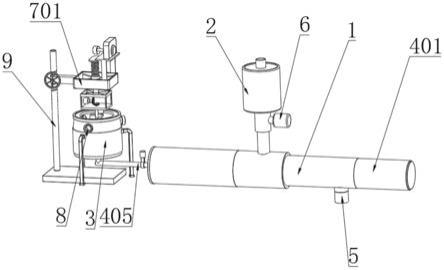
:
1.本实用新型涉及重质燃料油生产设备技术领域,具体为重质燃料油裂化分离装置。
背景技术:
2.重质燃料油是指以原油经常压蒸馏所得的渣油,经减黏或适当调入其他馏分油而制得的一种褐色黏稠状可燃性液体。常用做锅炉燃料、船用燃料,一般来说,在原油的加工过程中,较轻的组分总是最先被分离出来,燃料油作为成品油的一种,是石油加工过程中在汽油、煤油、柴油之后从原油中分离出来的较重的剩余产物。燃料油广泛用于船舶柴油机燃料、加热炉燃料、冶金炉和其他工业炉燃料。燃料油主要是由石油的裂化残渣油和直馏残渣油制成的,其特点是黏度大,含非烃化合物、胶质、沥青质多,其中裂化分离装置是重质燃料油生产的重要设备之一。
3.但是现有的重质燃料油裂化分离装置在使用时,存在催化剂液与重质燃烧油混合原料的裂化分离不彻底,导致重质燃烧油混合原料裂化分离效率较差的问题。
技术实现要素:
4.本实用新型的目的在于提供重质燃料油裂化分离装置,以解决现有的重质燃料油裂化分离装置在使用时,存在催化剂液与重质燃烧油混合原料的裂化分离不彻底,导致重质燃烧油混合原料裂化分离效率较差的问题。
5.本实用新型由如下技术方案实施:重质燃料油裂化分离装置,包括裂化反应罐、催化剂罐以及原料混合罐,所述催化剂罐贯通嵌入在所述裂化反应罐外壁顶部中间位置,所述原料混合罐安装在所述裂化反应罐外部一侧,所述裂化反应罐内部靠近所述催化剂罐底部嵌入安装有促裂化机构,所述促裂化机构用于对重质燃烧油与催化剂液进行充分接触裂化分离;
6.所述促裂化机构包括液压泵、活塞压柱、锥形管、滤盘以及注液管,所述液压泵嵌入安装在所述裂化反应罐内部一侧端部,所述活塞压柱卡接安装在所述液压泵外部一侧,所述锥形管固定套设在所述催化剂罐底部,所述滤盘固定卡接在所述裂化反应罐内壁中部,所述注液管嵌入安装在所述原料混合罐底部与所述裂化反应罐外壁一侧之间。
7.作为优选,所述催化剂罐外部底端一侧套设安装有增压泵,所述裂化反应罐外壁底端一侧嵌入安装有排料管,所述锥形管外部一侧端部与所述注液管一侧端部处于同一高度。
8.作为优选,所述原料混合罐顶部嵌入安装有混合机构,所述混合机构用于对所述原料混合罐内部的燃料油原料进行混合搅拌,所述混合机构包括固定支架、升降柱、搅拌框架、驱动电机、搅拌架以及旋转凸轮,所述固定支架固定卡接在所述原料混合罐顶部,所述升降柱活动贯穿在所述固定支架内部,所述搅拌框架固定卡接在所述升降柱底部,所述驱动电机卡接在所述搅拌框架内部一侧,所述搅拌架嵌入安装在所述搅拌框架底部中部,所
述旋转凸轮转动安装在所述升降柱顶部。
9.作为优选,所述原料混合罐外壁顶端均匀嵌入安装有进料端口,所述驱动电机顶部输出轴与所述搅拌架顶部之间通过齿牙啮合连接。
10.作为优选,所述原料混合罐外部一侧安装有支撑立柱,所述固定支架端部与所述支撑立柱之间通过活动卡环连接。
11.作为优选,所述升降柱外部与所述固定支架内壁顶部之间套设安装有支撑弹簧。
12.作为优选,所述裂化反应罐为不锈钢材质制成,且所述裂化反应罐内外壁表面均电镀有防锈漆。
13.本实用新型的优点:
14.1、本实用新型设置有促裂化机构,重质燃烧油混合原料经注液管排送至裂化反应罐内部,并经锥形管将催化剂罐内部的催化剂液排出,经催化剂液与重质燃烧油混合原料对流冲击,并配合液压泵周期驱使活塞压柱对反应液回流混合,使得重质燃烧油混合原料裂化分离更加充分彻底,有效提高了重质燃烧油混合原料裂化分离的效率。
15.2、本实用新型设置有由混合机构,经多个进料端口依次将重质燃烧油原料推送支裂化反应罐内部,并经搅拌框架内部驱动电机带动搅拌架对裂化反应罐内部搅拌,配合旋转凸轮持续推动升降柱在固定支架上下活动,实现对裂化反应罐内部不同高度的搅拌,保证了重质燃烧油原料混合的均匀性和彻底性。
附图说明:
16.为了更清楚地说明本实用新型实施例或现有技术中的技术方案,下面将对实施例或现有技术描述中所需要使用的附图作简单地介绍,显而易见地,下面描述中的附图仅仅是本实用新型的一些实施例,对于本领域普通技术人员来讲,在不付出创造性劳动的前提下,还可以根据这些附图获得其他的附图。
17.图1为本实用新型装置整体的结构示意图;
18.图2为本实用新型图1中催化剂罐内部的结构示意图;
19.图3为本实用新型图2中锥形管安装的结构示意图;
20.图4为本实用新型图1结中混合机构的结构示意图。
21.图中:1、裂化反应罐;2、催化剂罐;3、原料混合罐;4、促裂化机构;401、液压泵;402、活塞压柱;403、锥形管;404、滤盘;405、注液管;5、排料管;6、增压泵;7、混合机构;701、固定支架;702、升降柱;703、搅拌框架;704、驱动电机;705、搅拌架;706、旋转凸轮;8、进料端口;9、支撑立柱;10、活动卡环。
具体实施方式:
22.下面将结合本实用新型实施例中的附图,对本实用新型实施例中的技术方案进行清楚、完整地描述,显然,所描述的实施例仅仅是本实用新型一部分实施例,而不是全部的实施例。基于本实用新型中的实施例,本领域普通技术人员在没有作出创造性劳动前提下所获得的所有其他实施例,都属于本实用新型保护的范围。
23.参看图1
‑
4:重重质燃料油裂化分离装置,包括裂化反应罐1、催化剂罐2以及原料混合罐3,催化剂罐2贯通嵌入在裂化反应罐1外壁顶部中间位置,原料混合罐3安装在裂化
反应罐1外部一侧,裂化反应罐1内部靠近催化剂罐2底部嵌入安装有促裂化机构4;促裂化机构4包括液压泵401、活塞压柱402、锥形管403、滤盘404以及注液管405,液压泵401嵌入安装在裂化反应罐1内部一侧端部,活塞压柱402卡接安装在液压泵401外部一侧,锥形管403固定套设在催化剂罐2底部,滤盘404固定卡接在裂化反应罐1内壁中部,注液管405嵌入安装在原料混合罐3底部与裂化反应罐1外壁一侧之间,催化剂罐2外部底端一侧套设安装有增压泵6,裂化反应罐1外壁底端一侧嵌入安装有排料管5,锥形管403外部一侧端部与注液管405一侧端部处于同一高度,重质燃烧油混合原料经注液管405排送至裂化反应罐1内部,并经锥形管403将催化剂罐2内部的催化剂液排出,经催化剂液与重质燃烧油混合原料对流冲击,并配合液压泵401周期驱使活塞压柱402对反应液回流混合,使得重质燃烧油混合原料裂化分离更加充分彻底,有效提高了重质燃烧油混合原料裂化分离的效率,并经滤盘404对裂化液过滤后经排料管5进行排出,经增压泵6提高了催化剂罐2内部催化剂液的流量。
24.原料混合罐3顶部嵌入安装有混合机构7,混合机构7包括固定支架701、升降柱702、搅拌框架703、驱动电机704、搅拌架705以及旋转凸轮706,固定支架701固定卡接在原料混合罐3顶部,升降柱702活动贯穿在固定支架701内部,搅拌框架703固定卡接在升降柱702底部,驱动电机704卡接在搅拌框架703内部一侧,搅拌架705嵌入安装在搅拌框架703底部中部,旋转凸轮706转动安装在升降柱702顶部,原料混合罐3外壁顶端均匀嵌入安装有进料端口8,驱动电机704顶部输出轴与搅拌架705顶部之间通过齿牙啮合连接,升降柱702外部与固定支架701内壁顶部之间套设安装有支撑弹簧,经多个进料端口8依次将重质燃烧油原料推送支裂化反应罐1内部,并经搅拌框架703内部驱动电机704带动搅拌架705对裂化反应罐1内部搅拌,配合旋转凸轮706持续推动升降柱702在固定支架701上下活动,实现对裂化反应罐1内部不同高度的搅拌,保证了重质燃烧油原料混合的均匀性和彻底性。
25.为了可以根据实际使用需求,对固定支架701在支撑立柱9处安装高度进行适配改变,原料混合罐3外部一侧安装有支撑立柱9,固定支架701端部与支撑立柱9之间通过活动卡环10连接,为了改善裂化反应罐1内外壁的防腐蚀性能,裂化反应罐1为不锈钢材质制成,且裂化反应罐1内外壁表面均电镀有防锈漆。
26.本实用新型在使用时,经多个进料端口8依次将重质燃烧油原料推送支裂化反应罐1内部,并经搅拌框架703内部驱动电机704带动搅拌架705对裂化反应罐1内部搅拌,配合旋转凸轮706持续推动升降柱702在固定支架701上下活动,实现对裂化反应罐1内部不同高度的搅拌,然后重质燃烧油混合原料经注液管405排送至裂化反应罐1内部,并经锥形管403将催化剂罐2内部的催化剂液排出,经催化剂液与重质燃烧油混合原料对流冲击,并配合液压泵401周期驱使活塞压柱402对反应液回流混合,使得重质燃烧油混合原料裂化分离更加充分彻底,有效提高了重质燃烧油混合原料裂化分离的效率,并经滤盘404对裂化液过滤后经排料管5进行排出。
27.以上所述仅为本实用新型的较佳实施例而已,并不用以限制本实用新型,凡在本实用新型的精神和原则之内,所作的任何修改、等同替换、改进等,均应包含在本实用新型的保护范围之内。