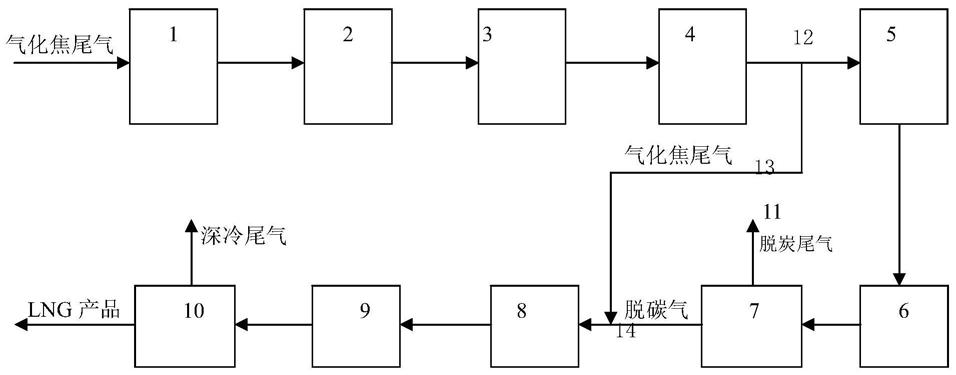
一种气化焦尾气变换、脱碳制lng的系统
技术领域
1.本实用新型属于气化焦尾气制lng(液化天然气)技术领域,具体为一种气化焦尾气变换、脱碳制lng的系统。
背景技术:
2.一般的焦化企业生产的是冶金焦,其焦炉气典型组成如下:
3.组分coco2o2ch4h2n2c
n
h
m
合计含量(%)6.202.200.6026.0058.004.502.50100.00
4.但由于市场需求的不同,现在有些焦化企业也生产气化焦,生产气化焦时气化焦尾气典型组成如下:
5.组分coco2o2ch4h2n2c
n
h
m
合计含量(%)15.035.130.4620.8452.862.712.97100.00
6.在生产冶金焦的时候,焦炉气中co、co2含量比较少、h2含量又比较多,所谓的氢碳比(每1分子co消耗3分子h2,每1分子co2消耗4分子h2,每1分子o2消耗2分子h2)在2左右,无论对甲烷化催化剂的使用,还是对co、co2的转化效果等各个方面,都比较有利。焦炉气经过压缩、脱除其中的有害杂质等处理后,可以直接进行甲烷化反应,使其中的co、co2和h2反应生成ch4,再通过深冷分离即得到lng产品(液化天然气)。
7.而在生产气化焦的时候,气化焦尾气中co、co2比生产冶金焦时高许多、h2又比生产冶金焦时少,所谓的氢碳比(每1分子co消耗3分子h2,每1分子co2消耗4分子h2,每1分子o2消耗2分子h2)不到理论值的80%,无论对甲烷化催化剂的使用,还是对co、co2的转化效果等各个方面,都是不利和不可行的。
技术实现要素:
8.为了解决以上技术问题,本实用新型提供一种气化焦尾气变换、脱碳制lng的系统,在生产气化焦的时候,通过增加变换、脱硫和脱碳系统,再经过精脱硫后进行甲烷化反应,深冷分离生产lng产品(液化天然气)。
9.解决以上技术问题的本实用新型中的一种气化焦尾气变换、脱碳制lng的系统,其特征在于:设有气化焦尾气压缩装置、气化焦尾气脱油脱萘装置和气化焦尾气脱苯脱氨装置,气化焦尾气压缩装置与气化焦尾气脱油脱萘装置连接,气化焦尾气脱油脱萘装置和气化焦尾气脱苯脱氨装置连接;还设有气化焦尾气耐硫变换装置、变换气脱硫装置、变换气湿法脱碳装置、混合气精脱硫装置、混合气甲烷化装置和甲烷化气深冷分离装置,气化焦尾气耐硫变换装置和变换气湿法脱碳装置通过变换气脱硫装置连接成一体,变换气湿法脱碳装置另一端通过管道ⅲ与混合气精脱硫装置连接,混合气精脱硫装置另一端与混合气甲烷化装置连接,混合气甲烷化装置和甲烷化气深冷分离装置连接;气化焦尾气脱苯脱氨装置通过管道ⅰ与气化焦尾气耐硫变换装置连接,管道ⅱ一端设在管道ⅰ上,另一端设在管道ⅲ上,且两端分别与管道ⅰ和管道ⅲ贯通连接。
10.以上各个装置通过通用管道进行相互连接。
11.所述系统还设有气化焦尾气预处理装置、气化焦尾气预处理装置与气化焦尾气压缩装置连接成一体。
12.所述气化焦尾气预处理装置与气化焦尾气压缩装置通过串联方式连接成一体。
13.所述气化焦尾气预处理装置中设有吸附剂层。
14.所述吸附剂层为采用对气化焦尾气中焦油和萘具有较强吸附能力的炭基吸附剂构成。
15.所述系统设有处理脱碳尾气的装置,处理脱碳尾气的装置与变换气湿法脱碳装置连接,对脱碳尾气进行处理。处理脱碳尾气的装置如火炬器或其它储存、进入下一步处理的装置。
16.所述气化焦尾气压缩装置、气化焦尾气脱油脱萘装置和气化焦尾气脱苯脱氨装置之间的连接方式为串联连接。
17.所述气化焦尾气耐硫变换装置、变换气脱硫装置和变换气湿法脱碳装置连接方式为串联连接。
18.本实用新型中生产气化焦时的气化焦尾气,经过预处理、压缩、脱油脱萘、脱苯脱氨后,分成两路,一路经过耐硫变换、变换气脱硫和湿法脱碳装置,将气化焦尾气中的co变换成co2后(同时生成h2)脱除;经过变换、脱硫和脱碳的气化焦尾气(称脱碳气)与另一路未经变换、脱硫和脱碳的气化焦尾气混合后(称混合气),满足甲烷化反应对氢碳比的要求;经过精脱硫后进行甲烷化反应,使其中的co、co2和h2反应生成ch4,再通过深冷分离得到lng产品(液化天然气)。
附图说明
19.图1为本实用新型中系统结构示意图
20.其中,图中标识具体为:
21.1.气化焦尾气预处理装置,2.气化焦尾气压缩装置,3.气化焦尾气脱油脱萘装置,4.气化焦尾气脱苯脱氨装置,5.气化焦尾气耐硫变换装置,6.变换气脱硫装置,7.变换气湿法脱碳装置,8.混合气精脱硫装置,9.混合气甲烷化装置,10.甲烷化气深冷分离装置,11.处理脱碳尾气的装置,12.管道ⅰ,13.管道ⅱ,14.管道ⅲ具体实施方式
22.下面结合附图和具体实施例对本实用新型作详细的说明。
23.实施例1
24.一种气化焦尾气变换、脱碳制lng的系统,其特征在于:设有气化焦尾气压缩装置、气化焦尾气脱油脱萘装置和气化焦尾气脱苯脱氨装置,气化焦尾气压缩装置与气化焦尾气脱油脱萘装置连接,气化焦尾气脱油脱萘装置和气化焦尾气脱苯脱氨装置连接;还设有气化焦尾气耐硫变换装置、变换气脱硫装置、变换气湿法脱碳装置、混合气精脱硫装置、混合气甲烷化装置和甲烷化气深冷分离装置,气化焦尾气耐硫变换装置和变换气湿法脱碳装置通过变换气脱硫装置连接成一体,变换气湿法脱碳装置另一端通过管道ⅲ与混合气精脱硫装置连接,混合气精脱硫装置另一端与混合气甲烷化装置连接,混合气甲烷化装置和甲烷
化气深冷分离装置连接;气化焦尾气脱苯脱氨装置通过管道ⅰ与气化焦尾气耐硫变换装置连接,管道ⅱ一端设在管道ⅰ上,另一端设在管道ⅲ上,且两端分别与管道ⅰ和管道ⅲ贯通连接。以上各个装置通过通用管道进行相互连接。
25.气化焦尾气预处理装置与气化焦尾气压缩装置通过串联方式连接成一体,气化焦尾气压缩装置、气化焦尾气脱油脱萘装置和气化焦尾气脱苯脱氨装置之间的连接方式为串联连接。另外,气化焦尾气耐硫变换装置、变换气脱硫装置和变换气湿法脱碳装置连接方式为串联连接。
26.气化焦尾气脱苯脱氨装置中气体分成两股,一股进入气化焦尾气耐硫变换装置中,再经变换气脱硫装置、变换气湿法脱碳装置成脱碳气体,与另一股气化焦尾气合并进入混合气精脱硫装置中进行进一步的处理。
27.实施例2
28.一种气化焦尾气变换、脱碳制lng的系统,设有气化焦尾气压缩装置、气化焦尾气脱油脱萘装置和气化焦尾气脱苯脱氨装置,气化焦尾气压缩装置与气化焦尾气脱油脱萘装置连接,气化焦尾气脱油脱萘装置和气化焦尾气脱苯脱氨装置连接;还设有气化焦尾气耐硫变换装置、变换气脱硫装置、变换气湿法脱碳装置、混合气精脱硫装置、混合气甲烷化装置和甲烷化气深冷分离装置,气化焦尾气耐硫变换装置和变换气湿法脱碳装置通过变换气脱硫装置连接成一体,变换气湿法脱碳装置另一端通过管道ⅲ与混合气精脱硫装置连接,混合气精脱硫装置另一端与混合气甲烷化装置连接,混合气甲烷化装置和甲烷化气深冷分离装置连接;气化焦尾气脱苯脱氨装置通过管道ⅰ与气化焦尾气耐硫变换装置连接,管道ⅱ一端设在管道ⅰ上,另一端设在管道ⅲ上,且两端分别与管道ⅰ和管道ⅲ贯通连接。
29.以上各个装置通过通用管道进行相互连接。
30.系统还设有气化焦尾气预处理装置和处理脱碳尾气的装置,气化焦尾气预处理装置与气化焦尾气压缩装置连接成一体。气化焦尾气预处理装置中设有吸附剂层,吸附剂层为采用对气化焦尾气中焦油和萘具有较强吸附能力的炭基吸附剂构成;处理脱碳尾气的装置与变换气湿法脱碳装置连接,对脱碳尾气进行处理,其它内容如实施例1中。
31.本实用新型中以上各个装置为常规通用装置。
32.本实用新型中气化焦尾气预处理装置,采用对气化焦尾气中焦油和萘具有较强吸附能力的炭基吸附剂,吸附气化焦尾气中的焦油和萘后,每隔一段时间用蒸汽吹扫再生一次,再生废水去焦化处理。该系统的特点是吸附剂对焦油和萘的脱除率高,且吸附条件温和(在常温常压下进行);
33.气化焦尾气压缩装置,可以采用往复式压缩机、螺杆压缩机+离心压缩机,压缩后的气化焦尾气压力为0.8~6.0mpa。气化焦尾气脱油脱萘装置,是经过气化焦尾气压缩机压缩后的气体,仍含有少量萘、油、水等杂质,采用炭基复合剂、硅酸盐复合剂等对其进行进一步精脱除,以减少对后续系统的影响。吸附油和萘后的炭基复合剂、硅酸盐复合剂等视操作工况每隔一段时间用蒸汽吹扫再生一次,再生废水去焦化处理;
34.气化焦尾气脱苯脱氨装置,采用变温吸附(tsa)技术对气化焦尾气中的苯和氨予以脱除,以减少对后续系统的影响。变温吸附(tsa)的再生气可以是深冷分离的尾气或自身净化气,通过蒸汽加热后对吸附塔进行吹扫使吸附剂得以再生。脱除苯和氨后,气化焦尾气中的苯≤10ppm、氨≤10ppm。气化焦尾气耐硫变换装置,压缩后的气化焦尾气补入适量的水
蒸汽,在耐硫变换催化剂的作用下,将绝大部分co变换生成co2和h2的过程。变换反应为放热反应,在反应器中采取适当措施(中间换热和/或冷激),控制好催化剂床层温度,防止催化剂过热而发生烧结失活,甚至损坏设备等事故;
35.变换气脱硫装置为将变换过程中由有机硫变换而来的h2s,在变换气出口温度条件下,通过固体脱硫剂将其脱除,以使变换气湿法脱碳系统的脱碳尾气硫含量可以达标排放或方便作其它利用;
36.变换气湿法脱碳装置为利用再生后的脱碳液将变换气中的co2脱除,以达到与未经过变换那部分气化焦尾气混合后调节氢碳比的目的,湿法脱碳有效组分损失少。吸收了co2的脱碳液通过加热再生得以循环使用,再生产生的脱碳尾气可以直接排放或作其它利用;
37.气化焦尾气脱苯脱氨装置脱苯脱氨后的气化焦尾气分成两路,一路去气化焦尾气耐硫变换系统、变换气脱硫系统、变换气湿法脱碳系统,经变换、脱硫、湿法脱碳后得到脱碳气;另一路气化焦尾气直接与上述得到的脱碳气混合形成混合气,该混合气进入混合气精脱硫系统;调节这两路气化焦尾气的相对气量,即可调节混合气的氢碳比。
38.混合气精脱硫装置为根据气化焦尾气(或混合气)中的无机硫(h2s)大部分已经被脱除,但其中的有机硫(硫氧碳、二硫化碳、硫醇、硫醚、噻吩等)含量还比较多的特点,通过固体催化剂将有机硫进行预加氢、一级加氢转化成无机硫(h2s),通过固体脱硫剂脱除生成的无机硫(h2s),再进行二级加氢转化剩余的有机硫为无机硫(h2s)、通过固体脱硫剂将其脱除,此时气化焦尾气(或混合气)中的总硫已脱至≤0.1ppm。再通过超精净化剂进一步处理,使出口气化焦尾气(或混合气)中的总硫脱至<0.05ppm。
39.混合气甲烷化装置为使气化焦尾气(或混合气)中的co、co2与h2反应生成ch4。这一方面增加了ch4的产量,同时可除去气化焦尾气中的co和co2,降低后续的分离难度和毒性危害。由于甲烷化反应为强放热反应,在流程设置中采用带循环三级甲烷化工艺,可以控制好每级催化剂床层温度,防止催化剂过热而发生烧结失活,甚至损坏设备等事故。气化焦尾气(或混合气)通过三级甲烷化反应,可使co2的浓度满足lng在进行低温分离时≤30ppm的要求,不需另加脱碳装置;
40.甲烷化气深冷分离装置使上述甲烷化系统所得到的富甲烷气通过深冷分离制得lng产品和深冷尾气的过程。在进行深冷分离前,需先进行精密过滤和干燥脱水,以分离其中1μm以上的杂质和使水份含量≤1ppm。深冷分离系统可以采用阶梯式制冷液化、混合冷剂(mrc)制冷液化和膨胀机制冷液化等工艺。
41.本实施例的一种气化焦尾气变换、脱碳制lng的工艺系统流程如下:
42.以38000nm3/h气化焦尾气制lng装置为例,压力6~7kpa、常温的气化焦尾气38000nm3/h,组成如下表所示:
43.组分coco2o2ch4h2n2c
n
h
m
合计含量(%)15.035.130.4620.8452.862.712.97100.00
44.杂质含量如下表所示:
45.组分h2s有机硫萘焦油+尘nh3b.t.x(苯)hcn含量(mg/nm3)≤20≤150≤300≤50≤50≤3000≤100
46.首先经过气化焦尾气预处理系统,采用炭基吸附剂吸附气化焦尾气中的焦油和
萘,预处理后气化焦尾气中:焦油+尘≤10mg/nm3,萘≤20mg/nm3。
47.然后采用两台往复式压缩机四级压缩,将预处理后的气化焦尾气压缩到2.4mpa。再采用炭基复合剂、硅酸盐复合剂等对其进行进一步的脱油脱萘,脱油脱萘后气化焦尾气中:焦油+尘≤1mg/nm3,萘≤2mg/nm3。
48.采用变温吸附(tsa)的对气化焦尾气中的苯和氨予以脱除,脱苯脱氨后气化焦尾气中的苯≤10ppm、氨≤10ppm;本变温吸附(tsa)采用三塔流程,一塔吸附、一塔加热再生、一塔冷吹降温,利用深冷分离出的氮氢尾气作为再生的气源,再生气通过蒸汽加热后对吸附塔进行吹扫加热使吸附剂得以再生,然后冷吹降温使吸附剂恢复吸附能力,三个塔轮流依次循环使用,整个过程连续进行。
49.脱苯脱氨后的气化焦尾气分出28000nm3/h进行耐硫变换,气化焦尾气首先经热的变换气加热至220℃,与补入的4700kg/h水蒸汽混合后进入变换反应器上层,以除去气化焦尾气中的氧和烯烃等有害杂质,氧和烯烃与氢气发生反应放出大量热量,气化焦尾气升温至~310℃,进入喷水降温器喷水降温到210℃后进入变换反应器下层,在此气化焦尾气中的co发生变换反应生成co2和h2,将co干基浓度降至~3.0%v、温度~320℃。在此温度下变换气进入精脱硫罐,由固体脱硫剂脱除变换气中的h2s至≤1ppm,尔后加热原料气化焦尾气自身降温,再去湿法脱碳再生塔作一部分热源后进入水冷器冷却至≤40℃,分离掉冷凝水后送去变换气湿法脱碳系统。
50.变换气组成如下:
51.组分coco2o2ch4h2n2c
n
h
m
合计含量(%)3.0015.26
‑
18.9057.682.462.70100.00
52.变换气气量为:30940nm3/h。
53.上述脱硫、降温后的变换气进入吸收塔用脱碳溶液洗涤,变换气经过半贫液洗涤、贫液洗涤后气体中的co2含量降到0.5%v以下,经过冷却、分离除去气体中微量的脱碳溶液后与另一股10000nm3/h脱苯脱氨后的气化焦尾气混合形成混合气。调节这两路气化焦尾气的相对气量,即可调节混合气的氢碳比。
54.从吸收塔底出来的富液,进入再生塔顶部减压到0.1mpa被来自塔下部的蒸汽汽提。从再生塔顶部汽提出来的气体冷却到40℃以下,分离出的冷凝液返回再生塔顶部作为回流液,冷却后的co2达标排放或去界外利用。
55.从再生塔上段底部出来的脱碳溶液为半贫液,分成两股。大部分的半贫液加压后循环到吸收塔中部;剩余的半贫液经预热后送到再生塔下段继续再生,再生塔下段底出来的脱碳溶液为贫液,经冷却后送到吸收塔的上部循环吸收。再生塔再沸器的热量一部分由前述变换气提供,不足部分由蒸汽补充。
56.脱碳气组成如下:
57.组分coco2o2ch4h2n2c
n
h
m
合计含量(%)3.530.50
‑
22.2067.752.893.13100.00
58.脱碳气气量为:26350nm3/h。
59.混合气组成如下:
60.组分coco2o2ch4h2n2c
n
h
m
合计
含量(%)6.891.850.1321.8163.392.843.09100.00
61.混合气气量为:36350nm3/h。
62.脱苯脱氨后的气化焦尾气与脱碳气形成的混合气,进入混合气精脱硫系统进行精脱硫。混合气与精脱硫后的气体换热升温后进入两台可并联或单独使用的预加氢罐,主要将混合气中的不饱和烃加氢饱和,并反应掉混合气中的氧,同时有少量有机脱硫加氢转化成为无机硫(h2s)。预加氢后的混合气进入一级加氢罐,对混合气中的有机脱硫进一步加氢转化,然后进入由两台可串可并或单独使用的一级精脱硫罐脱除加氢转化生成的h2s。为了进一步降低混合气中的有机硫和无机硫,混合气再进入二级加氢罐及两台二级精脱硫罐。当前面的加氢脱硫能满足工艺对总硫的要求时,净化混合气走旁路(不经过第二级加氢脱硫系统)。前述的净化气经降温后进入超精净化器,以使出口净化气中的总硫含量保证达到<0.05ppm。
63.前述的超精净化气按比例分成两路,分别去甲烷化一段反应器和甲烷化二段反应器。
64.去甲烷化一段反应器的净化气,与循环压缩机增压来的循环气混合,加热升温至≥250℃,进入甲烷化一段反应器进行甲烷化反应。从甲烷化一段反应器出来的高温反应气~505℃,副产2.5mpa蒸汽后温度降至360~400℃,再换热降温后与去甲烷化二段反应器的净化气混合,混合气温度在250~300℃,进入甲烷化二段反应器继续进行甲烷化反应。
65.甲烷化二段反应器出口的高温反应气~505℃,副产2.5mpa蒸汽后温度降至~360℃,预热进甲烷化三段反应器的工艺气、一段原料气、回收热量后分成两路。一路冷却至≤40℃、分离冷凝水、加热后进入甲烷化三段反应器,从甲烷化三段反应器出来的反应气co2的浓度≤30ppm,冷却至≤40℃、分离冷凝水后去深冷分离系统制取lng产品。
66.另一路冷却至≤60℃、分离冷凝水后,经循环气压缩机增压后返回甲烷化系统进口稀释原料气。
67.甲烷化气组成如下:
68.组分coco2o2ch4h2n2c
n
h
m
合计含量(%)
‑‑‑
53.4742.174.110.25100.00
69.甲烷化气气量为:25050nm3/h。
70.上述甲烷化气进入深冷分离系统,通过深冷分离制得lng产品和深冷尾气。在进行深冷分离前,先进行精密过滤和干燥脱水,以分离掉其中1μm以上的杂质和使水分含量≤1ppm。
71.上述甲烷化气进入液化冷箱,经混合冷剂冷却到一定温度从换热器中抽出到精馏塔底再沸器做热源,然后返回液化换热器经混合冷剂冷却、冷凝,再经节流后进入闪蒸罐,闪蒸罐出来富氢尾气节流后返回液化换热器复热后出冷箱,闪蒸罐出来的液体进入精馏塔,经精馏在塔顶得到富氮尾气节流复热后出冷箱,塔底得到lng并进入液化换热器过冷,lng经节流阀节流降到常压送出冷箱进入lng贮槽。
72.出冷箱的富氢尾气和富氮尾气(即深冷尾气),部分作为本系统干燥脱水的再生气,之后与剩余的深冷尾气一起作脱苯脱氨再生的气源。
73.lng组成如下:
74.组分coco2o2ch4h2n2c
n
h
m
合计
含量(%)
‑‑‑
98.54
‑
0.990.47100.00
75.lng产量为:13200nm3/h。
76.深冷尾气组成如下:
77.组分coco2o2ch4h2n2c
n
h
m
合计含量(%)
‑‑‑
3.2789.147.59
‑
100.00
78.深冷尾气气量为:11850nm3/h。
79.以上所述仅为本实用新型的较佳实施例而已,并不用以限制本实用新型,凡在本实用新型的精神和原则之内所作的任何修改、等同替换和改进等,均应包含在本实用新型的保护范围之内。