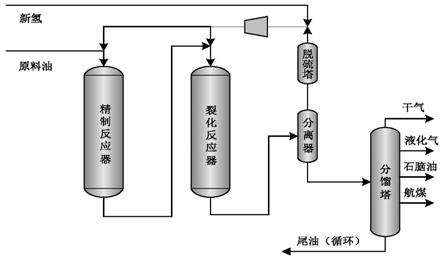
1.本发明涉及一种加氢裂化方法,特别是涉及一种加氢裂化方法,属于加氢裂化技术领域。
背景技术:
2.加氢裂化技术具有生产灵活度高、原料适应性强以及产品质量高的特点,在调节全厂生产平衡方面发挥着中流砥柱的作用,加氢裂化的工艺产品包括天然气、液化气、石脑油、喷气燃料、柴油以及尾油,传统加氢裂化工艺技术根据市场变化以多产石脑油或者中间馏分油为主,但是近些年来,由于北方冬天供暖,煤的简单燃烧使用造成大气污染严重,空气中pm2.5以及pm10严重超标。
3.我国从2017年起开始实施煤改气的供暖方案,其中所采用的燃气主要包括天然气、煤气、液化气以及沼气等,燃气属于清洁能源,因此可以很大程度地解决环境污染问题,天然气的使用量在燃气中占比最大,但与煤炭资源相比,我国天然气资源本就匮乏——我国天然气的使用总量中,有大约30%需要进口,即使没有大规模的“煤改气”,我国天然气供应也比较紧张,大量使用天然气必会导致对外依存度过高,影响国家能源安全,液化气是加氢裂化反应中的重要产物,其主要成分为c3与c4,其可以作为一种化工基本原料和新型燃料。
4.液化石油气经过分离得到乙烯、丙烯、丁烯、丁二烯等,用来生产合塑料、合成橡胶、合成纤维及生产医药、炸药、染料等产品,用液化气作燃料,由于其热值高、无烟尘、无炭渣,操作使用方便,已广泛地进入人们的生活领域。此外,液化石油气还用于切割金属,用于农产品的烘烤和工业窑炉的焙烧等,因此开发多产液化气的加氢裂化技术,解决我国燃气不足、供暖障碍的问题变得迫在眉睫。
5.针对上述问题,不仅需要开发具有合适孔结构、酸性质以及活性金属的催化剂,而且还要筛选合适的原料,不同的硫化条件以及工艺操作条件,以达到多产液化气的目的。
6.加氢裂化催化剂通常采用含有周期表中第
ⅷ
族及第
ⅵ
b族的金属氧化物负载到耐熔无机多孔材料中,一般采用γ
‑
氧化铝、无定型硅铝以及分子筛为载体,通过浸渍工艺过程,制备出催化剂前体,再经过若干步的干燥和焙烧工序制备出成品催化剂。
7.以无定型硅铝与氧化铝混合后作为载体的加氢裂化催化剂具有稳定性高、中油选择性高以及耐氮性能好的特点,以y分子筛与氧化铝混合后作为载体的加氢裂化催化剂具有芳烃转化能力强、活性高以及温度敏感度高的特点,以zsm
‑
5与氧化铝混合后作为载体的加氢裂化催化剂具有吸附能力强、择形选择性优异、裂化能力强以及二次裂解多的特点,以β分子筛与氧化铝混合为载体的加氢裂化催化剂具有烷基化能力强以及中油选择性高的特点,常规加氢裂化原料为减压蜡油、催化柴油、直馏柴油、焦化柴油、焦化蜡油、植物油、页岩油以及合成油等。
8.工业上加氢裂化装置的干气收率一般不高于2%,液化气收率不高于8%。液化气的收率主要取决于链烷烃的β断裂以及环烷烃的“剥皮反应”,因此为了提高液化气的收率
需要提高其酸性、减小孔径以及增加芳烃转化能力,而往往单一的分子筛体系已经无法满足要求。
9.在加氢裂化技术中,关于加氢裂化方法与技术的报道较多,但关于多产液化气的加氢裂化方法以及催化剂制备方面较少,现有技术中cn 102807895 b公开了一种多产中间馏分油的加氢裂化方法,将新鲜原料油以并流的方式同时引入加氢精制反应器和加氢裂化反应器,全部或部分尾油馏分进入加氢裂化反应器,加氢裂化反应器的反应流出物与部分原料油一起进入加氢精制反应器,该方法能处理重质馏分油,最大量生产中间馏分油。仅有尾油馏分进入加氢裂化反应器,提高了中间馏分油的选择性,部分原料油进入加氢裂化反应器,防止了加氢裂化反应器系统中无氨环境下加氢裂化催化剂的裂化活性过强,较多中间馏分油二次裂化现象的发生,从而有效提高中间馏分油的收率。
10.但是部分原料油与尾油混合后直接进入加氢裂化反应器,会加速第一床层加氢裂化催化剂的中毒速率,造成第一床层温升较低,提高反应器入口温度造成整个反应器温度倒挂,不利于反应器长周期运转。
11.cn103028442b公开了一种多孔载体的制备方法及其应用。该载体不仅具有较大的孔径和孔容,而且具有较高的孔径集中度,将发明的多孔载体应用在烃油加氢裂化技术上,其具有较高的催化活性和中间馏分油选择性。
12.cn104611040b公开了一种加氢裂化方法,重质馏分油与氢气混合后先进入加氢精制反应器进行加氢精制反应;加氢精制反应流出物与裂化反应器内级配的催化剂床层接触反应;其中加氢裂化反应器内设置至少两个裂化催化剂床层,按照反应物料的流动方向,加氢裂化催化剂的加氢活性呈降低趋势。
13.该方法可以在保证重组分加氢裂化效果的同时,减少了重石脑油的过度加氢及过度裂化,降低化学氢耗,从而提高了重石脑油的芳潜和选择性。
14.cn 100526434c公开了一种两段加氢裂化方法,主要特点在于第一段未转化油作为第二段进料与氢气混合后经过与第一段生成油换热进入第二段加氢裂化反应器,第二段无需加热炉,节约投资并降低了操作危险性。
15.但上述专利中并没有提供关于以各种重质馏分油为原料,生产高质量中间馏分油产品的具有加氢裂化工艺过程,使其在生产流程上具有明显的缺陷,而且现有的加氢裂化剂分子筛载体单一,为此设计一种加氢裂化方法来优化上述问题。
技术实现要素:
16.本发明的主要目的是为了提供一种加氢裂化方法,通过控制载体内部不同反应区内发生分级加氢裂化反应,增加芳烃、环烷烃以及链烷烃深度转化效率,并且进一步调变工艺流程从而达到多产液化气的目的。
17.本发明的目的可以通过采用如下技术方案达到:
18.一种加氢裂化方法,
19.步骤1:原料油与氢气混合进入加氢精制反应器发生加氢精制反应;
20.步骤2:反应流出物进入加氢裂化反应器;
21.步骤3:加氢裂化生成油经过高低压分离器进入分馏塔,得到干气、液化气、石脑油、航煤以及尾油;
22.步骤4::将尾油循环至加氢精制或者加氢裂化反应器入口进行深度裂解反应;
23.步骤5:将加氢精制反应器延物流方向分为1~6个反应区。
24.优选的,在步骤1中所采用的原料油为蜡油原料,并在加氢精制反应器内加入加氢精制剂,该加氢精制剂由载体和金属组成。
25.优选的,在步骤1中采用的金属为元素周期表中第
ⅵ
b金属组分,如钨或/和钼,并以金属氧化物重量计为5
‑
40wt%,载体为氧化铝、无定型硅铝、分子筛的单一载体或者混合物,载体按重量计为60
‑
90wt%,由以上载体负载活性金属后,制备加氢精制催化剂,或采用工业催化剂如ff
‑
36、ff
‑
46、ff
‑
56或ff
‑
66。
26.优选的,步骤3中在加氢裂化反应器中还加入加氢裂化剂以cu
‑
zsm
‑
5/y、氧化铝和无定型硅铝为载体,以第
ⅷ
族和第
ⅵ
b族金属为活性金属组分,第
ⅷ
族金属为co和/或ni,第
ⅵ
b族金属为w和/或mo,或以单一的第
ⅶ
主族金属为活性组分,包括pt、pd和/或rh。
27.优选的,其中步骤3中加入的加氢裂化剂制备方法包括如下步骤:
28.步骤1:将cu
‑
zsm
‑
5/y、氧化铝和无定型硅铝几种载体混合均匀后加入粘合剂;
29.步骤2:对步骤1的产物进行充分碾压成型,然后干燥、焙烧处理得到催化剂载体;
30.步骤3:用含有活性金属组分的溶液浸渍催化剂载体;
31.步骤4:进行再次干燥、焙烧后得到加氢裂化催化剂。
32.优选的,其中步骤3中采用的浸渍方法为等体积浸渍法、过量体积浸渍法或蒸汽浸渍法;
33.以催化剂的重量为基准,cu
‑
zsm
‑
5/y载体10~80wt%,氧化铝0~80wt%,无定形硅铝0~80wt%,活性金属以氧化物计的含量为10~40wt%。
34.优选的,步骤1中的cu
‑
zsm
‑
5/y采用原位水热合成法制备,具体包括如下步骤:
35.步骤1:控制ph在9~13之间,si/al在10:1~150:1之间,依次将铝源、模板剂以及水混合后搅拌至溶液澄清;
36.步骤2:加入硅源继续搅拌1~3h,控制cu/al摩尔比在1:5~1:100之间,加入适当比例的铜源继续搅拌1~2h,将混合溶液其并置于60~100℃的条件下加热蒸发除去醇和水;
37.步骤3:将得到的cu
‑
zsm
‑
5晶种与合成y分子筛所需原料质量按照5%~50%比例混合,合成y分子筛原料中的硅源、铝源、碱液与水的摩尔配比为1.5~15.0na2o:0.5~1.5al2o3:4~14sio2:160~270h2o;
38.步骤4:将混合液于50~80℃搅拌2~8h后于90~110℃下晶化,得到的晶化产物经冷却、过滤除去母液,滤饼用去蒸馏水洗至ph为10以下,干燥得到cu
‑
zsm
‑
5/y复合载体;
39.步骤5:将复合材料cu
‑
zsm
‑
5/y放置于0.5~1.5mol/l的nh4cl溶液中,其中固液投料质量比控制在1:5~1:40,混合液在60~90℃下搅拌2~24h或对cu
‑
zsm
‑
5/y复合载体做水热处理;
40.步骤6:然后用去离子水洗涤,并在50~100℃条件下干燥4~24h,此过程重复2~6次,在450~550℃条件下焙烧4~10h后即得到cu
‑
zsm
‑
5/hy型复合分子筛。
41.优选的,步骤1中铝源选自硫酸铝、铝酸钠、异丙醇铝、氯化铝中的至少一种;
42.模板剂选自氟化钠、氟化铵、四乙基氢氧化铵、四乙基溴化铵中的至少一种;
43.步骤2中硅源选自水玻璃、硅溶胶、硅酸钠、白炭黑或活性白土中的至少一种;
44.铜源选自硝酸铜、硫酸铜、氯化亚铜中的至少一种;
45.步骤3中硅源为含硅化合物,包括水玻璃、硅溶胶、正硅酸四乙酯;
46.铝源为含铝化合物,包括水合氧化铝、铝盐;
47.碱液为氢氧化钠、氢氧化钾。
48.优选的,步骤4中的cu
‑
zsm
‑
5/y复合载体做水热处理具体包括如下步骤:
49.步骤1:在100%水蒸气氛围下,500~800℃处理1~5h;
50.步骤2:水热处理后,使用浓度为0.1~1.0%mol/l的硝酸脱除非骨架铝,最终控制cu
‑
zsm
‑
5/y载体的si/al比为2~50之间。
51.本发明的有益技术效果:
52.本发明提供的一种加氢裂化方法,本发明方法通过原位合成cu
‑
zsm
‑
5/y载体,该载体具有多级孔道,较强的酸性。
53.y分子筛包裹cu
‑
zsm
‑
5载体,反应物分子特别是芳烃与环烷烃优先与孔径较大的y分子筛接触,一方面可以减少传质阻力,另一方面可以增加环烷烃的断裂开环反应。
54.cu
‑
zsm
‑
5载体孔径较小,二次裂解能力强,掺入cu金属后可将增加其对环烷烃与链烷烃吸附能力,有利于环烷烃“剥皮反应”与链烷烃的β断裂反应,从而增加c3与c4的收率。
55.将合成的载体cu
‑
zsm
‑
5/y负载活性金属后即可制备成加氢裂化催化剂。
56.为了最大限度多产轻组分烃类产品,将柴油以及尾油馏分循环至精制反应器或者裂化反应器入口,经过深度裂解转化为航煤、石脑油、液化气以及干气组分,还可以实现压减柴汽比的目的。
附图说明
57.图1为按照本发明的一种加氢裂化方法的一优选实施例的工艺流程图。
具体实施方式
58.为使本领域技术人员更加清楚和明确本发明的技术方案,下面结合实施例及附图对本发明作进一步详细的描述,但本发明的实施方式不限于此。
59.如图1所示,本实施例提供的一种加氢裂化方法,
60.步骤1:原料油与氢气混合进入加氢精制反应器发生加氢精制反应;
61.步骤2:反应流出物进入加氢裂化反应器;
62.步骤3:加氢裂化生成油经过高低压分离器进入分馏塔,得到干气、液化气、石脑油、航煤以及尾油;
63.步骤4::将尾油循环至加氢精制或者加氢裂化反应器入口进行深度裂解反应;
64.步骤5:将加氢精制反应器延物流方向分为1~6个反应区。
65.通常的加氢裂化工艺条件为:加氢精制平均反应温度250~420℃,最好为280~400℃;
66.加氢裂化平均反应温度280~420℃,最好为300~400℃;反应氢分压6~20mpa,最好为8~16mpa;
67.氢油体积比为300~2000h
‑1,最好为500~1200h
‑1;加氢精制液时体积空速为0.1
~2h
‑1,最好为0.5~1.5h
‑1;
68.加氢裂化液时体积空速为0.5~3h
‑1,最好为1.0~2.5h
‑
1;
69.优选分为2~4个反应区;加氢裂化反应器延物流方向分为2~6个反应区优选分为3~5个反应区;
70.表1原料油性质
[0071][0072][0073]
在本实施例中,在步骤1中所采用的原料油为蜡油原料,并在加氢精制反应器内加入加氢精制剂,该加氢精制剂由载体和金属组成。
[0074]
在本实施例中,在步骤1中采用的金属为元素周期表中第
ⅵ
b金属组分,如钨或/和钼,并以金属氧化物重量计为5
‑
40wt%,载体为氧化铝、无定型硅铝、分子筛的单一载体或者混合物,载体按重量计为60
‑
90wt%,由以上载体负载活性金属后,制备加氢精制催化剂,或采用工业催化剂如ff
‑
36、ff
‑
46、ff
‑
56或ff
‑
66。
[0075]
在本实施例中,步骤3中在加氢裂化反应器中还加入加氢裂化剂以cu
‑
zsm
‑
5/y、氧化铝和无定型硅铝为载体,以第
ⅷ
族和第
ⅵ
b族金属为活性金属组分,第
ⅷ
族金属为co和/或ni,第
ⅵ
b族金属为w和/或mo,或以单一的第
ⅶ
主族金属为活性组分,包括pt、pd和/或rh。
[0076]
在本实施例中,其中步骤3中加入的加氢裂化剂制备方法包括如下步骤:
[0077]
步骤1:将cu
‑
zsm
‑
5/y、氧化铝和无定型硅铝几种载体混合均匀后加入粘合剂;
[0078]
步骤2:对步骤1的产物进行充分碾压成型,然后干燥、焙烧处理得到催化剂载体;
[0079]
步骤3:用含有活性金属组分的溶液浸渍催化剂载体;
[0080]
步骤4:进行再次干燥、焙烧后得到加氢裂化催化剂。
[0081]
在本实施例中,其中步骤3中采用的浸渍方法为等体积浸渍法、过量体积浸渍法或蒸汽浸渍法;
[0082]
以催化剂的重量为基准,cu
‑
zsm
‑
5/y载体10~80wt%,氧化铝0~80wt%,无定形
硅铝0~80wt%,活性金属以氧化物计的含量为10~40wt%。
[0083]
一种加氢裂化方法,步骤1中的cu
‑
zsm
‑
5/y采用原位水热合成法制备,具体包括如下步骤:
[0084]
步骤1:控制ph在9~13之间,si/al在10:1~150:1之间,依次将铝源、模板剂以及水混合后搅拌至溶液澄清;
[0085]
步骤2:加入硅源继续搅拌1~3h,控制cu/al摩尔比在1:5~1:100之间,加入适当比例的铜源继续搅拌1~2h,将混合溶液其并置于60~100℃的条件下加热蒸发除去醇和水;
[0086]
步骤3:将得到的cu
‑
zsm
‑
5晶种与合成y分子筛所需原料质量按照5%~50%比例混合,合成y分子筛原料中的硅源、铝源、碱液与水的摩尔配比为1.5~15.0na2o:0.5~1.5al2o3:4~14sio2:160~270h2o;
[0087]
步骤4:将混合液于50~80℃搅拌2~8h后于90~110℃下晶化,得到的晶化产物经冷却、过滤除去母液,滤饼用去蒸馏水洗至ph为10以下,干燥得到cu
‑
zsm
‑
5/y复合载体;
[0088]
步骤5:将复合材料cu
‑
zsm
‑
5/y放置于0.5~1.5mol/l的nh4cl溶液中,其中固液投料质量比控制在1:5~1:40,混合液在60~90℃下搅拌2~24h或对cu
‑
zsm
‑
5/y复合载体做水热处理;
[0089]
步骤6:然后用去离子水洗涤,并在50~100℃条件下干燥4~24h,此过程重复2~6次,在450~550℃条件下焙烧4~10h后即得到cu
‑
zsm
‑
5/hy型复合分子筛。
[0090]
在本实施例中,步骤1中铝源选自硫酸铝、铝酸钠、异丙醇铝、氯化铝中的至少一种;
[0091]
模板剂选自氟化钠、氟化铵、四乙基氢氧化铵、四乙基溴化铵中的至少一种;
[0092]
步骤2中硅源选自水玻璃、硅溶胶、硅酸钠、白炭黑或活性白土中的至少一种;
[0093]
铜源选自硝酸铜、硫酸铜、氯化亚铜中的至少一种;
[0094]
步骤3中硅源为含硅化合物,包括水玻璃、硅溶胶、正硅酸四乙酯;
[0095]
铝源为含铝化合物,包括水合氧化铝、铝盐;
[0096]
碱液为氢氧化钠、氢氧化钾。
[0097]
在本实施例中,步骤4中的cu
‑
zsm
‑
5/y复合载体做水热处理具体包括如下步骤:
[0098]
步骤1:在100%水蒸气氛围下,500~800℃处理1~5h;
[0099]
步骤2:水热处理后,使用浓度为0.1~1.0%mol/l的硝酸脱除非骨架铝,最终控制cu
‑
zsm
‑
5/y载体的si/al比为2~50之间。
[0100]
表2工业催化剂以及分子筛的性质
[0101]
[0102][0103]
表3反应条件
[0104]
加氢精制剂ff
‑
66氢分压,mpa14.7精制/裂化反应温度,℃370/390氢油比900:1精制/裂化体积空速,h
‑11.0/1.5新鲜进料量,g/h100
[0105]
表4实施例中催化剂载体的组成以及加氢裂化装置操作方式
[0106]
项目实施例1实施例2实施例3实施例4活性金属,wt%5%nio+25%wo35%nio+25%mo37.5%nio+30%wo35%nio+25%wo3催化剂载体cu
‑
zsm
‑
5/ycu
‑
zsm
‑
5/ycu
‑
zsm
‑
5/ycu
‑
zsm
‑
5/y操作方式全循环1全循环1全循环1全循环2
[0107]
表5对比例中催化剂载体的组成以及加氢裂化装置操作方式
[0108]
项目对比例1对比例2对比例3对比例4活性金属,wt%5%nio+25%wo35%nio+25%wo35%nio+25%wo35%nio+25%wo3催化剂载体zsm
‑
5/ycu
‑
zsm
‑
5/y工业zsm
‑
5工业usy操作方式全循环1一次通过全循环1全循环1
[0109]
以下实施例和对比例中所使用的原料油为伊朗vgo,其性质如表1所示。以典型的三反应区为例,装置的简易流程图如图1所示。实施例与对比例中所使用的zsm
‑
5以及usy载体均为工业剂,采购于天津南化催化剂公司,两者以及工业精制剂ff
‑
66的性质如表2所示,所有实施例与对比例的工艺评价条件如表3所示,实施例与对比例中催化剂的组成以及加氢裂化装置操作方式如表4与表5所示。表中提到的全循环1为>260℃尾油循环至精制反应器入口,全循环2为>260℃尾油循环至裂化反应器入口。
[0110]
实施例1
[0111]
称取0.3mol异丙醇铝、3mol的四丙基氢氧化铵溶液(重量浓度为21%)加入2000g水搅拌至溶液澄清;加入7mol正硅酸乙酯,继续搅拌1h,然后加入0.03mol的cucl2,将混合溶液放置于80℃的条件下蒸发除去水和醇。称取1.5mol水合氧化铝,20mol水玻璃与4l的5mol/l的naoh溶液与上述cu
‑
zsm
‑
5的晶种混合,并将混合液于60℃搅拌4h后于100℃下晶化,得到的晶化产物经冷却、过滤除去母液,滤饼用去蒸馏水洗至ph为10以下,干燥得到cu
‑
zsm
‑
5/y复合载体。称取20g cu
‑
zsm
‑
5/y放置于的200g的nh4cl(1mol/l)溶液中,在80℃下搅拌4h,用去离子水洗涤后在80℃下干燥6h,此过程重复4次,将过滤后的固体500℃下焙烧6h。将上述合成的材料采用等体积浸渍法负载ni、w活性金属后得到niw/cu
‑
zsm
‑
5/y。以ff
‑
66为加氢精制剂,niw/cu
‑
zsm
‑
5/y为加氢裂化催化剂,采用全循环1的操作方式,原料油为伊朗vgo,其他工艺条件如表3所示。
[0112]
实施例2
[0113]
将实施例1中经水热处理后的cu
‑
zsm
‑
5/y材料采用等体积浸渍法负载ni、mo活性金属后得到nimo/cu
‑
zsm
‑
5/y。以ff
‑
66为加氢精制剂,nimo/cu
‑
zsm
‑
5/y为加氢裂化催化剂,采用全循环1的操作方式,原料油为伊朗vgo,其他工艺条件如表3所示。
[0114]
实施例3
[0115]
将实施例1中经水热处理后的cu
‑
zsm
‑
5/y材料采用等体积浸渍法负载ni、w活性金属后得到较高金属含量的niw/cu
‑
zsm
‑
5/y。以ff
‑
66为加氢精制剂,niw/cu
‑
zsm
‑
5/y为加氢裂化催化剂,采用全循环1的操作方式,原料油为伊朗vgo,其他工艺条件如表3所示。
[0116]
实施例4
[0117]
将实施例1中经水热处理后的cu
‑
zsm
‑
5/y材料采用等体积浸渍法负载ni、w活性金属后得到niw/cu
‑
zsm
‑
5/y。以ff
‑
66为加氢精制剂,niw/cu
‑
zsm
‑
5/y为加氢裂化催化剂,采用全循环2的操作方式,原料油为伊朗vgo,其他工艺条件如表3所示。
[0118]
对比例1
[0119]
称取0.3mol异丙醇铝、3mol的四丙基氢氧化铵溶液(重量浓度为21%)加入2000g水搅拌至溶液澄清;加入7mol正硅酸乙酯,继续搅拌1h,将混合溶液放置于80℃的条件下蒸发除去水和醇。称取1.5mol水合氧化铝,20mol水玻璃与4l的5mol/l的naoh溶液与上述zsm
‑
5的晶种混合,并将混合液于60℃搅拌4h后于100℃下晶化,得到的晶化产物经冷却、过滤除去母液,滤饼用去蒸馏水洗至ph为10以下,干燥得到zsm
‑
5/y复合载体。称取20g zsm
‑
5/y放置于的200g的nh4cl(1mol/l)溶液中,在80℃下搅拌4h,用去离子水洗涤后在80℃下干燥6h,此过程重复4次,将过滤后的固体500℃下焙烧6h。将铵交换后合成的zsm
‑
5/y,做水热处理,处理条件如下:在100%水蒸气氛围下,700℃处理2h。水热处理后,使用浓度为0.5%mol/l的硝酸脱除非骨架铝。将合成的材料采用等体积浸渍法负载ni、w活性金属后得到niw/zsm
‑
5/y。以ff
‑
66为加氢精制剂,niw/zsm
‑
5/y为加氢裂化催化剂,采用全循环1的操作方式,原料油为伊朗vgo,其他工艺条件如表3所示。
[0120]
对比例2
[0121]
将实施例1中经水热处理后的cu
‑
zsm
‑
5/y材料采用等体积浸渍法负载ni、w活性金属后得到niw/cu
‑
zsm
‑
5/y。以ff
‑
66为加氢精制剂,经水热处理的niw/cu
‑
zsm
‑
5/y为加氢裂化催化剂,采用一次通过的操作方式,原料油为伊朗vgo,其他工艺条件如表3所示。
[0122]
对比例3
[0123]
以工业zsm
‑
5为载体,采用等体积浸渍法负载ni、w活性金属后得到niw/zsm
‑
5。以ff
‑
66为加氢精制剂,niw/zsm
‑
5为加氢裂化催化剂,采用全循环1的操作方式,原料油为伊朗vgo,其他工艺条件如表3所示。
[0124]
对比例4
[0125]
以工业usy为载体,采用等体积浸渍法负载ni、w活性金属后得到niw/usy。以ff
‑
66为加氢精制剂,niw/usy为加氢裂化催化剂,采用全循环1的操作方式,原料油为伊朗vgo,其他工艺条件如表3所示。
[0126]
表6实施例的活性评价结果
[0127]
项目实施例1实施例2实施例3实施例4干气,%2.82.03.023
液化气,%16.315.117.515.5
[0128]
表7对比例的活性评价结果
[0129]
项目对比例1对比例2对比例3对比例4干气,%2.42.71.41.8液化气,%8.07.86.87.8
[0130]
通过对比例与实施例的实验结果可以看出,本专利的多产液化气的加氢裂化方法可以最大限度地提高液化气与干气收率。对比实施例1与对比例1可以看出,在zsm
‑
5分子筛中掺入cu金属可以明显提高干气与液化气的收率,这是由于其可以提高催化剂对反应物的吸附性能引起的。对比实施例与对比例可以看出,采用复合分子筛体系,可以使烃类分子分步与不同分子筛接触,分级反应转化为小分子,从而最大限度地提高干气与液化气收率。实施例3中,当催化剂中活性金属含量分别为nio 7.5wt%、wo330 wt%时,干气与液化气收率最高,分别为3.0%与17.5%。
[0131]
以上所述,仅为本发明进一步的实施例,但本发明的保护范围并不局限于此,任何熟悉本技术领域的技术人员在本发明所公开的范围内,根据本发明的技术方案及其构思加以等同替换或改变,都属于本发明的保护范围。