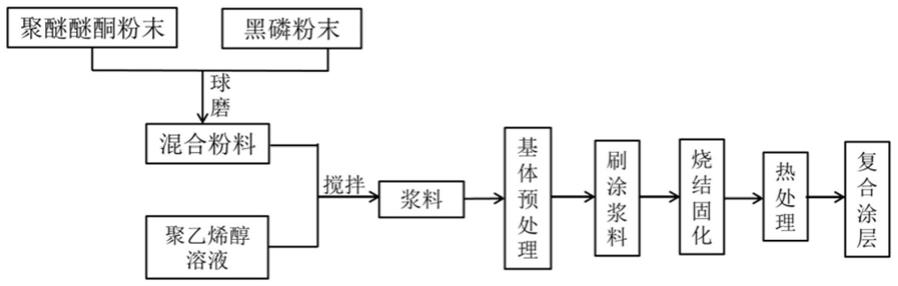
1.本发明属于固体自滑涂层技术领域,具体涉及一种聚醚醚酮/黑磷自润滑复合涂层、复合 材料及其制备方法。
背景技术:
2.轴承材质以铁基、铜基、铝基合金居多,摩擦系数较大,运行过程中易发生剧烈磨损,引 起零件变形、表面质量恶化以及额外的能量消耗,降低了系统的寿命和可靠性。传统的润滑油 润滑效果不足,且无法在高温、高压或水环境下服役,因此固体自润滑涂层的研究和应用近年 来得到快速的发展。高分子聚醚醚酮(peek)因其出色的自润滑性能、耐高温和机械性能被 称为“特种工程塑料”,同时是目前市场上性能最优异的涂料之一,其涂层制品广泛应用于工业 和制造业。
3.传统的聚醚醚酮涂层多采用火焰喷涂技术制备,喷涂过程中粉末需要在极短时间内完成从 熔化到附着于基体表面整个过程,涂料流动性不佳,空气来不及排出等因素使得涂层组织疏松, 结合力较差,机械性能和摩擦学性能不足。随着我国科技水平的高速发展,对机械零部件性能 和服役环境的要求也日益严苛,传统的聚醚醚酮涂层已不能满足机械加工要求,迫切需要研究 新工艺和新材料制备性能更为优异的聚醚醚酮基复合涂层。
技术实现要素:
4.为解决现有技术中存在的问题,本发明的目的是提供一种聚醚醚酮/黑磷自润滑复合涂层、 复合材料及其制备方法,以改善聚醚醚酮基复合涂层的润滑性能和磨损严重的问题。
5.本发明采用的技术方案如下:
6.一种聚醚醚酮/黑磷自润滑复合涂层的制备方法,包括如下过程:
7.将黑磷粉末、聚醚醚酮粉末和表面活性剂溶液混合制成的浆料涂覆于基体的表面,之后进 行烘干,在基体表面得到涂层粗制品;
8.对具有涂层粗制品的基体进行烧结固化以及热处理,在基体的表面形成所述聚醚醚酮/黑 磷自润滑复合涂层。
9.优选的,所述浆料的制备过程包括:将黑磷粉末与聚醚醚酮粉末进行球磨得到混合粉料; 将所述混合粉料倒入表面活性剂溶液中,充分搅拌配制成所述浆料。
10.优选的,制备所述浆料时,所述黑磷粉末的粒径不大于30μm,所述聚醚醚酮粉末的粒径 不大于20μm:
11.球磨时的球料比(10:1)-(20:1),大小球直径分别为10mm和5mm,球磨机转速为300-400 r/min,球磨时间2-5h。
12.优选的,所述混合粉料中,黑磷的质量百分含量为1%-6%。
13.优选的,所述表面活性剂溶液采用聚乙烯醇水溶液,聚乙烯醇的浓度范围 0.03g/ml-0.1g/ml;
14.将混合粉料与表面活性剂溶液按质量比(1:2)-(1:1.4)混合并搅拌30-50min制成所 述浆料;
15.当混合粉料中黑磷含量≥1wt.%且<2wt.%时,聚乙烯醇的浓度范围0.03g/ml-0.04g/mg;当 混合粉料中黑磷含量≥2wt.%且<4wt.%时,聚乙烯醇的浓度范围0.04g/ml-0.06g/ml;当混合粉 料中黑磷含量≥4wt.%且≤6wt.%时,聚乙烯醇的浓度范围0.06g/ml-0.1g/ml。
16.优选的,浆料在基体表面的涂覆厚度为200-400μm,所述聚醚醚酮/黑磷自润滑复合涂层 的厚度为40μm-120μm。
17.优选的,对具有涂层粗制品的基体进行烧结固化的过程包括:
18.将具有涂层粗制品的基体加热至390-410℃,保温10-30min后进行水淬,完成所述烧结 固化。
19.优选的,所述热处理过程包括:
20.烧结固化完成后,将涂层再次加热至240-270℃,保温10-30min后随炉冷却,在基体的 表面形成所述聚醚醚酮/黑磷自润滑复合涂层。
21.本发明还提供了一种聚醚醚酮/黑磷自润滑复合涂层,该聚醚醚酮/黑磷自润滑复合涂层通 过本发明如上所述的制备方法制得。
22.本发明还提供了一种复合材料包括基体和制备于所述基体表面的本发明如上所述的聚醚 醚酮/黑磷自润滑复合涂层。
23.本发明具有如下有益效果:
24.本发明聚醚醚酮/黑磷自润滑复合涂层的制备方法中,浆料中含有黑磷,通过黑磷能够有 效降低轴承运转时的摩擦系数,可显著降低低速、高速运转中机械零部件的磨损,提高了系统 的寿命和稳定性,提高经济效益。本发明通过涂覆的方法将涂覆于基体的表面黑磷粉末、聚醚 醚酮粉末和表面活性剂混合制成的浆料涂覆到基体表面,经烧结固化使涂料转变为致密的涂 层。所制备自润滑涂层与基体结合较好,硬度较高,可显著降低机械零部件在低速、高速运转 中的磨损,其制备工艺简单、涂层成分可控,可在航空、汽车、船舶等工业领域广泛应用。
附图说明
25.图1为本发明涂层聚醚醚酮/黑磷自润滑复合涂层的制备的工艺流程图。
26.图2(a)为本发明采用的黑磷(bp)的xrd图,图2(b)为本发明采用的黑磷的sem 图。
27.图3(a)为纯peek(聚醚醚酮)涂层sem图;图3(b)为本发明混合粉料中含有2wt.% bp时聚醚醚酮/黑磷自润滑复合涂层的sem图:图3(c)为本发明混合粉料中含有4wt.%bp 时聚醚醚酮/黑磷自润滑复合涂层的sem图。
28.图4为本发明中不同黑磷浓度的peek-bp复合涂层平均摩擦系数示意图。
29.图5(a)为纯peek涂层磨痕sem图;图5(b)为本发明混合粉料中含有2wt.%bp时 聚醚醚酮/黑磷自润滑复合涂层的磨痕sem图;图5(c)为本发明混合粉料中含有4wt.%bp 时聚醚醚酮/黑磷自润滑复合涂层的磨痕sem图。
具体实施方式
30.遵从上述技术方案,以下给出本发明的具体实施例,需要说明的是本发明并不局限于以下 具体实施例,凡在本技术技术方案基础上做的等同变换均落入本发明的保护范围。
31.如图1所示,本发明聚醚醚酮/黑磷自润滑复合涂层的制备方法,包括如下步骤:
32.步骤1,筛选粒径不大于20μm的聚醚醚酮粉末和粒径不大于30μm的黑磷粉末。
33.步骤2,将黑磷粉末和聚醚醚酮粉末球磨混粉,得到混合粉料,混合粉料中,黑磷粉末的 质量含量为1wt.%-6wt.%;球磨混料时:球料比为(10:1)-(20:1),大小球直径分别为10mm 和5mm,球磨时间为2-5h,球磨机转速为300-400r/min。
34.步骤3,将所述混合粉料置于烧杯中,并倒入聚乙烯醇(pva)的水溶液,搅拌30-50min, 配制成浆料。聚乙烯醇水溶液中,聚乙烯醇的浓度范围0.03g/ml-0.1g/ml;混合粉料与表面活 性剂溶液按质量比(1:2)-(1:1.4)混合;
35.当混合粉料中黑磷含量≥1wt.%且<2wt.%时,聚乙烯醇的浓度范围0.03g/ml-0.04g/mg;当 混合粉料中黑磷含量≥2wt.%且<4wt.%时,聚乙烯醇的浓度范围0.04g/ml-0.06g/ml;当混合粉 料中黑磷含量≥4wt.%且≤6wt.%时,聚乙烯醇的浓度范围0.06g/ml-0.1g/ml。
36.步骤4,基体选择不锈钢材质(基体零部件为产生往复滑动摩擦零部件,如轴承等),用 砂纸打磨除去基体表面的线切割痕迹,并用乙醇:丙酮=1:1溶液超声清洗2-3次,每次持续 20min,风干备用。
37.步骤5,将步骤3制备的浆料均匀刷涂在不锈钢基体上,涂料厚度为200-400μm。
38.步骤6,将基体和涂层一同置于马弗炉中,加热至390-410℃,保温10-30min后,淬入 冷水中冷却。
39.步骤7,对淬火得到的无定形涂层进行退火处理,退火加热温度240-270℃,保温10-30min 后随炉缓冷,在基体上制得厚度为40μm-120μm聚醚醚酮/黑磷自润滑复合涂层。
40.本发明拟采用浆料刷涂的方式,将黑磷颗粒引入聚醚醚酮,制备出聚醚醚酮/黑磷自润滑 复合涂层。本发明的难点和关键点在于浆料中各成分的配方比例,由于聚醚醚酮润湿性差以及 加入黑磷后异种颗粒间结合性差,选用聚乙烯醇(pva)作为表面活性剂,一方面解决由于聚 醚醚酮润湿性差导致的粉末团聚问题;另一方面将pva溶液作为粘接剂,解决了异种颗粒结 合性差的问题,使涂层在后续加热过程中不易开裂。但聚乙烯醇含量也不宜过高,过高会导致 浆料粘度过高,粉末分散性差,peek和bp难以分布均匀。
41.实施例1:
42.本实施例提供peek-1wt.%复合涂层,该涂层采用如下的制备方法制备:
43.(1)浆料配制:
44.1-1:筛选粒径不大于20μm的peek粉末。采用高能球磨法制备黑磷,筛选粒径不大于 30μm的黑磷粉末。
45.1-2:将黑磷和peek粉末按质量比1:99球磨混粉,球磨条件为:球料比为10:1,不锈钢 小球直径分别为10mm和5mm,球磨时间4h,球磨机转速为350r/min。得到黑磷含量为1wt.% 的混合粉料。
46.1-3:添加剂的准备:选择醇解度为50%的pva作为表面活性剂,称量3.5g pva颗粒
溶 于100ml水中,加热到95℃-100℃并不断搅拌,待充分溶解后停止加热,冷却得到浓度为0.035 g/ml的pva溶液。
47.1-4:称量上述混合粉料2.1g置于烧杯中,并倒入3ml上述pva溶液,搅拌40min后得 到peek-1wt.%bp复合涂层浆料。
48.(2)刷涂浆料:基体块材质选择cr22nimo3n不锈钢,线切割成尺寸为的圆柱体, 用砂纸打磨除去表面的线切割痕迹,并用乙醇:丙酮=1:1溶液超声清洗2-3次,每次持续20 min,风干。用载玻片将上述浆料均匀刮涂到基体上,涂敷厚度约300μm,并用鼓风干燥箱烘 干。
49.(3)涂层固化:将基体和涂层一同置于马弗炉中,以5℃/min升温速率加热至400℃,保 温15min后淬入冷水中冷却。对得到的无定形涂层进行退火处理,退火工艺:以10℃/min升 温速率加热至260℃,保温20min后随炉缓冷。
50.制备得到的peek-1wt.%bp复合涂层厚度约80μm,表面光滑、组织致密均匀。使用维 氏显微硬度计测得其硬度为32.2hv。选用球-盘摩擦磨损试验仪,摩擦副为直径6mm的gcr15 球,待测涂层为旋转盘,载荷1n,转速200r/min,旋转直径12mm,时间30min。测得涂层 平均摩擦系数为0.1645。
51.实施例2:
52.本实施例提供peek-2wt.%复合涂层,该涂层采用如下的制备方法制备:
53.(1)浆料配制:
54.1-1:筛选粒径不大于20μm的peek粉末。采用高能球磨法制备黑磷,筛选粒径不大于 30μm的黑磷粉末。
55.1-2:将黑磷和peek粉末按质量比1:49球磨混粉,球磨条件为:球料比为10:1,不锈钢 小球直径分别为10mm和5mm,球磨时间4h,球磨机转速为350r/min。得到黑磷含量为2wt.% 的混合粉料。
56.1-3:添加剂的准备:选择醇解度为50%的pva作为表面活性剂,称量4g pva颗粒溶于100ml水中,加热到95℃-100℃并不断搅拌,待充分溶解后停止加热,冷却得到浓度为0.04g/ml 的pva溶液。
57.1-4:称量上述混合粉料2.1g置于烧杯中,并倒入4ml上述pva溶液,搅拌40min后得 到peek-2wt.%bp复合涂层浆料。
58.(2)刷涂浆料:基体块材质选择cr22nimo3n不锈钢,线切割成尺寸为的圆柱体, 用砂纸打磨除去表面的线切割痕迹,并用乙醇:丙酮=1:1溶液超声清洗2-3次,每次持续20 min,风干。用载玻片将上述浆料均匀刮涂到基体上,涂敷厚度约300μm,并用鼓风干燥箱烘 干。
59.(3)涂层固化:将基体和涂层一同置于马弗炉中,以5℃/min升温速率加热至400℃,保 温15min后淬入冷水中冷却。对得到的无定形涂层进行退火处理,退火工艺:以10℃/min升 温速率加热至260℃,保温20min后随炉缓冷。
60.制备得到的peek-2wt.%bp复合涂层厚度约80μm,表面光滑、组织致密均匀。使用维 氏显微硬度计测得其硬度为27.6hv。选用球-盘摩擦磨损试验仪,摩擦副为直径6mm的gcr15 球,待测涂层为旋转盘,载荷1n,转速200r/min,旋转直径12mm,时间30min。测得涂层 平均摩擦系数为0.1225。
61.实施例3:
62.本实施例提供peek-4wt.%复合涂层,该涂层采用如下的制备方法制备:
63.(1)浆料配制:
64.1-1:筛选粒径不大于20μm的peek粉末。采用高能球磨法制备黑磷,筛选粒径不大于 30μm的黑磷粉末。
65.1-2:将黑磷和peek粉末按质量比1:24球磨混粉,球磨条件为:球料比为10:1,不锈钢 小球直径分别为10mm和5mm,球磨时间4h,球磨机转速为350r/min。得到黑磷含量为4wt.% 的混合粉料。
66.1-3:添加剂的准备:选择醇解度为50%的pva作为表面活性剂,称量6g pva颗粒溶于 100ml水中,加热到95℃-100℃并不断搅拌,待充分溶解后停止加热,冷却得到浓度为0.06g/ml 的pva溶液。
67.1-4:称量上述混合粉料2.1g置于烧杯中,并倒入4ml上述pva溶液,搅拌40min后得 到peek-4wt.%bp复合涂层浆料。
68.(2)刷涂浆料:基体块材质选择cr22nimo3n不锈钢,线切割成尺寸为的圆柱体, 用砂纸打磨除去表面的线切割痕迹,并用乙醇:丙酮=1:1溶液超声清洗2-3次,每次持续20 min,风干。用载玻片将上述浆料均匀刮涂到基体上,涂敷厚度约300μm,并用鼓风干燥箱烘 干。
69.(3)涂层固化:将基体和涂层一同置于马弗炉中,以5℃/min升温速率加热至400℃,保 温15min后淬入冷水中冷却。对得到的无定形涂层进行退火处理,退火工艺:以10℃/min升 温速率加热至260℃,保温20min后随炉缓冷。
70.制备得到的peek-4wt.%bp复合涂层厚度约90μm,表面光滑、组织致密均匀。使用维 氏显微硬度计测得其硬度为21.1hv。选用球-盘摩擦磨损试验仪,摩擦副为直径6mm的gcr15 球,待测涂层为旋转盘,载荷1n,转速200r/min,旋转直径12mm,时间30min。测得涂层 平均摩擦系数为0.1143。
71.实施例4:
72.本实施例提供peek-6wt.%复合涂层,该涂层采用如下的制备方法制备:
73.(1)浆料配制:
74.1-1:筛选粒径不大于20μm的peek粉末。采用高能球磨法制备黑磷,筛选粒径不大于 30μm的黑磷粉末。
75.1-2:将黑磷和peek粉末按质量比3:47球磨混粉,球磨条件为:球料比为10:1,不锈钢 小球直径分别为10mm和5mm,球磨时间4h,球磨机转速为350r/min。得到黑磷含量为6wt.% 的混合粉料。
76.1-3:添加剂的准备:选择醇解度为50%的pva作为表面活性剂,称量7g pva颗粒溶于 100ml水中,加热到95℃-100℃并不断搅拌,待充分溶解后停止加热,冷却得到浓度为0.07g/ml 的pva溶液。
77.1-4:称量上述混合粉料2.1g置于烧杯中,并倒入4ml上述pva溶液,搅拌40min后得 到peek-6wt.%bp复合涂层浆料。
78.(2)刷涂浆料:基体块材质选择cr22nimo3n不锈钢,线切割成尺寸为的圆柱体, 用砂纸打磨除去表面的线切割痕迹,并用乙醇:丙酮=1:1溶液超声清洗2-3次,每次持
续20 min,风干。用载玻片将上述浆料均匀刮涂到基体上,涂敷厚度约300μm,并用鼓风干燥箱烘 干。
79.(3)涂层固化:将基体和涂层一同置于马弗炉中,以5℃/min升温速率加热至400℃,保 温15min后淬入冷水中冷却。对得到的无定形涂层进行退火处理,退火工艺:以10℃/min升 温速率加热至260℃,保温20min后随炉缓冷。
80.制备得到的peek-6wt.%bp复合涂层厚度约70μm,表面光滑、组织致密均匀。使用维 氏显微硬度计测得其硬度为18.2hv。选用球-盘摩擦磨损试验仪,摩擦副为直径6mm的gcr15 球,待测涂层为旋转盘,载荷1n,转速200r/min,旋转直径12mm,时间30min。测得涂层 平均摩擦系数为0.0951。
81.对比例1:纯peek涂层的摩擦性能:
82.(1)纯peek涂层的制备
83.筛选粒径不大于20μm的peek粉末。称量7g peek粉末置于烧杯中,并倒入9.5ml水、0.5ml浓度为0.03g/ml的pva溶液,搅拌40min后得到纯peek涂层浆料。用载玻片将上述 浆料均匀刮涂到不锈钢基体上,涂敷厚度约300μm,并用鼓风干燥箱烘干。将基体和涂层一同 置于马弗炉中,以5℃/min升温速率加热至400℃,保温15min后淬入冷水中冷却。对得到的 无定形涂层进行退火处理,退火工艺:以10℃/min升温速率加热至260℃,保温20min后随 炉缓冷。
84.(2)纯peek涂层的性能
85.制备得到的纯peek涂层厚度约70μm,表面光滑、组织致密均匀。使用维氏显微硬度计 测得其硬度为21.8hv。选用球-盘摩擦磨损试验仪,摩擦副为直径6mm的gcr15球,待测涂 层为旋转盘,载荷1n,转速200r/min,旋转直径12mm,时间30min。测得涂层平均摩擦系 数为0.2067。
86.将实施例1、实施例2、实施例3、实施例4和对比例1所述涂层的摩擦系数绘制成曲线, 如图4所示,复合涂层的摩擦系数随黑磷含量的增加而下降,添加了黑磷颗粒的peek/bp复 合涂层的减摩效果明显优于纯peek。
87.对实施例2、实施例3和对比例1的所述涂层的摩痕表面进行sem观察,如图5(a)~ 图5(c)所示,纯peek涂层磨痕宽度489.8μm,表面分布较深的犁沟,个别部位发生了撕 裂,磨损机理为严重的磨粒磨损;peek-2wt.%bp复合涂层磨痕宽度478.3μm,表面犁沟变 浅,磨粒磨损减弱;peek-2wt.%bp复合涂层磨痕宽度448.9μm,表面分布着浅而细小的犁 沟,表面较为光滑且没有裂纹,仅发生了轻微的磨粒磨损。因此,随着黑磷含量的提高,涂层 耐磨性能提高。
88.上述结果表明,将黑磷引入peek制备成peek-bp复合涂层能显著提高涂层的减磨耐磨 性能。将聚醚醚酮/黑磷复合涂层应用至滑动轴承或机械加工领域后,能够提高金属零部件表 面耐磨性能,保护基体,提高经济效益。
89.从上述可以看出,本发明的技术方案具有以下几个特点:(1)本发明的固体自润滑涂层, 创新性的引入了黑磷作为填料,有效降低了轴承运转时的摩擦系数,可显著降低低速、高速运 转中机械零部件的磨损,提高了系统的寿命和稳定性,提高经济效益。
90.(2)本发明的固体自润滑涂层,组织致密、硬度较高且稳定性好,可在高温、高压以及 海洋环境等恶劣工况下服役,应用范围广泛。
91.(3)本发明采用的制备工艺为浆料刷涂法,制备工艺简单,涂层成分可控,具有良好的 工业应用前景。