统微调打桩船的位置,重新校准打桩船上钢管桩的位置,使得钢管桩位于预设桩基位点的正上方,为了避免海上波浪的影响,立即进行插打作业,打桩锤敲击钢管桩,使得钢管桩的底部一部分进入到海底的泥土中。同时,对钢管桩的位置和斜率进行测试复核,确保钢管桩的位置和斜率与设计一致。如果钢管桩的位置和斜率与设计不一致出现了偏差,则利用起重机从海底泥土中拔出钢管桩,回到s5步骤,再次进行s5和s6步骤,重现调整钢管桩的斜率并进行钢管桩初打,直至钢管桩的位置和斜率与设计相一致。
33.s7钢管桩稳压,锁定桩架的斜度,并且使得打桩锤从上部抵压钢管桩,同时在gps系统的辅助下始终保持打桩船的相对位置不变,确保在施工过程中,钢管桩的插入点和斜率稳定不变。
34.s8钢管桩沉桩,沉桩初期,打桩锤采用小能量轻击钢管桩,每入泥10cm,检测一次钢管桩的斜率。在钢管桩入泥达到一定深度后,打桩锤采用大能量重击钢管桩,每入泥50cm检测一次钢管桩的斜率,直至将钢管桩沉至设计标高。在具体实施过程中,还需要严格控制沉桩时间,一般将沉桩时间控制在20min-30min以内,打桩船和钢管桩在海水中工作,容易受到海浪和潮汐的影响,当施工时间超过一定范围,钢管桩的斜率和位置将受到剧烈影响。在具体实施过程中,在钢管桩剩余最后10m的灌入量时,进行大能量重击,在这个过程中的锤击数小于1500击,优选小于800击,并且打桩锤的总锤击数不超过3000击。
35.s9贯入度检测,当钢管桩沉桩完成后,需要检测钢管桩灌入海底泥土中的深度,确
保钢管桩插入深度与预设贯入度一致。当当钢管桩插入深度与预设贯入度不一致时,则回到s8步骤,继续击打钢管桩,直到钢管桩插入深度与预设贯入度一致为止。
36.s10钢管桩割桩,将钢管桩突出水面的部分按照同一标高切割,对钢管桩标高以上部分进行同步式整体割桩,可以便于承台的安装。
37.所述施工工艺重复进行,对多个钢管桩进行沉桩施工且使多桩呈圆形分布在作业海域,多个钢管桩共同支撑承台。
38.以上所述,仅为本发明较佳的具体实施方式,但本发明的保护范围并不局限于此,任何熟悉本技术领域的技术人员在本发明揭露的技术范围内,可轻易想到的变化或替换,都应涵盖在本发明之内。