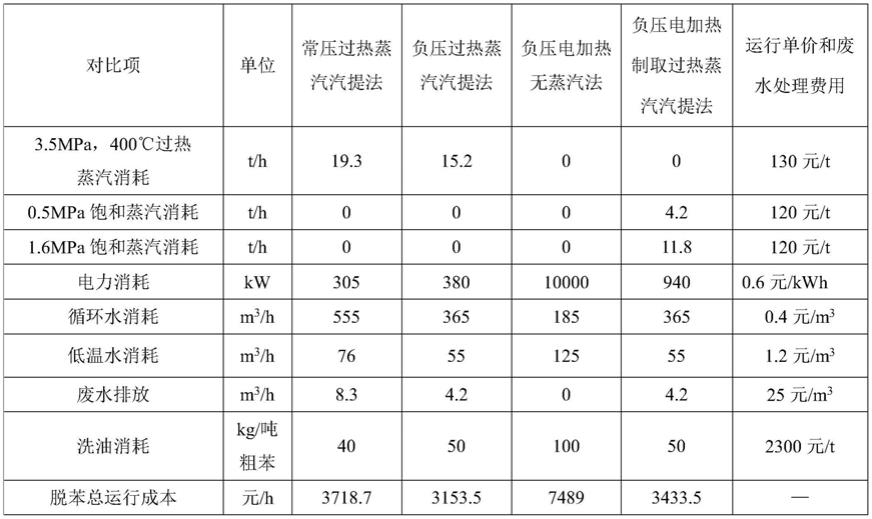
1.本实用新型涉及焦化产品回收技术领域,尤其涉及一种电加热制取过热蒸汽的负压脱苯系统。
背景技术:
2.焦炉煤气中的苯系物属于高价值副产物,通常采用焦化洗油吸收焦炉煤气中的苯系物后形成富油,富油再经脱苯工序后得到粗苯或轻苯等高价值副产物。
3.目前,焦化行业的脱苯工艺一般包括常压过热蒸汽汽提法脱苯工艺、负压过热蒸汽汽提法脱苯工艺以及管式炉加热洗油无蒸汽法脱苯工艺,其中:
4.常压过热蒸汽汽提法脱苯工艺的技术成熟、操作稳定,但此工艺消耗蒸汽量较大,每得到1吨粗苯约消耗1.5吨的400℃过热蒸汽。
5.负压过热蒸汽汽提法脱苯是近年来在焦化行业逐渐推广的工艺。其利用真空设备将粗苯冷凝冷却器后未被冷凝的不凝气抽取,使得脱苯系统呈负压状态。相对于常压过热蒸汽汽提法脱苯工艺,此工艺增加了真空设备等少量投资,但能够大幅降低过热蒸汽的消耗,每得到1吨粗苯约消耗0.75吨的过热蒸汽。目前,国内外的新建焦化厂大多采用负压过热蒸汽汽提法脱苯工艺。
6.上述两种脱苯工艺均需要采用过热蒸汽进行脱苯。目前,过热蒸汽的产生方法有:(1)管式炉加热低压饱和蒸汽产生低压过热蒸汽;(2)干熄焦高压过热蒸汽进行减温减压产生中压过热蒸汽。其中,管式炉加热低压饱和蒸汽产生低压过热蒸汽的方法简单易行,目前大多数焦化企业仍采用此法生产过热蒸汽。但管式炉一般消耗焦化自产煤气,产生的烟气中so2极易达不到焦化环保标准要求。另外,管式炉的热效率较低,燃料消耗较大,操作费用较高。且因工业安全需求,管式炉与其他设备有间距要求,因此占地面积较大,目前新建粗苯蒸馏单元一般较少采用此方法。干熄焦产高压过热蒸汽进行减温减压产生中压过热蒸汽方法是替代管式炉法的一种方法,但此法需要厂区内有干熄焦装置,且需要增添减温减压等设备。一般新建厂均配有干熄焦装置,此法尚可实施,但对于老厂区的脱苯工艺改造,因老厂区条件有限,此法较难适用。
7.管式炉加热洗油无蒸汽法脱苯工艺与上述两种脱苯工艺不同,其利用洗油被管式炉加热闪蒸后形成洗油蒸汽来汽提粗苯。相对于上述两种脱苯工艺,此工艺系统需要的真空度更高,增加了真空泵、塔底循环贫油加热用管式炉、贫油循环泵等设备投资;且相对于蒸汽汽提法脱苯工艺中脱苯塔塔底贫油温度为175℃~180℃,无蒸汽法脱苯工艺脱苯塔底贫油温度一般控制在220~240℃,塔底贫油温度较高,增加了洗油变质的程度,必然会加大洗油消耗量。但此工艺没有外来蒸汽进入脱苯系统,不会增加废水的产生,综合来看,此脱苯方法与上述两种过热蒸汽汽提法脱苯相比较,操作成本较高,目前国内外此方法应用较少。
8.授权公告号为cn 103555377b的中国实用新型专利公开了“一种减压脱苯方法”,采用无蒸汽法脱苯工艺,脱苯塔底热源与再生洗油用热源均采用电加热方式进行供热,替
代了管式炉的加热方式,减少了燃烧尾气污染物的排放。但此种脱苯方法运行能耗相对于现有的负压过热蒸汽汽提脱苯工艺仍然较高,且此种工艺虽然避免了管式炉加热管壁温高导致的洗油变质程度大,洗油消耗量高的特性,但其操作温度相对于负压过热蒸汽汽提脱苯工艺较高,洗油消耗量相对于压蒸过热蒸汽汽提脱苯工艺仍然较高,整体运行成本较大。
技术实现要素:
9.本实用新型提供了一种电加热制取过热蒸汽的负压脱苯系统,具有固定投资少、能耗较低、流程简单、环保性好的优点。
10.为了达到上述目的,本实用新型采用以下技术方案实现:
11.一种电加热制取过热蒸汽的负压脱苯系统,包括脱苯塔、再生器、粗苯冷凝冷却器、气液分离器、真空装置、油水分离装置、粗苯回流泵、热贫油泵、电加热器、贫富油换热器、富油加热器、一段贫油冷却器及二段贫油冷却器;所述脱苯塔的上部设富油入口通过富油管道连接终冷洗苯单元的富油出口,富油管道上沿富油流动方向依次设有贫富油换热器及富油加热器;所述脱苯塔的底部设热贫油出口,通过热贫油管道连接贫富油换热器的贫油入口,热贫油管道上设热贫油泵;贫富油换热器的贫油出口依次连接一段贫油冷却器、二段贫油冷却器;脱苯塔的塔顶设粗苯出口通过粗苯管道依次连接粗苯冷凝冷却器及气液分离器;气液分离器的气相出口通过真空装置连接终冷洗苯单元上游的煤气管道;气液分离器的液相出口与油水分离装置中的油水混合液入口相连;油水分离装置的油相出口通过粗苯回流泵连接脱苯塔上部的回流粗苯入口;所述再生器的顶部设蒸汽出口与脱苯塔下部的蒸汽入口相连;饱和蒸汽管道通过电加热器连接再生器下部的过热蒸汽入口及脱苯塔下部的蒸汽入口,中压饱和蒸汽管道与富油加热器的蒸汽入口相连。
12.所述脱苯塔为填料式、板式或填料与板式组合的脱苯塔。
13.所述再生器具有板式塔盘结构。
14.与现有技术相比,本实用新型的有益效果是:
15.1)采用电加热器将蒸汽加热为过热蒸汽作为贫油再生和脱苯操作的汽源,与采用管式加热炉加热蒸汽的方式相比,避免了燃烧尾气导致的环保问题,也进一步减少了占地和设备投资;
16.2)采用电加热器将蒸汽加热为过热蒸汽作为贫油再生和脱苯操作的汽源,可解决厂区无过热蒸汽汽源,而且不能采用管式炉的脱苯用汽问题;
17.3)与现有的过热蒸汽汽提脱苯工艺相比,本实用新型所述工艺可摆脱脱苯对厂区过热蒸汽汽源的依赖;且采用电加热器制取过热蒸汽的方式,对蒸汽汽源的要求较低,普遍适用于各类焦化厂。
附图说明
18.图1是本实用新型所述一种电加热制取过热蒸汽的负压脱苯系统的结构示意图。
19.图中:1.脱苯塔 2.再生器 3.粗苯冷凝冷却器 4.气液分离器 5.真空装置6.油水分离装置 7.粗苯回流泵 8.热贫油泵 9.电加热器 10.贫富油换热器 11.富油加热器 12.一段贫油冷却器 13.二段贫油冷却器
具体实施方式
20.下面结合附图对本实用新型的具体实施方式作进一步说明:
21.如图1所示,本实用新型所述一种电加热制取过热蒸汽的负压脱苯系统,包括脱苯塔1、再生器2、粗苯冷凝冷却器3、气液分离器4、真空装置5、油水分离装置6、粗苯回流泵7、热贫油泵8、电加热器9、贫富油换热器10、富油加热器11、一段贫油冷却器12及二段贫油冷却器13;所述脱苯塔1的上部设富油入口通过富油管道连接终冷洗苯单元的富油出口,富油管道上沿富油流动方向依次设有贫富油换热器10及富油加热器11;所述脱苯塔1的底部设热贫油出口,通过热贫油管道连接贫富油换热器10的贫油入口,热贫油管道上设热贫油泵8;贫富油换热器10的贫油出口依次连接一段贫油冷却器12、二段贫油冷却器13;脱苯塔1的塔顶设粗苯出口通过粗苯管道依次连接粗苯冷凝冷却器3及气液分离器4;气液分离器4的气相出口通过真空装置5连接终冷洗苯单元上游的煤气管道;气液分离器4的液相出口与油水分离装置6中的油水混合液入口相连;油水分离装置6的油相出口通过粗苯回流泵7连接脱苯塔1上部的回流粗苯入口;所述再生器2的顶部设蒸汽出口与脱苯塔1下部的蒸汽入口相连;饱和蒸汽管道通过电加热器9连接再生器2下部的过热蒸汽入口及脱苯塔1下部的蒸汽入口,中压饱和蒸汽管道与富油加热器11的蒸汽入口相连。
22.所述脱苯塔1为填料式、板式或填料与板式组合的脱苯塔。
23.所述再生器2具有板式塔盘结构。
24.本实用新型所述一种电加热制取过热蒸汽的负压脱苯系统的工艺过程如下:
25.1)终冷洗苯单元送来的富油,经贫富油换热器10与脱苯塔1底抽出的热贫油换热至175℃~185℃后,进入富油加热器11升温,升温后进入脱苯塔1内进行脱苯操作;
26.2)脱苯塔1顶部操作真空度为
‑
40kpa~
‑
80kpa,从塔顶出来的粗苯蒸汽和水蒸汽进入粗苯冷凝冷却器3进行冷凝冷却,冷凝冷却后的气液混合物进入气液分离器4进行气液两相分离;
27.3)经气液分离器4分离后的液相部分进入油水分离装置6进行油水两相分离操作,两相分离后的粗苯油相一部分被粗苯回流泵7送至脱苯塔顶作为塔顶回流,另一部分直接送至油库储存;分离后的水相部分送至终冷洗苯单元或焦油氨水分离单元;
28.4)经气液分离器4分离后的不凝气相部分通过真空装置5抽吸产生负压,使脱苯系统维持负压状态;被抽吸后的不凝气相经真空装置5后排入洗苯前的煤气管道;
29.5)压力为1.2mpa~4.0mpa的中压饱和蒸汽或过热蒸汽进入富油加热器11,作为富油升温的热源;压力为0.2mpa~2.0mpa的饱和蒸汽进入电加热器9,通过电加热升温为300~420℃的过热蒸汽后进入再生器2,作为贫油再生时的上升汽提蒸汽;
30.6)再生器2顶部的操作真空度为
‑
30kpa~
‑
70kpa,从再生器2顶部出来的洗油蒸汽与水蒸汽进入脱苯塔1底部,作为脱苯操作时的上升汽提蒸汽;
31.7)脱苯塔底的热贫油温度为170℃~190℃,由热贫油泵8送至贫富油换热器10与终冷洗苯单元送来的富油换热后,进入一段贫油冷却器12和二段贫油冷却器13进行冷却,冷却后送至终冷洗苯单元中的洗苯塔进行洗苯操作。
32.以下实施例在以本实用新型技术方案为前提下进行实施,给出了详细的实施方式和具体的操作过程,但本实用新型的保护范围不限于下述的实施例。下述实施例中所用方法如无特别说明均为常规方法。
33.【实施例】
34.本实施例中,以焦化生产能力为250万吨/年焦炭,洗油循环量为300m3/h,粗苯产量5.5t/h为例,采用四种不同脱苯工艺的能耗对比详见表1。
35.表1
[0036][0037]
由上表可知,四种脱苯工艺运行成本依次为:负压电加热无蒸汽法脱苯工艺>常压过热蒸汽汽提法脱苯工艺>负压电加热制取过热蒸汽汽提法>负压过热蒸汽汽提法脱苯工艺。
[0038]
因此,本实用新型特别适用于厂区无过热蒸汽汽源,而且不能采用管式炉的焦化企业。
[0039]
以上所述,仅为本实用新型较佳的具体实施方式,但本实用新型的保护范围并不局限于此,任何熟悉本技术领域的技术人员在本实用新型揭露的技术范围内,根据本实用新型的技术方案及其实用新型构思加以等同替换或改变,都应涵盖在本实用新型的保护范围之内。