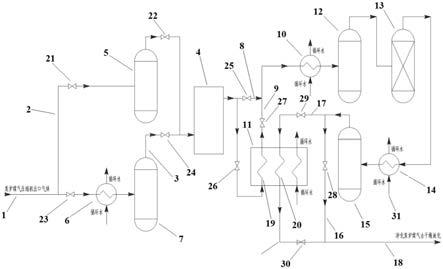
1.本实用新型属于焦炉煤气非甲烷化液化技术领域,涉及余热,具体涉及一种焦炉煤气液化工艺中的余热利用装置。
背景技术:
2.焦炉煤气是重要的焦化副产品,其原有的利用方式为直接燃烧,造成了大量的浪费,如今国家环保政策逐渐严格,焦炉煤气通常用于生产化工产品,非甲烷化的液化分离便是其中的一个重要工艺方向。在焦炉煤气非甲烷化液化工艺中,压缩机出口和精脱硫末段有大量余热未经利用,充分、经济的回收这部分热量,是装置生产的一个重要方面。目前我国焦炉煤气非甲烷化液化工艺对压缩机出口和精脱硫的热量通常直接采用循环水冷却的方式,未对此部分热量进行回收。
3.现有技术中至少存在以下技术缺陷:
4.现有技术中的制造工艺,仅仅是满足生产工艺的需求,其工艺过程中的压缩机出口、精脱硫末段气体温度可达100
‑
150℃,现有技术中直接采用循环水对气体冷却后进入下游,未对该部分热量进行利用,浪费大量能源。
技术实现要素:
5.针对现有技术存在的不足,本实用新型的目的在于,提供了一种焦炉煤气液化工艺中的余热利用装置,解决现有技术的工艺过程不能有效利用气体热量的技术问题。
6.为了解决上述技术问题,本实用新型采用如下技术方案予以实现:
7.一种焦炉煤气液化工艺中的余热利用装置,包括焦炉煤气压缩机出口气体管道和净化焦炉煤气去干燥液化管道,焦炉煤气压缩机出口气体管道分别与第一支路管道的一端和第二支路管道的一端相连通,第一支路管道与第二支路管道并联设置,第一支路管道的另一端和第二支路管道的另一端分别与精脱硫装置的进气口相连通;
8.所述的第一支路管道上设置有第一分离器,所述的第二支路管道上沿着气体流动方向依次串联设置有第一冷却器和第二分离器;
9.所述的精脱硫装置的出气口分别与第三支路管道的一端和第四支路管道的一端相连通,第三支路管道与第四支路管道并联设置,第三支路管道的另一端和第四支路管道的另一端分别与第二冷却器的进气口相连通;
10.所述的第四支路管道上连通设置有溴化锂装置内的第一蒸发组件管道;
11.所述的第二冷却器的出气口与第三分离器的进气口相连通,第三分离器的出气口与脱碳吸收塔的进气口相连通,脱碳吸收塔的出气口与第三冷却器的进气口相连通,第三冷却器的出气口与第四分离器的进气口相连通;
12.所述的第四分离器的出气口分别与第五支路管道的一端和第六支路管道的一端相连通,第五支路管道与第六支路管道并联设置,第五支路管道的另一端和第六支路管道的另一端分别与净化焦炉煤气去干燥液化管道相连通;
13.所述的第六支路管道上连通设置有溴化锂装置内的第二蒸发组件管道。
14.本实用新型还具有如下技术特征:
15.所述的第一支路管道上第一分离器之前设置有第一阀门,第一分离器之后设置有第二阀门;所述的第二支路管道上第一冷却器之前设置有第三阀门,第二分离器之后设置有第四阀门。
16.所述的第三支路管道上设置有第五阀门;所述的第四支路管道上溴化锂装置之前设置有第六阀门,溴化锂装置之后设置有第七阀门。
17.所述的第五支路管道上设置有第八阀门;所述的第六支路管道上溴化锂装置之前设置有第九阀门,溴化锂装置之后设置有第十阀门。
18.所述的第一冷却器、第二冷却器、第三冷却器和溴化锂装置上均设置有循环水管路。
19.本实用新型与现有技术相比,具有如下技术效果:
20.(ⅰ)本实用新型的装置将压缩机出口的气体热量加以利用,使精脱硫末段的气体温度升高,再将精脱硫末段的高温气体通入溴化锂装置,预冷要进入干燥液化工段的气体,起到降低液化能耗的作用。
21.(ⅱ)蒸发组件管道对排出产物进行过滤和利用,通过蒸发组件管道吸收排出产物中的热量,解决技术中焦炉煤气压缩机、精脱硫末段直接通过循环水冷却浪费热能的技术问题,能源回收再利用,实现现代工业节能化目标。
22.(ⅲ)本实用新型的装置用以完善焦炉煤气液化工艺的功能,满足人们对降低焦炉煤气液化能耗的需求。
附图说明
23.图1为焦炉煤气液化工艺中的余热利用装置的整体结构示意图。
24.图中各个标号的含义为:1
‑
焦炉煤气压缩机出口气体管道,2
‑
第一支路管道,3
‑
第二支路管道,4
‑
精脱硫装置,5
‑
第一分离器,6
‑
第一冷却器,7
‑
第二分离器,8
‑
第三支路管道;9
‑
第四支路管道,10
‑
第二冷却器,11
‑
溴化锂装置,12
‑
第三分离器,13
‑
脱碳吸收塔,14
‑
第三冷却器,15
‑
第四分离器,16
‑
第五支路管道,17
‑
第六支路管道,18
‑
净化焦炉煤气去干燥液化管道,19
‑
第一蒸发组件管道,20
‑
第二蒸发组件管道,21
‑
第一阀门,22
‑
第二阀门,23
‑
第三阀门,24
‑
第四阀门,25
‑
第五阀门,26
‑
第六阀门,27
‑
第七阀门,28
‑
第八阀门,29
‑
第九阀门,30
‑
第十阀门,31
‑
循环水管路。
25.以下结合实施例对本实用新型的具体内容作进一步详细解释说明。
具体实施方式
26.焦炉煤气是指用几种烟煤配制成炼焦用煤,在炼焦炉中经过高温干馏后,在产出焦炭和焦油产品的同时所产生的一种可燃性气体,是炼焦工业的副产品。焦炉煤气的化产利用工艺和国内发展现密切相关,以体积比计,其主要成分为氢气(55%~60%)和甲烷(23%~27%),另外还含有少量的一氧化碳(5%~8%)、c2以上不饱和烃(2%~4%)、二氧化碳(1.5%~3%)、氧气(0.3%~0.8%))、氮气(3%~7%)。其中氢气、甲烷、一氧化碳、c2以上不饱和烃为可燃组分,二氧化碳、氮气、氧气为不可燃组分,另外其还含有少量的焦油、
苯、萘、硫化氢、有机硫等杂质。
27.目前焦炉煤气的化产利用有制lng、制甲醇、制甲醇联产lng、合成氨联产lng等,以制甲醇联产lng(液化天然气)流程液化前的主要过程为例:先加压至0.45~0.8mpa进入tsa(变温吸附)脱除焦油、萘、苯等,再加压到2.2~2.8mpa进入精脱硫脱除有机硫、无机硫,然后经mdea(n
‑
甲基二乙醇胺)脱碳、分子筛脱水、脱汞后进入液化系统。
28.其中在投入生产过程能够采用本实用新型的焦炉煤气液化工艺中的余热利用装置进行能源回收再利用。
29.需要说明的是,本实用新型中的所有零部件,在没有特殊说明的情况下,均采用本领域已知的零部件。
30.以下给出本实用新型的具体实施例,需要说明的是本实用新型并不局限于以下具体实施例,凡在本技术技术方案基础上做的等同变换均落入本实用新型的保护范围。
31.实施例:
32.本实施例给出一种焦炉煤气液化工艺中的余热利用装置,如图1所示,包括焦炉煤气压缩机出口气体管道1和净化焦炉煤气去干燥液化管道18,焦炉煤气压缩机出口气体管道1分别与第一支路管道2的一端和第二支路管道3的一端相连通,第一支路管道2与第二支路管道3并联设置,第一支路管道2的另一端和第二支路管道3的另一端分别与精脱硫装置4的进气口相连通;
33.第一支路管道2上设置有第一分离器5,第二支路管道3上沿着气体流动方向依次串联设置有第一冷却器6和第二分离器7;
34.精脱硫装置4的出气口分别与第三支路管道8的一端和第四支路管道9的一端相连通,第三支路管道8与第四支路管道9并联设置,第三支路管道8的另一端和第四支路管道9的另一端分别与第二冷却器10的进气口相连通;
35.第四支路管道9上连通设置有溴化锂装置11内的第一蒸发组件管道19;
36.第二冷却器10的出气口与第三分离器12的进气口相连通,第三分离器12的出气口与脱碳吸收塔13的进气口相连通,脱碳吸收塔13的出气口与第三冷却器14的进气口相连通,第三冷却器14的出气口与第四分离器15的进气口相连通;
37.第四分离器15的出气口分别与第五支路管道16的一端和第六支路管道17的一端相连通,第五支路管道16与第六支路管道17并联设置,第五支路管道16的另一端和第六支路管道17的另一端分别与净化焦炉煤气去干燥液化管道18相连通;
38.第六支路管道17上连通设置有溴化锂装置11内的第二蒸发组件管道20。
39.本实施例中,精脱硫装置4采用本领域现有技术中已知常用的精脱硫装置,溴化锂装置11采用本领域现有技术中已知常用的溴化锂装置。
40.作为本实施例的一种具体方案,第一支路管道2上第一分离器5之前设置有第一阀门21,第一分离器5之后设置有第二阀门22;第二支路管道3上第一冷却器6之前设置有第三阀门23,第二分离器7之后设置有第四阀门24。
41.作为本实施例的一种具体方案,第三支路管道8上设置有第五阀门25;第四支路管道9上溴化锂装置11之前设置有第六阀门26,溴化锂装置11之后设置有第七阀门27。
42.作为本实施例的一种具体方案,第五支路管道16上设置有第八阀门28;第六支路管道17上溴化锂装置11之前设置有第九阀门29,溴化锂装置11之后设置有第十阀门30。
43.作为本实施例的一种具体方案,第一冷却器6、第二冷却器10、第三冷却器14和溴化锂装置11上均设置有循环水管路31。
44.将本实用新型的装置用于精脱硫与液化之间无合成反应的焦炉煤气液化工艺中,其过程具体包括以下步骤:
45.s1:在焦炉煤气压缩机出口气体的第一冷却器6上增设旁路,即第一支路管道2,使80~130℃的压缩机出口焦炉煤气不经第一冷却器6的冷却直接进入精脱硫工段的精脱硫装置4。
46.s2:焦炉煤气进入精脱硫工段的精脱硫装置4后,与催化加氢反应和氧化锌脱硫后的焦炉煤气换热,最终未进入需要循环水冷却的第一冷却器6的气体温度由于利用了压缩机出口的热量而达到了160~220℃,将此气体通入溴化锂装置11内的第一蒸发组件管道19,回收热量至90~130℃,然后再通入需要循环水冷却的第二冷却器10中冷却至40℃进入mdea脱碳工段的脱碳吸收塔13。
47.s3:在焦炉煤气通过mdea脱碳工段的脱碳吸收塔13后温度有少许升高,在经过需要循环水冷却的第三冷却器14冷却至40℃后,返回精脱硫工段处的溴化锂装置11内的第二蒸发组件管道20进行预冷至7℃后进入干燥液化工段的净化焦炉煤气去干燥液化管道18,以降低液化工段的能耗。
48.具体的,本实用新型的装置的流体热量交换的步骤为:
49.a1:焦炉煤气压缩机出口气体不通过循环水冷却,以利用这部分热量;
50.a2:由于利用了压缩机出口的热量,精脱硫在自身进出口换热后的出口温度可以达到130~250℃;
51.a3:在精脱硫末段设置溴化锂装置,利用130~250℃的气体热量作为热源;
52.a4:精脱硫冷却后的气体经过mdea吸收塔吸收、冷却后返回精脱硫末段的溴化锂装置进行预冷后去干燥液化工段。
53.应用例:
54.以45000nm3/h的焦炉煤气制甲醇联产lng项目为例,45000nm3/h的焦炉煤气在压缩机出口温度为120℃,不经冷却进入精脱硫装置4,通过精脱硫装置4后去溴化锂装置11的焦炉煤气为180℃,通过溴化锂装置11后降为120℃;从脱碳吸收塔13经冷却分离后的焦炉煤气为40℃,通过溴化锂装置11后降为10℃进入冷箱。焦炉煤气由40℃降至10℃,热量降低7400mj/h。
55.现有技术的方案:
56.45000nm3/h的焦炉煤气在焦炉煤气压缩机出,120℃,经冷却器冷却至。40℃进入精脱硫装置4,通过精脱硫装置4后直接用循环水冷却到40℃后进入mdea脱碳,脱碳后的焦炉煤气再次用冷却水冷却到40℃后进入冷箱。
57.应用例与现有技术的方案的数据对比:
58.采用本实用新型的装置可使进冷箱的45000nm3/h焦炉煤气的温度由原来的40℃降为10℃,节约冷量约7400mj/h,节省掉此部分制冷所需的电能。