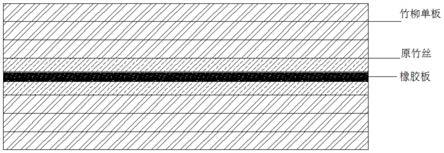
1.本发明属于建筑模板材料技术领域,更具体的涉及一种原竹丝/聚丙烯/橡胶板/竹柳单板的建筑模板制备方法。
背景技术:
2.我国竹资源丰富,竹林面积和竹材蓄积量居世界首位,且竹材强度大、韧性好具有良好的加工性能。竹柳是一种种植面积广,成材周期短,可利用沿海滩头盐碱地进行种植的经济林树种。近年来,为了提高竹材和速生材资源的利用率,开发了各种以竹、木材为基材的建筑复合板材。发明专利201110065040.0以竹材整张化组培加工而成的建筑材料,其竹材和木材都是单层。该板材厚度较薄,容易曲翘变形,抗弯强度较低,只适合建筑装饰用材,达不到建筑模板要求。发明专利200910309019.3以麻纤维和聚丙烯纤维热压成型的复合材料。该生产方式过程复杂,板材耐水性较差,力学强度低。发明专利201610241213.2为了解决麻纤维板材耐水性和强度问题,采用麻纤维和聚丙烯复合板进行加工。但板材厚度较薄,抗弯强度低,也不适合做建筑模板的加工方式。
技术实现要素:
3.本发明的目的是克服现有技术中的不足,提供一种原竹丝/聚丙烯/橡胶板/竹柳单板的建筑模板制备方法,本发明采用竹材原丝、竹柳单板和橡胶板进行多层交叉组胚,采用聚丙烯为胶合材料。板材耐水性大幅提高,板材厚度可以达12mm以上,力学性能优异,可作为建筑模板用材。
4.本发明是通过如下技术方案实现上述目的的,一种原竹丝/聚丙烯/橡胶板/竹柳单板的建筑模板制备方法,以橡胶板为中间层(一层),将原竹丝铺放在橡胶板上形成原竹丝层,橡胶板正反面进行对称铺装原竹丝层,然后在原竹丝表面正反表面对称铺装竹柳单板(各3层)形成板胚,各层之间涂刷聚丙烯;最后将铺装好的板胚,在热压机中进行热压得原竹丝/聚丙烯/橡胶板/竹柳单板的建筑模板。
5.优选地,所述方法包括如下步骤:
6.(1)新鲜或含水率大于15%的毛竹截成长毛竹材,加工成竹条,去除竹黄和竹青得原竹;
7.(2)将原竹进行高温蒸煮后,进行疏解,然后进行干燥得原竹丝;
8.(3)将竹柳木材旋切成宽单板,并烘干,并将单板胶带拼接成板材得竹柳单板;
9.(4)将聚丙烯加热到160℃以上,在拼接好的竹柳单板上均匀涂刷聚丙烯,再将原竹丝也涂刷上聚丙烯,并将涂胶后的原竹丝铺放在中间层的橡胶板上,正反面进行对称铺装;正反面各铺装原竹丝一层;在原竹丝层的正反面对称铺装竹柳单板(各3层)得板胚,最后准备闭合热压;
10.(5)将铺装好的板胚,在热压机中进行热压,热压成型后卸板、冷却得原竹丝/聚丙烯/橡胶板/竹柳单板建筑模板(即复合板材)。
11.优选地,步骤(1)具体步骤为:新鲜或含水率大于15%的毛竹按要求截成2440mm长毛竹材;通过一装有内铣刀和外刨削刀的装置,将毛竹的内节和外节同时去除,然后加工成竹条,去除竹黄和竹青得原竹;
12.优选地,步骤(2)具体步骤为:将原竹进行高温蒸煮处理1个小时后,进行疏解,将软化后的竹条疏解成1mm左右的竹丝,然后进行干燥得原竹丝;
13.优选地,步骤(3)具体步骤为:将直径为300mm及以上的竹柳木材旋切成1220mm宽单板,并烘干;并将单板胶带拼接成2440*1220mm板材得竹柳单板;
14.优选地,步骤(4)具体步骤为:将聚丙烯加热到160℃以上,在拼接好的竹柳木材单板上均匀涂刷聚丙烯,再将原竹丝也涂刷上聚丙烯,并将涂胶后的原竹丝铺放在中间层的橡胶板上,正反面进行对称铺装;板胚按照2440*1220mm标准规格铺装;正反面各铺装原竹丝一层,原竹丝厚度均为2mm;正反面竹柳单板各3层,厚度均为3mm;中间层的橡胶板一层为2mm,板胚总厚度为12
‑
13mm,最后,准备闭合热压;
15.优选地,步骤(5)具体步骤为:将铺装好的板胚,在热压机中进行热压,热压工艺:热压温度180
‑
210℃、热压时间19
‑
30min、热压压力2.5
‑
3.5mpa;热压成型后卸板、冷却得原竹丝/聚丙烯/橡胶板/竹柳单板建筑模板(即复合板材);进一步优选为热压温度200℃、热压时间30min、热压压力3.0mpa。
16.与现有技术相比,本发明具有如下优点:
17.通过本发明中提供的技术方案生产加工的建筑模板,产品厚度在12mm以上,通过增加单板层数,最厚可达20mm,其力学强度和吸水率都显著降低,厚度膨胀率也比同类产品优异。
附图说明
18.图1为本发明生产工艺流程图。
19.图2为原竹丝/聚丙烯/橡胶板/竹柳单板建筑模板的剖面结构图。
具体实施方式
20.一种原竹丝/聚丙烯/橡胶板/竹柳单板建筑模板制备方法
21.(1)新鲜或含水率大于15%的毛竹按要求截成2440mm长毛竹材;通过一装有内铣刀和外刨削刀的装置,将毛竹的内节和外节同时去除,然后加工成竹条,去除竹黄和竹青得原竹。
22.(2)将原竹进行高温蒸煮处理1个小时后,进行疏解,将软化后的竹条疏解成1mm左右的竹丝,然后进行干燥得原竹丝。
23.(3)将直径为300mm及以上的竹柳木材旋切成1220mm宽单板,并烘干;并将单板胶带拼接成2440*1220mm板材得竹柳单板。
24.(4)将聚丙烯加热到160℃以上,在拼接好的竹柳木材单板上均匀涂刷聚丙烯,再将原竹丝也涂刷上聚丙烯,并将涂胶后的原竹丝铺放在中间层的橡胶板上,正反面进行对称铺装。板胚按照2440*1220mm标准规格铺装;正反面各铺装原竹丝一层,原竹丝厚度均为2mm;原竹丝层正反面竹柳单板各3层,厚度均为3mm;中间层的橡胶板一层为2mm,板胚总厚度为12
‑
13mm,最后,准备闭合热压;
25.(5)将铺装好的板胚,在热压机中进行热压,热压工艺:热压温度200℃、热压时间30min、热压压力3.0mpa;热压成型后卸板、冷却得原竹丝/聚丙烯/橡胶板/竹柳单板建筑模板(即复合板材)。
26.对所生产的复合板材,采用gb/t 17657
‑
2013《人造板及饰面人造板理化性能试验方法》标准测定板材的胶合强度、静曲强度、弹性模量、冲击强度、吸水厚度膨胀率、吸水率进行检测。本发明在研发过程中分别研究了热压温度和热压时间对复合板材的影响,具体如下:
27.试验一:以热压温度分别为:180℃、190℃、200℃、210℃时,时间为30min,热压压力为3.0mpa进行热压,结果分别见表1和表2所示:
28.表1 试验结果表
[0029][0030]
表2 实验结果表
[0031][0032]
试验二:以热压时间分别为:19、22、25、30min时,热压温度为200℃,热压压力为3.0mpa进行热压,结果分别见表3和表4所示:
[0033]
表3 试验结果表
[0034][0035]
表4 试验结果表
[0036][0037]
实验结果表明:
[0038]
(1)温度是影响四项复合材料力学性能的主要因数,温度越高,物理力学性能越好,温度过高,表面单板会炭化影响复合材料的物理力学性能,热压温度越热压时间是相辅相成的,热压温度越高,需要的热压时间就越短。本发明以单因素试验探究四项复合材料一次成型的热压工艺,得出热压温度200℃、热压时间30min、热压压力3.0mpa为最佳热压工艺,热压后的板材厚度为8mm。
[0039]
(2)原竹丝/聚丙烯/橡胶板/竹柳单板四项复合材料的一次成型工艺下静曲强度为39.82mpa,弹性模量3756.29mpa,冲击强度22.17kj/m2,吸水厚度膨胀率4.16%,吸水率5.7%。
[0040]
上述实施例为本发明较佳的实施方式,但本发明的实施方式并不受上述实施例的限制,其他的任何未背离本发明的精神实质与原理下所作的改变、修饰、替代、组合、简化,均应为等效的置换方式,都包含在本发明的保护范围之内。