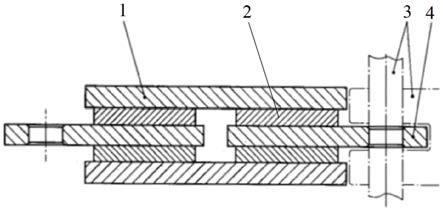
1.本发明属于胶粘剂技术领域,具体涉及一种复合材料预浸料与三元乙丙橡胶绝热层共固化粘接胶膜及其制备方法。
背景技术:
2.树脂基复合材料具有比强度高、比模量高、力学性能可设计性等优点,是目前轻量化设计的最理想材料。由于轻量化的要求,如前高速飞行器发动机的制造大都采用复合材料代替金属材料进行制造,即复合材料预浸料与三元乙丙橡胶绝热层通过界面胶接材料实现共固化成型。
3.然而,目前高速飞行器发动机复合材料壳体与三元乙丙橡胶绝热层粘接沿用了原金属壳体与三元乙丙橡胶绝热层粘接材料及粘接工艺,即通过人工刷涂糊状胶工艺。采用此工艺进行粘接复合材料预浸料及三元乙丙橡胶绝热层,胶层厚度难以控制、质量均一性不好,施胶工艺稳定性差;在升温固化过程中胶黏剂在表面张力作用下出现聚集现象,胶层厚度进一步失去控制,造成胶接强度分散性扩大,在大面积整体胶接时易造成裙与壳体局部脱粘,严重影响复合材料壳体与三元乙丙绝热层共固化粘接的可靠性。
4.因此,研制一种既能与复合材料预浸料共固化粘接成型、同时又与三元乙丙橡胶绝热层共硫化粘接成型的胶膜材料,对提高复合材料壳体与三元乙丙绝热层共固化粘接的可靠性具有重要意义。
技术实现要素:
5.本发明的目的是要解决现有高速飞行器发动机复合材料壳体与三元乙丙橡胶绝热层粘接沿用了原金属壳体与三元乙丙橡胶绝热层粘接材料及粘接工艺,胶层厚度难以控制、质量均一性不好,施胶工艺稳定性差和粘结的可靠性差的问题,而提供一种复合材料预浸料与三元乙丙橡胶绝热层共固化粘接胶膜及其制备方法。
6.复合材料预浸料与三元乙丙橡胶绝热层共固化粘接胶膜按照重量份数由30~50份主体树脂、25~45份主增韧剂、10~25份辅助增韧剂、5~15份固化剂、3~12份硫化剂和1~4份填料制备而成;
7.所述的主体树脂由侧链含萘环结构环氧树脂和其它环氧树脂组成,其中,侧链含萘环结构环氧树脂占主体树脂质量的40%~50%;所述的其它环氧树脂为双酚a型环氧树脂、三官能团脂环族环氧树脂和邻甲酚醛型环氧树脂中的一种或其中几种的混合物。
8.一种复合材料预浸料与三元乙丙橡胶绝热层共固化粘接胶膜的制备方法,是按以下步骤完成的:
9.一、按照重量份数称取30~50份主体树脂、25~45份主增韧剂、10~25份辅助增韧剂、5~15份固化剂、3~12份硫化剂和1~4份填料;
10.二、首先将30~50份主体树脂加入到反应釜中,然后将反应釜加热至240℃,再在
搅拌状态下加入10~25份辅助增韧剂,最后在190℃~200℃下保温30min,制得均相共混树脂;
11.三、采用机械共混法将步骤二制得的均相共混树脂与25~45份主增韧剂、5~15份固化剂、3~12份硫化剂和1~4份填料混合均匀,制得胶料;
12.四、将步骤三制得的胶料在50℃~80℃的烘箱中预热20min~40min,然后在辊温为70℃~90℃的压延机上压制成膜,即得到复合材料预浸料与三元乙丙橡胶绝热层共固化粘接胶膜。
13.本发明有益效果:
14.本发明的一种复合材料预浸料与三元乙丙橡胶绝热层共固化粘接胶膜即与复合材料预浸料具有良好的共固化粘接匹配性能,又与三元乙丙橡胶绝热层具有良好的共硫化粘接匹配性能;采用该胶膜粘接复合材料预浸料,常温双搭接拉伸剪切强度可达24.12mpa,120℃双搭接拉伸剪切强度可达12.59mpa;采用该胶膜粘接复合材料预浸料与三元乙丙橡胶绝热层,120℃四板剪切(试件形式如图1所示)强度为3.55mpa、常温180
°
剥离强度为52.16n/cm。本发明的胶膜材料具有良好的自粘性,对三元乙丙橡胶绝热层具有很好的铺贴性;同时胶膜厚度均一、单位面积质量精确可控,确保了复合材料预浸料与三元乙丙橡胶绝热层共固化胶接的稳定性和可靠性;另外,在升温固化过程中不会出现采用传统糊状胶因聚集而引起的胶层失控现象,所以保证了高速飞行器复合材料壳体与三元乙丙橡胶绝热层共固化胶接的稳定性和可靠性。
附图说明
15.图1为采用实施例一制备的复合材料预浸料与三元乙丙橡胶绝热层共固化粘接胶膜粘接复合材料预浸料与三元乙丙橡胶绝热层的四板剪切试件结构示意图,图中1为复合材料预浸料,2为三元乙丙橡胶绝热层,3为测试夹具螺栓,4为复合材料预浸料。
具体实施方式
16.以下实施例进一步说明本发明的内容,但不应理解为对本发明的限制。在不背离本发明实质的情况下,对本发明方法、步骤或条件所作的修改和替换,均属于本发明的范围。
17.具体实施方式一:本实施方式复合材料预浸料与三元乙丙橡胶绝热层共固化粘接胶膜按照重量份数由30~50份主体树脂、25~45份主增韧剂、10~25份辅助增韧剂、5~15份固化剂、3~12份硫化剂和1~4份填料制备而成;
18.所述的主体树脂由侧链含萘环结构环氧树脂和其它环氧树脂组成,其中,侧链含萘环结构环氧树脂占主体树脂质量的40%~50%;所述的其它环氧树脂为双酚a型环氧树脂、三官能团脂环族环氧树脂和邻甲酚醛型环氧树脂中的一种或其中几种的混合物。
19.具体实施方式二:本实施方式与具体实施方式一不同点是:步骤一中所述的侧链含萘环结构环氧树脂的结构式为:
20.所述的三官能团脂环族环氧树脂的结构式为:
21.所述的邻甲酚醛型环氧树脂的结构式为:
22.其它步骤与具体实施方式一相同。
23.具体实施方式三:本实施方式与具体实施方式一或二之一不同点是:复合材料预浸料与三元乙丙橡胶绝热层共固化粘接胶膜按照重量份数由30~45份主体树脂、30~45份主增韧剂、15~20份辅助增韧剂、8~12份固化剂、6~9份硫化剂和2~4份填料制备而成。其它步骤与具体实施方式一或二相同。
24.具体实施方式四:本实施方式与具体实施方式一至三之一不同点是:复合材料预浸料与三元乙丙橡胶绝热层共固化粘接胶膜按照重量份数由43份主体树脂、39份主增韧剂、17份辅助增韧剂、10份固化剂、8份硫化剂和3份填料制备而成。其它步骤与具体实施方式一至三相同。
25.具体实施方式五:本实施方式与具体实施方式一至四之一不同点是:所述的主增韧剂为溴化三元乙丙橡胶和其它橡胶组成,其中,溴化三元乙丙橡胶占主增韧剂质量的40%~50%;所述的其它橡胶为固体丁腈橡胶、固体羧基丁腈橡胶和氢化丁腈橡胶中的一种或其中几种的混合物;所述的溴化三元乙丙橡胶的结构式为:
26.其它步骤与具体实施方式一至四相同。
27.具体实施方式六:本实施方式与具体实施方式一至五之一不同点是:所述的辅助增韧剂由笼型聚倍半硅氧烷、聚砜和其它辅助增韧剂组成,其中笼型聚倍半硅氧烷占辅助增韧剂质量的20%~35%,聚砜占辅助增韧剂质量的15%~30%;所述的其它辅助增韧剂为酚酞基聚芳醚酮、核-壳粒子和聚醚酰亚胺中的一种或其中几种的混合物;所述的笼型聚倍半硅氧烷的结构式为:
28.其中r为其它步骤与具体实施方式一至五相同。
29.具体实施方式七:本实施方式与具体实施方式一至六之一不同点是:所述的固化剂由双氰胺、二氨基二苯砜和4-氨基-邻苯二甲酰亚胺组成,其中双氰胺、二氨基二苯砜和4-氨基-邻苯二甲酰亚胺的质量比为(2~6):(1~3):1。其它步骤与具体实施方式一至六相同。
30.具体实施方式八:本实施方式与具体实施方式一至七之一不同点是:所述的硫化剂为硫磺粉、过氧化二异丙苯、二叔丁基过氧化物、氧化锌和硬脂酸中的一种或几种的混合物;所述的填料为炭黑、白炭黑、纳米级钛白粉、轻质碳酸钙和碳纳米管中的一种或几种的混合物。其它步骤与具体实施方式一至七相同。
31.具体实施方式九:本实施方式是一种复合材料预浸料与三元乙丙橡胶绝热层共固化粘接胶膜的制备方法是按以下步骤完成的:
32.一、按照重量份数称取30~50份主体树脂、25~45份主增韧剂、10~25份辅助增韧剂、5~15份固化剂、3~12份硫化剂和1~4份填料;
33.二、首先将30~50份主体树脂加入到反应釜中,然后将反应釜加热至240℃,再在搅拌状态下加入10~25份辅助增韧剂,最后在190℃~200℃下保温30min,制得均相共混树脂;
34.三、采用机械共混法将步骤二制得的均相共混树脂与25~45份主增韧剂、5~15份固化剂、3~12份硫化剂和1~4份填料混合均匀,制得胶料;
35.四、将步骤三制得的胶料在50℃~80℃的烘箱中预热20min~40min,然后在辊温为70℃~90℃的压延机上压制成膜,即得到复合材料预浸料与三元乙丙橡胶绝热层共固化粘接胶膜。
36.具体实施方式十:本实施方式与具体实施方式一至九之一不同点是:步骤四中将步骤三制得的胶料在60℃~75℃的烘箱中预热30min,然后在辊温为80℃~85℃的压延机上压制成膜,即得到复合材料预浸料与三元乙丙橡胶绝热层共固化粘接胶膜。其它步骤与具体实施方式一至九相同。
37.下面结合附图和实施例对本发明进行详细的说明。
38.实施例一:一种复合材料预浸料与三元乙丙橡胶绝热层共固化粘接胶膜的制备方法,是按以下步骤完成的:
39.一、按照重量份数称取18份侧链含萘环结构的环氧树脂、12份通用型双酚a型环氧树脂、6份三官能团脂环族环氧树脂、4份邻甲酚醛型环氧树脂、17份溴化三元乙丙橡胶、9份固体丁腈橡胶、6份固体羧基丁腈橡胶、6份笼型聚倍半硅氧烷、4份聚砜(psf)、2份核-壳粒子、4份双氰胺、2份二氨基二苯砜、1份4-氨基-邻苯二甲酰亚胺、2份硫磺粉、5份过氧化二异丙苯、3份氧化锌、2份炭黑和1份轻质碳酸钙;
40.二、将18份侧链含萘环结构的环氧树脂、12份通用型双酚a型环氧树脂、6份三官能团脂环族环氧树脂、4份邻甲酚醛型环氧树脂加入到反应釜中,然后将反应釜加热至240℃,再在搅拌状态下加入6份笼型聚倍半硅氧烷、4份聚砜(psf)、2份核-壳粒子,最后在200℃下保温30min,制得均相共混树脂;
41.三、采用机械共混法将步骤二制得的均相共混树脂与17份溴化三元乙丙橡胶、9份固体丁腈橡胶、6份固体羧基丁腈橡胶、4份双氰胺、2份二氨基二苯砜、1份4-氨基-邻苯二甲酰亚胺、2份硫磺粉、5份过氧化二异丙苯、3份氧化锌、2份炭黑和1份轻质碳酸钙混合均匀,制得胶料;
42.四、将步骤三制得的胶料在65℃的烘箱中预热30min,然后在辊温为80℃的压延机上压制成膜,即得到复合材料预浸料与三元乙丙橡胶绝热层共固化粘接胶膜。
43.实施例一中使用的原料来源为:侧链含萘环结构的环氧树脂生产厂家为上海众司实业有限公司,牌号为nc-7300l;通用型双酚a型环氧树脂生产厂家为,牌号为e-51;三官能团脂环族环氧树脂由哈尔滨工业大学提供;邻甲酚醛型环氧树脂生产厂家为天太高新科技(广州)有限公司,牌号cne-220;溴化三元乙丙橡胶为自制品(证明材料:王德志,曲春艳,张杨,等.三元乙丙橡胶粘接用胶黏剂的研制[j].化学与粘合,2006(3));固体丁腈橡胶生产厂家为南帝化工,牌号为1051;固体羧基丁腈橡胶厂家为南帝化工,牌号为1072;笼型聚倍半硅氧烷由哈尔滨工业大学提供;聚砜(psf)生产厂家为大连聚砜塑料有限公司;核-壳粒子生产厂家为日本钟渊化学工业公司,牌号为mx-125;双氰胺生产厂家为宁夏远大兴博化工有限公司;二氨基二苯砜生产厂家为河北冠朗生物科技有限公司;4-氨基-邻苯二甲酰亚
胺生产厂家为上海源叶生物科技有限公司;硫磺粉生产厂家为天津市天力化学试剂有限公司;过氧化二异丙苯生产厂家为阿拉丁生化科技股份有限公司;氧化锌生产厂家为上海源叶生物科技有限公司;炭黑生产厂家为上海源叶生物科技有限公司;轻质碳酸钙生产厂家为河北陌槿生物科技有限公司。
[0044]
实施例一制备的复合材料预浸料与三元乙丙橡胶绝热层共固化粘接胶膜的厚度均一、具有良好的自粘性。采用该胶膜进行性能测试,测试结果如表1所示。
[0045]
表1实施例一制备的胶膜性能测试结果
[0046][0047][0048]
实施例二:一种复合材料预浸料与三元乙丙橡胶绝热层共固化粘接胶膜的制备方法,是按以下步骤完成的:
[0049]
一、按照重量份数称取20份侧链含萘环结构的环氧树脂、13份通用型双酚a型环氧树脂、7份邻甲酚醛型环氧树脂、19份溴化三元乙丙橡胶、5份固体丁腈橡胶、8份固体羧基丁腈橡胶、6份笼型聚倍半硅氧烷、3份酚酞基聚芳醚酮(pek-c)、4份核-壳粒子、5份双氰胺、2.5份二氨基二苯砜、1.5份4-氨基-邻苯二甲酰亚胺、3份硫磺粉、3份过氧化二异丙苯、4份氧化锌、3份炭黑;
[0050]
二、首先将20份侧链含萘环结构的环氧树脂、13份通用型双酚a型环氧树脂、7份邻甲酚醛型环氧树脂加入到反应釜中,然后将反应釜加热至240℃,再在搅拌状态下加入6份笼型聚倍半硅氧烷、3份酚酞基聚芳醚酮(pek-c)、4份核-壳粒子,最后在193℃下保温30min,制得均相共混树脂;
[0051]
三、采用机械共混法将步骤二制得的均相共混树脂与19份溴化三元乙丙橡胶、5份固体丁腈橡胶、8份固体羧基丁腈橡胶、5份双氰胺、2.5份二氨基二苯砜、1.5份4-氨基-邻苯二甲酰亚胺、3份硫磺粉、3份过氧化二异丙苯、4份氧化锌、3份炭黑混合均匀,制得胶料;
[0052]
四、将步骤三制得的胶料在70℃的烘箱中预热35min,然后在辊温为86℃的压延机上压制成膜,即得到复合材料预浸料与三元乙丙橡胶绝热层共固化粘接胶膜。
[0053]
实施例二中使用的原料来源为:侧链含萘环结构的环氧树脂生产厂家为上海众司实业有限公司,牌号为nc-7300l;通用型双酚a型环氧树脂生产厂家为,牌号为e-51;邻甲酚醛型环氧树脂生产厂家为天太高新科技(广州)有限公司,牌号cne-220;溴化三元乙丙橡胶为自制品(证明材料:王德志,曲春艳,张杨,等.三元乙丙橡胶粘接用胶黏剂的研制[j].化学与粘合,2006(3));固体丁腈橡胶生产厂家为南帝化工,牌号为1051;固体羧基丁腈橡胶厂家为南帝化工,牌号为1072;笼型聚倍半硅氧烷由哈尔滨工业大学提供;酚酞基聚芳醚酮(pek-c)生产厂家为黑龙江英创新材料有限公司;核-壳粒子生产厂家为日本钟渊化学工业公司,牌号为mx-125;双氰胺生产厂家为宁夏远大兴博化工有限公司;二氨基二苯砜生产厂家为河北冠朗生物科技有限公司;4-氨基-邻苯二甲酰亚胺生产厂家为上海源叶生物科技有限公司;硫磺粉生产厂家为天津市天力化学试剂有限公司;过氧化二异丙苯生产厂家为阿拉丁生化科技股份有限公司;氧化锌生产厂家为上海源叶生物科技有限公司;炭黑生产厂家为上海源叶生物科技有限公司。
[0054]
实施例二制备的复合材料预浸料与三元乙丙橡胶绝热层共固化粘接胶膜的厚度均一、具有良好的自粘性。采用该胶膜进行性能测试,测试结果如表2所示。
[0055]
表2实施例二制备的胶膜性能测试结果
[0056][0057]
实施例三:一种复合材料预浸料与三元乙丙橡胶绝热层共固化粘接胶膜的制备方法,是按以下步骤完成的:
[0058]
一、按照重量份数称取25份侧链含萘环结构的环氧树脂、9份通用型双酚a型环氧树脂、8份三官能团脂环族环氧树脂、22份溴化三元乙丙橡胶、4份固体丁腈橡胶、4份固体羧基丁腈橡胶、7份笼型聚倍半硅氧烷、3份聚砜(psf)、3份酚酞基聚芳醚酮(pek-c)、6份双氰胺、3份二氨基二苯砜、4份硫磺粉、2份过氧化二异丙苯、1份氧化锌、4份白炭黑和1份纳米级钛白粉;
[0059]
二、将25份侧链含萘环结构的环氧树脂、9份通用型双酚a型环氧树脂、8份三官能
团脂环族环氧树脂加入到反应釜中,然后将反应釜加热至240℃,再在搅拌状态下加入7份笼型聚倍半硅氧烷、3份聚砜(psf)、3份酚酞基聚芳醚酮(pek-c),最后在197℃下保温30min,制得均相共混树脂;
[0060]
三、采用机械共混法将步骤二制得的均相共混树脂与22份溴化三元乙丙橡胶、4份固体丁腈橡胶、4份固体羧基丁腈橡胶、6份双氰胺、3份二氨基二苯砜、4份硫磺粉、2份过氧化二异丙苯、1份氧化锌、4份白炭黑和1份纳米级钛白粉混合均匀,制得胶料;
[0061]
四、将步骤三制得的胶料在72℃的烘箱中预热28min,然后在辊温为78℃的压延机上压制成膜,即得到复合材料预浸料与三元乙丙橡胶绝热层共固化粘接胶膜。
[0062]
实施例二中使用的原料来源为:侧链含萘环结构的环氧树脂生产厂家为上海众司实业有限公司,牌号为nc-7300l;通用型双酚a型环氧树脂生产厂家为,牌号为e-51;三官能团脂环族环氧树脂由哈尔滨工业大学提供;溴化三元乙丙橡胶为自制品(证明材料:王德志,曲春艳,张杨,等.三元乙丙橡胶粘接用胶黏剂的研制[j].化学与粘合,2006(3));固体丁腈橡胶生产厂家为南帝化工,牌号为1051;固体羧基丁腈橡胶厂家为南帝化工,牌号为1072;笼型聚倍半硅氧烷由哈尔滨工业大学提供;聚砜(psf)生产厂家为大连聚砜塑料有限公司;酚酞基聚芳醚酮(pek-c)生产厂家为黑龙江英创新材料有限公司;双氰胺生产厂家为宁夏远大兴博化工有限公司;二氨基二苯砜生产厂家为河北冠朗生物科技有限公司;硫磺粉生产厂家为天津市天力化学试剂有限公司;过氧化二异丙苯生产厂家为阿拉丁生化科技股份有限公司;氧化锌生产厂家为上海源叶生物科技有限公司;白炭黑生产厂家为河北贞田食品添加剂有限公司;纳米级钛白粉生产厂家为郑州耀满化工有限公司。
[0063]
实施例三制备的复合材料预浸料与三元乙丙橡胶绝热层共固化粘接胶膜的厚度均一、具有良好的自粘性。采用该胶膜进行性能测试,测试结果如表3所示。
[0064]
表3实施例三制备的胶膜性能测试结果
[0065][0066]