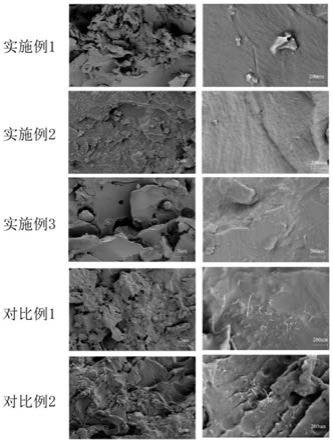
一种低voc含量、耐候耐盐雾腐蚀的涂料及其制备方法和应用
技术领域
1.本发明属于涂料生产技术领域,尤其涉及一种用于沿海区域、海洋环境下钢材的腐蚀防护的低锌粉、低voc含量的耐候耐盐雾腐蚀的涂料及其制备方法和应用。
背景技术:
2.中国是海陆兼备的大国,对海洋的探索从最初的鱼盐之利,到近些年大力提倡的发展海洋经济、创新海洋科技、保护海洋环境、建设海洋生态文明等一系列思路,对海洋的开发已经进入一个由浅入深的阶段。同时,随着科技水平的进步,对海洋资源的开发和利用已从浅海走向深海,甚至超深海。尤其在海洋能源、海底矿业、海洋养殖等工业产业方面。但是,恶劣的海洋环境所造成的严重的腐蚀结果直接影响到海洋工程结构钢等的使用安全,造成了巨大的经济损失和安全隐患。富锌重防腐涂层广泛应用于海洋装备的腐蚀防护,传统富锌重防腐涂层基于富含的锌粉的阴极保护机理为基材提供腐蚀保护,因此锌粉的含量与防腐蚀效果密切相关,但是干膜中高含量的锌粉(60~85%)也为富锌重防腐涂层带来诸多弊端:(1)锌粉含量高造成涂层致密性差,强度低;(2)锌粉含量高导致久置会引起漆料沉淀,在喷涂过程中锌粉易堵住喷枪,给贮存和施工带来不便;(3)锌粉含量高对环境存在一定的危害,造成严重的“锌污染”的问题;(4)锌资源的消耗大,有统计数据,按照现在的使用速度,锌将在40年内被消耗殆尽。
3.随着工业科技迅速发展,各国工业污染严重,二氧化碳大量排放,温室气体猛增,对世界环境、生物系统造成严重的破坏,随着各国人类对环境保护的意识,大力倡导保护地球生态环境下的可持续发展,在这一背景下,我国提出碳达峰和碳中和目标。其中最重要的就是对于涂料中溶剂型涂料中voc含量的限制。voc是挥发性有机化合物(volatile organic compound),从广义上讲是在常温常压下,任何在大气中可挥发的液体或固体有机化合物。美国环保局(epa)的定义:所有参与大气光化学反应的碳化合物,不包括co、co2、碳酸、金属碳化物或碳酸盐和碳酸铵。欧盟对voc的定义:在标准大气压(101.3kpa)下,初沸点低于或等于250℃的有机化合物。目前,主流的重防腐蚀涂料基本上以溶剂型涂料为主,相关标准规定(gb30981-2020),应用于建筑物和构筑物防护的金属基材防腐溶剂型无机车间底漆涂料的voc限量值不得超过720g/l,应用于建筑物和构筑物防护的金属基材防腐溶剂型有机车间底漆涂料的voc限量值不得超过650g/l,应用于集装箱和船舶的溶剂型喷涂类车间底漆要求voc含量不得超过700g/l,应用于集装箱和船舶的溶剂型辊涂类车间底漆要求voc含量不得超过700g/l,这些可以看出溶剂型重防腐涂料的voc含量依旧很高,长久使用会造成严重的环境破坏。还有一种为水性无机富锌涂层(其中干膜中金属锌含量在60-80%wt),根据相关标准(gb/t 38597-2020)中,应用于工业防护涂料合船舶涂料voc含量普遍不高于200~420g/l,但是水性涂料不能被使用在c5和cx环境下,并且高含量的锌粉对于环境也会造成破坏。因此对于恶劣环境下的腐蚀防护依然需要使用溶剂型重防腐涂料,溶剂型涂料的广泛使用,不仅涂料中溶剂含量高,涂料的施工工具须采用挥发性有机溶剂清洗,在这个过程中,不可避免地会对人体或环境造成危害,因此溶剂型低voc含量的重防腐
涂料的开发迫在眉睫。
技术实现要素:
4.有鉴于此,本发明的目的在于提供了一种低voc含量、耐候耐盐雾腐蚀的涂料及其制备方法和应用,克服了现有富锌重防腐涂层的问题,可减轻涂层质量,大幅度降低锌粉以及voc含量,进而降低对环境的污染危害。
5.为了实现以上目的,本发明提供了一种低voc含量、耐候耐盐雾腐蚀的涂料,按质量百分比计,包含如下组分:混合树脂30~50%;锌粉10~30%;碳纳米材料0.2-1.5%;填料10~30%;助剂0.5~3%以及溶剂10~20%。
6.进一步地,其中所述涂料的voc含量不高于120g/l。
7.进一步地,其中所述混合树脂包括质量比为:(1~3):(1~3):(0.5~1.5):(1~3)的氢化环氧树脂、聚酰胺固化剂、改性液体聚硫橡胶以及有机硅树脂;其中,所述氢化环氧树脂的型号为ep-4080e,其环氧当量为200~230g/eq,粘度为1500~3000mpa.s/25℃;所述聚酰胺固化剂的胺值200
±
20(mgkoh/g),粘度为2000~4000mpa.s;所述液体聚硫橡胶型号为jyl-121,分子量为800~6000;所述的有机硅树脂的型号为me-8750,粘度为1000~2500mpa.s/25℃。
8.进一步地,其中所述锌粉为金属锌含量是99%的一级锌粉(gb/t6890-2012),粒径为30μm。
9.进一步地,其中所述碳纳米材料为碳纳米管、石墨烯或富勒烯。
10.进一步地,其中所述碳纳米管是纯度大于95%,外径为8~15nm,内径为3~5nm,长度为15~30μm的多壁碳纳米管。
11.进一步地,其中所述石墨烯是纯度大于98%,厚度为3.4~8nm,片层直径为5~50μm,层数为5~10层的多层石墨烯。
12.进一步地,其中所述富勒烯是纯度为98%的c60/c70混合物,其中c60占80%。
13.进一步地,其中所述填料包括钛粉、磷铁粉、铝合金粉、不锈钢粉和疏水二氧化硅中的至少一种。
14.进一步地,其中所述填料由钛粉、磷铁粉、铝合金粉、不锈钢粉和疏水二氧化硅组成,五者之间的质量比为:(0.5~2):(0.5~2):(0.5~2):(0.5~2):(0.5~2)。
15.进一步地,其中所述溶剂为丁基缩水甘油醚和二甲苯的混合溶剂,其体积比为(1~3):(2~5)。
16.为了实现以上目的,本发明还提供了一种低voc含量、耐候耐盐雾腐蚀的涂料的制备方法,包括以下步骤:
17.(1)将配方量的锌粉、碳纳米材料、填料以及助剂加入溶剂中,以1000~2000r/min的转速高速搅拌20~40分钟,得到分散均匀的基料;
18.(2)将配方量的混合树脂和步骤(1)中的基料混合,密封后通入高纯氮气,球磨10~12小时,得到分散均匀的第一浆料;
19.(3)将步骤(2)中的第一浆料加入与环氧树脂质量比1:1的聚酰胺固化剂,以1000~2000r/min的转速高速搅拌20~40分钟,得到分散均匀的第二浆料,即可得到所述涂料。
20.进一步地,其中步骤(2)中,所述混合树脂通过以下步骤制得:将质量比为:(1~
3):(0.5~1.5):(1~3)的氢化环氧树脂、改性液体聚硫橡胶以及有机硅树脂混合,以1000~2000r/min的转速高速搅拌20~40分钟,分散均匀,即得到所述混合树脂。
21.进一步地,其中所述改性液体聚硫橡胶通过以下步骤制得:将液体聚硫橡胶、偶联剂、二甲苯按质量比(12~20):(9~15):(30~35)混合均匀,在高纯氮气的环境下持续搅拌并升温到120℃,反应24~36小时,得到透明的粘稠状液体产物,石油醚萃取,收集下层粘稠液体,即可得到所述改性液体聚硫橡胶。
22.为了实现以上目的,本发明还提供了一种低voc含量、耐候耐盐雾腐蚀的涂层的制备方法,包括以下步骤:
23.将上述的涂料采用刷涂工艺,涂敷于基板上,室温下自然放置,完全固化后即可得到所述低voc含量、耐候耐盐雾腐蚀的涂层;其中,干燥环境的温度为25~40℃;干燥环境的湿度为85%或以下。
24.为了实现以上目的,本发明还提供了一种低voc含量、耐候耐盐雾腐蚀的涂层,其锌粉含量低于30wt%,voc含量不高于120克/升;所述涂层通过上述的方法制得。
25.本发明采用氢化环氧树脂来增加涂料的耐候性,但是环氧树脂中存在的苯环以及交联密度高等导致的固化后涂层脆性大、附着力差等缺点,因此加入聚硫橡胶来增加涂层的弹性、提升涂层的附着力;使得最终制备的涂料中的锌粉含量低于30wt%,voc含量不高于120克/升,具有优异的耐候耐盐雾腐蚀性能,同时对于钢铁基材具有优异的附着力,可满足用于c5和cx环境下的钢材的腐蚀防护涂层。
26.相比于现有技术,本发明所述的低voc含量、耐候耐盐雾腐蚀的涂料及其制备方法和应用具有以下有益效果:
27.本发明所提供的涂料,其在固化后得到的涂层对钢材的保护作用可达到富锌涂层的腐蚀防护性能,为钢材提供有效的阴极保护,并且与钢材具有优异的附着力(钢材基底附着力达到10mpa),同时涂料的voc含量低于120克/升。
28.本发明所提供的涂料,其采用高纯度、低含量锌粉,极大减少对海洋环境的污染,并且具有优异的耐盐雾腐蚀、老化和干湿交替变化的性能,适用于对于耐腐蚀和耐候性要求高的沿海区域以及海洋环境下钢材使用场所,具有广泛的应用前景。
29.本发明所提供的涂料,其锌粉含量低于30wt%,voc含量不高于120克/升,具有优异的耐候耐盐雾腐蚀性能,同时对于钢铁基材具有优异的附着力,可满足用于c5和cx环境下的钢材的腐蚀防护涂层领域。
附图说明
30.图1为本发明实施例1-3的固化后的低voc含量、耐候耐盐雾腐蚀的涂层及对比例1-2的涂层的sem形貌图;
31.图2为本发明实施例1-3的固化后的低voc含量、耐候耐盐雾腐蚀的涂层及对比例1-2的涂层的电化学极化曲线图;
32.图3为本发明实施例1-3的固化后的低voc含量、耐候耐盐雾腐蚀的涂层及对比例1-2的涂层的电化学交流阻抗图;
33.图4为本发明实施例1-3的固化后的低voc含量、耐候耐盐雾腐蚀的涂层及对比例1-2的涂层的耐盐雾腐蚀效果图。
具体实施方式
34.为了更进一步阐述本发明为达成预期发明目的所采取的技术手段及功效,以下结合较佳实施例进行说明。下列实施例中未注明具体条件的实验方法,按照常规方法和条件,或按照商品说明书选择。以下材料或试剂,如非特别说明,均为市购。
35.本发明提供了一种低voc含量、耐候耐盐雾腐蚀的涂料,包含混合树脂、锌粉、碳纳米材料、填料、助剂以及溶剂;选用混合树脂可改善单一树脂材料的缺点,改善单一涂料附着力低、脆性大、耐候、耐腐蚀性能不足等缺陷,提高涂料的强度、耐候耐盐雾腐蚀性能以及附着力,锌粉提高涂料的耐盐雾腐蚀性能,对基体材料起到阴极保护能力,填料的加入可以降低成本、降低锌含量,提高涂料的硬度及耐候、耐腐蚀性能,再通过加入碳材料,提高加入的填料与混合树脂间的结合力,提高涂料的致密性,提高涂料的硬度及耐侯、耐腐蚀性能,防止填料的加入使得涂料致密性降低带来的问题,助剂与混合溶剂使得各组分更容易均匀分散制备涂料,降低浆料的粘度,使得涂料更容易涂膜固化,便于制备均匀,平整的耐候、耐盐雾腐蚀涂层。考虑到上述各种因素,所述涂料按照质量百分比计可以包含如下组分:混合树脂30~50%;锌粉10~30%;碳纳米材料0.2-1.5%;填料10~30%;助剂0.5~3%以及溶剂10~20%。
36.在本发明的一些实施方案中,所述混合树脂可以为氢化环氧树脂、聚酰胺固化剂、改性液体聚硫橡胶和有机硅树脂四种树脂以质量比为:(1~3):(1~3):(0.5~1.5):(1~3)混合的混合物;由于四种树脂相互改善树脂之间的耐候、耐腐蚀性能,固化后树脂的脆性大,附着力等问题,若四种树脂的质量比低于下限值或高于上限值会导致混合树脂的粘度不适宜、混合树脂固化后的强度、附着力,涂层的脆性等性能不佳,为此,三种树脂的优选质量比选择为:(2~2.5):(2~2.5):(1~1.2):(1.5~2),这样优选后使得树脂粘度更适中,涂料的耐候耐盐雾腐蚀性能更好。
37.在此处需要说明的是,所述聚酰胺固化剂可与氢化环氧树脂发生反应交联,使得树脂固化;通过改性聚硫橡胶的加入引入柔性基团,可避免氢化环氧树脂固化后涂层内部应力集中导致涂层力学性能降低、涂层脆的特性;有机硅树脂加入增加涂层的弹性,改善涂层的耐候性能,同时改性聚硫橡胶可改善有机硅树脂和氢化环氧树脂对基体材料的附着性能,四种树脂相互协同改善,使得混合树脂具有较优异的耐候耐腐蚀性能以及对基板材料的优异的附着力。
38.在上述实施例中,所述氢化环氧树脂的型号为ep-4080e,其环氧当量为200~230g/eq,粘度为1500~3000mpa.s/25℃,选用氢化环氧树脂可提高涂料的耐候性;所述聚酰胺固化剂的胺值200
±
20(mgkoh/g),粘度为2000~4000mpa.s,其主要作用是为了固化氢化环氧树脂;所述液体聚硫橡胶的型号为jyl-121,分子量为800~6000,选用聚硫橡胶可提高涂料的弹性以及附着力;所述有机硅树脂的型号为me-8750,粘度为1000~2500mpa.s/25℃,选用有机硅树脂可降低涂料表面能,提高涂料的耐候耐盐雾腐蚀性能。
39.在本发明的一些实施方案中,所述填料为钛粉、磷铁粉、铝合金粉、不锈钢粉和疏水二氧化硅以质量比为:(0.5~2):(0.5~2):(0.5~2):(0.5~2):(0.5~2)均匀混合分散的混合物,若五种组分的质量比低于下限值会使得作用效果不明显,不能限制提高涂料的强度、硬度、附着力及耐腐蚀性能等;高于上限值会使得涂料中金属颗粒过多,导致涂料粘度过大,致密性差,不成膜,开裂等问题。为了提高涂料的耐候性和耐腐蚀性能,所述粉、磷
铁粉、铝合金粉、不锈钢粉、疏水二氧化硅的质量比优选为(0.8~1):(1~1.3):(1.5~1.8):(1.5~1.8):(0.8~1)。
40.在本发明的一些实施方案中,所述溶剂为丁基缩水甘油醚和二甲苯以体积比为(1~3):(2~5)的混合溶剂,若丁基缩水甘油醚和二甲苯二者的体积比低于下限值会使得混合浆料中锌粉、填料等不易分散,浆料粘度大,不易涂膜造成涂料开裂、性能降低等;高于上限值会使得浆料粘度过低,附着力降低,voc含量上升,长期使用对环境造成污染。另,前述的体积比优选为(2~2.5):(3~3.5),这样优选后混合溶剂的挥发速度合适,固化后的涂层平整均一。
41.在本发明的一些实施方案中,所述氢化环氧树脂、改性液体聚硫橡胶、有机硅树脂三者的质量比为:(1~3):(0.5~1.5):(1~3),由于三种树脂相互改善树脂之间的耐候、耐腐蚀性能,改善单一树脂固化后树脂的脆性大,附着力等问题,若三种树脂的质量比低于下限值或高于上限值会导致混合树脂的粘度不适宜、混合树脂固化后的强度、附着力,涂层的脆性等性能不佳,优选后使得混合树脂粘度更适中,固化后的涂层附着力,弹性等更好,涂料的耐候耐盐雾腐蚀性能更好。优选的质量比为:(2~2.5):(1~1.2):(1.5~2),这样优选后使得树脂粘度更适中,涂料的耐侯耐盐雾腐蚀性能更好。
42.在本发明的一些实施方案中,所述的锌粉可以为锌含量大于99%的一级锌粉,粒径约为30μm,作为涂料中重要的腐蚀防护组分,对基体材料起到阴极保护左右,高纯度的锌粉保证优异的保护能力,粒径过低会导致锌粉的团聚,制备过程分散困难,且增加成本;粒径较大,无法均匀的分散在混合树脂中,导致耐腐蚀性能不稳定,或者需要增加锌粉含量才能是大粒径的锌粉均匀分散;因此合适的粒径粒径有利于锌粉均匀分散在涂料中,同时降低锌粉含量,使得涂料耐腐蚀性能更好。
43.在本发明的一些实施方案中,所述碳纳米材料可以为碳纳米管、石墨烯或富勒烯碳材料,其中碳纳米管是纯度大于95%,外径为8~15nm,内径为3~5nm,长度为15~30μm的多壁碳纳米管;石墨烯是纯度大于98%,厚度为3.4~8nm,片层直径为5~50μm,层数5~10层的多层石墨烯;富勒烯是纯度为98%的c60/c70混合物,其中c60约占80%,这样可以提高涂料的硬度以及耐候耐盐雾腐蚀性能。
44.经测试结果得知,所述涂料的体积固含量不小于95%,voc含量不高于120g/l。
45.本发明还提供了一种低voc含量、耐候耐盐雾腐蚀的涂料的制备方法,包括以下步骤:
46.(1)将配方量的氢化环氧树脂、改性液体聚硫橡胶以及有机硅树脂混合,以1000~2000r/min转速高速搅拌20~40分钟,得到分散均匀的混合树脂;前述的转速、时间优选为1500r/min、30min,这样优选后的分散效果好,时间短;
47.(2)将配方量的锌粉、碳纳米材料、填料以及助剂加入溶剂中,以1000~2000r/min转速高速搅拌20~40分钟,得到分散均匀的基料;前述的转速、时间优选为1500r/min、30min,这样优选后的分散效果好,时间短;
48.(3)将步骤(1)中的混合树脂和步骤(2)中的基料加入提前放入球磨球的球磨罐,球磨球为粒径15mm的球磨球,球磨球用量约占球磨罐体积的三分之二,密封后通入纯度大于99.999%的高纯氮气,使得球磨罐内处于氮气氛围,这样可以防止金属粉体氧化,在球磨机中球磨10~12小时,得到分散均匀的第一浆料;
49.(4)将步骤(3)中的第一浆料加入与氢化环氧树脂质量比(1~1.5):(1~1.5)(优选的质量比为1:1,这样优选后的固化时间合适,涂层强度更好)的聚酰胺固化剂,以1000~2000r/min转速高速搅拌20~40分钟,最终得到均匀分散的第二浆料,即可得到所述涂料;前述的转速、时间优选为1500r/min、30min,这样优选后的分散效果好,时间短。
50.本发明还提供了一种低voc含量、耐候耐盐雾腐蚀的涂层的制备方法,包括以下步骤:
51.将上述的涂料采用刷涂工艺,涂敷于基板上,室温下自然放置,完全固化后即可得到所述低voc含量、耐候耐盐雾腐蚀的涂层;其中,所述自然放置的温度为25~40℃;自然放置的湿度为85%或以下。
52.本发明还提供了一种低voc含量、耐候耐盐雾腐蚀的涂层,其锌粉含量低于30%,voc含量不高于120克/升;所述涂层通过上述的方法制得。
53.上述低voc含量、耐候耐盐雾腐蚀的涂层与钢材具有良好的附着力并且具有优异的耐盐雾、老化和干湿交替变化的性能。
54.以下结合具体实施例进行进一步说明。
55.实施例1
56.本实施例提供了一种低voc含量、耐候耐盐雾腐蚀的涂料,其具体配方如表1所示。
57.表1
[0058][0059]
上述涂料的制备方法,包括以下步骤:
[0060]
(1)将配方量的氢化环氧树脂、改性液体聚硫橡胶以及有机硅树脂混合,以1500r/min的转速高速搅拌30分钟,得到分散均匀的第一基料;
[0061]
(2)将配方量的锌粉、石墨烯、钛粉、磷铁粉、铝合金粉、不锈钢粉、疏水二氧化硅以及分散剂加入配方量的溶剂(丁基缩水甘油醚和二甲苯的质量比为1:1)中进行分散混合,以1500r/min转速高速搅拌30分钟,得到分散均匀的第二基料;
[0062]
(3)将步骤(1)中的第一基料和步骤(2)中的第二基料加入提前放入球磨球的球磨罐,球磨球为粒径15mm的球磨球,球磨球用量约占球磨罐体积的三分之二,密封后通入纯度大于99.999%的高纯氮气,使得球磨罐内处于氮气氛围,这样可以防止金属粉体氧化,在球磨机中球磨12小时,得到分散均匀的第一浆料;
[0063]
(4)将步骤(3)中的第一浆料加入与氢化环氧树脂质量比1:1的聚酰胺固化剂,以1500r/min的转速高速搅拌30分钟,得到均匀分散的第二浆料,即可得到所述涂料。
[0064]
将上述的涂料采用刷涂工艺,涂敷于基板上,室温下自然放置7天后即可得到低
voc含量、耐候耐盐雾腐蚀的涂层;其中,自然放置的温度为30℃;自然放置的湿度为50%。
[0065]
实施例2
[0066]
本实施例提供了一种低voc含量、耐候耐盐雾腐蚀的涂料,其具体配方如表2所示。
[0067]
表2
[0068][0069][0070]
上述涂料的制备方法,包括以下步骤:
[0071]
(1)将配方量的氢化环氧树脂、改性液体聚硫橡胶以及有机硅树脂混合,以1500r/min转速高速搅拌30分钟,得到分散均匀的第一基料;
[0072]
(2)将配方量的锌粉、碳纳米管、钛粉、磷铁粉、铝合金粉、不锈钢粉、疏水二氧化硅以及分散剂加入配方量的溶剂(丁基缩水甘油醚和二甲苯的质量比为1:1)中进行分散混合,以1500r/min转速高速搅拌30分钟,得到分散均匀的第二基料;
[0073]
(3)将步骤(1)中的第一基料和步骤(2)中的第二基料加入提前放入球磨球的球磨罐,球磨球为粒径15mm的球磨球,球磨球用量约占球磨罐体积的三分之二,密封后通入纯度大于99.999%的高纯氮气,使得球磨罐内处于氮气氛围,这样可以防止金属粉体氧化,在球
磨机中球磨12小时,得到分散均匀的第一浆料;
[0074]
(4)将步骤(3)中的第一浆料加入与氢化环氧树脂质量比1:1的聚酰胺固化剂,以1500r/min转速高速搅拌30分钟,得到均匀分散的第二浆料,即可得到所述涂料。
[0075]
将上述的涂料采用刷涂工艺,涂敷于基板上,室温下自然放置7天后即可得到低voc含量、耐候耐盐雾腐蚀的涂层;其中,自然放置的温度为30℃;干燥环境的湿度为50%。
[0076]
实施例3
[0077]
本实施例提供了一种低voc含量、耐候耐盐雾腐蚀的涂料,其具体配方如表3所示。
[0078]
表3
[0079][0080]
上述涂料的制备方法,包括以下步骤:
[0081]
(1)将配方量的氢化环氧树脂、改性液体聚硫橡胶以及有机硅树脂混合,以1500r/min转速高速搅拌30分钟,得到分散均匀的第一基料;
[0082]
(2)将配方量的锌粉、富勒烯、钛粉、磷铁粉、铝合金粉、不锈钢粉、疏水二氧化硅以及分散剂加入配方量的溶剂(丁基缩水甘油醚和二甲苯的质量比为1:1)中进行分散混合,
以1500r/min转速高速搅拌30分钟,得到分散均匀的第二基料;
[0083]
(3)将步骤(1)中的第一基料和步骤(2)中的第二基料加入提前放入球磨球的球磨罐,球磨球为粒径15mm的球磨球,球磨球用量约占球磨罐体积的三分之二,密封后通入纯度大于99.999%的高纯氮气,使得球磨罐内处于氮气氛围,这样可以防止金属粉体氧化,在球磨机中球磨12小时,得到分散均匀的第一浆料;
[0084]
(4)将步骤(3)中的第一浆料加入与氢化环氧树脂质量比1:1的聚酰胺固化剂,以1500r/min转速高速搅拌30分钟,得到均匀分散的第二浆料,即可得到所述涂料。
[0085]
将上述的涂料采用刷涂工艺,涂敷于基板上,室温下自然放置7天后即可得到低voc含量、耐候耐盐雾腐蚀的涂层;其中,自然放置的温度为30℃;干燥环境的湿度为50%。
[0086]
对比例1
[0087]
本对比例提供了一种低voc含量、耐候耐盐雾腐蚀的涂料,其具体配方如表4所示。
[0088]
表4
[0089][0090][0091]
上述涂料的制备方法,包括以下步骤:
[0092]
(1)将配方量的氢化环氧树脂、改性液体聚硫橡胶以及有机硅树脂混合,以1500r/min转速高速搅拌30分钟,得到分散均匀的第一基料;
[0093]
(2)将配方量的锌粉、富勒烯、钛粉、磷铁粉、铝合金粉、不锈钢粉、疏水二氧化硅以及分散剂加入配方量的溶剂(丁基缩水甘油醚和二甲苯的质量比为1:1)中进行分散混合,以1500r/min转速高速搅拌30分钟,得到分散均匀的第二基料;
[0094]
(3)将步骤(1)中的第一基料和步骤(2)中的第二基料加入提前放入球磨球的球磨罐,球磨球为粒径15mm的球磨球,球磨球用量约占球磨罐体积的三分之二,密封后通入纯度大于99.999%的高纯氮气,使得球磨罐内处于氮气氛围,这样可以防止金属粉体氧化,在球磨机中球磨12小时,得到分散均匀的第一浆料;
[0095]
(4)将步骤(3)中的第一浆料加入与氢化环氧树脂质量比1:1的聚酰胺固化剂,以1500r/min转速高速搅拌30分钟,得到均匀分散的第二浆料,即可得到所述涂料。
[0096]
将上述的涂料采用刷涂工艺,涂敷于基板上,室温下自然放置7天后即可得到低voc含量、耐候耐盐雾腐蚀的涂层;其中,自然放置的温度为30℃;干燥环境的湿度为50%。
[0097]
对比例2
[0098]
本对比例提供了一种低voc含量、耐候耐盐雾腐蚀的涂料,其具体配方如表5所示。
[0099]
表5
[0100][0101]
上述涂料的制备方法,包括以下步骤:
[0102]
(1)将配方量的氢化环氧树脂、改性液体聚硫橡胶以及有机硅树脂混合,以1500r/min转速高速搅拌30分钟,得到分散均匀的第一基料;
[0103]
(2)将配方量的锌粉、富勒烯、钛粉、磷铁粉、铝合金粉、不锈钢粉、疏水二氧化硅以及分散剂加入配方量的溶剂(丁基缩水甘油醚和二甲苯的质量比为1:1)中进行分散混合,以1500r/min转速高速搅拌30分钟,得到分散均匀的第二基料;
[0104]
(3)将步骤(1)中的第一基料和步骤(2)中的第二基料加入提前放入球磨球的球磨罐,球磨球为粒径15mm的球磨球,球磨球用量约占球磨罐体积的三分之二,密封后通入纯度大于99.999%的高纯氮气,使得球磨罐内处于氮气氛围,这样可以防止金属粉体氧化,在球磨机中球磨12小时,得到分散均匀的第一浆料;
[0105]
(4)将步骤(3)中的第一浆料加入与氢化环氧树脂质量比1:1的聚酰胺固化剂,以1500r/min转速高速搅拌30分钟,得到均匀分散的第二浆料,即可得到所述涂料。
[0106]
将上述的涂料采用刷涂工艺,涂敷于基板上,室温下自然放置7天后即可得到低
voc含量、耐候耐盐雾腐蚀的涂层;其中,自然放置的温度为30℃;干燥环境的湿度为50%。
[0107]
采用以下测试方法对本发明实施例1-3所述的低voc含量、耐候耐盐雾腐蚀的涂层及对比例1-2的涂层进行测试,测试结果如表4所示。
[0108]
用傅立叶红外光谱(ft-ir)对涂层进行表征,测试条件为4000~400cm-1
,分辨率为4cm-1
。
[0109]
采用扫描电子显微镜(sem)对所述的低锌粉低voc含量、耐候耐盐雾腐蚀的涂层的表面形貌、断面形貌进行表征。
[0110]
所述的低voc含量、耐候耐盐雾腐蚀的涂层的附着力采用gb/t 5210为标准进行测试。
[0111]
所述的低voc含量、耐候耐盐雾腐蚀的涂层的耐盐雾腐蚀试验按照gb/t 10125为标准测试耐腐蚀性能。
[0112]
autolab电化学工作站等测试与分析仪器对所述低voc含量、耐候耐盐雾腐蚀的涂层进行电化学交流阻抗谱(eis)测试与极化曲线测试。
[0113]
表4
[0114][0115]
从表4的测试数据可以看出,本发明实施例1-3所制备的涂层具有优异的附着性能和耐盐雾腐蚀性能,而且在低voc含量的条件下涂层依然具有良好的其他性能,对比例1~2的锌粉含量大幅度降低至最低约5%所获得涂料的附着力等性能没有显著变化,但是耐候、耐盐雾腐蚀性能急剧降低,见图1-图4。
[0116]
从实施例1~3中,改性聚硫橡胶的加入引入柔性基团,可避免氢化环氧树脂固化后涂层内部应力集中导致涂层力学性能降低、涂层脆的特性,有机硅树脂加入增加涂层的弹性,改善涂层的耐候性能,同时改性聚硫橡胶可改善有机硅树脂和氢化环氧树脂对基体材料的附着性能,三种树脂相互协同改善,使得混合树脂具有较优异的耐候耐腐蚀性能以及对基体材料的优异的附着力。锌粉作为本涂层中重要的防腐蚀组分,防腐蚀机理是锌粉的存在提供对基体材料的阴极保护能力,而锌粉易氧化产生的稳定的钝化膜提供更进一步的防腐蚀保护。填料的加入一方面降低成本,另一方面降低锌粉的含量,防止高含量的锌粉在实际长期应用中对环境造成锌污染,破坏生态环境,同时填料的添加可提高树脂涂层的硬度强度以及耐盐雾腐蚀性能,通过加入碳材料增加树脂涂层与加入的填料之间的结合
力,提高涂料的致密性,防止填料的加入导致涂料的开裂等严重破坏。对比例1~2在保持其他组分不变的情况下,大幅度降低锌粉含量的条件下,所获得的涂料的强度、硬度、附着力等性能没有显著变化,但是耐腐蚀性能却急剧下降(见图4),电化学交流阻抗以及盐雾测试都表明涂料的耐腐蚀性能的降低,说明锌粉的含量对于涂层的腐蚀防护起着重要作用,因此这也说明常见的重防腐材料为何以富锌涂料(60~80%)为主,本发明在相比富锌防腐涂料大幅度降低含锌量(10~30%)的条件下,依旧具有优异的耐候、耐盐雾腐蚀性能。
[0117]
如图1~4所示,通过实施例1~3与降低锌粉含量的对比例1~2的测试结果进行分析,图1所示的涂层的sem图用于观察不同组分配方下涂层材料的致密性,防止涂层材料由于致密性问题导致的涂层材料失效的问题,在高分辨率下的sem图显示所有涂层均具有良好的致密性。图2显示了对实施例和对比例的极化曲线,实施例1~3的极化曲线显示出三种涂层都具有较低的腐蚀电流,说明实施例1~3具有良好的耐腐蚀性能,对于对比例1~2的结果显示,相比于实施例1-3具有更高的腐蚀电流,说明由于锌粉含量的显著降低,使得涂层材料的耐腐蚀性能下降,因为锌粉在涂层中均匀分布对基体提供了阴极保护能力,保护涂覆的材料不发生腐蚀。图3的电化学交流阻抗(eis)测试结果同样验证了改结果,eis结果显示实施例1-3的三种涂层在频率为0.01hz时都具有较高阻抗值,通常都用0.01hz时的阻抗值反映涂层材料的耐腐蚀性能,这说明本发明的涂层具有优异的防腐蚀性能,对于对比例1~2的结果显示,由于锌粉含量的显著下降,涂层的阻抗值也在逐渐降低,说明涂层的耐腐蚀性能逐渐下降。图4所示的盐雾测试结果值观的显示了实施例与对比例的耐盐雾腐蚀性能,实施例1-3的三种涂层在盐雾环境下具有优异的耐候、耐盐雾腐蚀性能,在经过1440小时的盐雾环境下的腐蚀,其表面没有发生明显的腐蚀扩散和,涂层材料也没有发生起泡等现象;对于对比例,由于锌粉含量的显著降低,涂层的耐腐蚀性能发生明显的骤降,经过360小时的测试就发生明显的腐蚀扩散现象,随后也出现涂层的起泡等严重的问题,这是由于锌粉含量过少导致对基体的阴极保护能力下降,防腐蚀性能降低,随后对涂层带来一系列严重的问题。可见本发明的涂料适合用于海边化工环境下的户外结构使用,也可用于其他对于耐腐蚀和耐候性要求高的海上风电钢结构或其他海洋结构上。
[0118]
综上,实施例1~3和对比例1~2的测试结果验证了本发明的制备原理以及各组分在涂料中的作用机理,盐雾测试表明了本发明的涂料具有优异的耐盐雾腐蚀性能,电化学交流阻抗(eis)测试结果显示,本发明的涂料具有优异的防腐蚀性能。
[0119]
以上所述,仅是本发明的较佳实施例而已,并非对本发明作任何形式上的限制,依据本发明的技术实质对以上实施例所作的任何简单修改、等同变化与修饰,均仍属于本发明技术方案的范围内。