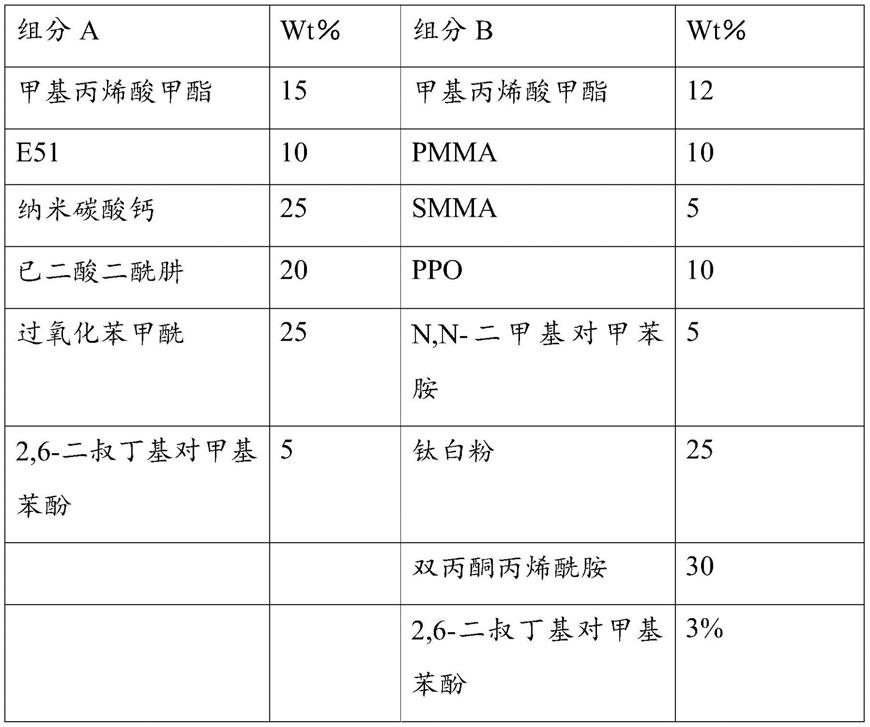
1.本发明涉及丙烯酸酯结构胶技术领域,具体涉及一种高硬度丙烯酸酯胶粘剂。
背景技术:
2.随着生活水平的不断提升,越来越多的家庭和宾馆会安装浴缸提升生活体验。浴缸材质经过不断升级换代,已经由金属材料升级到陶瓷材质,并进一步升级到了复合材料亚克力材质。亚克力是聚甲酯丙烯酸甲酯的别称,其具有质轻、强度高、硬度高,易加工,耐候耐腐蚀性好的优点。
3.浴缸通常由内外缸体两部分组成,内外缸体因为都为亚克力制作而成,无法进行焊接,因此内外缸体的拼接需要使用胶黏剂进行。在现有种类的胶粘剂中,丙烯酸酯胶因主要成分为甲基丙烯酸甲酯,其对亚克力材料有很好的粘接性,同时能够快速固化的特性,因此可以用于浴缸制造行业。
4.但现有的丙烯酸酯胶在固化后胶体会收缩且散发出大量气体,在胶体表面形成凹陷和气孔,使得浴缸成品的外管不达标,同时由于现有产品的固化硬度不足,成品打磨抛光也很难达标。
技术实现要素:
5.基于此,本发明的目的在于提供一种新的高硬度丙烯酸酯胶粘剂,该胶粘剂对亚克力具有良好的粘结性,同时其邵d强度可以达到75以上,拉伸剪切强度能够达到基材破坏且固化物黄变情况也能够有效得到改善。
6.本发明采用如下技术方案来实现上述技术目的:
7.本发明提供一种高硬度丙烯酸酯胶粘剂,包括组分a和组分b两种组分,其中组分a和组分b主要由如下重量百分比的各原料制备而成:
8.组分a:甲基丙烯酸甲酯10~20%、环氧树脂e-51 10~30%、纳米碳酸钙25%、己二酸二酰肼15~25%、氧化剂15~25%、2,6-二叔丁基对甲基苯酚3~5%;
9.组分b:甲基丙烯酸甲酯5~30%、硬化剂10~30%、还原剂1~9%、无机填料10~30%、双丙酮丙烯酰胺15~45%、2,6-二叔丁基对甲基苯酚3~5%;
10.其中,所述硬化剂由聚甲基丙烯酸甲酯、苯乙烯二甲基丙烯酸甲酯共聚物和聚苯醚按照质量比(0~2):1:2混合而成。
11.本发明所提供的高硬度丙烯酸酯胶粘剂,其通过搭建不同于同类产品的复合氧化还原体系,解决了同类产品固化过程中因自由基聚合大量放热导致体系收缩且气体大量散出,造成表面容易凹陷和气孔的问题;通过引入新型聚合物树脂(即硬化剂),有效提升了固化物硬度,拉伸剪切强度能够达到基材破坏且固化物黄变情况也能有效得到改善。
12.优选地,组分a和组分b主要由如下重量百分比的各原料制备而成:
13.组分a:甲基丙烯酸甲酯10~15%、环氧树脂e-51 10~30%、纳米碳酸钙25%、己二酸二酰肼20~25%、氧化剂15~25%、2,6-二叔丁基对甲基苯酚3~5%;
14.组分b:甲基丙烯酸甲酯5~30%、硬化剂10~30%、还原剂1~9%、无机填料10~30%、双丙酮丙烯酰胺15~45%、2,6-二叔丁基对甲基苯酚3~5%;
15.其中,所述硬化剂由聚甲基丙烯酸甲酯、苯乙烯二甲基丙烯酸甲酯共聚物和聚苯醚按照质量比(1~2):1:2混合而成。
16.采用上述更优的方案,制备得到的丙烯酸酯胶粘剂,其能够彻底解决气泡和黄变问题。
17.优选地,氧化剂选自过氧化苯甲酰、异丙苯过氧化氢、过氧化叔丁酯和过氧化甲乙酮中的一种或几种。更优选地,所述氧化剂为过氧化苯甲酰。
18.优选地,还原剂选自四甲基硫脲、乙撑硫脲、n,n-二甲基对甲苯胺、三乙烯二胺和二乙烯三胺中的一种或多种。更优选地,所述还原剂为n,n-二甲基对甲苯胺。
19.优选地,组分b中的无机填料选自钛白粉、氧化铝粉末和氢氧化铝粉末中一种或多种。
20.在浴缸制造业中通常对拼接用胶有颜色要求,即亮白色,但常规丙烯酸酯胶在还原剂与氧化剂发生氧化还原反应时会放出大量的热量,导致体系内物质受热发生黄变,从而使颜色不满足要求,发明人在实验过程中,加入了各种白色填料或染料也均未解决该问题。
21.本发明通过引入己二酸二酰肼和双丙酮丙烯酸胺,形成新的复合氧化还原体系,有效降低了体系放热量,使聚合反应趋于平缓,能够很好的解决黄变问题。其具体的原理如下:双丙酮丙烯酰胺在自由基引发下可以参与自由基聚合,从而与体系主链相连接,己二酸二酰肼与双丙酮丙烯酰胺可以发生酮肼交联,剧烈放热的自由基聚合在酮肼交联的反应效应影响下,有效控制了反应热量的散热,并保持了较为平稳的反应转化率,从而大幅降低了黄变。该复合氧化还原体系不仅控制了体系热量的散发,有效控制产品的收缩,同时减少了体系内气泡的生成及扩散,使固化物外观得到有效改善。
22.复合硬化剂的搭配使用,不仅提升了产品的硬度,使胶粘剂固化物的硬度达到了树脂的相近硬度;同时复合硬化剂在体系中溶解后因其不同的形状结构与白色无机粉料具有非常好的相容性,使得产品固化后的颜色白度更好,进一步改善了黄变问题。
23.与现有的丙烯酸胶粘剂相比,采用本发明制备得到的丙烯酸胶粘剂,固化物表面光洁无气孔且低收缩,固化物硬度(邵d强度)大于75,产生气泡和黄变的问题能够得到有效改善,拉伸剪切强度能够达到基材破坏。
具体实施方式
24.下面结合具体实施例对本发明作进一步的详细说明,以使本领域的技术人员更加清楚地理解本发明。
25.以下各实施例,仅用于说明本发明,但不止用来限制本发明的范围。基于本发明中的具体实施例,本领域普通技术人员在没有做出创造性劳动的情况下,所获得的其他所有实施例,都属于本发明的保护范围。
26.在本发明实施例中,若无特殊说明,所有原料组分均为本领域技术人员熟知的市售产品;在本发明实施例中,若未具体指明,所用的技术手段均为本领域技术人员所熟知的常规手段。
27.实施例1
28.表1
[0029][0030]
性能测试:
[0031]
相关性能测试包括固化后产品的硬度、剪切强度、黄变程度,具体测试方法如下:
[0032]
(1)硬度的测试方法:按照标准《gb/t2411-2008塑料和硬橡胶使用硬度计测定压痕硬度》进行测试;
[0033]
(2)剪切强度的测试方法:按照标准《gb t7124-2008胶粘剂拉伸剪切强度测定方法》进行测试;
[0034]
(3)黄变的测试:目视法测试黄变程度。
[0035]
实施例2
[0036]
表2
[0037][0038]
在本实施例中氧化剂组分与还原剂组分按照体积比为1:1制备丙烯酸酯胶。
[0039]
实施例3
[0040]
表3
[0041]
[0042][0043]
在本实施例中氧化剂组分与还原剂组分按照体积比为1:1制备丙烯酸酯胶。
[0044]
实施例1-3,固定氧化剂组分组成不变,验证不同pmma使用量对产品硬度的影响
[0045]
实施例4
[0046]
表4
[0047]
[0048][0049]
在本实施例中氧化剂组分与还原剂组分按照体积比为1:1制备丙烯酸酯胶。
[0050]
实施例5
[0051]
表5
[0052][0053]
在本实施例中氧化剂组分与还原剂组分按照体积比为1::1制备丙烯酸酯胶。
[0054]
实施例4-5,固定还原剂组分不变,验证不同已二酸二酰肼用量对固化后外观及强度的影响
[0055]
对照例1
[0056]
表6
[0057][0058]
在本实施例中氧化剂组分与还原剂组分按照体积比为1:1制备丙烯酸酯胶。
[0059]
对照例2
[0060]
表7
[0061]
[0062][0063]
在本实施例中氧化剂组分与还原剂组分按照体积比为1:1制备丙烯酸酯胶。
[0064]
对照例1-2作为常规技术方案与本发明技术方案的对比例,验证已二酸二酰肼、双丙酮丙烯酰胺和硬化剂对产品硬度及外观气泡的影响。
[0065]
实施例1-5与对照例1-2按各自配方制备双组份丙烯酸酯胶粘剂,对上述配方进行各项指标的测试,测试结果如下:
[0066]
表8
[0067][0068][0069]
据上表中测试结果可以得出以下结论:
[0070]
1、甲基丙烯酸甲酯和复合型硬化剂pmma+smma+ppo用量的增加都会提升产品硬度;
[0071]
2、已二酸二酰肼与双丙酮丙烯酰胺的搭配使用,有效控制了反应体系的反应热量的散发,降低了黄变,同时减少了体系内气泡的生成及扩散;
[0072]
3、优选甲基丙烯酸甲酯、已二酸二酰肼、双丙酮丙烯酰胺和复合型硬化剂并确定适宜的用量可制得满足现有行业要求的产品。
[0073]
在此有必要指出的是,以上实施例仅限于对本发明的技术方案做进一步的阐述和说明,并不是对本发明的技术方案的进一步的限制,本发明的方法仅为较佳的实施方案,并非用于限定本发明的保护范围。凡在本发明的精神和原则之内,所作的任何修改、等同替换、改进等,均应包含在本发明的保护范围之内。