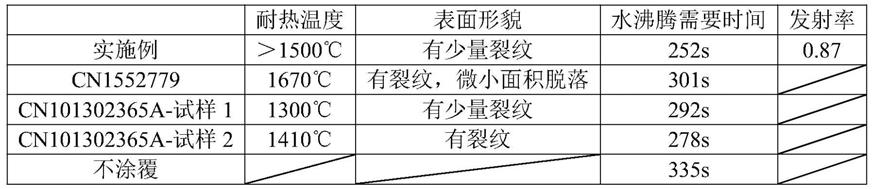
2h,烧结结束后随炉冷却至室温,得到焙烧料;
11.c.将焙烧料、mgo与过渡金属氧化物按质量比100∶8-10∶4-5的比例混合均匀,得到混料b;
12.d.将混料b进行烧结,升温至1300-1400℃保温0.5-3h,烧结结束后冷却至室温,机械破碎后得到红外涂层粉料;
13.e.将红外涂层粉料、高温粘结剂和水充分混合后,得到红外涂层涂料。
14.上述步骤a中,所述冶金固废为钒钛冶炼过程中的高温碳化渣固废,其化学成分按质量百分比为:tti 10-15%,tic 10-20%,al2o315-25%,sio220-30%,cao 23-35%,及不可避免的杂质。
15.进一步的是,所述冶金固废的粒度为-200目的占比≥70%。
16.上述步骤a中,所述氧化铁红为冷轧酸洗后的氧化铁皮,其化学成分按质量百分比为95-98%的fe2o3,及不可避免的杂质。
17.进一步的是,所述氧化铁红的粒度为-200目。
18.上述步骤c中,所述焙烧料的粒度为-200目的占比≥70%。
19.上述步骤c中,所述过渡金属氧化物为cuo、coo、cr2o3、mno2、zro2中至少一种。
20.上述步骤d中,机械破碎后的红外涂层粉料粒度为-300目。
21.上述步骤e中,所述高温粘结剂为水玻璃,模数为2.0-2.5。
22.进一步的是,高温粘结剂的加入量为红外辐射涂层粉料质量的5-10%。
23.本发明的有益效果是:首先,本发明利用冶金固废的中tic在600-800℃下,与空气中氧气反应,产生tio2,而tio2、cao与氧化铁红的fe2o3在1000-1200℃的温度下采用高温烧结工艺制备钙钛矿复合氧化物,能极大提高材料红外辐射性能;其次,通过固废中的al2o3、sio2、mgo在1300-1400℃高温熔融状态下合成堇青石(mg2a
l4
si5o
18
),然后利用过渡金属氧化物对堇青石改性,使其具有较强的红外辐射相应特性。
24.本发明制备方法利用钒钛冶炼过程的高温碳化渣与氧化铁红中有效成分掺混过渡金属氧化物,采用分步与分阶段高温烧结工艺制备杂项堇青石和钙钛矿复合氧化物,同时结合对高温粘结剂的控制配合制备得到杂项堇青石-钙钛矿晶体即红外涂层涂料,这种晶体材料具有良好耐热性能和高发率,其软化温度不低于1500℃,高温粘结性较好,综合发射率不低于0.87,其低波段发射率(1-5μm)不低于0.93,综合性能优异,本发明利用冶金固废为原料制备得到红外涂层涂料,生产成本低廉,可大规模生产应用。
具体实施方式
25.本发明的技术方案,具体可以按照以下方式实施。
26.利用冶金固废制备红外涂层涂料的方法,包括如下步骤:
27.a.将冶金固废与氧化铁红按照质量比100∶30-35的比例混合均匀,得到混料a;
28.b.将混料a进行烧结,升温至600-800℃保温3-4h后,再升温至1000-1200℃保温1-2h,烧结结束后随炉冷却至室温,得到焙烧料;
29.c.将焙烧料、mgo与过渡金属氧化物按质量比100∶8-10∶4-5的比例混合均匀,得到混料b;
30.d.将混料b进行烧结,升温至1300-1400℃保温0.5-3h,烧结结束后冷却至室温,机
械破碎后得到红外涂层粉料;
31.e.将红外涂层粉料、高温粘结剂和水充分混合后,得到红外涂层涂料。
32.上述步骤a中,所述冶金固废为钒钛冶炼过程中的高温碳化渣固废,其化学成分按质量百分比为:tti 10-15%,tic 10-20%,al2o315-25%,sio220-30%,cao 23-35%,及不可避免的杂质,所述冶金固废的粒度为-200目的占比≥70%。
33.上述步骤a中,所述氧化铁红为冷轧酸洗后的氧化铁皮,其化学成分按质量百分比为95-98%的fe2o3,及不可避免的杂质,所述氧化铁红的粒度为-200目。
34.本发明采用固废中的tic在600-800℃下,与空气中氧气反应,生成tio2,而固废中cao与生成的tio2在1000-1200℃高温条件下可以合成catio3晶体;同时利用氧化铁红的三价铁离子高温下替代晶体中b位离子形成钙钛矿复合氧化物。钙钛矿复合氧化物具有独特的晶体结构,尤其经掺杂后形成的晶体缺陷结构和性能,杂质的引入致使晶格产生畸变,增强了晶格振动吸收,能极大提高材料红外辐射性能,尤其是短波段(1-5μm)。
35.上述步骤c中,所述焙烧料的粒度为-200目的占比≥70%。
36.上述步骤c中,所述过渡金属氧化物为cuo、coo、cr2o3、mno2、zro2中至少一种。
37.而固废成分中的al2o3、sio2与额外添加的mgo在1300-1400℃高温条件下可以合成堇青石(mg2a
l4
si5o
18
),加入过渡金属氧化可以替代堇青石的中的金属元素,在高温条件下改性堇青石,使得原有晶体结构有杂质合理加入,对称性变差,晶格振动的时偶极矩变化较大,具有较强的红外辐射相应特性。此外,堇青石由于具有热稳定性能好、热膨胀系数小的优点,固被作为红外辐射材料的化学组成的骨架。
38.上述步骤d中,机械破碎后的红外涂层粉料粒度为-300目。
39.水玻璃模数是水玻璃的重要参数,水玻璃模数越大,固体水玻璃越难溶于水,n为1时常温水即能溶解,n加大时需热水才能溶解,n大于3时需4个大气压以上的蒸汽才能溶解。水玻璃模数越大,氧化硅含量越多,水玻璃粘度增大,易于分解硬化,粘结力增大。因此优选的是,上述步骤e中,所述高温粘结剂为水玻璃,模数为2.0-2.5。本发明采用模数2.0-2.5的水玻璃,是为了工业规模化制备,采用热水进行混合有利于规模化制备,而模数太低不利于分解硬化,高温粘结性会变低,经过试验后确定2.0-2.5的范围。水玻璃的中氧化硅成分在炉内高温下能进一步的促进杂项堇青石-钙钛矿晶体的形成。
40.进一步的是,高温粘结剂的加入量为红外辐射涂层粉料质量的5-10%。
41.下面通过实际的例子对本发明的技术方案和效果做进一步的说明。
42.实施例
43.本发明提供一组采用本发明方法制备红外涂层涂料的实施例,本实施例中采用的固废高温碳化渣的化学成分按质量百分比为:tti 14.6%,tic 17.2%,al2o318.7%,sio222.1%,cao 26.4%,及不可避免的杂质。
44.本发明利用冶金固废制备红外涂层涂料的具体实验步骤如下:
45.a.将200g固废高温碳化渣破碎至-200目的占比≥70%,将破碎后固废、氧化铁红按照质量比100∶30进行均匀混合,得到混料a,共计460g;
46.b.将混料a,放入马弗炉中,在700℃进行高温烧结4h,然后升温至1100℃烧结2h,随炉冷却至室温,得到焙烧料;
47.c.将焙烧料b破碎至200目的占比≥70%,然后与mgo、mno2按照质量比100∶10∶5混
合,共计529g,充分混合,得到混料b;
48.d.将混料b,置于马弗炉中,在1300℃烧结2h,冷却到室温后,机械破碎至-300目,得到红外涂层粉料;
49.e.按照质量百分比将90%的红外涂层粉料与10%的2.3模数的水玻璃混合,并加入热水进行搅拌,得到得到红外涂层涂料。
50.对实施例制备得到的红外涂层粉料和涂料进行检测,具体如下:
51.1、通过熔点仪和发射率测试仪对实施例制备得到的红外涂层粉料进行检测,结果为:其软化温度为>1500℃,1-22μm波段内的平均发射率为0.89,其中1-5μm的短波段发射率在0.93。
52.2、将实施例制备得到的红外涂层涂料涂覆到基体表面,然后进行检测:
53.(1)将红外涂层涂料涂抹到装有500ml水的1l烧杯底部,然后在烧杯底部进行火焰加热;
54.(2)将红外涂层涂料涂抹到1块进行了抛光处理的300mm
×
300mm耐火砖上,放入马弗炉中,温度从常温升至1000℃,然后随炉冷却,重复25次,然后进行观察涂层形貌。
55.同时,本发明按专利cn101302365a、cn1552779中的涂料配方及制备方法制备了涂料,同样进行(1)(2)的实验,作为对比例进行对比分析,实验结果如表1所示。
56.表1红外涂层涂料测试结果
[0057][0058]
由表1可知,采用本发明实施例制备的红外涂层涂料涂覆后的烧杯,将水加热至沸腾所需时间比不涂覆的烧杯快了24.7%,比对比例中用时最短的cn101302365a-试样2快了9.3%,由此可知,采用本发明方法制备的红外涂层涂料具有优异的节能降耗性能;并且本发明实施例的红外涂层涂料进行25次热震实验后,高温粘结性良好,耐热温度>1500℃,发射率为0.87,综合性能优于同类产品。