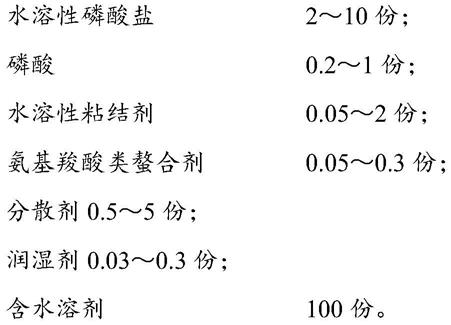
1.本发明属于涂料领域,尤其是一种高耐腐蚀性的环保涂料及其制备方法。
背景技术:
2.大多数金属材料(如铁、铝、铜等)化学性质比较活泼,具有较强的还原性。长期暴露于潮湿环境中,金属材料会缓慢与空气中的水分和氧气发生反应,从而生锈。同时,金属材料的耐酸性较差,极易被酸性介质腐蚀。如何提高金属制品的耐腐蚀性,一直困扰着金属市场的各级制造厂商。
3.现阶段,常见的防腐蚀技术为以下三种方案:一是通过电镀、喷镀或合金化处理的方式,在金属基材覆盖一层耐腐蚀性的金属或金属合金,但此种方式形成的金属镀层与金属基材的牢固性偏低,覆盖层疏松,且存在较大的环保问题;二是在金属制品原材料中添加缓蚀填料,当遇空气中水、氧气或酸碱性介质时,缓蚀填料优先发生作用,从而降低腐蚀速率,但缓蚀填料的添加,往往会降低金属制品本身的理化性能,大大降低金属制品的应用效果;三是通过浸渍、喷涂或辊涂工艺,在金属表面涂布一层耐腐蚀涂料,耐腐蚀涂料固化后在金属表面形成一层保护膜,从而达到耐腐蚀效果,此种方式形成的保护膜与金属基材牢固度高,致密性好,且不会改变金属本身的理化性能,从而受到行业越来越多的关注。
4.已经市场化的耐腐蚀性金属表面涂料,主要包括铬酸盐体系、磷酸盐体系、钼酸盐体系、硅酸盐体系,以及稀土金属盐体系。其中,铬酸盐体系耐腐蚀涂料形成的涂层中,铬主要以三价铬和六价铬的形式存在,三价铬作为主体,六价铬起到自修复功能,耐腐蚀性最好,但六价铬具有极高的毒性和致癌性,从而使铬酸盐体系的使用受到严格的限制。磷酸盐体系、钼酸盐体系、硅酸盐体系和稀土金属盐体系的耐腐蚀涂料,无毒,具有良好的环境友好性,但其涂层与铬酸盐体系相比,闭孔性较差,存在一定程度的微孔,且易开裂,对水分和酸性介质的阻隔性相对较低,使耐腐蚀性大大降低。
技术实现要素:
5.为了克服上述技术缺陷,本发明提供一种高耐腐蚀性的环保涂料及其制备方法,以解决背景技术所涉及的问题。
6.本发明提供一种高耐腐蚀性的环保涂料,以质量份数计,所述环保涂料包括:
7.[0008][0009]
优选地或可选地,所述纳米级金属氧化物为mno2、ceo2、tio2、zro2、sro、bao中的一种或几种的组合。
[0010]
更优选地,所述纳米级金属氧化物为ceo2。
[0011]
更优选地,所述纳米级金属氧化物所占含水溶剂的质量比为2%~5%。
[0012]
优选地或可选地,所述水溶性磷酸盐为正磷酸的钠盐、正磷酸的钾盐、缩聚磷酸的钠盐、缩聚磷酸的钾盐中的一种或几种的组合。
[0013]
更优选地,所述水溶性磷酸盐为缩聚磷酸的钠盐。
[0014]
更优选地,所述水溶性磷酸盐所占含水溶剂的质量比为4%~8%。
[0015]
更优选地,所述磷酸所占含水溶剂的质量比为0.2%~0.5%。
[0016]
优选地或可选地,所述水溶性粘结剂为聚乙烯醇类水性粘结剂、乙烯乙酸酯类水性粘结剂、丙烯酸类水性粘结剂、聚氨酯类水性粘结剂、环氧水性粘结剂、酚醛水性粘结剂、有机硅类水性粘结剂中的一种或几种的组合。
[0017]
更优选地,所述水溶性粘结剂为丙烯酸类水性粘结剂。
[0018]
更优选地,所述水溶性粘结剂所占纳米级金属氧化物的质量比为5%~20%。
[0019]
优选地或可选地,所述氨基羧酸类螯合剂为乙二胺四乙酸(edta)、氨基三乙酸(nta)、二亚乙基三胺五乙酸(dtpa)及其盐中的一种或几种的组合。
[0020]
更优选地,所述氨基羧酸类螯合剂为乙二胺四乙酸(edta)及其盐。
[0021]
更优选地,所述氨基羧酸类螯合剂所占含水溶剂的质量比为0.1%~0.2%。
[0022]
优选地或可选地,所述分散剂为三聚磷酸钠、六偏磷酸钠、三乙基己基磷酸、十二烷基硫酸钠、聚丙烯酰胺、脂肪酸聚乙二醇酯中的一种或几种的组合。
[0023]
更优选地,所述分散剂为六偏磷酸钠。
[0024]
更优选地,所述分散剂所占含水溶剂的质量比为0.5%~5%。
[0025]
优选地或可选地,所述润湿剂为聚醚改性聚有机硅氧烷、十二烷基硫酸钠、十二烷基磺酸钠、聚氧乙烯烷基酚醚、聚氧乙烯脂肪醇醚中的一种或几种的组合。
[0026]
更优选地,所述润湿剂为聚醚改性聚有机硅氧烷。
[0027]
更优选地,所述润湿剂所占含水溶剂的质量比为0.03%~0.3%。
[0028]
优选地或可选地,所述含水溶剂为含水的甲醇溶剂。
[0029]
更优选地,所述含水溶剂中甲醇所占纯水的质量比为10%~30%。
[0030]
本发明还提供一种高耐腐蚀性的环保涂料的制备方法,包括如下步骤:
[0031]
将甲醇、水溶性磷酸盐、磷酸、分散剂依次加入预先注入水的搅拌釜中,以第一搅
拌速度搅拌第一时长得到混合溶液;
[0032]
向所述第一混合溶液中,加入纳米级金属氧化物,以第二搅拌速度搅拌第二时长,得到第一混合浆料;
[0033]
向所述混合浆料中,依次加入氨基羧酸类螯合剂、水溶性粘结剂、润湿剂,以第三搅拌速度搅拌第三时长得到第二混合浆料;
[0034]
所述第二混合浆料经过滤网过滤,即得到一种高耐腐蚀性的环保涂料。
[0035]
优选地或可选地,所述第一搅拌速度在100rpm~300rpm之间;所述第一时长在15min~30min之间;
[0036]
所述第二搅拌速度在1000rpm~2000rpm之间;所述第二时长在60min~90min之间;
[0037]
所述第三搅拌速度在100rpm~300rpm之间;所述第三时长在15min~30min之间;
[0038]
所述过滤网目数在200目~400目之间。
[0039]
本发明涉及一种高耐腐蚀性的环保涂料及其制备方法,相较于现有技术,具有如下有益效果:
[0040]
1、在磷酸盐体系耐腐蚀涂料的基础上,通过将纳米级金属氧化物均匀分散于涂料中,使其兼具磷酸盐体系耐腐蚀涂料和金属氧化物涂层的双重作用,在金属制品表面优先形成磷化膜,在磷化膜表面再生成纳米级金属氧化物涂层。纳米级金属氧化物可沉积于磷化膜的微孔或裂缝中,起到封孔的作用,从而大大提高了金属制品对水分和酸性介质的耐腐蚀效果。
[0041]
2、本发明通过加入水性粘结剂,保证了涂料固化后纳米级金属氧化物对磷化膜的附着性。
[0042]
3、本发明通过采用含水的甲醇溶剂和润湿剂,可明显增加金属制品的表面张力,保证了涂料在涂布于金属制品表面时,对金属制品的充分润湿性。
[0043]
4、本发明选用的金属氧化物用作为防腐蚀涂料中的填充粒子,由于金属氧化物mno2、ceo2、tio2、zro2、sro、bao具有高的氧化点位,不会与空气中水分和氧气发生反应,且能与磷酸和磷酸盐保持良好的化学惰性。
[0044]
5、本发明的水溶性磷酸盐通过化学和电化学反应,可在金属制品表面形成一种惰性的磷化膜,从而阻隔空气中水分和酸性介质的腐蚀。尤其是,缩合磷酸盐具有很强的螯合效应,与金属离子作用后,产生凝胶现象,使涂层的牢固度增强,且涂层自身不易开裂。
[0045]
6、本发明通过分散剂将所述纳米级金属氧化物以微粒的形式分散于含水溶剂中,形成均相体系。
[0046]
7、本发明的制备方法通过选用多个不同的搅拌速度和搅拌时间,大大提高了环保涂料的稳定性。
[0047]
综上,本发明涉及高耐腐蚀性的环保涂料,大大提高了对金属制品对水分和酸性介质的耐腐蚀效果。另外,由于采用无铬体系,确保环境友好性。
附图说明
[0048]
图1是本发明的环保涂料固化后涂层示意图。
[0049]
附图标记为:纳米金属氧化物1、磷化膜2、金属制品3。
具体实施方式
[0050]
在下文的描述中,给出了大量具体的细节以便提供对本发明更为彻底的理解。然而,对于本领域技术人员而言显而易见的是,本发明可以无需一个或多个这些细节而得以实施。在其他的例子中,为了避免与本发明发生混淆,对于本领域公知的一些技术特征未进行描述。
[0051]
发明概述
[0052]
磷酸盐体系涂料与铬酸盐体系涂料相比,闭孔性较差,存在一定程度的微孔,且易开裂,对水分和酸性介质的阻隔性相对较低,使耐腐蚀性大大降低。鉴于以上所述现有技术存在的不足,本发明的目的在于提供一种高耐腐蚀性的环保涂料及其制备方法,在基于环境友好的基础上,赋予金属制品优异的水分阻隔性和耐酸性性能。
[0053]
本发明所述一种高耐腐蚀性的环保涂料,其组成包括纳米级金属氧化物、水溶性磷酸盐、磷酸、水溶性粘结剂、氨基羧酸类螯合剂、分散剂、润湿剂以及含水溶剂。其中,所述纳米级金属氧化物为过渡金属氧化物或稀土金属氧化物;所述纳米级金属氧化物以微粒的形式分散于含水溶剂中,形成均相体系;所述含水溶剂为含水的甲醇溶剂。由于所述环保涂料采用无铬体系,确保环境友好性,同时,在磷酸盐体系耐腐蚀涂料的基础上,通过将纳米级金属氧化物均匀分散于涂料中,使其兼具磷酸盐体系耐腐蚀涂料和金属氧化物涂层的双重作用,在金属制品表面优先形成磷化膜,在磷化膜表面再生成纳米级金属氧化物涂层。当外界水分和酸性介质侵入时,纳米级金属氧化物涂层起到第一层防护的作用,将大部分水分和酸性介质阻隔在外侧;磷化膜起到第二层防护的作用,可将透过纳米级金属氧化物涂层的少量水分和酸性介质完全的阻隔;进一步的,纳米级金属氧化物可沉积于磷化膜的微孔或裂缝中,起到封孔的作用,从而大大提高了金属制品对水分和酸性介质的耐腐蚀效果。本发明通过加入水性粘结剂,保证了涂料固化后纳米级金属氧化物对磷化膜的附着性。本发明通过采用含水的甲醇溶剂和润湿剂,可明显增加金属制品的表面张力,保证了涂料在涂布于金属制品表面时,对金属制品的充分润湿性。
[0054]
下面结合实施例,对本发明作进一步说明,所述的实施例的示例旨在解释本发明,而不能理解为对本发明的限制。
[0055]
实施例1
[0056]
向搅拌釜中注入定量的纯水,向纯水中加入所占纯水质量比10%的甲醇,得到含水的甲醇溶剂,向溶剂中加入所占溶剂质量比2%的三聚磷酸钠,向溶剂中加入所占溶剂质量比0.2%的磷酸,向溶剂中加入所占溶剂质量比0.5%的六偏磷酸钠,以第一搅拌速度100rpm和第一时长15min进行搅拌分散;向溶剂中加入所占溶剂质量比1%的纳米级mno2,以第二搅拌速度1000rpm和第二时长60min进行搅拌分散;向溶剂中加入所占溶剂质量比0.05%的edta,向溶剂中加入所占纳米级mno2质量比5%的丙烯酸类水性粘结剂,向溶剂中加入所占溶剂质量比0.03%的十二烷基硫酸钠,以第三搅拌速度100rpm和第三时长15min进行搅拌分散;将上述所得涂料经200目过滤网过滤,即得到一种高耐腐蚀性的环保涂料。
[0057]
实施例2
[0058]
向搅拌釜中注入定量的纯水,向纯水中加入所占纯水质量比30%的甲醇,得到含水的甲醇溶剂,向溶剂中加入所占溶剂质量比10%的三聚磷酸钠,向溶剂中加入所占溶剂质量比1%的磷酸,向溶剂中加入所占溶剂质量比5%的十二烷基硫酸钠,以第一搅拌速度
300rpm和第一时长30min进行搅拌分散;向溶剂中加入所占溶剂质量比8%的纳米级ceo2,以第二搅拌速度2000rpm和第二时长90min进行搅拌分散;向溶剂中加入所占溶剂质量比0.3%的nta,向溶剂中加入所占纳米级ceo2质量比20%的聚乙烯醇水性粘结剂,向溶剂中加入所占溶剂质量比0.3%的聚氧乙烯烷基酚醚,以第三搅拌速度300rpm和第三时长30min进行搅拌分散;将上述所得涂料经400目过滤网过滤,即得到一种高耐腐蚀性的环保涂料。
[0059]
实施例3
[0060]
向搅拌釜中注入定量的纯水,向纯水中加入所占纯水质量比20%的甲醇,得到含水的甲醇溶剂,向溶剂中加入所占溶剂质量比5%的三聚磷酸钠,向溶剂中加入所占溶剂质量比0.5%的磷酸,向溶剂中加入所占溶剂质量比3%的六偏磷酸钠,以第一搅拌速度200rpm和第一时长25min进行搅拌分散;向溶剂中加入所占溶剂质量比5%的纳米级ceo2,以第二搅拌速度1500rpm和第二时长75min进行搅拌分散;向溶剂中加入所占溶剂质量比0.15%的edta,向溶剂中加入所占纳米级ceo2质量比12%的丙烯酸类水性粘结剂,向溶剂中加入所占溶剂质量比0.15%的聚醚改性聚有机硅氧烷,以第三搅拌速度200rpm和第三时长25min进行搅拌分散;将上述所得涂料经300目过滤网过滤,即得到一种高耐腐蚀性的环保涂料。
[0061]
实施例4
[0062]
向搅拌釜中注入定量的纯水,向纯水中加入所占纯水质量比20%的甲醇,得到含水的甲醇溶剂,向溶剂中加入所占溶剂质量比5%的磷酸氢钾,向溶剂中加入所占溶剂质量比0.5%的磷酸,向溶剂中加入所占溶剂质量比3%的三乙基己基磷酸,以第一搅拌速度150rpm和第一时长15min进行搅拌分散;向溶剂中加入所占溶剂质量比5%的纳米级tio2,以第二搅拌速度1500rpm和第二时长75min进行搅拌分散;向溶剂中加入所占溶剂质量比0.15%的dtpa,向溶剂中加入所占纳米级tio2质量比10%的聚乙烯醇水性粘结剂,向溶剂中加入所占溶剂质量比0.15%的聚醚改性聚有机硅氧烷,以第三搅拌速度150rpm和第三时长15min进行搅拌分散;将上述所得涂料经200目过滤网过滤,即得到一种高耐腐蚀性的环保涂料。
[0063]
实施例5
[0064]
向搅拌釜中注入定量的纯水,向纯水中加入所占纯水质量比20%的甲醇,得到含水的甲醇溶剂,向溶剂中加入所占溶剂质量比5%的磷酸氢钾,向溶剂中加入所占溶剂质量比0.5%的磷酸,向溶剂中加入所占溶剂质量比3%的六偏磷酸钠,以第一搅拌速度200rpm和第一时长25min进行搅拌分散;向溶剂中加入所占溶剂质量比5%的纳米级ceo2,以第二搅拌速度1500rpm和第二时长75min进行搅拌分散;向溶剂中加入所占溶剂质量比0.15%的edta,向溶剂中加入所占纳米级ceo2质量比12%的丙烯酸类水性粘结剂,向溶剂中加入所占溶剂质量比0.15%的聚醚改性聚有机硅氧烷,以第三搅拌速度200rpm和第三时长25min进行搅拌分散;将上述所得涂料经300目过滤网过滤,即得到一种高耐腐蚀性的环保涂料。
[0065]
对比例1
[0066]
对比例1与实施例1的唯一区别在于,对比例1所述涂料中不添加纳米级金属氧化物mno2,其他物料的种类、比例以及涂料的制备方法,与实施例1完全一样。
[0067]
对比例2
[0068]
对比例2与实施例3的唯一区别在于,对比例2所述涂料中不添加甲醇,其他物料的
种类、比例以及涂料的制备方法,与实施例3完全一样。
[0069]
检测例
[0070]
使用上述实施例1
‑
4和对比例1
‑
2得到的涂料对铝制品表面进行处理,待涂料完全固化后,对所得铝制品进行耐腐蚀评价。
[0071]
耐酸性介质评价:将处理后的铝制品置于15l的密闭不锈钢桶中,不锈钢桶中预先准备有50ml浓度为0.01mol/l的盐酸溶液,将不锈钢桶放置在60℃恒温干燥箱中,保留时间为1周、2周、4周和9周,目视铝制品表面是否被腐蚀。
[0072]
耐高温高湿评价:将处理后的铝制品置于60℃、90%rh的恒温恒湿试验箱中,保留时间分别为1周、2周、4周和9周,目视铝制品表面是否被腐蚀。
[0073]
耐纯水浸泡评价:将处理后的铝制品置于50℃的恒温水浴中,保留时间分别为1周、2周、4周和9周,目视铝制品表面是否被腐蚀。
[0074]
评价结果如表1所示。
[0075][0076][0077]
注::表面未腐蚀;:表面轻微腐蚀;:表面严重腐蚀。
[0078]
由评价结果可见,本发明实施例的一种高耐腐蚀性的环保涂料,可显著提高金属制品对水分和酸性介质的耐腐蚀效果。
[0079]
另外需要说明的是,在上述具体实施方式中所描述的各个具体技术特征,在不矛盾的情况下,可以通过任何合适的方式进行组合。为了避免不必要的重复,本发明对各种可能的组合方式不再另行说明。