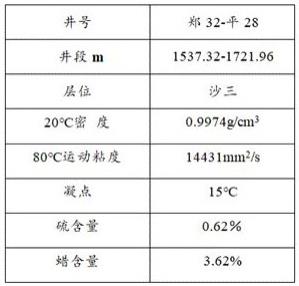
1.本技术涉及一种用于提高低渗透油藏注水效率的表面活性剂及制备方法与应用,属于油气田开采用表面活性剂技术领域。
背景技术:
2.低渗透油藏是指油层储层渗透率低、丰度低、单井产能低的油藏。在已探明的油藏储量中,低渗透油藏储量的比例很高,约占全国储量的2/3以上,达到50多亿吨,因此低渗透油藏在我国石油开发中有着重要意义,开发潜力巨大。低渗油藏相对于中高渗油藏,具有低渗透率、孔隙度小、粘土矿物类型多样且含量高、岩性致密及注水水质差(矿化度高、高钙镁)等特征,这些易导致油藏注水压力高、注入速率低、注水量不足等问题,水质二次污染使得油层遭到进一步伤害,常规的压裂酸化技术可以对低渗油藏改造起到一定作用,但作用范围和时间受限,表面活性剂降压增注技术以其独特的优越性越来越受到关注。
3.注入合适表面活性剂是解决残余油滴堵塞和低渗透孔隙水化膜阻力大的主要方法,其机理主要为通过降低油、水及岩石间的界面张力,降低原油在岩石表面的粘附力,改变岩石表面的润湿性,降低渗流阻力,改善两相渗流能力,提高水井注水能力,同时表面活性剂能清理部分粘附于井筒壁面和岩层表面的油污,从而增大渗流通道,实现水井的正常注水。但是由于影响注水开发效果的因素很多,而当前使用的化学体系性能比较单一,且使用浓度大,成本高,渗吸性不佳,往往达不到满意的效果。
技术实现要素:
4.为了解决上述问题,提供了一种用于提高低渗透油藏注水效率的表面活性剂及其制备方法与应用,该表面活性剂能够有效地降低注水井注水压力,避免对原油造成大量乳化引起注水压力升高,提高注井注水能力,改变岩石润湿性,降低毛管压力,抑制碳酸钙等碳酸盐沉淀对地层的伤害;同时能够有效的降低油水界面张力,具有优异的表面性能,有利于原油采收率的提高。
5.根据本技术的一个方面,提供了一种用于提高低渗透油藏注水效率的表面活性剂,按重量份数计,其包括:非离子型表面活性剂1-5份,阳离子型表面活性剂25-50份,其中,所述非离子型表面活性剂的分子式如式ⅰ所示:式ⅰ,所述r1、r2、r4、r6独立的选自含有1个碳原子至5个碳原子的具有直链或支链的烃基中的一种,所述r3、r5独立的选自含有6个碳原子至20个碳原子的具有直链或支链的烃基中的一种,所述m、n独立的选自1-20之间的整数;所述阳离子型表面活性剂的分子式如式ⅱ所示:
式ⅱ,所述r7、r8独立的选自含有1个碳原子至5个碳原子的具有直链或支链的烃基中的一种,所述r9、r
11
独立的选自含有1个碳原子至3个碳原子的直链烷基中的一种,所述r
10
选自含有1个碳原子至20个碳原子的具有直链或支链的烃基中的一种,所述x为cl或br。
6.可选地,按重量份数计,所述表面活性剂还包括0.01-10份的高分子表面活性剂,所述高分子表面活性剂的分子式如式ⅲ所示:式ⅲ,其中,所述r
12
选自含有8个碳原子至20个碳原子的具有直链或支链的烷基、环烷基、烯基或芳香基中的一种,所述r
13
选自甲基、乙基和丙基中的一种,所述r
14
选自含有0个碳原子至5个碳原子的直链烃基中的一种,所述m选自硫酸根、羧酸根和磺酸根中的一种,所述p、q独立的选自1-500之间的整数。
7.可选地,所述r
12
选自含有8个碳原子至18个碳原子的具有直链或支链的烷基、环烷基、烯基或芳香基中的一种,所述r
13
为甲基,所述r
14
选自含有0个碳原子至3个碳原子的直链烃基中的一种,所述p、q独立的选自1-50之间的整数,所述m为钠盐、钾盐和铵盐中的一种;更优选的,所述r
12
为含有12个碳原子的烷基,所述r
14
为含有0个碳原子的烃基,所述p为30,所述q为30,所述m为-so3na。
8.可选地,式ⅰ中,所述r1、r2、r4、r6均为乙基,所述r3、r5独立的选自含有8个碳原子至12个碳原子的具有直链或支链的烃基中的一种,所述m、n独立的选自1-20之间的整数;优选的,所述r3、r5相同,所述m、n相同;更优选的,所述r3、r5均为含有10个碳原子的烷基,所述m、n均为10。
9.可选地,式ⅱ中,所述r7选自含有1个碳原子至3个碳原子的具有直链或支链的烃基中的一种,所述r8选自含有3个碳原子至5个碳原子的具有直链或支链的烃基中的一种,所述r9、r
11
相同,所述r
10
选自含有1个碳原子至15个碳原子的具有直链或支链的烃基中的一种,所述x为cl或br。
10.优选的,所述r7为甲基,所述r8为正丁基,所述r9、r
11
均为甲基,所述r
10
为含有12个碳原子的烷基,所述x为br;可选地,所述阳离子型表面活性剂的合成路线为:
;优选的,以丙二酸二甲酯与n,n-二甲基-1,4-丁二胺为原料合成双(4-二甲基氨基丁基)丙二酰胺;然后将所述双(4-二甲基氨基丁基)丙二酰胺与溴代十二烷季铵化反应得到含酰胺基的季铵盐型双子表面活性剂混合物,用丙酮重结晶,得到所述阳离子型表面活性剂。
11.可选地,按重量份数计,所述表面活性剂包括溶剂,所述溶剂包括20-60份的水和0.01-10份的含有1个碳原子至8个碳原子的低分子醇。
12.优选的,所述低分子醇为乙醇、乙二醇和异丙醇中的至少一种,更优选为乙醇。
13.可选地,按重量份数计,其包括:非离子型表面活性剂2份,阳离子型表面活性剂38份。
14.优选的,按重量份数计,其包括非离子型表面活性剂2份,阳离子型表面活性剂38份、高分子表面活性剂5份、水40份、低分子醇10份。
15.根据本技术的另一个方面,提供了一种用于制备上述任一项所述的表面活性剂的方法,其包括以下步骤:在20-50℃下,将所述非离子型表面活性剂、阳离子型表面活性剂和水搅拌不低于1h后,制得所述表面活性剂。
16.优选的,所述方法包括以下步骤:在常压条件下,向反应釜中加入水,30-40℃下搅拌;向所述反应釜中加入所述高分子表面活性剂,搅拌1-3h,混合均匀;向所述反应釜中加入所述非离子型表面活性剂和所述阳离子型表面活性剂,搅拌0.5-2h,混合均匀;向所述反应釜中加入所述低分子醇,在30-40 ℃的条件下搅拌0.5-2h,混合均匀,制得所述表面活性剂。
17.根据本技术的又一个方面,提供了一种上述任一项所述的表面活性剂或上述所述的方法制得的表面活性剂在提高低渗透油层注水效率中的应用,所述低渗透油藏的渗透率不高于50
×
10-3
μm2。
18.本技术的有益效果包括但不限于:1.根据本技术的表面活性剂,能够有效地降低注水井注水压力,避免对原油造成大量乳化引起注水压力升高,提高注井注水能力,改变岩石润湿性,降低毛管压力,抑制碳酸钙等碳酸盐沉淀对地层的伤害;同时能够有效的降低油水界面张力,具有优异的表面性能,有利于原油采收率的提高。
19.2.根据本技术的表面活性剂,通过加入双子阳离子型表面活性剂,其注入地层后,依靠离子间静电相互作用,在油膜局部脱落的岩石表面上吸附,降低原油在岩石表面的粘附力,改变岩石表面的润湿性,降低渗流阻力,从岩石表面剥离下的原油在表面活性剂作用下分散为小的油滴,提高原油通过喉道的流动能力,从而提高储层渗透率,疏通地层恢复油井供液能力,实现水井的正常注水,且双子阳离子型表面活性剂具有生物降解性好、低毒性、高活性、疏水性强、对地层矿物吸附性好等优点;此外,羰基的存在具有较强的吸电子性,可以减少地层阳离子对该表面活性剂的消耗,使其耐盐性好,可以用于矿化度较大的地层中;通过加入非离子型表面活性剂,可以增加该表面活性剂体系的亲水性,同时因为位阻效应减弱了各个表面活性剂之间的强烈相互作用,以避免表面活性剂的液晶化及沉淀等现象的发生,提高了该表面活性剂体系的稳定性;此外,通过控制非离子表面活性剂的支链,该长链侧基能够在原油中形成疏水缔合,提高该表面活性剂的耐温性,使其具有抗高温性能。
20.3.根据本技术的表面活性剂,通过加入高分子表面活性剂,由于储层岩石表面带有负电荷,高分子表面活性剂可以依靠静电引力吸附在储层岩石表面自组装形成超薄膜,扩大有效渗流通道,改变岩石表面润湿性,降低注水摩阻及原油开采阻力,不仅能够实现注水井近端减阻增注,还可以达到远端驱油增注的效果。
21.4.根据本技术的表面活性剂的制备方法,步骤简单环保,条件温和,适于工业化生产。
具体实施方式
22.下面结合实施例详述本技术,但本技术并不局限于这些实施例。
23.如无特别说明,本技术的实施例中的原料和催化剂均通过商业途径购买。
24.实施例1 表面活性剂1#(1)以26.4g丙二酸二甲酯与46.4g n,n-二甲基-1,4-丁二胺为原料,加入1.5g甲酸钠在100℃条件下反应24h,反应完全后滴加2.5ml乙酸搅拌1h,冷却得到淡黄色固体,在105℃烘箱中烘干得到双(4-二甲基氨基丁基)丙二酰胺粗品;称取29.6g双(4-二甲基氨基丁基)丙二酰胺粗品与50.0g溴代十二烷在50℃条件下反应得到含酰胺基的季铵盐型双子表面活性剂混合物,用丙酮重结晶,得到阳离子型表面活性剂1#。
25.(2)向反应釜内加入40.0g水,30-40℃下边搅拌边加入5.0g高分子表面活性剂,搅拌2h;再加入2.0g非离子型表面活性剂及38.0g阳离子型表面活性剂1#,搅拌1h后,加入10.0g乙醇,继续搅拌1h,混合均匀后,得到表面活性剂1#;其中,非离子型表面活性剂的分子式如下:,r1、r2、r4及r6均为乙基,r3、r5均为正十烷基,m、n均为10;高分子表面活性剂的分子式如下:
,r
12
为正十二烷基,r
13
为甲基,r
14
为含有0个碳原子的烃基,m为-so
3-,p为30、q为30。
26.实施例2 表面活性剂2#实施例2与实施例1的不同之处在于:步骤(2)中,向反应釜内加入40.0g水,30-40℃下边搅拌边加入5.0g高分子表面活性剂,搅拌2h;再加入5.0g非离子型表面活性剂及35.0g阳离子型表面活性剂1#,搅拌1h后,加入10.0g乙醇,继续搅拌1h,混合均匀后,得到表面活性剂2#;其余条件与实施例1相同。
27.实施例3 表面活性剂3#实施例3与实施例1的不同之处在于:步骤(2)中,向反应釜内加入40.0g水,30-40℃下边搅拌边加入2.0g高分子表面活性剂,搅拌2h;再加入5.0g非离子型表面活性剂及38.0g阳离子型表面活性剂1#,搅拌1h后,加入10.0g乙醇,继续搅拌1h,混合均匀后,得到表面活性剂3#;其余条件与实施例1相同。
28.实施例4 表面活性剂4#实施例4与实施例1的不同之处在于:步骤(2)中,向反应釜内加入40.0g水,30-40℃下边搅拌边加入5.0g非离子型表面活性剂及40.0g阳离子型表面活性剂1#,搅拌1h后,加入10.0g乙醇,继续搅拌1h,混合均匀后,得到表面活性剂4#;其余条件与实施例1相同。
29.实施例5 表面活性剂5#实施例5与实施例1的不同之处在于:向反应釜内加入40.0g水,30-40℃下边搅拌边加入10.0g高分子表面活性剂,搅拌2h;再加入2.0g非离子型表面活性剂及33.0g阳离子型表面活性剂1#,搅拌1h后,加入10.0g乙醇,继续搅拌1h,混合均匀后,得到表面活性剂5#;其余条件与实施例1相同。
30.实施例6 表面活性剂6#实施例6与实施例1的不同之处在于:步骤(2)中,向反应釜内加入40.0g水,30-40℃下边搅拌边加入5.0g高分子表面活性剂,搅拌2h;再加入2.0g非离子型表面活性剂及38.0g阳离子型表面活性剂1#,搅拌1h后,加入10.0g乙醇,继续搅拌1h,混合均匀后,得到表面活性剂6#;其余条件与实施例1相同,其中,非离子型表面活性剂的分子式如下:,r1、r2、r4及r6均为乙基,r3、r5均为正十烷基,m、n均为10;高分子表面活性剂的分子式如下:
,r
12
为正十二烷基苯基,r
13
为甲基,r
14
为正丙基,m为羧酸钾,即-coo-,p为30、q为30。
31.实施例7 表面活性剂7#实施例7与实施例1的不同之处在于:步骤(2)中,向反应釜内加入40.0g水,30-40℃下边搅拌边加入5.0g高分子表面活性剂,搅拌2h;再加入2.0g非离子型表面活性剂及38.0g阳离子型表面活性剂1#,搅拌1h后,加入10.0g乙醇,继续搅拌1h,混合均匀后,得到表面活性剂7#;其余条件与实施例1相同,其中,非离子型表面活性剂的分子式如下:,r1为乙基,r2为乙基,r3为正十烷基,r4为正丙基,r5为正十八烷基,r6均为乙基,m为10,n为10;高分子表面活性剂的分子式如下:,r
12
为正十二烷基,r
13
为甲基,r
14
为含有0个碳原子的烃基,m为-so
3-,p为30、q为30。
32.实施例8 表面活性剂8#实施例8与实施例1的不同之处在于:步骤(1)中,以34.8g己二酸二甲酯与46.4g n,n-二甲基-1,4-丁二胺为原料,加入1.5g甲酸钠在100℃条件下反应24h,反应完全后滴加2.5ml乙酸搅拌1h,冷却得到淡黄色固体,在105℃烘箱中烘干得到双(4-二甲基氨基丁基)己二酰胺粗品;称取34.6g双(4-二甲基氨基丁基)己二酰胺粗品与50.0g溴代十二烷在50℃条件下反应得到含酰胺基的季铵盐型双子表面活性剂混合物,用丙酮重结晶,得到阳离子型表面活性剂2#。
33.步骤(2)中,向反应釜内加入40.0g水,30-40℃下边搅拌边加入5.0g高分子表面活性剂,搅拌2h;再加入2.0g非离子型表面活性剂及38.0g阳离子型表面活性剂2#,搅拌1h后,加入10.0g乙醇,继续搅拌1h,混合均匀后,得到表面活性剂8#;其余条件与实施例1相同。
34.实施例9 表面活性剂9#实施例9与实施例1的不同之处在于:步骤(2)中,高分子表面活性剂的分子式为:,r
15
为正十二烷基,r
14
为正丙基,m为-so
3-,x为60,得到表面活性剂9#;其余条件与实施例1相同。
35.对比例1 表面活性剂d1#对比例1与实施例1的不同之处在于:步骤(2)中,向反应釜内加入40.0g水,30-40℃下边搅拌边加入6.0g高分子表面活性剂,搅拌2h;再加入39.0g阳离子型表面活性剂1#,搅拌1h后,加入10.0g乙醇,继续搅拌1h,混合均匀后,得到表面活性剂d1#;其余条件与实施例1相同。
36.对比例2 表面活性剂d2#对比例2与实施例1的不同之处在于:步骤(2)中,向反应釜内加入40.0g水,30-40℃下边搅拌边加入19.0g高分子表面活性剂,搅拌2h;再加入16.0g非离子型表面活性剂及10.0g阳离子型表面活性剂1#,搅拌1h后,加入10.0g乙醇,继续搅拌1h,混合均匀后,得到表面活性剂d2#;其余条件与实施例1相同。
37.对比例3 表面活性剂d3#对比例3与实施例1的不同之处在于:步骤(2)中,非离子型表面活性剂的分子式为:,r
16
为乙基,r
17
为正十烷基,r
18
为乙基,y为20(实施例1中的m和n之和),得到表面活性剂d3#;其余条件与实施例1相同。。
38.对比例4 表面活性剂d4#对比例4与实施例1的不同之处在于:步骤(1)中,以26.4g丙酸甲酯与46.4g n,n-二甲基-1,4-丁二胺为原料,加入1.5g甲酸钠在100℃条件下反应24h,反应完全后滴加2.5ml乙酸搅拌1h,冷却得到淡黄色固体,在105℃烘箱中烘干得到(4-二甲基氨基丁基)丙酰胺粗品;称取29.6g(4-二甲基氨基丁基)丙酰胺粗品与25.0g溴代十二烷在50℃条件下反应得到含酰胺基的季铵盐型表面活性剂混合物,用丙酮重结晶,得到阳离子型表面活性剂d1#。
39.步骤(2)中,向反应釜内加入40.0g水,30-40℃下边搅拌边加入5.0g高分子表面活性剂,搅拌2h;再加入2.0g非离子型表面活性剂及38.0g阳离子型表面活性剂d1#,搅拌1h后,加入10.0g乙醇,继续搅拌1h,混合均匀后,得到表面活性剂d4#;其余条件与实施例1相同。
40.实验例1 表面活性剂的表面张力、界面张力、洗油率、采油率及降压率的测定取实施例1-9、对比例1-4制得的表面活性剂1#-9#、表面活性剂d1#-d4#,分别用蒸馏水配置质量浓度为0.3wt%的溶液,分别测试各个表面活性剂的表面张力、界面张力、洗油率、降压率和采油率,测试结果如表1所述,测试方法如下:表面张力:按照q/sh1020 2252-2019降压增注用表面活性剂技术要求的测试方法,在测试温度为25℃下使用jyw-200b全自动界面张力仪测定其表面张力。
41.界面张力:按照q/sh1020 2252-2019降压增注用表面活性剂技术要求的测试方法,在测试温度为70℃下使用tx-500c型界面张力仪测定油水界面张力;洗油率:以郑32-平28原油为测试用油样,按照q/sh1020 2252-2019降压增注用表面活性剂技术要求的测试方法,测试其洗油率。郑32-平28原油物性信息见下表:表1
降压率:以郑32-平28为测试用油样,按照q/sh1020 2252-2019降压增注用表面活性剂技术要求的测试方法,测试其降压率。
42.采收率:在长度为30cm、直径为2.5cm、渗透率为1.5μm2的岩心上进行驱油试验,先用胜利油田地层水驱至含水92%,转注表面活性剂溶液(0.4pv)进行驱替,气驱至累计气驱量大于1.2pv时,停止驱替,接着水驱至含水100%,分别计算提高的采收率。
43.表2由表2可以看出,本发明的表面活性剂能够显著降低油水界面张力,降低注水压
力,提高洗油率,进而大大提高了原油采收率。
44.实验例2 表面活性剂耐盐性、耐温性的测定取实施例1-9、对比例1-4制得的表面活性剂1#-9#、表面活性剂d1#-d4#,分别用蒸馏水配置质量浓度为0.3wt%的溶液,分别测试各个表面活性剂溶液的耐盐性及耐温性,测试结果如表2所述,测试方法如下:耐盐性:按照q/sh1020 2252-2019降压增注用表面活性剂技术要求的测试方法,配置40000mg/l和80000mg/l标准盐水,分别用40000mg/l和80000g/l标准盐水配置0.3 wt%的表面活性剂溶液,使用tx-500c型界面张力仪测定油水界面张力,使用jyw-200b全自动界面张力仪测定其表面张力,其中,界面张力测试温度为70 ℃,表面张力测试温度为25℃。
45.耐温性:按照q/sh1020 2252-2019降压增注用表面活性剂技术要求的测试方法,用蒸馏水配置 0.3 wt%的表面活性剂溶液,装入耐温耐压容器中,上紧螺纹,密封放于130℃烘箱中,恒温48 h后,取出冷却至室温,使用jyw-200b全自动界面张力仪测定其表面张力。
46.表3由表3可以看出,本发明制备的表面活性剂耐盐性良好,适用于矿化度较大的地层中,且耐温性能佳,在油藏地层温度下性能稳定。
47.以上所述,仅为本技术的实施例而已,本技术的保护范围并不受这些具体实施例的限制,而是由本技术的权利要求书来确定。对于本领域技术人员来说,本技术可以有各种更改和变化。凡在本技术的技术思想和原理之内所作的任何修改、等同替换、改进等,均应包含在本技术的保护范围之内。