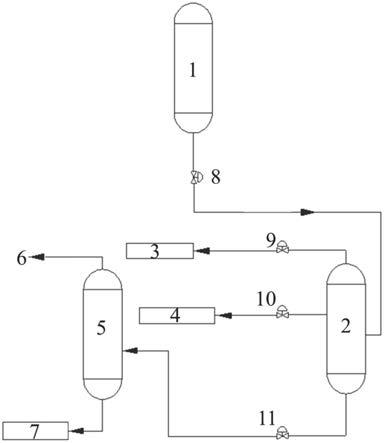
1.本实用新型属于一种热钾碱脱碳系统处理装置,涉及一种热钾碱脱碳系统轻油回收装置。
背景技术:
2.公开该背景技术部分的信息仅仅旨在增加对本实用新型的总体背景的理解,而不必然被视为承认或以任何形式暗示该信息构成已经成为本领域一般技术人员所公知的现有技术。
3.费托合成总的工艺流程主要包括煤气化、气体净化、变换和重整、合成和产品精制改质等部分,是非石油含碳资源(天然气、煤炭、渣油以及生物质等)高效转化利用最重要的途径之一。费托合成的产物主要是c1至c200的直链烷烃,初产品经进一步处理得到一定规格的汽油、柴油等油品燃料以及乙烯、丙烯、润滑油和石蜡等化学品。
4.而脱碳工艺是费托合成工艺的配套技术,其功能是将费托合成尾气中的部分co2从循环气中脱除,以保证费托反应达到设计的转化效率,一般工业化铁基催化剂浆态床费托反应器单程转化率(co+h2)在30%~35%,合成尾气中co2含量在10%~15%,co2选择性在2%~4%。为提高合成气总转化率,大量合成尾气需进行循环,首先送至脱碳装置脱除co2至2%以下,然后循环返回费托合成反应器,保证入塔气co2含量在0.5%左右,总转化率可达90%~95%。
5.但是发明人研究费托合成尾气中含有大量的烃类物质进入脱碳溶液中会导致溶液发泡,引起塔压差上涨,严重时会导致吸收塔液泛,影响装置稳定运行,为降低溶液系统油含量,避免脱碳溶液中的油相发生闪蒸现象后大量烃类物质进入蓄热式焚烧炉氧化,造成了大量油气资源的浪费。此外脱碳溶液含油量占比过高会破坏碳酸钾溶液性能导致脱碳效率降低、物料消耗高、影响费托合成转化效率。
技术实现要素:
6.为了解决热钾碱脱碳系统中,气体存在较多烃类组分,影响热钾碱脱碳过程的进行,避免轻油组分对焚烧炉的影响,本实用新型提出一种热钾碱脱碳系统轻油回收装置,通过在热钾碱脱碳装置前设计三相分离器,不仅去除合成尾气中的烃类物质,避免影响脱碳过程,还能避免轻油组分对焚烧炉的影响,同时还能分理出气、油、水相,分别用于不同用途,增加利用率。
7.具体地,本实用新型通过如下技术方案实现:
8.提供一种热钾碱脱碳系统轻油回收装置,包括净化气分离器,所述净化气分离器与三相分离器连接,三相分离器设有三个出口,分别连接燃料气罐、油罐、闪蒸槽,所述燃料气罐与热钾碱脱碳装置连接。
9.以上一个或多个技术方案具有以下有益效果:
10.1)传统技术直接将合成尾气通过热钾碱脱碳系统,尤其合成尾气含有大量烃类成
分,在热钾碱脱碳系统中容易发生导致溶液发泡,影响装置稳定运行,因此在净化气分离器与热钾碱脱碳系统之间添加三相分离器,将合成尾气分成水、油、气三相,不仅能解决烃类成分对热钾碱脱碳系统的影响,提高脱碳效果,还能分理处可再利用成分水相和气相,提高利用率。
11.2)在实验研究中还发现,如果将三相分离器分离出的气体直接输送至费托合成反应器中,存在co2,因此将燃料气罐与与热钾碱脱碳系统连接。
12.3)如果直接将三相分离器分离获得的水相排出,容易造成能源浪费,因此在一些方案中,将水相通入闪蒸槽中,经降温、降压产生二次蒸汽和液相,闪蒸出来的二次蒸汽送入对应的预热装置进行预热。
附图说明
13.构成本实用新型的一部分的说明书附图用来提供对本实用新型的进一步理解,本实用新型的示意性实施例及其说明用于解释本实用新型,并不构成对本实用新型的不当限定。
14.图1为本实用新型实施例1所述热钾碱脱碳系统轻油回收装置;
15.图2为本实用新型实施例2所述热钾碱脱碳系统轻油回收装置;
16.图3为本实用新型对比例1所述热钾碱脱碳系统轻油回收装置;
17.其中:1、第一净化气分离器,2、三相分离器,3、燃料气罐,4、油罐,5、闪蒸槽,6、闪蒸气出口,7、再生塔,8、第一阀门,9、第二阀门,10、第三阀门,11、第四阀门,12、第二净化气分离器,13、第五阀门。
具体实施方式
18.应该指出,以下详细说明都是示例性的,旨在对本实用新型提供进一步的说明。除非另有指明,本文使用的所有技术和科学术语具有与本实用新型所属技术领域的普通技术人员通常理解的相同含义。
19.需要注意的是,这里所使用的术语仅是为了描述具体实施方式,而非意图限制根据本实用新型的示例性实施方式。如在这里所使用的,除非上下文另外明确指出,否则单数形式也意图包括复数形式,此外,还应当理解的是,当在本实用新型中使用术语“包括”时,其指明存在特征、步骤、操作、器件、组件和/或它们的组合。
20.需要理解的是,术语“上”、“下”、“水平”、“顶”、“底”等指示的方位或位置关系为基于附图所示的方位或位置关系,仅是为了便于描述本实用新型和简化描述,而不是指示或暗示所指的装置或元件必须具有特定的方位、以特定的方位构造和操作,因此不能理解为对本实用新型的限制。
21.发明人研究发现费托合成尾气中有机烃类含量较高,采用热钾碱化学吸收法虽然能减少烃类的溶解损失,但脱碳装置在运行过程中,由于费托合成尾气中含有大量的烃类物质,进入脱碳溶液中会导致溶液发泡,引起塔压差上涨,严重时会导致吸收塔液泛,影响装置稳定运行,另外,溶液系统中轻油组分含量过高,在一定程度上还会造成蓄热式焚烧炉再生气热值过高,焚烧炉运行不稳定。
22.为了解决热钾碱脱碳系统中,气体存在较多烃类组分,影响热钾碱脱碳过程的进
行,避免轻油组分对焚烧炉的影响,本实用新型提出一种热钾碱脱碳系统轻油回收装置,通过在热钾碱脱碳装置前设计三相分离器,不仅去除合成尾气中的烃类物质,避免影响脱碳过程,还能避免轻油组分对焚烧炉的影响,同时还能分理出气、油、水相,分别用于不同用途,增加利用率。
23.具体地,本实用新型通过如下技术方案实现:
24.提供一种热钾碱脱碳系统轻油回收装置,包括净化气分离器,所述净化气分离器与三相分离器连接,三相分离器设有三个出口,分别连接燃料气罐、油罐、闪蒸槽,所述闪蒸槽与热钾碱脱碳装置连接。
25.传统技术直接将合成尾气通过热钾碱脱碳系统,尤其合成尾气含有大量烃类成分,在热钾碱脱碳系统中容易发生导致溶液发泡,影响装置稳定运行,因此在净化气分离器与热钾碱脱碳系统之间添加三相分离器,将合成尾气分成水、油、气三相,不仅能解决烃类成分对热钾碱脱碳系统的影响,提高脱碳效果,还能分理出可再利用成分水相和气相,提高利用率。
26.在实验研究中还发现,如果将三相分离器分离出的气体直接输送至费托合成反应器中,存在co2,因此将燃料气管与与热钾碱脱碳系统连接。
27.闪蒸是减压导致汽液分离现象是从一个热力学平衡态到下一个热力学平衡态的变化过程。闪蒸槽就是压力和温度较高的水相进入到低压的容器中由于压力的降低使铝酸钠溶液中的水分以蒸汽的形式分离出来,实际中生产限于压力容器的体积和闪蒸能力往往通过多级闪蒸使水相中的二次蒸汽充分的进行分离为生产提供所需要的热量。
28.常规处理均是直接将三相分离器分离获得的水相排出,容易造成能源浪费,因此在一些方案中,将水相通入闪蒸槽中,经降温、降压产生二次蒸汽和液相,闪蒸出来的二次蒸汽送入对应的预热装置进行预热。
29.为了保证运输性能,所述分离的气相压力不小于1.0mpa。
30.在一些实施方式中,所述闪蒸槽顶部设有闪蒸气出口,闪蒸槽连接再生塔。
31.闪蒸气出口可以收集高温蒸汽回收热量,节约能源,闪蒸槽分离出的液相可用于其它反应。
32.在一个或多个实施方式中,所述净化气分离器与三相分离器之间,三相分离器与燃料气罐之间,三相分离器与油罐之间,三相分离器与闪蒸槽之间,均设有阀门。加设阀门是为了更好控制各个装置,或者在某一装置进行检修时,能够与前一工序、下一工序的装置分隔开。
33.为了提高切断阀使用安全性,在一些实施方式中,所述阀门的进口端和出口端分别设置切断阀。
34.在一些热钾碱脱碳系统或者费托合成装置中,净化气分离器数量仅为一个,这是由于当为设置三相分离器时,气提过多进入热钾碱脱碳系统中时,容易造成吸收塔液泛,影响装置稳定运行,另外,溶液系统中轻油组分含量过高,在一定程度上还会造成蓄热式焚烧炉再生气热值过高,焚烧炉运行不稳定。即使使用三相分离器,获得的水相数量不大,经闪蒸槽处理后无法产生足够多的二次蒸汽,进而无法利用二次蒸汽的热能去助推其它反应。而在本实用新型一些实施方式中,由于设置了三相分离器,将油、水、气三相分离,使用多个净化气分离器,多个净化气分离器连接三相分离器,也不会产生上述问题。
35.在一些实施方式中设置两个净化气分离器i、ii。
36.本实用新型一些实施例通过对热钾碱脱碳装置净化气分离器i、ii冷凝液中组分进行分析研究,发现其富集大量油类物质(其组分与低碳烃液体产品组分相类似),新增烃类分离回收系统,增加油水分离器,将富集的大量油类物质的冷凝液进行三相分离,改善油水分离系统的运行条件,实现脱碳装置净化气分离器i、ii冷凝液油水分离,烃类作为粗产品回收,冷凝水返回系统再利用,进一步提高冷凝液循环利用率、降低系统脱盐水消耗、提高油品产量。
37.本实用新型一些实施例通过设置三相分离器或油水分离器,进一步降低了脱碳装置物料消耗、增加了装置的操作弹性、改善了油水分离系统的运行条件,解决了脱碳装置能耗高、水平衡较差、碳酸钾消耗高等系统问题,不仅起到了节能减排、节支降耗的目的,还大大提升了脱碳装置的运行质量。
38.本实用新型一些实施例具有至少以下优点:(1)系统脱盐水消耗量明显下降,从原来平均每天消耗1254m3脱盐水降至每天消耗350m3脱盐水,即系统脱盐水消耗量降低约37.64m3/h,若每年按8000h生产计算,即每年节约脱盐水约301.1km3;(2)脱碳油水分离工艺流程优化后平均每天回收轻油产量约33.71吨,若每年按8000h计算生产,即每年可提高产量约1.12万吨。
39.本实用新型一些实施例对大型煤制油费托合成尾气脱碳装置原始设计流程优化运行提供技术经验,并改善热钾碱脱碳系统运行条件,为企业提产、节能降耗提供可借鉴的宝贵经验。
40.为了实现能源再利用,在一个或多个实施方式中,所述闪蒸槽上闪蒸气出口与吸热反应装置连接。
41.在一些实施方式中,所述燃料气罐设有压力表,便于实时监控气体压力,避免压力过大时,进入热钾碱脱碳系统,对溶液造成较大冲击,引起剧烈反应,提高安全性。
42.在一个或多个实施方式中,所述油罐连接低碳烃回收油管线,用于回收再利用。
43.三相分离器分离处的烃类物质或油具有一定的易燃性和危险性,因此在一个或多个实施方式中,所述油罐在高度为整体高度80%位置上设置液位调节阀。
44.在一些实施方式中,所述闪蒸槽在高度为整体高度30%位置上设置液位调节阀,控制液面高度小于整体高度的30%,此时能闪蒸出较多的蒸汽,为其它反应提供热能。
45.主要通过对热钾碱脱碳装置净化气分离器分离得到的含有大量油类物质的冷凝液进行三相分离,实现脱碳装置净化气分离器冷凝液油水分离且进行回收利用,进一步提高冷凝液循环利用率、降低系统脱盐水消耗量、提高油品产量、降低生产成本。
46.下面结合具体的实施例,对本实用新型做进一步的详细说明,应该指出,所述具体实施例是对本实用新型的解释而不是限定。
47.实施例1
48.如图1所示,为本实施例提供的一种热钾碱脱碳系统轻油回收装置,包括净化气分离器1,所述净化气分离器1与三相分离器2连接,三相分离器2设有三个出口,分别连接燃料气罐3、油罐4、闪蒸槽5,所述燃料气罐3与热钾碱脱碳装置连接,闪蒸槽5顶部设有闪蒸气出口6,闪蒸槽5连接再生塔7。
49.净化气分离器1与三相分离器2之间设有第一阀门8,三相分离器2与燃料气罐3之
间设有第二阀门9,三相分离器2与油罐4之间设有第三阀门10,三相分离器2与闪蒸槽5之间设有第四阀门11。
50.实施例2
51.如图2所示,为本实施例提供的一种热钾碱脱碳系统轻油回收装置,与实施例1区别在于,净化气分离器数量为2个,分别于三相分离器2连接,净化分离器12与三相分离器2之间设有第五阀门13,第一阀门8控制净化气分离器1,第五阀门13控制净化气分离器2,能单独实现净化气分离器1和净化气分离器2混合尾气通乳三相分离器2中。第一阀门8、第二阀门9、第三阀门10、第四阀门11、第五阀门13的进口端和出口端分别设置切断阀。
52.对比例1
53.如图3所示,为本实施例提供的一种热钾碱脱碳系统轻油回收装置,与实施例1区别在于,未设计三相分离器,净化气分离器1直接与闪蒸槽5连接,所述燃料气罐3与热钾碱脱碳装置连接,闪蒸槽5顶部设有闪蒸气出口6,闪蒸槽5连接再生塔7,闪蒸气出口6与热钾碱脱碳装置连接。净化气分离器1与闪蒸槽5连接之间设有第一阀门8,第一阀门8前后设有切断阀。
54.就生产过程而言,对比例1直接将尾气通如闪蒸槽,不利于烃类气提的分离,影响后续脱碳效果。而且压力骤降,对于混合气体(水、油、气相)危险性较大。
55.以上所揭露的仅为本实用新型的优选实施例而已,当然不能以此来限定本实用新型之权利范围,因此依本实用新型申请专利范围所作的等同变化,仍属本实用新型所涵盖的范围。