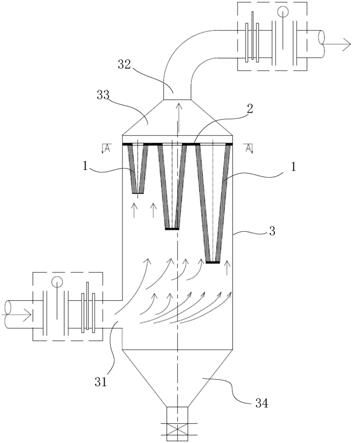
1.本实用新型属于煤气除尘技术领域,特别是涉及一种煤气干法除尘装置。
背景技术:
2.高炉煤气为含尘、含气态杂质的酸性腐蚀性气体,例如含有油、氯、硫等杂质;需经除尘系统除尘,并脱除杂质后才能输送给用户。现有技术中,通常是先通过高炉煤气干法除尘装置除尘,然后再通过下游单独设置的脱氯装置、水解脱硫装置去除氯、硫等杂质。
3.但是,现有技术中,煤气在除尘装置中并非均匀通过滤筒,通常是从除尘装置的侧面进入,距离煤气进口近的位置为低流速、低流量的背风面区,而距离煤气进口远的位置为高流速、高流量的迎风面区,不同位置煤气的流速和流量有差距,需要匹配不同的处理量,如果均匀布置滤筒,无法达到自均流、自适应以及较好的处理效率。通常的做法是在筒体入口段一定高度范围内设置均流装置,结构较为复杂。
技术实现要素:
4.鉴于以上所述现有技术的缺点,本实用新型的目的在于提供一种煤气干法除尘装置,提高煤气进入筒体后的自均流、自适应效果,提高装置的整体效率和使用寿命。
5.为实现上述目的及其他相关目的,本实用新型提供种煤气干法除尘装置,包括筒体,所述筒体的下部设置有煤气进口,筒体的上部设置有煤气出口,所述煤气进口的进气方向沿筒体的径向,在所述筒体的横截面上沿煤气的进气方向由近及远设置为至少两个分区,每个分区内设置有滤筒,所述滤筒位于煤气出口的下方;各个分区的滤筒的长度、直径或数量不同,且各个分区的煤气过滤能力沿煤气进口的进气方向逐区递增。
6.可选地,沿煤气的进气方向,从距离煤气进口最近的分区至距离煤气进口最远的分区,滤筒的长度逐区递增。
7.可选地,沿煤气的进气方向,从距离煤气进口最近的分区至距离煤气进口最远的分区,滤筒的直径逐区递增。
8.可选地,沿煤气的进气方向,从距离煤气进口最近的分区至距离煤气进口最远的分区,滤筒的数量逐区递增。
9.可选地,所述滤筒为从上至下由粗变细的倒锥形结构,或者所述滤筒为圆筒形结构。
10.可选地,各个所述分区的滤筒上端平齐,沿煤气进气方向,滤筒的下端的高度逐区递减。
11.可选地,在筒体的横截面上,各个所述分区的滤筒的中心分布在以煤气进口的中心为圆心的同一圆弧上。
12.可选地,在筒体的横截面上,沿煤气进气方向分为三个区,各个分区的最远边界处距离煤气进口中心的径向距离比为1:2-2.5:4-4.5。
13.可选地,所述筒体内设置有支撑板,所述支撑板与筒体顶部之间围成煤气收集腔
室,所述煤气收集腔室与煤气出口连通,所述支撑板将净化前和净化后的煤气隔开,所述滤筒的上端安装在支撑板上,且支撑板上开设有与滤筒的上端出气口对应的开孔。
14.可选地,所述筒体的内壁设置有限位结构,所述滤筒的下端设置有限位件,所述限位结构与限位件的其中一个开设有限位槽,另一个竖向设置有限位销,所述限位销伸入限位槽内,限制滤筒的横向摆动范围。
15.可选地,所述煤气干法除尘装置还包括喷吹清灰装置,所述喷吹清灰装置包括供气装置、喷吹总管和喷吹支管,所述喷吹支管为上粗下细的倒锥形结构,所述喷吹支管的侧面开设有多个喷吹口,所述喷吹支管伸入所述滤筒中。
16.可选地,所述喷吹口呈喇叭状,且同一喷吹支管上喷吹口的大小相同。
17.如上所述,本实用新型具有以下有益效果:采用上述结构,根据煤气进入筒体后不同位置流量和流速的不同,对应地将筒体沿煤气进行方向横向划分为多个分区,每个分区设置滤筒,且各个分区的煤气过滤能力依次增大,实现各区处理能力与煤气流量和流速的匹配,达到自均流、自适应以及较好的处理效率。
附图说明
18.图1为一个实施例的结构示意图;
19.图2为图1中a-a视图;
20.图3为筒体的横截面上的分区示意图;
21.图4为另一实施例的结构示意图;
22.图5为图4中局部放大视图;
23.图6为又一实施例的结构示意图;
24.图7为又一实施例的结构示意图。
25.零件标号说明:
26.1-滤筒;2-支撑板;3-筒体;3a-第一分区;3b-第二分区;3c-第三分区;31-煤气进口; 32-煤气出口;33-煤气收集腔室;34-集灰斗;41-限位结构;42-限位销;43-限位槽;5-喷吹清灰装置;51-总管;52-支管;53-喷吹口。
具体实施方式
27.以下由特定的具体实施例说明本实用新型的实施方式,熟悉此技术的人士可由本说明书所揭露的内容轻易地了解本实用新型的其他优点及功效。
28.实施例1
29.如图1至图3所示,一种煤气干法除尘装置,用于煤气除尘,其包括筒体3,所述筒体3 的下部侧面设置有煤气进口31,煤气进口31连接进口管路,筒体3的上部设置有煤气出口 32,煤气出口32连接出口管路,在筒体3内横向并排设置有多个滤筒1,滤筒1位于煤气出口32的下方,煤气进口31的上侧;其中,在筒体3的上部设置有煤气收集腔室33,煤气收集腔室33位于滤筒1的上方,并与煤气出口32连通;所述滤筒1的外周侧为煤气净化时的进气口,滤筒1下端封闭,滤筒1上端设置有煤气净化后的出气口,该出气口与所述煤气收集腔室33连通。使用时,未净化的煤气由煤气进口31送入,在筒体3内向上流动,经滤筒 1除尘过滤后得到净化后的煤气,净化后的煤气进入煤气收集腔室33后通过煤气出口32排出,供用户使用,
筒体3底部设置有集灰斗34和排灰口等,用于清理收集的灰尘。
30.其关键在于,在所述筒体的横截面上沿煤气的进气方向由近及远划分至少两个分区(即由靠近煤气进口31的位置至远离煤气进口31的位置设置为至少两个分区),进气方向沿筒体的径向,每个分区内设置有一个至多个滤筒,所述滤筒位于煤气出口的下方;将各个分区的滤筒的长度、直径或数量的其中至少之一设置为不同,以使得各个分区的煤气过滤能力沿煤气的进气方向逐区递增。
31.采用上述结构,根据煤气进入筒体后不同位置流量和流速的不同,对应地将筒体沿煤气进行方向横向划分为多个分区,每个分区设置滤筒,且各个分区的煤气过滤能力依次增大,实现各区处理能力与煤气流量和流速的匹配,达到自均流、自适应以及较好的处理效率。
32.在一个实施方式中,所述筒体3内设置有支撑板2,支撑板2与筒体3顶部之间围成煤气收集腔室33,该支撑板2将净化前和净化后的煤气隔开,起到密封作用,避免未净化的煤气逸出,滤筒1的上端安装在支撑板2上,且支撑板2上开设有与滤筒1的内套的上端对应的开孔。
33.本例中,沿煤气的进气方向,从距离煤气进口最近的分区至距离煤气进口最远的分区,滤筒的长度逐区递增。如图2和图3所示,沿箭头所示方向由近及远划分为多个分区,本例中为3个分区,其他实施方式中根据筒体3的大小可增减分区数量。根据距筒体3进气口的平面径向距离范围设为多个分区,第一分区距离煤气进口31最近的低流速、低流量背风面区,该区匹配滤筒1长度最短;最末区,距离煤气进口31最远的高流速、高流量迎风面区,匹配最长滤筒1;即第一区和最末区之间的区域,滤筒1长度介于第一分区、最末分区之间,其滤筒1长度逐区递增,实现煤气流量第一级自动分配。
34.本例中以三个分区为例进行说明,沿煤气的进气方向,依次划分为第一分区3a、第二分区3b和第三分区3c,从距离煤气进口31最近的第一分区3a至距离煤气进口31最远的第三分区3c,滤筒1的长度逐区递增。如图1所示,第一分区3a滤筒1的长度小于第二分区3b 滤筒1的长度,第二分区3b滤筒1的长度小于第三分区3c滤筒1的长度,各分区滤筒1的数量可相等或者不同,例如可以依次增加。
35.经由滤筒1精除尘后的净煤气,汇聚于煤气收集腔室内,使得通过各滤筒1的煤气流速基本相当,保证各滤筒1的使用寿命基本一致,便于维护。同时,气流能够在滤筒1高度差构成的缓冲范围内逐步扩散,自均流、自适应,无需另外设置均流装置。
36.本例中,所述滤筒1为从上至下由粗变细的倒锥形结构,该结构滤筒1的外周侧面积增大,可增大除尘效率,并且通过锥面可实现气流的缓冲。
37.本例中,各个所述分区滤筒1的上端平齐,沿煤气进气方向,滤筒1的下端的高度逐区递减。该结构便于滤筒1的统一安装,并且流速和流量越大的区域配置的滤筒1更长,可减缓流速,增大过滤面积,流速和流量较小的区域配置较短的滤筒1,从而实现各个区域内煤气的均流效果。
38.在另一实施例中,各分区的滤筒1直径规格相同,各分区之间数量不同,例如数量可依次递增。
39.在本实施例中,滤筒1的直径还逐区递增,即第二分区3b内滤筒1的直径大于第一分区 3a内滤筒1的直径,第三分区3c内滤筒1的直径大于第二分区3b内滤筒1的直径。在其
他实施例中各区滤筒1的直径相同,长度不同。
40.进一步地如图7所示,在筒体3的横截面上,各个分区的滤筒1的中心分布在以煤气进口31的中心o为圆心的同一圆弧上,该圆弧如图中双点划线所示,以便与煤气进入筒体3 内的扩散形式对应。
41.如图3所示,在筒体3的横截面上,沿煤气进气方向分为三个区,各个分区的最远边界处距离煤气进口31中心的径向距离比为d1:d2:d3=1:2-2.5:4-4.5,以合理规划各分区范围。
42.实施例2
43.如图4和图5所示,由于滤筒1的下端无支撑结构,在长度较长或者受气流影响可能产生晃动,影响煤气处理效果,在实施例1或2的基础上,本例中设置有限制滤筒1横向摆动范围的限位结构41,以便控制滤筒1的径向移动范围。
44.具体地如图5所示,所述筒体3的内壁设置有限位结构41,限位结构41可以为限位块、限位板等结构,滤筒1的下端设置有限位件,限位结构41上开设有限位槽43,限位件为竖向设置在滤筒1下端的限位销42,限位销42伸入限位槽43内,可以与限位槽43之间有横向间隙,从而通过限位槽43和限位销42限制滤筒1的横向摆动范围,且该结构也便于设置和安装,不影响滤筒1更换吸附剂。
45.根据各个分区的高度不同,在不同的高度位置设置对应的限位结构41,限位结构41可采用条状或框架结构,减少对煤气的阻挡。
46.实施例3
47.在实施例1-2的基础上,为便于清理滤筒1的外套上的灰尘或者清洗吸附剂,煤气干法除尘装置还包括喷吹清灰装置5,所述喷吹清灰装置5包括供气装置(未示出)、用于进气的喷吹总管51和用于对滤筒反喷吹的喷吹支管52,所述喷吹支管52为上粗下细的倒锥形结构,所述喷吹支管52的侧面开设有多个喷吹口53,所述喷吹支管52伸入所述滤筒中。各个喷吹支管52伸入对应的滤筒1的内腔中,即位于内套13中,通过喷吹口53对滤筒1进行反喷吹清理,如图4和图5所示。
48.其中喷吹支管52的直径沿轴线从上到下逐渐缩小,其进气端为大径端,与喷吹总管51 连接,总管51供气装置连通,最小截面端封闭(即下端封闭);喷吹口53呈逐渐扩大的喇叭状结构,并且每个喷吹支管52的侧壁各渐扩喷口直径相等,使得各喷吹口53气流速度与流量相同。
49.其中,滤筒1直径大小不同,对应的喷吹支管52大小可不同,喷吹支管52的直径可随着滤筒1直径的增大而增大。
50.根据除尘装置工况需求,供气装置可以提供清灰用的惰性气体或洁净煤气,也可以提供清洗吸附剂表面孔隙的过热蒸汽,两者可通过不同的供气管路进行输送。
51.实施例4
52.如图6所示,与实施例1的不同之处在于,本例中各分区中滤筒1的长度相同,滤筒1 的直径可逐区递增,或者滤筒1的数量逐区递增。并且各个滤筒1可共用一个限位结构61,便于结构的布置。
53.由于在筒体3的横截面上,沿煤气进气方向依次分为至少两个分区,并且各分区滤筒1 的长度或直径不同,滤筒1长度逐区递增和/或滤筒1直径逐区递增,实现煤气流量第一
级自动分配。经由滤筒1的精除尘后的净煤气,汇聚于煤气收集腔室33后流出,实现煤气流量的第二级自动分配,使得通过各滤筒1的煤气流速基本相当,保证各滤筒1的使用寿命基本一致,便于维护。同时,气流能够在滤筒1高度差构成的缓冲范围内逐步扩散,自均流、自适应,无需另外设置均流装置。滤筒1过滤的粉尘,可通过反喷吹清灰,清灰时关闭煤气进口 31,清灰气体由反喷吹管路吹至滤筒1内腔,实现粉尘与滤筒1的分离,清灰完毕关闭喷吹气体装置的控制阀;粉尘收集在筒体3的底部锥段内,积累到一定料位后卸灰。
54.实施例5
55.如图7所示,与上述实施例的不同之处在于,滤筒1为圆筒形结构,长度逐区递增,各区滤筒1的直径可相同或者逐区递增。
56.对于煤气流速不高或者对于均流过滤要求不高的场合,通过分区实现煤气流量的第一级自动分配,满足过滤要求,采用圆筒型滤筒可以适当降低加工制造难度。
57.本实用新型,根据煤气进入筒体后不同位置流量和流速的不同,对应地将筒体沿煤气进行方向横向划分为多个分区,每个分区设置滤筒,且各个分区的煤气过滤能力依次增大,实现各区处理能力与煤气流量和流速的匹配,达到自均流、自适应以及较好的处理效率。
58.上述实施例仅例示性说明本实用新型的原理及其功效,而非用于限制本实用新型。任何熟悉此技术的人士皆可在不违背本实用新型的精神及范畴下,对上述实施例进行修饰或改变。因此,举凡所属技术领域中具有通常知识者在未脱离本实用新型所揭示的精神与技术思想下所完成的一切等效修饰或改变,仍应由本实用新型的权利要求所涵盖。