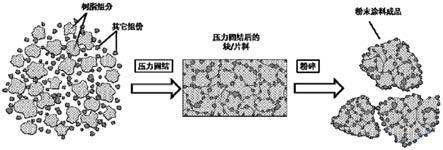
1.本发明涉及粉末涂料的制备领域,尤其涉及一种粉末涂料的制作工艺方法。
背景技术:
2.粉末涂料是一种由树脂、颜料、助剂、填料等组成的粉末状颗粒,粉末涂料以树脂为主要成膜物质,组料成分中可以包含一种或多种树脂。按其树脂性质,粉末涂料可分为热塑性粉末涂料和热固性粉末涂料。热塑性粉末涂料是由热塑性树脂、颜料、填料、增塑剂和稳定剂等成分组成的。热塑性粉末涂料按所使用的树脂可分为:聚乙烯、聚丙烯、丙烯酸树脂、聚酯、聚氯乙烯、氯化聚醚、聚苯硫醚、聚酰胺、纤维素、氟碳等树脂体系。热固性粉末涂料是由热固性树脂、固化剂、颜料、填料和助剂等组成。热固性粉末涂料按所使用的树脂可分为:环氧树脂、环氧-聚酯、聚酯、聚氨酯、丙烯酸树脂、氟树脂等树脂体系。
3.现有的粉末涂料加工工艺主要包括熔融挤出(或称为熔炼)和粉碎过程两个重要部分:熔融挤出是将经过预混合各组料成分(或称为原料组分)通过挤出机内的高温和高剪切力,使除树脂外的各组分材料充分分散于处于熔融状态的主体树脂中;粉碎过程是将完成熔炼并冷却至室温的挤出料破碎至具有目标粒径的粉末产品,理想状况下每个粉末颗粒均含有所有的各原料组分。在熔融挤出过程中,首先将树脂、固化剂(使用热固性树脂时)、颜料、助剂、填料等原料充分混合后,经挤出机在100℃以上进行熔融混炼、压辊冷却后,得到半成品片料;在粉碎过程中,将半成品片料放入空气分级磨(air classifying mill)或气流粉碎机(jet mill) 中进行破碎、分级并收集,收集到的颗粒经过100-180目筛网筛分后,得到中粒径 (d50)一般为25-45微米的成品粉末涂料。对热塑性粉末涂料,多数情况下需要采用冷冻粉碎工艺获得成品粉末涂料。
4.然而,使用“熔融挤出-粉碎”工艺制备粉末涂料时,因一些树脂熔融温度高,挤出温度也相应更高,熔融挤出这类树脂时,增加了挤出机的能耗;一些颜料、填料或助剂对挤出机有较强的磨损(如涂料增硬填料、富锌涂料里高比例的锌粉等),大幅度增加设备维护成本;对于一些韧性强的树脂(主要是热塑性树脂,如氟碳树脂、聚丙烯酸树脂等),经熔融挤出后,得到的半成品片料很难使用空气分级磨或气流粉碎机粉碎至理想粒径,常温下粉碎效率低或根本无法粉碎。部分厂家使用液氮粉碎的方法将熔融挤出的片料粉碎至理想粒径,但该方法液氮消耗量大,加工成本高昂。在加工一些难挤出、难粉碎的树脂时,或原料中含有磨损性材料时,一些制造商会使用将原材料直接干混的办法,避免挤出。但因为不同原料组分在喷涂过程中带电性、上粉率的不一致,会导致涂膜实际组分与配方组分不一致,无法大规模应用。
5.另一方面,与液体涂料相比,粉末涂料调色相对困难。粉末涂料因不含溶剂,在调色过程中无法直接在粉末涂料产品中直接干混加入颜料,每次调配新色都必须多次彻底清理设备并重复上述的熔融挤出和粉碎两个步骤,调色效率极低。为此,曾有一些公司及研发机构尝试“粉调粉”的方式来解决调色难的问题,即先通过熔融挤出法制成多种颜色的、含所有组分材料的基色粉(红色、黄色、蓝色、黑色、白色等),然后按照不同比例进行干混调
配,得到所需颜色的成品粉末涂料。这种方法避免了传统调色工艺中每次调色必须经过熔融挤出和粉碎的缺点,但因为每种基色粉的带电性不同,且相互间没有粘结吸附,在静电喷涂过程中,不同基色粉的上粉率会出现差异,导致涂膜色差。因此,“粉调粉”一直没有进入实际应用阶段。
6.某些情况下,颜料或助剂不能通过挤出混炼工艺在主体材料中实现分散和固结,例如金属和仿金属颜料在挤出后会失去大部分的金属闪光效果,一些外加型纹理剂在挤出后会失去产生纹理的功能。而简单地将金属或仿金属颜料干混入粉末涂料底粉进行喷涂又会因为颜料和底粉上粉率的差异而出现严重色差。行业内一般采用热粘结的方法将这类颜料颗粒粘结在底粉颗粒上,以避免颜料和底粉在运输和喷涂过程中的分离。这种热粘结工艺对解决色差问题显示了很好的效果,但这一工艺的操作控制要求高,设备昂贵,限制了其更大规模的应用。而外加型纹理剂也存在纹理剂和底粉在运输和喷涂过程中的分离问题。同样,热粘结也是一种有效但成本高昂的解决方案。
技术实现要素:
7.本发明提供了一种通过压力将各种细粉组料成分结成块状或片状材料,再粉碎至目标粒径(大于各细粉组料成分的中粒径)制备粉末涂料的新方法工艺。可以解决传统熔融挤出法所带来的上述各种问题,为粉末涂料制备提供了一种全新的技术方案。
8.本发明提供了一种粉末涂料的制作工艺方法,采用高压压实的方式,使不同组分的细粉状原料间实现压密固结,再将压密固结块料或片料粉碎至理想粒径(中粒径=15-100微米),得到均一的粉末成品,从而替代了现行工艺中熔融挤出的环节。
9.为达上述目的,本发明提供了一种新型的粉末涂料的制作工艺方法,包括如下步骤:
10.步骤一:将多个组料成分,按预设比例进行搅拌预混合,并通过气流混合机或高剪切混合机再次混合,制得混合料;
11.步骤二:通过活塞式或压辊式压实机,将所述混合料通过高压压实,制得压密固结的块料或片料;
12.步骤三:用气流粉碎机或空气分级磨或其它类型磨机将所述块料或片料进行粉碎,并用筛网进行分选,制得粉末涂料成品。
13.与现有技术相比,本发明的有益效果是:
14.本发明的制作工艺,对细粉状的各种粉末涂料原料混合物采用物理压实的方法,使原料间进行紧密粘结,再经粉碎得到粉末涂料成品。可将树脂、固化剂、填料、助剂等直接混合、压实、破碎,得到均一的粉末成品,从而完全替代现行的熔融挤出工艺。也可将配方中的部分树脂和部分填料、颜料、助剂等先进行熔融挤出并粉碎成细粉,再与配方中剩余的树脂和填料、颜料、助剂等混合,进行高压压实、破碎,得到均一的粉末成品,从而部分替代熔融挤出,无须将所有原料熔融挤出,这解决了熔融挤出过程中一些树脂难挤出的问题、高能耗问题、挤出某些材料产生的挤出机高磨损问题、韧性材料挤出后难破碎的问题、金属粉色差问题以及粉末涂料调色困难等问题。
附图说明
15.下面结合附图和具体实施方式对本发明作进一步详细的说明。
16.图1是本发明的粉末涂料的制作工艺方法的实施例一的流程示意图。
具体实施方式
17.下面对本发明实施的技术方案和实施例进行清楚、完整地描述,显然,所描述的实施例仅仅是本发明的一部分实施例,而不是全部的实施例。基于本发明中的实施例,本领域普通技术人员在没有做出创造性劳动前提下所获得的所有其他实施例,都属于本发明保护的范围。
18.在下面的描述中阐述了很多具体细节以便于充分理解本发明,但是本发明还可以采用其他不同于在此描述的其它方式来实施,本领域技术人员可以在不违背本发明内涵的情况下做类似推广,因此本发明不受下面公开的具体实施例的限制。
19.本发明中,主要包括以下步骤:
20.步骤一:将多个组料成分,按预设比例进行搅拌预混合,并通过气流混合机或高剪切混合机再次混合,制得混合料;
21.步骤二:通过活塞式或压辊式压实机,将所述混合料通过高压压实,制得压密固结的块料或片料;
22.步骤三:用气流粉碎机或空气分级磨将所述块料或片料进行粉碎,并用筛网进行分选,制得粉末涂料成品。
23.其中,所述多个组料成分包括树脂、固化剂、填料、颜料、助剂;或还包括所述树脂、固化剂、填料、颜料、助剂中的一种或多种经熔融挤出、粉碎得到的细粉颗粒。所述多个组料成分包括一种或多种底粉,所述一种或多种底粉为经熔融挤出、粉碎得到的细粉颗粒。
24.因此,针对不同的应用需求,实施本发明的技术方案时可选用如下不同的实施方式:
25.1.完全取代熔融挤出实施方式:
26.将粉末涂料配方中的所有n个组分m1,m2,m3,
…
mn,按照发明内容“步骤一”至“步骤三”进行加工处理,制得粉末涂料成品。其中的树脂组分可为单一树脂(例如m1)或多个不同树脂(例如m1,m2,m3)。“步骤一”中每个组分的颗粒中粒径均小于成品粉末涂料中粒径。
27.2.部分取代熔融挤出的实施方式:
28.将粉末涂料配方中所有n个组分m1,m2,m3,
…
mn中的k个组分(k《n),即m1,m2,m3,
…
mk,先按照熔融挤出工艺进行混合、挤出、粉碎,制得预挤出粉。再将其与配方中其它组分(难挤出的树脂、对挤出机磨损严重的材料、挤出后难粉碎的韧性材料、金属或仿金属颜料、外加型纹理剂等),即mk+1,mk+2,mk+3,
…ꢀ
mn一起按照发明内容“步骤一”至“步骤三”进行加工处理,制得粉末涂料成品。其中的树脂组分可为单一树脂(例如m1)或多个不同树脂(例如m1,m2,m3)。“步骤一”中每个组分的颗粒中粒径均小于成品粉末涂料中粒径。
29.3.保留熔融挤出的实施方式:
30.对于需要实现“粉调粉”效果的粉末涂料,先分别采用熔融挤出工艺制得预挤出粉e1,e2,e3,
…
ej,再将它们按指定比例、遵循发明内容“步骤一”至“步骤三”进行加工处理,制得粉末涂料成品。j个预挤出粉之间配方组成不同,可以是树脂不同,也可以是颜料、填
料、助剂不同。这种不同既可以是种类不同,也可以是剂量不同,还可以是种类、剂量均不同。“步骤一”中每个预挤出粉的颗粒中粒径均小于成品粉末涂料中粒径。
31.如图1所示,为本发明的粉末涂料的制作工艺方法的实施例一的流程示意图,实施例一:
32.本实施例中,粉末涂料组分由以下原料及比例组成:
[0033][0034][0035]
上述组分质量百分比之和为100%,每个组分的颗粒中粒径均小于15μm。按下列步骤制得丙烯酸粉末涂料成品:
[0036]
(1)将上述成分按照质量比,在容器中进行预混合搅拌,再通过高剪切混合机混合,制得混合料,在混合时,所述高剪切混合机混合时转速为 1000rpm-3000rpm;
[0037]
(2)使用活塞式压实机,在室温条件下,将步骤(1)得到的混合料加压至30mpa,进行高压压实,得到压密固结片料;
[0038]
(3)用空气分级磨将步骤(2)制得的压密固结片料进行粉碎,粉碎至中粒径 30微米,并用180目筛网分选,得到粉末涂料成品;
[0039]
通过上述步骤制作完成粉末涂料,采用电镜分析及喷涂测试的方式,对本实施例制作的粉末涂料进行验证,确认粉末原料各组分均匀结合;喷涂测试结果表明,涂膜表面平整均一、无色差,且涂膜性能良好。
[0040]
所述步骤一中,将多个组料成分在气流混合机中进行混合,通过袋滤器在气流混合机的下游收集,所述气流混合机进气压力为0.1-1.0mpa;或将多个组料成分在高剪切混合机中进行混合,所述高剪切混合机混合时转速为500rpm-10000rpm。
[0041]
所述步骤二中,通过活塞式或压辊式压实机进行高压压实时,温度为0-50℃,物料承受压力为1-50mpa;
[0042]
所述步骤三中,经气流粉碎机或空气分级磨粉碎得到的颗粒,其颗粒中粒径为 15-100微米,大于所述步骤一中的各组料成分的中粒径。
[0043]
优选地,所述筛网为50-600目的标准筛。
[0044]
作为优选方案,所述树脂包括热固性树脂:环氧树脂、环氧-聚酯、聚酯、聚氨酯、丙烯酸树脂、氟树脂等中的一种或多种;或热塑性树脂,包括聚乙烯、聚丙烯、丙烯酸树脂、聚酯、聚氯乙烯、氯化聚醚、聚苯硫醚、聚酰胺、纤维素、氟碳等中的一种或多种。
[0045]
所述助剂包括安息香、消泡剂、流平剂、光亮剂、偶联剂、防腐剂、抗氧化剂、疏水剂、亲水剂、抗紫外剂等中的一种或多种。
[0046]
所述颜料包括有机颜料、无机颜料、金属颜料及仿金属颜料中的一种或多种;所述填料包括硫酸钡、碳酸钙等常规填料及锌粉等功能性填料中的一种或多种。
[0047]
实施例二:
[0048]
本实施例中,粉末涂料组分由以下原料及比例组成:
[0049][0050][0051]
上述组分质量百分比之和为100%。
[0052]
首先将除铝粉金属颜料之外的所有组分通过熔融挤出并粉碎至中粒径d50=15
ꢀ±
2μm,获得底粉,然后按下列步骤制得聚酯金属粉末涂料成品:
[0053]
(1)在98质量份底粉中加入1.5质量份铝粉金属颜料和0.5质量份云母仿金属颜料,在容器中进行预混合搅拌,再通过高剪切混合机混合,制得混合料,在混合时,所述高剪切混合机混合时转速为500rpm-2000rpm;
[0054]
(2)使用活塞式压实机,在室温条件下,将步骤(1)得到的混合料加压至20mpa,进行高压压实,得到压密固结片料;
[0055]
(3)用空气分级磨将步骤(2)制得的压密固结片料进行粉碎,粉碎至中粒径 35微米,并用180目筛网分选,得到金属粉末涂料成品。
[0056]
通过上述步骤制作完成金属粉末涂料,采用电镜分析及喷涂测试的方式,对本实施例制作的金属粉末涂料进行验证,确认金属粉与底粉均匀结合;喷涂测试结果表明,涂膜表面平整均一、无色差,金属闪光效果好。
[0057]
实施例三:
[0058]
本实施例中,皱纹粉末涂料组分由以下原料及比例组成:
[0059][0060]
上述组分质量百分比之和为100%。
[0061]
首先将除皱纹剂之外的所有组分通过熔融挤出并粉碎至中粒径d50=15
±
2μm,获得底粉,然后按下列步骤制得聚酯金属粉末涂料成品:
[0062]
(1)在97质量份底粉中加入3质量份皱纹剂,在容器中进行预混合搅拌,再通过高剪切混合机混合,制得混合料,在混合时,所述高剪切混合机混合时转速为 1000rpm-2000rpm;
[0063]
(2)使用活塞式压实机,在室温条件下,将步骤(1)得到的混合料加压至20mpa,进行高压压实,得到压密固结片料;
[0064]
(3)用气流粉碎机将步骤(2)制得的压密固结片料进行粉碎,粉碎至中粒径 35微米,并用150目筛网分选,得到皱纹粉末涂料成品。
[0065]
通过上述步骤制作完成皱纹粉末涂料,采用电镜分析及喷涂测试的方式,对本实施例制作的金属粉末涂料进行验证,确认皱纹剂与底粉均匀结合;喷涂测试结果表明,涂膜表面皱纹均匀、无色差。
[0066]
实施例四:
[0067]
本实施例中,粉末涂料组分由以下原料及比例组成:
[0068][0069]
上述组分质量百分比之和为100%。
[0070]
首先将除锌粉之外的所有组分通过熔融挤出并粉碎至中粒径d50=15
±
2μm,获得底粉,然后按照按下列步骤制得富锌聚酯粉末涂料成品:
[0071]
(1)在20质量份底粉中加入80质量份铝粉金属颜料,在容器中进行预混合搅拌,再通过高剪切混合机混合,制得混合料,在混合时,所述高剪切混合机混合时转速为500rpm-2000rpm;
[0072]
(2)使用压辊式压实机,在室温条件下,将步骤(1)得到的混合料加压至35mpa,进行高压压实,得到压密固结片料;
[0073]
(3)用空气分级磨将步骤(2)制得的压密固结片料进行粉碎,粉碎至中粒径 35微米,并用180目筛网分选,得到富锌粉末涂料成品;
[0074]
通过上述步骤制作完成富锌粉末涂料,采用电镜分析、喷涂测试及耐腐蚀测试的方式,对本实施例制作的富锌粉末涂料进行验证,确认锌粉与底粉均匀结合;喷涂测试结果表明,涂膜表面平整均一、无色差;耐腐蚀性能与相同配方的挤出法制备的富锌粉一致。
[0075]
实施例五:
[0076]
本实施例为通过制备两种基色粉末涂料,再将它们按比例混合、压片、粉碎,获得目标颜色的例子。两种基色粉末涂料组分由以下原料及比例组成:
[0077]
蓝色粉末涂料:
[0078][0079][0080]
上述组分质量百分比之和为100%。
[0081]
黄色粉末涂料:
[0082][0083]
上述组分质量百分比之和为100%。
[0084]
首先分别通过熔融挤出制备黄色和蓝色基色片料并分别粉碎至中粒径d50=12
ꢀ±
2μm,获得黄色和蓝色基色粉,然后按照按下列步骤制得绿色环氧-聚酯粉末涂料成品:
[0085]
(1)将30质量份蓝色基色粉与70质量份黄色基色粉在容器中进行预混合搅拌,再通过高剪切混合机混合,制得混合料,在混合时,所述高剪切混合机混合时转速为1500rpm-2000rpm;
[0086]
(2)使用压辊式压实机,在室温条件下,将步骤(1)得到的混合料加压至30mpa,进行高压压实,得到压密固结片料;
[0087]
(3)用空气分级磨将步骤(2)制得的压密固结片料进行粉碎,粉碎至中粒径 30微米,并用180目筛网分选,得到绿色粉末涂料成品;
[0088]
通过上述步骤制作完成富锌粉末涂料,采用光学显微镜分析、喷涂测试及色差仪测试的方式,对本实施例制作的绿色环氧-聚酯粉末涂料成品进行验证,确认两种基色粉均匀结合;喷涂测试结果表明,涂膜表面平整均一;色差仪测试与标板色差小于指定值。
[0089]
实施例六:
[0090]
本实施例为通过将易粉碎的丙烯酸树脂与颜料、助剂、填料等熔融挤出、粉碎,制备成为丙烯酸底粉,再按比例与难挤出、粉碎的纯pvdf氟碳树脂细粉混合、压片、粉碎,获得丙烯酸改性pvdf氟碳粉末涂料的例子。丙烯酸底粉组分由以下原料及比例组成:
[0091]
丙烯酸底粉:
[0092][0093]
上述组分质量百分比之和为100%。
[0094]
首先通过熔融挤出制备丙烯酸底粉片料并粉碎至中粒径d50=20
±
2μm,获得丙烯酸底粉,然后按照按下列步骤制得丙烯酸改性pvdf氟碳粉末涂料成品:
[0095]
(1)将51质量份丙烯酸底粉与49质量份纯pvdf树脂细粉(d50:0.2-2μm) 在容器中进行预混合搅拌,再通过高剪切混合机混合,制得混合料,在混合时,所述高剪切混合机混合时转速为1500rpm-2000rpm;
[0096]
(2)使用压辊式压实机,在室温条件下,将步骤(1)得到的混合料加压至30mpa,进行高压压实,得到压密固结片料;
[0097]
(3)用空气分级磨将步骤(2)制得的压密固结片料进行粉碎,粉碎至中粒径 30微
米,并用180目筛网分选,得到丙烯酸改性pvdf氟碳粉末涂料成品;
[0098]
通过上述步骤制作完成丙烯酸改性pvdf氟碳粉末涂料,采用光学显微镜分析、喷涂测试及色差仪测试的方式,对本实施例制作的丙烯酸改性pvdf氟碳粉末涂料成品进行验证,确认丙烯酸底粉与pvdf树脂粉末均匀结合;喷涂测试结果表明,涂膜表面平整均一;耐紫外老化性能、耐腐蚀性能与相同配方的挤出法制备的丙烯酸改性pvdf氟碳粉末涂料一致。