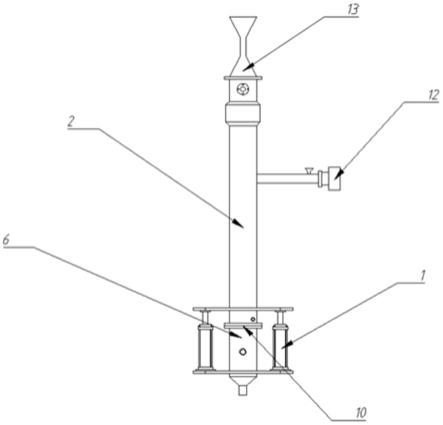
1.本实用新型涉及废旧轮胎裂解技术领域,具体涉及单室流化床裂解废旧轮胎实验装置。
背景技术:
2.轮胎的普遍应用使得废旧轮胎的数量急速上升,而对废旧轮胎的回收处理综合利用却十分困难。废轮胎作为数量巨大以及利用价值极高的“城市矿产”,愈发引起社会的关注。废旧轮胎具有很强的抗降解特性,很难通过自然降解处理,如果处理不当,还会形成一种新的“黑色污染”。因此,如何实现废旧轮胎绿色、高效回收利用己成为世界关注方向。
3.废旧轮胎的热裂解循环利用,不仅可以解决废旧轮胎造成的“黑色污染”,而且可以得到油品等产品获得可观的经济收入。目前主流的废旧轮胎热裂解工艺流程:先将废旧轮胎破碎成块状,然后连续地输送到密闭高温反应釜进行热裂解。
4.高炉渣是钢铁生产过程的主要副产品,根据生产工艺的不同和受原料辅料的影响,每产出1t生铁会副产0.3~0.6 t高炉渣,高炉排渣温度高,余热资源极其丰富,每吨高炉渣含有显热约为50 kg标准煤。目前对于高炉渣余热回收还没有较好的方法。高炉熔渣主要成分是ca0, si02, al
203
, fe
203
, mg0, mn0, ti02等。随着冷却方式的不同高炉渣会呈现出不同的固相结构:缓慢冷却时形成晶体相,快速冷却时形成非晶相(或称玻璃相)。经估算,后者释放的热量比前者约少17%;但是玻璃相高炉渣具有较高的水合活性,可作为水泥原料。现行的处理方法是采用水淬工艺实现高炉渣的物料利用,即是用大量的冷水对高温熔渣进行急冷使熔渣破碎成颗粒并形成水淬后的高炉渣可用作硅酸盐水泥的部分替代品,生产普通硅酸盐水泥。然而此法有许多缺点,不仅高炉渣的显热无法回收利用,而且造成水资源的大量浪费,对大气、水和土壤也会产生严重的污染,恶化环境。
5.目前还未见有将高炉渣余热回收与废旧轮胎裂解相结合的相关研究报道。
技术实现要素:
6.本实用新型的目的是为了弥补现有技术中的缺陷,提供一种单室流化床裂解废旧轮胎实验装置,利用该装置开展以高炉渣为热载体的轮胎裂解实验研究,考察反应温度、高炉渣和胶粉的当量比,胶粉粒径对气、液、固裂解产物产率的影响规律,明确提高裂解效率和油、气产率的最佳参数。
7.为了实现上述目的,本实用新型采用的技术方案是:一种单室流化床裂解废旧轮胎实验装置,包括反应炉,所述反应炉的炉体顶部设有料斗,炉体中部设有进料器;下部连接进气管。
8.作为本实用新型的一种优选方式,所述反应炉的炉体分为上气室和下气室,所述上、下气室可分离或合并。
9.进一步优选地,所述上气室和下气室之间设有布风板。
10.进一步优选地,上气室的上端设有减速段,所述加速段的内径大于所述上气室的
内径。
11.进一步优选地,所述上气室设有若干热电偶接口。
12.进一步优选地,所述的上气室设有辅助进气口。
13.进一步优选地,所述下气室的底部设有出渣口。
14.与现有技术相比,本实用新型的有益效果为:
15.1. 本实用新型利用的热源是高炉渣,而高炉渣是钢铁生产过程的主要副产品,每吨高炉渣含有显热约为50 kg标准煤,本实用新型的裂解质是废旧轮胎胶粒,通过合理利用工业副产品与废弃物,产生新的经济价值。
16.2.通过在该实验装置上开展以高炉渣为热载体的轮胎裂解实验研究,考察反应温度、高炉渣和胶粉的当量比,胶粉粒径对气、液、固裂解产物产率的影响规律,明确提高裂解效率和油、气产率的最佳参数,为实际工业生产提供理论支持。
附图说明
17.图1为本实用新型实施例提供的单室流化床裂解废旧轮胎实验装置结构示意图;
18.图2为本实用新型装置的左视图;
19.图 3为本实用新型装置的俯视图;
20.图4为本实用新型装置的上、下气室分离结构示意图;
21.图5为本实用新型装置的上、下气室分离左视图;
22.图6为本实用新型装置的液压杆结构示意图;
23.图7为本实用新型装置的螺旋进料器结构示意图;
24.图8为本实用新型装置的布风板结构示意图;
25.1、液压杆,2、反应炉上气室,3、进气管,4、出渣口,5、排气管,6、反应炉下气室,7、反应炉减速段,8、定位孔,9、辅助进气口,10、布风板,11、热电偶接口,12、螺旋进料器,13、上端料斗。
具体实施方式
26.为了便于理解本实用新型,下面结合附图和具体实施例,对本实用新型进行更详细的说明。附图中给出了本实用新型的较佳的实施例。但是,本实用新型可以以许多不同的形式来实现,并不限于本说明书所描述的实施例。相反地,提供这些实施例的目的是使对本实用新型公开内容的理解更加透彻全面。
27.本实用新型提供的单室流化床裂解废旧轮胎实验装置,结构如图1所示,主要包括:反应炉上气室2、反应炉下气室6。反应炉上气室2和反应炉下气室6通过液压杆1可以分离或合并。在反应炉上气室2的上端,设有反应炉减速段7,该反应炉减速段7的内径比反应炉上气室2的内径大。在反应炉上气室2的顶部,设有上端料斗13,用来向炉体内送入高炉渣料。
28.如图1、图2和图7所示,在反应炉上气室2上连接有螺旋进料器12,用来向炉体被输送废旧轮胎颗粒。反应炉上气室2的侧壁上等间隔开始有若干热电偶接口11,用来连接热电偶,测量炉体内不反应段的温度。反应炉上气室2设有辅助进风口9,辅助进风口9从反应炉侧边进风,防止反应炉死床。反应炉上气室2的上端设有出风口,出风口连接排气管5,将载
体气体与裂解气共同排出反应炉。
29.如图3所示,反应炉下气室6上设有进风口,进风口与进气管3连接,风机提供风从进风口进入反应炉内。反应炉下气室6还设有出渣口4,裂解反应时有废渣会通过布风板孔洞掉落,这些废渣就会通过出渣口排出。
30.如图1、图4、图5和图6所示,液压杆1底座焊接在反应炉下气室6上,液压杆1与底座通过螺栓连接。液压杆上板焊接在反应炉上气室2上,液压杆1与上板通过螺栓连接。如图1和图8所示,在反应炉上气室2和反应炉下气室6之间设有布风板10,该布风板10通过定位孔8可拆卸地安装在反应炉上气室2和反应炉下气室6之间,布风板10上有密集的孔洞,使进入反应炉上气室2的气体更加均匀。
31.本实用新型提供的单室流化床裂解废旧轮胎实验装置,其工作过程为:载气通过风机从进气管3吹入到反应炉下气室6,布风板10将载气分散均匀,之后载气进入到反应炉上气室2,此时高温高炉渣颗粒通过上端料斗13进入到反应炉上气室2,废旧轮胎颗粒通过螺旋进料器12进入到反应炉上气室2,在裂解废旧轮胎颗粒过程中会产生大量的裂解气体,在反应炉上部有一段反应炉炉体直径会变大,这部分就是反应炉减速段 7,因为炉体直径变大所以流化气体速度变小,未裂解完全的轮胎颗粒经过反应炉减速段 7后重新回到反应炉内进行裂解。此时从插在热电偶接口11上的热电偶读取不同反应段的温度,载气分支从辅助进风口 9吹入,防止物料在反应炉底部堆积,反应后的载气连同裂解气从排气管5排出反应炉,之后进行下一步的气体成分检测。
32.通过调整高炉渣与废旧轮胎颗粒的进料比,调整进气的流速与流量来得出最优的裂解条件参数。
33.反应结束后,如图4通过液压杆1伸缩将反应炉上气室2与反应炉下气室6分离,拿掉布风板10,将料渣从出渣口4排出反应炉,随后液压杆1伸缩将反应炉上气室2与反应炉下气室6合并,进行下一次的反应。
34.该实验装置利用高炉渣余热裂解废旧轮胎,通过检测排出的裂解气中的气体成分与含量来判断高炉渣与废旧轮胎颗粒在什么温度,什么风速下流化裂解的效果最好,从而推测出大规模工业生产所需要的参数。