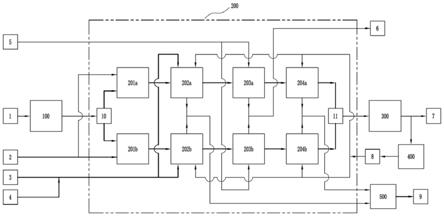
1.本发明属于能源领域,涉及一种生物质气化系统及方法。
背景技术:
2.目前,我国生物质利用的主要方式是生物质发酵制沼气或通过固定床、流化床气化生产中低热值燃气再进行燃烧发电、供热。专利cn109181772a公开了一种基于斯特林机的生物质气化发电系统,包括生物质干燥器、生物质气化炉、气化炉送风机、除尘器及斯特林机;专利cn109578961a公开了一种生物质气化耦合直燃发电系统及方法,系统包括生物质气化系统和生物质直燃发电系统,生物质气化系统包括生物质气化炉和换热器;专利cn109297048a公开了一种生物质气化暖炉,包括主体以及设置于主体内的气化燃烧系统,用于将生物质燃料进行分解裂变后气化,并对气化后的生物质燃料进行燃烧产生用以产生热量;专利cn109536207a公开了一种常压固定床生物质气化炉及生物质常压气化方法,包括集气室、冷凝室、除油室、除尘室、气化室等和气化剂室;专利cn109504459a公开了一种干式出渣的生物质气化炉,包括炉体和干式出渣炉底结构,其中,炉底结构包括炉排、用于将炉体内的炉渣排出的出渣装置、用于收集并排出出渣装置中炉渣的炉渣分隔装置;专利cn209338470u公开了一种生物质气化制合成气的生产装置,包括生物质气化装置、旋风分离器、水蒸汽发生装置、气体混合器、重整反应装置和产品收集装置;
3.但目前的生物质气化技术主要存在以下几个方面的问题:
4.1)主要以常压固定床、流化床气化为主,主要产物是作为用于供暖、发电锅炉系统的中低热燃料气,且合成气品质较差,h2/co比低,合成气中焦油含量高,极易发生管路系统结焦、堵塞;
5.2)现有气化技术气化温度较低、碳转化率较低,且由于气化炉结构设计缺陷,导致进料、排渣系统极易出现故障,导致气化炉很难实现连续化运行和规模化生产;
6.3)装置规模小,工业化放大困难,合成气品质差、有效气含量低、合成气含尘量及焦油含量高,很难与合成气制甲醇、乙醇、二甲醚、生物质柴油等液体燃料、化学品合成生产系统耦合;
7.4)气化炉对生物质原料适应性差,合成气冷却降温、除焦油、净化除尘会产生大量难处理的组成复杂的废水,环保性差。
技术实现要素:
8.针对现有技术存在的不足,基于高倍率循环流化、快速热量分散核心理念,本发明目的在于提供一种生物质气化系统及方法,基于高倍率循环流化及快速热量分散核心技术,具有生物质原料适应性强、碳转化率高、合成气有效气含量高、进料连续稳定,且可实现连续化、规模生产。
9.为了实现上述目的,本发明采用以下技术方案:
10.一种生物质气化系统,包括进料系统、反应系统和气体后处理系统;
11.所述的反应系统包括两套相同的反应设备
‑
第一反应设备和第二反应设备,第一反应设备包括依次连接的第一加料器、第一高倍率循环流化气化炉、第一合成气冷却器和第一固体颗粒控制器;第二反应设备包括依次连接的第二加料器、第二高倍率循环流化气化炉、第二合成气冷却器和第二固体颗粒控制器;
12.用于生物质脱水、挤压和造粒的进料系统分别与第一反应设备和第二反应设备的第一加料器、第二加料器连接供料,第一反应设备和第二反应设备合成气出口与气体后处理系统连通;
13.所述第一加料器和第二加料器还分别连接有输送气管路,第一高倍率循环流化气化炉和第二高倍率循环流化气化炉分别连接氧气和蒸汽混合输送管路,第一合成气冷却器和第二合成气冷却器设置有锅炉给水管道和蒸汽排出管道;
14.生物质原料经过进料系统进行干燥脱水、破碎及成型后制成当量粒径分布符合要求的进料颗粒,进料颗粒分别通过第一加料器和第二加料器被定量加入到第一高倍率循环流化气化炉、第二高倍率循环流化气化炉中进行反应,将生物质原料转化为以co、h2为主要组成的高温粗合成气,高温粗合成气依次进入第一合成气冷却器和第二合成气冷却器、第一固体颗粒控制器、第二固体颗粒控制器中分别完成显热回收及净化除尘后产生的低温净化合成气进入下游的合成气后处理系统进行变换反应及脱硫脱碳后得到满足后续合成工艺的合成气。
15.进一步,所述第一高倍率循环流化气化炉、第二高倍率循环流化气化炉和第一固体颗粒控制器、第二固体颗粒控制器的排渣口连接有渣冷却及收集系统。
16.进一步,所述气体后处理系统合成气出口通过循环气管路又分别与第一高倍率循环流化气化炉、第二高倍率循环流化气化炉和第一固体颗粒控制器、第二固体颗粒控制器连接,循环气管路上安装有循环气压缩机。
17.一种生物质气化方法,包括如下步骤:
18.第一步、作为原料的生物质经过进料系统进行脱水、挤压、造粒并破碎后形成粒径均匀的进料颗粒,同时第一高倍率循环流化气化炉和第二高倍率循环流化气化炉中预热至500~900℃;
19.第二步、进料颗粒在输送气的辅助作用下分别通过第一加料器和第二加料器被定量加入到预热后的第一高倍率循环流化气化炉和第二高倍率循环流化气化炉中,与此同时,氧气和蒸汽在定量混合后加入到第一高倍率循环流化气化炉和第二高倍率循环流化气化炉中;
20.第三步、控制第一高倍率循环流化气化炉和第二高倍率循环流化气化炉达到操作条件,在合适的进料颗粒、氧气和蒸汽的配比下,发生部分氧化反应并生成高温粗合成气;
21.第四步,高温粗合成气进入第一合成气冷却器和第二合成气冷却器与送入其中的锅炉给水换热进行降温及热量回收后形成低温粗合成气,锅炉给水变成蒸汽产品排出,低温粗合成气然后进入第一固体颗粒控制器和第二固体颗粒控制器进行固体颗粒脱除,经降温和固体颗粒脱除后的两股粗合成气合并进入气体后处理系统并形成满足后续工艺的合成气。
22.进一步,气体后处理系统排出的一部分合成气经循环气压缩机返回反应系统作为循环气送入第一高倍率循环流化气化炉、第二高倍率循环流化气化炉和第一固体颗粒控制
器、第二固体颗粒控制器;所述气化反应残余的固渣从第一高倍率循环流化气化炉、第二高倍率循环流化气化炉和第一固体颗粒控制器、第二固体颗粒控制器经过固渣冷却及收集系统排出。
23.进一步,所述第一高倍率循环流化气化炉、第二高倍率循环流化气化炉采用循环倍率为80~150倍且进料颗粒的升温速率为90000~100000℃/s的流化床气化炉,操作温度为1000~1300℃,系统反应压力3.0~4.0mpa。
24.进一步,所述出第一固体颗粒控制器和第二固体颗粒控制器的粗合成气特征为:ch4:0.5~1mol%、co2:10~15mol%、co:25~30mol%、h2:25~35mol%、h2o:20~30mol%、n2:2~5mol%、nh3:0.1~1mol%、h2s:0.1~1mol%。
25.进一步,所述生物质1为由秸秆、木屑、椰壳、玉米秆或其他富含有机质的废弃物中的一种或两种以上原料经干燥、成型预处理后所制成的当量粒径<6mm的颗粒物;送入第一高倍率循环流化气化炉和第二高倍率循环流化气化炉的蒸汽和氧气质量比为0.8~1.5,混合后温度为180~280℃。
26.进一步,所述第一合成气冷却器和第二合成气冷却器采用水管锅炉、火管锅炉或流化床锅炉三种热量回收形式之一,同时通过锅炉给水产生300~450℃的蒸汽产品。
27.进一步,所述气体后处理系统采用变换反应、cos水解、低温甲醇洗或nhd工艺对粗合成气进行有效组分调控、酸性气脱除后获得产品合成气。
28.本发明具有以下有益效果:
29.1)在加压、高温操作条件下可实现生物质的高效转化。80~150的高倍率颗粒循环、90000~100000℃/s的温升速率、980~1200℃的系统气化温度区间,可保证核心气化反应装置内的热、质传递速率及温度场的均匀分布,进而确保总碳转化率可达99.5%以上,3.0~4.0mpa的气化反应操作压力,保证了气化装置可与后续的合成气变换、低温甲醇洗、甲醇合成、费托合成等碳一合成生产系统实现稳态兼容、耦合;
30.2)合成气品质高。产品合成气中有效气(co+h2)含量>75vol%(干基),出气化炉界区合成气中灰含量<30mg/nm3,合成气中无焦油组分,h2/co>1,可为后续的碳一合成生产系统提供稳定、连续高品质的原料气;
31.3)原料适应性广。可以农作物秸秆、农产品加工残余物、林木、有机固废、生活垃圾等作为原料,对生物质的灰分含量、灰熔点、挥发分含量、固定碳含量、可磨性等无特殊要求,突破了生物质灰分中因碱金属含量高导致的灰熔点降低所引发的气化装置系统易结渣、堵塞而无法实现连续运行的技术瓶颈。
32.4)规模效应明显。基于独有的高倍率循环流化及快速热量分散核心技术,核心气化装置易于实现规模化放大,技术安全可靠,操作弹性大,比氧耗、比蒸汽消耗低于常规生物质气化技术,装置运行负荷可灵活调节,投资强度及单位合成气生产成本优势明显。
33.5)节能环保竞争性强。出界区合成气中无焦油组分,含尘量较低,无需进行复杂的焦油及灰尘脱除,干法排灰,无需急冷,合成气显热高效干法回收,无难处理的除焦油、激冷、除尘废水产生。
附图说明
34.图1为本发明的系统结构示意图
35.图中:1
‑
生物质原料;2
‑
输送气;3
‑
氧气;4
‑
蒸汽;5
‑
锅炉给水;6
‑
蒸汽产品;7
‑
合成气;8
‑
循环气;9
‑
固渣;10
‑
进料颗粒;11
‑
粗合成气;100
‑
进料系统、200
‑
反应系统和300
‑
气体后处理系统;400
‑
循环气压缩机;500
‑
固渣冷却及收集系统;201a
‑
第一加料器;201b
‑
第二加料器;202a
‑
第一高倍率循环流化气化炉;202b
‑
第二高倍率循环流化气化炉;203a
‑
第一合成气冷却器;203b
‑
第二合成气冷却器、204a
‑
第一固体颗粒控制器;204b
‑
第二固体颗粒控制器。
具体实施方式
36.以下结合实施例对本发明的具体内容做进一步详细解释说明。
37.如图1所示,生物质气化系统包括进料系统100、反应系统200和气体后处理系统300;
38.所述的反应系统200由两套相同的反应设备组成,即第一反应设备和第二反应设备,第一反应设备包括依次连接的第一加料器201a、第一高倍率循环流化气化炉202a、第一合成气冷却器203a和第一固体颗粒控制器204a;第二反应设备包括依次连接的第二加料器201b、第二高倍率循环流化气化炉202b、第二合成气冷却器203b和第二固体颗粒控制器204b。
39.所述进料系统100用于生物质脱水、挤压和造粒,进料系统100分别与第一反应设备和第二反应设备的第一加料器201a、第二加料器201b连接供料。第一反应设备和第二反应设备合成气出口与气体后处理系统300连通。
40.所述第一加料器201a和第二加料器201b还分别连接有输送气管路,第一高倍率循环流化气化炉202a和第二高倍率循环流化气化炉202b分别连接氧气3和蒸汽4混合输送管路,第一合成气冷却器203a和第二合成气冷却器203b设置有锅炉给水管道和蒸汽排出管道。
41.所述第一高倍率循环流化气化炉202a、第二高倍率循环流化气化炉202b和第一固体颗粒控制器204a、第二固体颗粒控制器204b的排渣口与渣冷却及收集系统500连接,所述气体后处理系统300合成气出口通过循环气管路又分别与第一高倍率循环流化气化炉202a、第二高倍率循环流化气化炉202b和第一固体颗粒控制器204a、第二固体颗粒控制器204b连接,循环气管路上安装有循环气压缩机400,部分合成气经循环气压缩机400返回反应系统200作为循环气8使用。
42.生物质原料1经过进料系统100进行干燥脱水、破碎及成型后制成当量粒径分布符合要求的进料颗粒10,进料颗粒10在输送气2的辅助作用下,分别通过第一加料器201a和第二加料器201b被定量加入到提前预热至500~900℃的第一高倍率循环流化气化炉202a、第二高倍率循环流化气化炉202b中,与此同时,根据生物质的组成及气化特性,由空气/富氧空气/二氧化碳/氧气3和蒸汽4按比例混合后加入提前预热至设定目标温度的第一高倍率循环流化气化炉202a、第二高倍率循环流化气化炉202b,再通过参数调控,使第一高倍率循环流化气化炉202a、第二高倍率循环流化气化炉202b达到设定的目标操作温度、压力,在适宜的生物质原料1进料量、空气/富氧空气/二氧化碳/氧气3、蒸汽4质量配下,所有进入第一高倍率循环流化气化炉202a、第二高倍率循环流化气化炉202b的物料发生热裂化反应、高温碳氧化/还原反应、催裂解反应、水煤气变换反应、甲烷化反应等,将生物质原料1转化为
以co、h2为主要组成的高温粗合成气,高温粗合成气依次进入第一合成气冷却器203a和第二合成气冷却器203b、第一固体颗粒控制器204a、第二固体颗粒控制器204b中分别完成显热回收及净化除尘后产生的低温净化合成气11继续进入下游的合成气后处理系统300,根据下游生物质液体燃料及化学品合成工段对原料气的组成要求,继续进行变换反应及脱硫脱碳等过程,输出满足后续合成工艺的合成气流股7,根据工艺要求,合成气7中一部分需经循环气压缩机400返回反应系统200。第一高倍率循环流化气化炉202a、第二高倍率循环流化气化炉202b产生的固体粗渣及第一固体颗粒控制器204a、第二固体颗粒控制器204b所捕集的合成气中的细颗粒汇合后经固渣冷却及收集系统500回收显热后排出。
43.生物质气化方法具体过程为:
44.第一步、作为生物质原料1的生物质经过进料系统100进行脱水、挤压、造粒并破碎后形成粒径均匀的进料颗粒10,同时,第一高倍率循环流化气化炉202a和第二高倍率循环流化气化炉202b中预热至500~900℃;
45.第二步、进料颗粒10在输送气2的辅助作用下,分别通过第一加料器201a和第二加料器201b被定量加入到预热至500~900℃的第一高倍率循环流化气化炉202a和第二高倍率循环流化气化炉202b中,与此同时,氧气3和蒸汽4在定量混合后加入到提前预热至一定温度的第一高倍率循环流化气化炉202a和第二高倍率循环流化气化炉202b中;
46.第三步、控制第一高倍率循环流化气化炉202a和第二高倍率循环流化气化炉202b达到操作条件,在合适的进料颗粒10、氧气3和蒸汽4的配比下,发生部分氧化反应并生成高温粗合成气;
47.第四步,高温粗合成气进入第一合成气冷却器203a和第二合成气冷却器203b与送入其中的锅炉给水5换热,进行降温及热量回收后形成低温粗合成气11,锅炉给水5变成蒸汽产品6排出,低温粗合成气11然后进入第一固体颗粒控制器204a和第二固体颗粒控制器204b进行固体颗粒脱除,经降温和固体颗粒脱除后的两股粗合成气11合并进入气体后处理系统300并形成满足后续工艺的合成气7;
48.第五步,其中一部分合成气7经循环气压缩机400返回反应系统200作为循环气8送入第一高倍率循环流化气化炉202a、第二高倍率循环流化气化炉202b和第一固体颗粒控制器204a、第二固体颗粒控制器204b,气化反应残余的固渣9从第一高倍率循环流化气化炉202a、第二高倍率循环流化气化炉202b和第一固体颗粒控制器204a、第二固体颗粒控制器204b经过固渣冷却及收集系统500排出。
49.所述的第一加料器201a、第二加料器201b采用以旋转或螺旋为转动方式的机械式加料器或气力输送式加料器的两种形式之一。
50.第一高倍率循环流化气化炉202a、第二高倍率循环流化气化炉202b采用循环倍率为80~150倍且进料颗粒10的升温速率为90000~100000℃/s的流化床气化炉,操作压力为3.0~4.0mpa,操作温度为1000~1300℃。
51.进一步,所述气体后处理系统(300)采用变换反应、cos水解、低温甲醇洗或nhd工艺对粗合成气(11)进行有效组分调控、酸性气脱除后获得产品合成气(7)。
52.第一合成气冷却器203a和第二合成气冷却器203b采用水管锅炉、火管锅炉或流化床锅炉三种热量回收形式之一,同时通过锅炉给水5产生300~450℃的蒸汽产品6。
53.第一固体颗粒控制器204a和第二固体颗粒控制器204b采用以旋流和过滤相组合
的形式实现粗合成气11固体颗粒脱除,出第一固体颗粒控制器204a和第二固体颗粒控制器204b的气体典型特征为:ch4:0.5~1mol%、co2:10~15mol%、co:25~30mol%、h2:25~35mol%、h2o:20~30mol%、n2:2~5mol%、nh3:0.1~1mol%、h2s:0.1~1mol%。气体后处理系统300采用变换反应、cos水解、低温甲醇洗或nhd工艺对粗合成气11进行有效组分调控、酸性气脱除后获得产品合成气7,其中,该合成气7的一部分需经循环气压缩机400压缩后作为循环气8返回反应系统200。
54.所述的生物质和进料颗粒10由秸秆、木屑、椰壳、玉米杆或碳基垃圾的一种或多种物质组成,可以是单纯的由玉米秸杆、稻草秸秆、小麦秸秆、棉花秸秆、豆类秸秆、油料作物秸秆、蔗渣、高粱秸秆等农作物秸秆、农产品加工废弃物、林木生物质及加工废弃物、富含有机质的有机污泥及生活垃圾等生物质中的一种,也可以根据进料h/c比、灰分含量、挥发分含量、固定碳含量、反应活性调整需要由上述生物质中的两种及以上按比例组成的复合生物质原料经干燥、成型预处理后所制成的当量粒径<6mm的颗粒物。
55.送入第一高倍率循环流化气化炉202a和第二高倍率循环流化气化炉202b的蒸汽4和氧气3质量比为0.8~1.5,混合后温度为180~280℃。所述的进料颗粒10的粒径分布为0~6mm。
56.所述的固渣冷却及收集系统500采用内部设有冷却水管的容器对固渣9进行冷却和收集,最终将固渣9以旋转或螺旋为转动方式的机械式或气力输送式的排料器排出系统。
57.所述的蒸汽4和氧气3质量比为0.8~1.5,混合后温度为180~280℃。
58.所述的循环气8压力高于第一高倍率循环流化气化炉202a和第二高倍率循环流化气化炉202b操作压力2~5mpa,用于第一高倍率循环流化气化炉202a、第二高倍率循环流化气化炉202b和第一合成气冷却器203a和第二合成气冷却器203b的吹扫气,以及第一固体颗粒控制器204a和第二固体颗粒控制器204b的反吹气。
59.生物质气化制合成气反应原理或者反应过程:
60.焦油蒸汽及二氧化碳重整、催化热裂解反应:
61.c
n
h
m
+nh2o
→
n co+(n+m/2)h262.c
n
h
m
+2nh2o
→
n co2+(2n+m/2)h263.c
n
h
m
→
n co+m/2h264.c
n
h
m
+n co2→
2n co+m/2h265.氧化反应:
66.c+o2→
co267.c+o2→
2co
68.水蒸汽还原反应:
69.c+h2o
→
co+h270.c+2h2o
→
co2+2h271.二氧化碳还原反应:
72.co2+c
→
2co
73.一氧化碳变换反应:
74.co+h2o
→
co+h2。