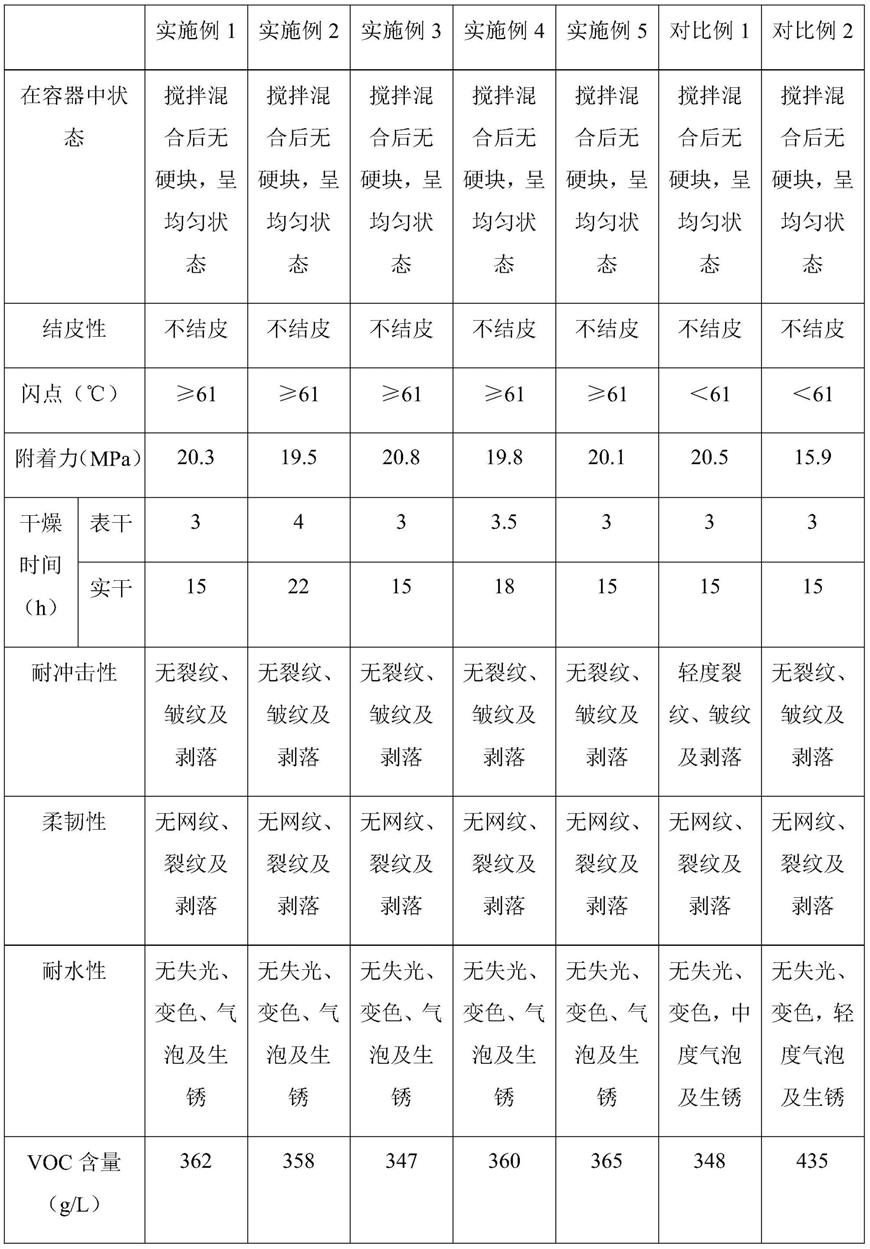
1.本发明涉及防腐涂料技术领域,具体为一种环境友好型高闪点酚醛防腐涂料及其制备工艺。
背景技术:
2.传统的酚醛树脂涂料,以酚醛树脂为主要成膜物质,配以200#溶剂油、颜填料、催干剂组成,存在以下不足:产品闪点低,安全性低,在生产、经营、运输、储存和使用过程中对相关生产设施、经营许可、车辆运输工具、仓库储存设施及施工管理都有严格法规要求。传统酚醛树脂涂料,为满足施工条件,需大量采用有机溶剂进行稀释,所以voc含量高,用户后期环保处理费用及压力大。传统酚醛树脂涂料,耐水性好但耐候性差,不能适应户外轻防腐涂装的需求。
技术实现要素:
3.本发明的目的在于提供一种环境友好型高闪点酚醛防腐涂料及其制备工艺,以解决上述背景技术中提出的问题。
4.为了解决上述技术问题,本发明提供如下技术方案:
5.包括以下步骤:
6.s1:原料制备:
7.a:在甲醛溶液中缓慢加入硫酸,温度保持在40℃以下,混合均匀后加入二甲苯,在70
‑
80℃下反应8
‑
9h,静置15
‑
30min,去除下层溶液,用水洗涤至中性,对产物进行抽真空直至无脱出物,冷却至室温,加入苯酚,温度达到40
‑
50℃时,加入盐酸,升温,40min内温度达到65℃,75min内温度达到93℃,沸腾反应15
‑
35min,95℃下再反应20
‑
30min,快速冷却至40
‑
45℃,加入液碱,反应10
‑
15min后,加入甲醛,40min内升温至70
‑
75℃,75min内升温至90
‑
95℃,沸腾反应15
‑
35min,90℃下反应20
‑
30min,75℃下进行脱水,当样品能拉出丝时,降温至60
‑
70℃,加入乙醇混合均匀后,即得改性酚醛树脂;
8.b:将二甲苯、豆油酸、三羟甲基丙烷、邻苯二甲酸酐和二月硅酸二丁基锡混合均匀后,通入氮气,进行升温反应,当酸值降为20mgkoh/g以下时,进行降温,加入偏苯三酸苷,170
‑
190℃下反应2
‑
4h,进行酸值检测,降温,干燥,加入丙二醇甲醚、三乙胺和水混合均匀后,加入二氧化钛微球,混合均匀后,超声反应30
‑
45min,即得改性醇酸树脂;
9.c:将2
‑
乙基己酸、水以及松香水混合均匀,升温至80
‑
85℃,缓慢加入氢氧化钠溶液,回流40
‑
50min,调整溶液ph值为6
‑
7,加入氧氯化锆水溶液,反应0.5
‑
1h,静置分层,去除下层溶液,上层溶液水洗2
‑
3次后,进行减压蒸馏,即得复合催干剂;
10.s2:防腐涂料制备:
11.将改性酚醛树脂、改性醇酸树脂、高闪点溶剂、复合催干剂、密胺焦磷酸盐、颜料、助剂混合均匀,反应30
‑
45min后,研磨30
‑
45min,过滤,加入硅丙乳液,混合均匀,即得防腐涂料。
12.进一步地,所述酚醛防腐涂料所需材料包括,以重量计:改性酚醛树脂60
‑
80份、改性醇酸树脂40
‑
70份、高闪点溶剂5
‑
10份、复合催干剂1
‑
3份、密胺焦磷酸盐15
‑
35份、颜料5
‑
20份、助剂1
‑
6份、硅丙乳液10
‑
15份。
13.进一步地,所述改性酚醛树脂固含量应为80%。
14.进一步地,所述改性醇酸树脂升温反应为:2h内升温至180℃,反应1h,继续升温至200℃,反应2h,最后升温至230℃,反应1h。
15.进一步地,酸值检测应为50
‑
60mgkoh/g。
16.进一步地,所述二氧化钛微球的制备工艺为:将聚苯乙烯微球和异丙醇、水在室温下混合均匀后,缓慢加入正硅酸乙酯和无水乙醇,40
‑
60℃下反应6
‑
8h,离心、洗涤、干燥,研磨均匀后,与无水乙醇混合均匀,超声反应10
‑
20min,加入钛酸四丁酯,升温至70
‑
80℃,反应,离心、洗涤、干燥,即得二氧化钛微球。
17.进一步地,所述二氧化钛微球粒径为200nm。
18.进一步地,所述高闪点溶剂为环己酮、四氯化碳中的一种或多种。
19.进一步地,所述颜料为钛白粉、氧化铁红、铬黄、酞青绿、酞菁蓝、炭黑中的一种或多种。
20.进一步地,所述助剂为纳米硫酸钡、滑石粉、聚二甲基硅氧烷中的一种或多种。
21.进一步地,所述改性酚醛树脂所需材料包括,以重量计:甲醛20
‑
30份、硫酸10
‑
15份、二甲苯25
‑
35份、苯酚10
‑
15份、盐酸0.1
‑
0.5份、液碱1
‑
5份、甲醛12
‑
18份、乙醇20
‑
35份。
22.进一步地,所述改性醇酸树脂所需材料包括,以重量计:二甲苯5
‑
15份、豆油酸1
‑
5份、三羟甲基丙烷1
‑
5份、邻苯二甲酸酐1
‑
5份、二月硅酸二丁基锡1
‑
5份、偏苯三酸苷5
‑
10份、丙二醇甲醚10
‑
20份、三乙胺5
‑
15份、水20
‑
40份、二氧化钛微球10
‑
20份。
23.进一步地,所述复合催干剂所需材料包括,以重量计:2
‑
乙基己酸2
‑
10份、水10
‑
20份、松香水1
‑
5份、氢氧化钠2
‑
8份、氧氯化锆1
‑
5份。
24.进一步地,所述二氧化钛微球所需材料包括,以重量计:聚苯乙烯微球10
‑
25份、异丙醇5
‑
15份、水30
‑
50份、正硅酸乙酯5
‑
10份、无水乙醇20
‑
30份、钛酸四丁酯1
‑
5份。
25.进一步地,根据以上任意一项所述的一种环境友好型高闪点酚醛防腐涂料的制备工艺制备的防腐涂料。
26.与现有技术相比,本发明所达到的有益效果是:
27.(1)使用二甲苯对酚醛树脂进行改性,首先合成二甲苯甲醛树脂,通过二甲苯甲醛树脂与苯酚和甲醛反应将二甲苯环引入至酚醛树脂结构中,二甲苯环为疏水结构,在反应过程中,严格控制温度,使分子量均匀分布,使改性酚醛树脂具有较大粘性的同时又具有一定的流动性,并且在合成过程中,参与反应的主要为二甲苯当中的间二甲苯,而其余物质与甲醛反应速率很小,并且在经过水洗、蒸馏时已基本除去,因此不会产生毒性,使得涂料具有耐水性以及粘性。
28.(2)本发明制备的二氧化钛微球中具有空腔结构,而空腔结构可以贮存大量空气,吸收或反射紫外线,起到隔热保温的作用,制备过程中,选用钛酸四丁酯作为钛源,使得二氧化钛微球具有较大的比表面积和缺陷,当受到外部冲击时,二氧化钛微球内部因产生的微开裂而吸收了大量的冲击能,提高了涂料的抗紫外性能、光反射率、断裂伸长率以及抗拉伸强度。
29.(3)通过二氧化钛微球对水性醇酸酯树脂进行改性,控制二氧化钛微球粒径在200nm,不会使微球粒子在水性醇酸树脂中出现团聚现象,使得涂层表面出现粗糙结构,增大了水接触角,并且使涂料不会受到腐蚀,同时,又增强了涂料的的紧密性,防止水、腐蚀性物质以及氧气进入涂料内部,增强了涂料的自我保护能力,涂料致密性的增强,使得硬度也进一步提升。
30.(4)锆催干剂的加入提高了涂料的有效交联密度,改善了产品为提高安全性能导致干性延缓的不足,同时使涂料具有无毒、稳定性好的特性,增强涂料的硬度、附着力以及耐水性。
31.(5)高闪点溶剂的加入,使涂料的整体闪点大于60℃,产品在生产、使用、运输、储存、使用过程中无需采取特殊防护,即可满足各环节对安全管理的要求。
32.(6)密胺焦磷酸盐作为阻燃剂加入至涂料制备过程中,降低了涂料的voc含量,提高了产品闪点,从而提高了产品的安全性,涂料在高温受热时,密胺焦磷酸盐会与酚醛树脂发生反应,生成酯化物,同时在涂料表面形成一层绝热的炭层,从而提高了涂料的阻燃性。
33.本发明制备的涂料具有低voc含量,抗紫外性能、力学性能、防腐蚀性能、耐水性以及耐阻燃性,环保无毒。
具体实施方式
34.下面将对本发明实施例中的技术方案进行清楚、完整地描述,显然,所描述的实施例仅仅是本发明一部分实施例,而不是全部的实施例。基于本发明中的实施例,本领域普通技术人员在没有做出创造性劳动前提下所获得的所有其他实施例,都属于本发明保护的范围。
35.实施例1:包括以下步骤:
36.s1:原料制备:
37.a:在20份甲醛溶液中缓慢加入10份硫酸,温度保持在40℃以下,混合均匀后加入25份二甲苯,在70℃下反应8h,静置15min,去除下层溶液,用水洗涤至中性,对产物进行抽真空直至无脱出物,冷却至室温,加入10份苯酚,温度达到40℃时,加入0.1份盐酸,升温,40min内温度达到65℃,75min内温度达到93℃,沸腾反应15min,95℃下再反应20min,快速冷却至40℃,加入1份液碱,反应10min后,加入12份甲醛,40min内升温至70℃,75min内升温至90℃,沸腾反应15min,90℃下反应20min,75℃下进行脱水,当样品能拉出丝时,降温至60℃,加入20份乙醇调整固含量为80%,即得改性酚醛树脂;
38.b:将10份聚苯乙烯微球和5份异丙醇、30份水在室温下混合均匀后,缓慢加入5份正硅酸乙酯和10份无水乙醇,40℃下反应6h,离心、洗涤、干燥,研磨均匀后,与10份无水乙醇混合均匀,超声反应10min,加入1份钛酸四丁酯,升温至70℃,反应,离心、洗涤、干燥,即得二氧化钛微球;
39.c:将5份二甲苯、1份豆油酸、1份三羟甲基丙烷、1份邻苯二甲酸酐和1份二月硅酸二丁基锡混合均匀后,通入氮气,2h内升温至180℃,反应1h,继续升温至200℃,反应2h,最后升温至230℃,反应1h,当酸值降为20mgkoh/g以下时,进行降温,加入5份偏苯三酸苷,170℃下反应2h,当酸值检测为50mgkoh/g时,降温,干燥,加入10份丙二醇甲醚、5份三乙胺和20份水混合均匀后,加入10份二氧化钛微球,混合均匀后,超声反应30min,即得改性醇酸树
脂;
40.d:将2份2
‑
乙基己酸、10份水以及1份松香水混合均匀,升温至80℃,缓慢加入2份氢氧化钠溶液,回流40min,调整溶液ph值为6,加入1份氧氯化锆水溶液,反应0.5h,静置分层,去除下层溶液,上层溶液水洗2次后,进行减压蒸馏,即得复合催干剂;
41.s2:防腐涂料制备:
42.将60份改性酚醛树脂、40份改性醇酸树脂、5份四氯化碳、1份复合催干剂、15份密胺焦磷酸盐、5份钛白粉、1份纳米硫酸钡混合均匀,反应30min后,研磨30min,过滤,加入10份硅丙乳液,混合均匀,即得防腐涂料。
43.实施例2:包括以下步骤:
44.s1:原料制备:
45.a:在22份甲醛溶液中缓慢加入11份硫酸,温度保持在40℃以下,混合均匀后加入28份二甲苯,在72℃下反应8.2h,静置18min,去除下层溶液,用水洗涤至中性,对产物进行抽真空直至无脱出物,冷却至室温,加入11份苯酚,温度达到42℃时,加入0.2份盐酸,升温,40min内温度达到65℃,75min内温度达到93℃,沸腾反应18min,95℃下再反应22min,快速冷却至41℃,加入2份液碱,反应11min后,加入13份甲醛,40min内升温至71℃,75min内升温至91℃,沸腾反应18min,90℃下反应22min,75℃下进行脱水,当样品能拉出丝时,降温至62℃,加入25份乙醇调整固含量为80%,即得改性酚醛树脂;
46.b:将15份聚苯乙烯微球和8份异丙醇、35份水在室温下混合均匀后,缓慢加入6份正硅酸乙酯和12份无水乙醇,45℃下反应6.2h,离心、洗涤、干燥,研磨均匀后,与12份无水乙醇混合均匀,超声反应12min,加入2份钛酸四丁酯,升温至72℃,反应,离心、洗涤、干燥,即得二氧化钛微球;
47.c:将8份二甲苯、2份豆油酸、2份三羟甲基丙烷、2份邻苯二甲酸酐和2份二月硅酸二丁基锡混合均匀后,通入氮气,2h内升温至180℃,反应1h,继续升温至200℃,反应2h,最后升温至230℃,反应1h,当酸值降为20mgkoh/g以下时,进行降温,加入6份偏苯三酸苷,175℃下反应2.5h,当酸值检测为50mgkoh/g时,降温,干燥,加入12份丙二醇甲醚、8份三乙胺和25份水混合均匀后,加入12份二氧化钛微球,混合均匀后,超声反应35min,即得改性醇酸树脂;
48.d:将3份2
‑
乙基己酸、12份水以及2份松香水混合均匀,升温至81℃,缓慢加入3份氢氧化钠溶液,回流42min,调整溶液ph值为6.2,加入2份氧氯化锆水溶液,反应0.6h,静置分层,去除下层溶液,上层溶液水洗2次后,进行减压蒸馏,即得复合催干剂;
49.s2:防腐涂料制备:
50.将65份改性酚醛树脂、45份改性醇酸树脂、6份四氯化碳、1.5份复合催干剂、20份密胺焦磷酸盐、10份钛白粉、2份纳米硫酸钡混合均匀,反应35min后,研磨35min,过滤,加入11份硅丙乳液,混合均匀,即得防腐涂料。
51.实施例3:包括以下步骤:
52.s1:原料制备:
53.a:在25份甲醛溶液中缓慢加入12份硫酸,温度保持在40℃以下,混合均匀后加入30份二甲苯,在74℃下反应8.5h,静置25min,去除下层溶液,用水洗涤至中性,对产物进行抽真空直至无脱出物,冷却至室温,加入13份苯酚,温度达到45℃时,加入0.3份盐酸,升温,
40min内温度达到65℃,75min内温度达到93℃,沸腾反应20min,95℃下再反应25min,快速冷却至43℃,加入3份液碱,反应13min后,加入15份甲醛,40min内升温至73℃,75min内升温至93℃,沸腾反应20min,90℃下反应26min,75℃下进行脱水,当样品能拉出丝时,降温至65℃,加入30份乙醇调整固含量为80%,即得改性酚醛树脂;
54.b:将20份聚苯乙烯微球和10份异丙醇、40份水在室温下混合均匀后,缓慢加入8份正硅酸乙酯和13份无水乙醇,50℃下反应7h,离心、洗涤、干燥,研磨均匀后,与13份无水乙醇混合均匀,超声反应15min,加入3份钛酸四丁酯,升温至75℃,反应,离心、洗涤、干燥,即得二氧化钛微球;
55.c:将10份二甲苯、3份豆油酸、3份三羟甲基丙烷、3份邻苯二甲酸酐和3份二月硅酸二丁基锡混合均匀后,通入氮气,2h内升温至180℃,反应1h,继续升温至200℃,反应2h,最后升温至230℃,反应1h,当酸值降为20mgkoh/g以下时,进行降温,加入8份偏苯三酸苷,180℃下反应3h,当酸值检测为55mgkoh/g时,降温,干燥,加入15份丙二醇甲醚、10份三乙胺和30份水混合均匀后,加入15份二氧化钛微球,混合均匀后,超声反应40min,即得改性醇酸树脂;
56.d:将5份2
‑
乙基己酸、15份水以及3份松香水混合均匀,升温至83℃,缓慢加入5份氢氧化钠溶液,回流45min,调整溶液ph值为6.5,加入3份氧氯化锆水溶液,反应0.7h,静置分层,去除下层溶液,上层溶液水洗3次后,进行减压蒸馏,即得复合催干剂;
57.s2:防腐涂料制备:
58.将70份改性酚醛树脂、50份改性醇酸树脂、8份四氯化碳、2份复合催干剂、25份密胺焦磷酸盐、15份钛白粉、4份纳米硫酸钡混合均匀,反应40min后,研磨40min,过滤,加入13份硅丙乳液,混合均匀,即得防腐涂料。
59.实施例4:包括以下步骤:
60.s1:原料制备:
61.a:在28份甲醛溶液中缓慢加入13份硫酸,温度保持在40℃以下,混合均匀后加入33份二甲苯,在78℃下反应8.8h,静置28min,去除下层溶液,用水洗涤至中性,对产物进行抽真空直至无脱出物,冷却至室温,加入14份苯酚,温度达到48℃时,加入0.4份盐酸,升温,40min内温度达到65℃,75min内温度达到93℃,沸腾反应30min,95℃下再反应28min,快速冷却至44℃,加入4份液碱,反应14min后,加入16份甲醛,40min内升温至74℃,75min内升温至94℃,沸腾反应25min,90℃下反应28min,75℃下进行脱水,当样品能拉出丝时,降温至68℃,加入33份乙醇调整固含量为80%,即得改性酚醛树脂;
62.b:将23份聚苯乙烯微球和13份异丙醇、45份水在室温下混合均匀后,缓慢加入9份正硅酸乙酯和14份无水乙醇,55℃下反应7.5h,离心、洗涤、干燥,研磨均匀后,与14份无水乙醇混合均匀,超声反应18min,加入4份钛酸四丁酯,升温至78℃,反应,离心、洗涤、干燥,即得二氧化钛微球;
63.c:将13份二甲苯、4份豆油酸、4份三羟甲基丙烷、4份邻苯二甲酸酐和4份二月硅酸二丁基锡混合均匀后,通入氮气,2h内升温至180℃,反应1h,继续升温至200℃,反应2h,最后升温至230℃,反应1h,当酸值降为20mgkoh/g以下时,进行降温,加入9份偏苯三酸苷,185℃下反应3.5h,当酸值检测为60mgkoh/g时,降温,干燥,加入18份丙二醇甲醚、13份三乙胺和35份水混合均匀后,加入18份二氧化钛微球,混合均匀后,超声反应43min,即得改性醇酸
树脂;
64.d:将8份2
‑
乙基己酸、18份水以及4份松香水混合均匀,升温至84℃,缓慢加入6份氢氧化钠溶液,回流48min,调整溶液ph值为7,加入4份氧氯化锆水溶液,反应0.9h,静置分层,去除下层溶液,上层溶液水洗3次后,进行减压蒸馏,即得复合催干剂;
65.s2:防腐涂料制备:
66.将75份改性酚醛树脂、60份改性醇酸树脂、9份四氯化碳、2.5份复合催干剂、30份密胺焦磷酸盐、18份钛白粉、5份纳米硫酸钡混合均匀,反应43min后,研磨43min,过滤,加入14份硅丙乳液,混合均匀,即得防腐涂料。
67.实施例5:包括以下步骤:
68.s1:原料制备:
69.a:在30份甲醛溶液中缓慢加入15份硫酸,温度保持在40℃以下,混合均匀后加入35份二甲苯,在80℃下反应9h,静置30min,去除下层溶液,用水洗涤至中性,对产物进行抽真空直至无脱出物,冷却至室温,加入15份苯酚,温度达到50℃时,加入0.5份盐酸,升温,40min内温度达到65℃,75min内温度达到93℃,沸腾反应35min,95℃下再反应30min,快速冷却至45℃,加入5份液碱,反应15min后,加入18份甲醛,40min内升温至75℃,75min内升温至95℃,沸腾反应35min,90℃下反应30min,75℃下进行脱水,当样品能拉出丝时,降温至70℃,加入35份乙醇调整固含量为80%,即得改性酚醛树脂;
70.b:将25份聚苯乙烯微球和15份异丙醇、50份水在室温下混合均匀后,缓慢加入10份正硅酸乙酯和15份无水乙醇,60℃下反应8h,离心、洗涤、干燥,研磨均匀后,与15份无水乙醇混合均匀,超声反应20min,加入5份钛酸四丁酯,升温至80℃,反应,离心、洗涤、干燥,即得二氧化钛微球;
71.c:将15份二甲苯、5份豆油酸、5份三羟甲基丙烷、5份邻苯二甲酸酐和5份二月硅酸二丁基锡混合均匀后,通入氮气,2h内升温至180℃,反应1h,继续升温至200℃,反应2h,最后升温至230℃,反应1h,当酸值降为20mgkoh/g以下时,进行降温,加入10份偏苯三酸苷,190℃下反应4h,当酸值检测为60mgkoh/g时,降温,干燥,加入20份丙二醇甲醚、15份三乙胺和40份水混合均匀后,加入20份二氧化钛微球,混合均匀后,超声反应45min,即得改性醇酸树脂;
72.d:将10份2
‑
乙基己酸、20份水以及5份松香水混合均匀,升温至85℃,缓慢加入8份氢氧化钠溶液,回流50min,调整溶液ph值为7,加入5份氧氯化锆水溶液,反应1h,静置分层,去除下层溶液,上层溶液水洗3次后,进行减压蒸馏,即得复合催干剂;
73.s2:防腐涂料制备:
74.将80份改性酚醛树脂、70份改性醇酸树脂、10份四氯化碳、3份复合催干剂、35份密胺焦磷酸盐、20份钛白粉、6份纳米硫酸钡混合均匀,反应45min后,研磨45min,过滤,加入15份硅丙乳液,混合均匀,即得防腐涂料。
75.对比例
76.对比例1:与实施例3做对比,原料中不加入改性醇酸树脂和高闪点溶剂,制备工艺与本文相同。
77.对比例2:与实施例3做对比,原料中不加入改性酚醛树脂和密胺焦磷酸盐,制备工艺与本文相同。
78.实验数据
79.闪点:gb/t5208
‑
1985《涂料闪点测定法》
80.附着力:gb/t5210
‑
2006《色漆和清漆拉开法附着力实验》
81.干燥时间:gb/t1728
‑
1979《漆膜、腻子膜干燥时间测定法》
82.耐冲击性:gb/t1732
‑
1993《漆膜耐冲击测定法》
83.柔韧性:gb/t1731
‑
1993《漆膜柔韧性测定法》
84.耐水性:gb/t1733
‑
1993《漆膜耐水性测定法》
85.voc含量:gb/t30981
‑
2020《工业防护涂料中有害物质限量》
86.耐盐水性:gb/t9274
‑
1988《色漆和清漆耐液体介质的测定》
[0087][0088][0089]
结论:由上表可知,本发明通过合理的制备工艺以及各组分参数,制备的酚醛涂料
具有良好的耐水性、抗冲击性、防腐蚀性以及具有低voc含量,环保无毒。
[0090]
最后应说明的是:以上所述仅为本发明的优选实施例而已,并不用于限制本发明,尽管参照前述实施例对本发明进行了详细的说明,对于本领域的技术人员来说,其依然可以对前述各实施例所记载的技术方案进行修改,或者对其中部分技术特征进行等同替换。凡在本发明的精神和原则之内,所作的任何修改、等同替换、改进等,均应包含在本发明的保护范围之内。