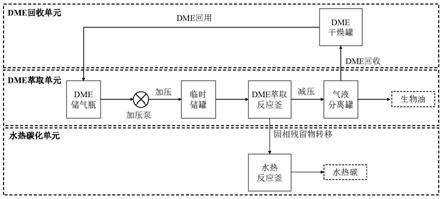
1.本发明属于环境工程固废资源化技术领域与生物质能源技术领域,特别涉及污泥低氮含量生物油及水热碳同步制备的工艺。
背景技术:
2.随着我国城市污水的产生量不断提高,污泥年产量逐年增大。污泥具有较高的含水率,且存在重金属、有机物等污染物。因此,使用焚烧,填埋等常规方法对污泥进行处置,存在含水率不满足要求、能耗大、污染风险高等问题。
3.目前,常用的市政污泥处置技术主要包括卫生填埋、干化焚烧、土地利用及建材制备(制砖,制陶粒等)四类。卫生填埋存在水分渗漏污染地下水,造成水源污染问题;干化焚烧普遍存在产生二次污染、需外加燃料的问题;土地利用对污泥中重金属含量要求高,持久性有机物会给土壤带来的二次污染;而以制砖、制肥及制陶粒等技术为代表的其他形式的处置技术,虽然存在一定的应用案例,但始终难以进行大规模推广。综上所述,我国目前主要的污泥处理、处置技术仍然存在多方面的不足。
4.污泥含有的大量有机物使其具有作为生物质能源利用的潜力。如将污泥中有机质转化为生物油、生物碳等能源中间体。现有的从污泥中获得生物油的方式,如水热液化法,在加工市政污泥产生生物油的同时产生大量工艺废水,该工艺废水组成为市政污泥中的水、反应产水及反应产生的水溶性物质混合物,市政污泥水热液化过程中,超过20%的碳、50%的氮及大量营养物质均进入了该工艺废水,废水中的cod、氨氮等含量极高,油品低,燃烧会产生较多的氮氧化物。
5.与水热气化和水热液化相比,水热碳化所需要的温度化和压力都较低,反应条件相对温和,在处理固体废物方面耗能相对较少,可基于其简单的处理设备、方便的操作方法获得水热碳材料,应用规模可调性相对较强。从能量密度上而言,水热碳性质接近于低阶褐煤,可作为再生燃料直接燃用。此外,水热碳化可以得到尺寸均一、形貌较好的炭材料,并可通过进一步合成、改质来生产高效稳定、具有纳米尺度的炭微球材料,用于废水处理、超级电容器等领域。
6.通过有机溶剂进行有机物提取也是获取污泥等生物质中广谱化合物的方法之一。液态二甲醚(l
‑
dme)是一种极具潜力的绿色有机溶剂,其原料来源丰富,生产成本低;且能与水、有机物以一定比例互溶,不仅可以作为有机物的萃取剂,还能在与湿生物质混合后通过减压实现相分离,从而特别适合于湿生物质的处理;此外,由于污泥中含有大量氮元素(主要存在于蛋白质中),通过水热法所生成的生物油中含氮量通常较高,后续需要通过脱氮工艺进行提质。而l
‑
dme能溶解90%以上的脂类,但只能溶解6%的蛋白质,从而避免了氮元素进入生物油中,因此可将l
‑
dme作为萃取剂获得品质较高的生物油。
技术实现要素:
7.解决的技术问题:本技术主要是提出一种污泥低氮含量生物油及水热碳同步制备
的工艺,解决现有技术中存在的含水率不满足要求,且存在重金属、有机物等污染物、能耗大、污染风险高等技术问题。
8.技术方案:
9.一种污泥低氮含量生物油及水热碳同步制备的工艺,使用液态二甲醚对污泥萃取,借助液态l
‑
dme萃取污泥中90%以上的脂类和水分,得到低氮含量生物油,其氮含量小于0.5%,对萃取后的固相残留物进行水热碳化得到水热碳。
10.作为本发明的一种优选技术方案:所述污泥低氮含量生物油及水热碳同步制备的工艺,具体包括如下步骤:
11.第一步,使用有机溶剂进行污泥萃取,获得低氮含量生物油:将dme储气瓶中的dme经加压泵增压液化并保存在l
‑
dme临时储罐中备用,加压泵增压后压力为0.5~3mpa;将污泥放入dme萃取反应釜中,dme萃取反应釜带有搅拌叶片和水浴加热部分,搅拌叶片的搅拌速度为0~1500r/min(不取端点0);将l
‑
dme临时储罐中的l
‑
dme通入dme萃取反应釜中,控制l
‑
dme与污泥含水量的质量比为l
‑
dme:污泥中含水量=1:0~25(不取端点0),随后打开dme萃取反应釜的搅拌装置并反应0~120min(不取端点0),反应的温度为20~100℃;
12.第二步,有机溶剂相与残留固相进行分离:反应结束后,打开dme萃取反应釜下方阀门利用dme萃取反应釜与气液分离罐的压差(0.5mpa),通过dme萃取反应釜底部铺设的过滤滤网(180目不锈钢滤网)分离固相和液相产物;液相产物完全进入气液分离罐后,将气液分离罐进行减压,液相中的l
‑
dme气化进入后面的dme干燥罐,经干燥处理后加压进行储存供再次利用;打开气液分离罐下端的阀门收集脱除的液相产物,得到的液相产物通过蒸馏分离得到水相和低氮含量生物油;
13.第三步,萃取后固相残留物水热碳化获得水热碳;收集dme萃取反应釜中存留的固相产物,将固相残留物转移至水热反应釜中,进行水热碳化,反应温度为180~250度,反应时间为1~5小时,水热碳化结束后的产物进行过滤,
14.烘干即得到水热碳。
15.作为本发明的一种优选技术方案:所述第一步中运行参数为,控制液态二甲醚与污泥含水量的质量比为10~13倍,可在实现较好生物油提取率的同时有效降低l
‑
dme使用量;dme萃取反应釜的搅拌装置反应时间为30~40min;反应温度为20~100℃。
16.作为本发明的一种优选技术方案:所述污泥是自污水处理厂带式脱水机或离心机脱水后的污泥,其含水率为75
‑
85%。
17.作为本发明的一种优选技术方案:所述第二步中低氮含量生物油,氮含量小于0.5%。
18.作为本发明的一种优选技术方案:所述水热碳化反应过程是n2气氛条件下进行,将固相残留物与超纯水按1:9的比例加入水热反应釜中并搅拌均匀。
19.作为本发明的一种优选技术方案:所述污泥经过液化二甲醚萃取后,脂类提取率超过90%,但蛋白质的提取率小于10%,且含水率小于30%。
20.作为本发明的一种优选技术方案:所述水热碳化结束后的产物冷却至80℃以下,之后进行过滤分离,烘干得到水热碳。
21.作为本发明的一种优选技术方案:所述水热碳,h/c和o/c较低。
22.作为本发明的一种优选技术方案:所述水热碳化结束后的产物冷却温度优选为60
℃以下。
23.有益效果:本技术所述污泥低氮含量生物油及水热碳同步制备的工艺采用以上技术方案与现有技术相比,具有以下技术效果:
24.1、本发明有效的实现了污泥的无害化、资源化、减量化。所产生的低氮生物油和水热碳可作为燃料用于水热碳化反应器加热,实现能量自给,在污泥资源化方面具有广阔的应用前景。
25.2、使用液态二甲醚对污泥萃取,可以萃取污泥中90%以上的脂类和水分,而萃取较少的蛋白质。
26.3、可以得到低氮含量生物油,其氮含量小于0.5%。
27.4、对萃取后的固相残留物进行水热碳化得到水热碳,h/c和o/c值较低,因此,具有良好的燃料性能。
28.5、相比污泥的常规处理、处置方法,本工艺适用于含水率较高的湿污泥,且能同时获得生物油与水热碳两种具有附加价值的产物,实现污泥资源化利用。
29.6、通过l
‑
dme萃取的手段提高了生物油品质,后续水热碳化所需的反应条件也较为温和,本工艺相较传统水热液化方法具有多方面的优势。
附图说明
30.图1为本技术一种污泥低氮含量生物油及水热碳同步制备的工艺的工艺流程图。
31.图2为本技术实施例3中含水率、脱水率随质量比的变化图。
32.图3为本技术实施例3中含水率、脱水率随反应时间变化图。
33.图4为本技术实施例3中含水率、脱水率随反应温度的变化图。
具体实施方式
34.下面结合具体实施例对本发明作进一步说明,以使本领域的技术人员可以更好的理解本发明并能予以实施,但所举实施例不作为对本发明的限定。
35.实施例1:应用例
36.污泥低氮含量生物油及水热碳同步制备的工艺,具体包括如下步骤:
37.第一步:将dme储气瓶中的dme经加压泵增压液化并保存在l
‑
dme临时储罐中备用,加压泵增压后压力为0.5~3mpa;取50g污水厂市政脱水污泥(含水率85%)放入dme萃取反应釜中,然后通入l
‑
dme,控制l
‑
dme与污泥中含水量的质量比、反应时间、反应温度,搅拌速度分布15、20min、25℃、750r/min。
38.第二步:反应完成后,打开dme萃取反应釜下方阀门利用dme萃取反应釜与气液分离罐的压差(0.5mpa),通过dme萃取反应釜底部铺设的过滤滤网(180目不锈钢滤网)分离固相和液相产物;液相产物完全进入气液分离罐后,将气液分离罐进行减压,液相中的l
‑
dme气化进入后面的dme干燥罐,经干燥处理后加压进行储存供再次利用;打开气液分离罐下端的阀门收集脱除的液相产物,得到的液相产物通过蒸馏分离得到水相和低氮含量生物油。
39.第三步:收集dme萃取反应釜中存留的固相产物,将固相残留物转移至水热反应釜中,进行水热碳化,设置反应温度为220℃,反应时间1~5h,进行水热碳化,反应结束后待反应产物冷却至60度以下时,将产物进行过滤分离,烘干得到水热碳。
40.实施例2
41.取50g污水厂市政脱水污泥(含水率85%),测量原污泥的灰分和碳含量,之后将该污泥放入dme萃取反应釜中,按照实施例1的工艺方法得到生物油和水热碳,测量产物的性质如表1所示。
42.表1原污泥及产物性质对比
[0043][0044]
a
基于干基重量
[0045]
b
基于无灰分干基重量
[0046]
由表1可知,l
‑
dme萃取可极大程度上减少氮含量,提高生物油的品质;同时,经反应其c含量增加约1.3倍,获得的水热碳比表面积可以达到15.782m2/g,后续经过改性可以进一步提升,从而作为吸附材料使用。
[0047]
实施例3
[0048]
取50g污水厂市政脱水污泥(含水率85%)放入反应釜中,然后通入液态二甲醚,控制液态二甲醚与污泥中含水量的质量比、反应时间、反应温度,搅拌速度分布15、20min、25℃、750r/min,反应完成后用烘干法测定污泥含水率。
[0049]
由图2、3、4可知,液态二甲醚与污泥含水量的质量比为10~13倍,反应时间为30~40min,反应温度为20~100℃时,效果较佳。
[0050]
以上所述,仅是本技术的实施例,并非对本技术做任何形式的限制,虽然本技术以较佳实施例揭示如上,然而并非用以限制本技术,任何熟悉本专业的技术人员,在不脱离本技术技术方案的范围内,利用上述揭示的技术内容做出些许的变动或修饰均等同于等效实施案例,均属于技术方案范围内。