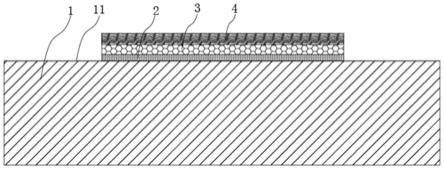
1.本发明属于雾化技术领域,特别地,涉及一种雾化芯、雾化芯、雾化器、气溶胶发生装置及雾化芯制备方法。
背景技术:
2.气溶胶发生装置使用的薄膜发热式雾化芯,通常是将发热薄膜附着在多孔陶瓷的雾化面上,通过发热薄膜对雾化面上的气溶胶形成基质进行加热,使气溶胶形成基质雾化形成烟雾。当前的薄膜发热式雾化芯,存在连续性差、厚度难以调节控制的问题,容易导致薄膜式发热层电阻阻值稳定性差,进而造成薄膜发热式雾化芯发热均匀性差。
技术实现要素:
3.基于现有技术中存在的上述问题,本发明实施例的目的之一在于提供一种通过在多孔基底的至少部分外表面上首先覆设一层过渡层,再在过渡层上覆设由镍铬合金材料加工形成的发热层,使得发热层具有良好的连续性,便于调节控制发热层厚度,降低发热层成本,增强发热层电阻稳定性的的雾化芯。
4.为实现上述目的,本发明采用的技术方案是:提供一种雾化芯,包括:
5.多孔基底,至少部分外表面形成有用于供气溶胶形成基质加热雾化的雾化面,所述多孔基底内部具有吸附、存储气溶胶形成基质的微孔结构,所述多孔基底吸附、存储的气溶胶形成基质可经由所述微孔结构传输至所述雾化面;
6.过渡层,覆设于至少部分所述雾化面上;
7.发热层,用于在通电后加热并雾化气溶胶形成基质,所述发热层结合于所述过渡层背离所述多孔基底的一面上,所述发热层为镍铬合金层;以及
8.保护层,覆设于所述发热层背离所述过渡层的一面上。
9.进一步地,所述雾化芯还包括用于电性连接所述发热层与电源装置的两个电极,所述电极通过厚膜沉积工艺形成于所述雾化面上,所述电极为金层、银层、铂层、钯层、铝层、铜层、金银合金层、银铂合金层、银钯合金层中的至少一种。
10.进一步地,所述保护层为氧化铝层、氧化硅层、氮化铝层、氮化硅层、氧化钛层、氮化钛层中的至少一种。
11.进一步地,所述保护层的厚度为0.5~3μm。
12.进一步地,所述发热层的厚度为1~5μm。
13.进一步地,所述过渡层为氮化铝层、氮化硅层、氮化铬层、碳化铬层中的至少一种。
14.进一步地,所述过渡层的厚度为0.1~1μm。
15.进一步地,所述电极成对并间隔布置于所述雾化面上的第一区域,所述过渡层覆设于所述雾化面上的第二区域,所述第二区域为所述雾化面上于所述第一区域之外的区域,以使所述第一区域与所述第二区域在所述雾化面上为连续区域,所述电极的厚度大于所述发热层厚度与所述过渡层厚度之和。
16.进一步地,两个所述电极之间形成凹槽,由所述凹槽的内底面自下往上依次层叠设置有所述过渡层、所述发热层的发热部和所述保护层,且所述电极的厚度大于所述过渡层、所述发热部和所述保护层的厚度之和。
17.进一步地,所述发热层包括形成于所述第二区域的发热部、形成于其中一个所述电极至少部分表面的第一连接部,形成于另一个所述电极至少部分表面的第二连接部,所述第一连接部、所述第二连接部分别与所述发热部连接。
18.进一步地,所述第一连接部包括形成于其中一个所述电极背离所述多孔基底的一面上的第一结合部,所述第二连接部包括形成于另一个所述电极背离所述多孔基底的一面上的第二结合部,所述第一结合部的对应侧边与所述发热部的对应侧边相连,所述第二结合部的对应侧边与所述发热部的对应侧边相连。
19.进一步地,所述电极的厚度为20~60μm。
20.基于现有技术中存在的上述问题,本发明实施例的目的之二在于提供一种具有上述任一方案提供的雾化芯的雾化器。
21.为实现上述目的,本发明采用的技术方案是:提供一种雾化器,包括上述任一方案提供的所述雾化芯。
22.基于现有技术中存在的上述问题,本发明实施例的目的之三在于提供一种具有上述任一方案提供的雾化芯或雾化器的气溶胶发生装置。
23.为实现上述目的,本发明采用的技术方案是:提供一种气溶胶发生装置,包括上述任一方案提供的所述雾化芯或所述雾化器。
24.本发明实施例中的上述一个或多个技术方案,与现有技术相比,至少具有如下有益效果之一:
25.本发明实施例中的雾化芯、雾化器及气溶胶发生装置,雾化芯通过在雾化面上覆设过渡层,再将由镍铬合金材料加工形成的发热层覆设于过渡层上,使得过渡层隔设于发热层与多孔基底之间。由于发热层使用的材料为镍铬合金,其成本远低于银、钯、金等贵金属,便可降低雾化芯的成本。并且,过渡层的设置,不仅可降低多孔基底表面的粗糙度,使得发热层具有良好的连续性,便于调节控制发热层的厚度,而且过渡层还可以阻隔多孔基底的钠、钾离子在电场作用下扩散进入发热层,增强发热层电阻阻值的稳定性。此外,过渡层能够起到调节镍铬合金发热层与多孔基底表面的应力匹配,增强镍铬合金发热层与多孔基底之间的附着力,提高发热层工作性能的稳定可靠性,延长雾化芯的使用寿命。
26.基于现有技术中存在的上述问题,本发明实施例的目的之四在于提供一种雾化芯制备方法。
27.为实现上述目的,本发明采用的技术方案是:提供一种雾化芯制备方法,包括如下步骤:
28.沉积过渡层:通过薄膜沉积工艺,在多孔基底的至少部分雾化面上沉积形成过渡层;
29.沉积发热层:通过薄膜沉积工艺,在所述过渡层背离所述多孔基底的一面上沉积形成发热层,所述发热层为镍铬合金层;
30.沉积保护层:通过薄膜沉积工艺,在所述发热层背离所述过渡层的一面上沉积形成保护层。
31.可选的,所述发热层的镍铬合金材料中,ni/(ni+cr)的质量比为0.2~0.9。
32.可选的,所述多孔基底的孔隙率为30%~80%,所述多孔基底的孔径为10~30μm。
33.本发明实施例中的上述一个或多个技术方案,与现有技术相比,至少具有如下有益效果之一:
34.本发明实施例中的雾化芯制备方法,首先将过渡层以薄膜沉积的方式形成于雾化面上,再通过薄膜沉积工艺在过渡层背离多孔陶瓷基体的一面上形成发热层,然后将保护层通过薄膜沉积工艺形成在发热层上,且发热层为由镍铬合金材料加工形成的金属层。由于发热层使用的材料为镍铬合金,其成本远低于银、钯、金等贵金属,便可降低雾化芯的成本。并且,过渡层的设置,不仅可降低多孔基底表面的粗糙度,使得发热层具有良好的连续性,便于调节控制发热层的厚度,而且过渡层还可以阻隔多孔基底的钠、钾离子在电场作用下扩散进入发热层,增强发热层电阻阻值的稳定性。同时,过渡层能够起到调节镍铬合金发热层与多孔基底表面的应力匹配,增强镍铬合金发热层与多孔基底之间的附着力,保护层有效防止镍铬合金发热层发生碳化或氧化,提高发热层工作性能的稳定可靠性,延长雾化芯的使用寿命。此外,本发明实施例中的雾化芯制备方法加工的雾化芯,发热面积更大,发热更均匀,不会出现局部温度过高现象。
附图说明
35.为了更清楚地说明本发明实施例中的技术方案,下面将对实施例或现有技术描述中所需要使用的附图作简单地介绍,显而易见地,下面描述中的附图仅仅是本发明的一些实施例,对于本领域普通技术人员来讲,在不付出创造性劳动性的前提下,还可以根据这些附图获得其他的附图。
36.图1为本发明实施例一提供的雾化芯的剖视结构示意图;
37.图2为本发明实施例一提供的雾化芯的另一剖视结构示意图;
38.图3为本发明实施例二提供的雾化芯的俯视结构示意图;
39.图4为本发明实施例二提供的雾化芯的剖视结构示意图;
40.图5为本发明实施例二提供的多孔基底的剖视结构示意图;
41.图6为本发明实施例三提供的雾化芯的剖视结构示意图;
42.图7为本发明实施例三提供的多孔基底的剖视结构示意图;
43.图8为本发明实施例四提供的雾化芯的剖视结构示意图;
44.图9为本发明实施例1至实施例15中制备的雾化芯循环测试电阻值对比图;
45.图10为本发明实施例2、实施例5、实施例8、实施例11及实施例14中制备的雾化芯循环测试电阻值对比图;
46.图11为本发明实施例1至实施例3中制备的雾化芯循环测试电阻值对比图;
47.图12为本发明实施例2及实施例4至实施例6中制备的雾化芯循环测试电阻值对比图;
48.图13为本发明实施例5及实施例7至实施例9中制备的雾化芯循环测试电阻值对比图;
49.图14为本发明实施例8及实施例10至实施例12中制备的雾化芯循环测试电阻值对比图;
50.图15为本发明实施例11及实施例13至实施例15中制备的雾化芯循环测试电阻值对比图。
51.其中,图中各附图标记:
[0052]1‑
多孔基底;11
‑
雾化面;11a
‑
第一区域;11b
‑
第二区域;11c
‑
第一表面;11d
‑
第二表面;11e
‑
第三表面;11f
‑
第一过渡面;11g
‑
第二过渡面;12
‑
凸起部;13
‑
第一凹陷部;14
‑
第二凹陷部;
[0053]2‑
过渡层;
[0054]3‑
发热层;31
‑
发热部;32
‑
第一连接部;321
‑
第一侧部;322
‑
第一结合部;33
‑
第二连接部;331
‑
第二侧部;332
‑
第二结合部;
[0055]4‑
保护层;41
‑
裸露部;5
‑
电极;6
‑
凹槽。
具体实施方式
[0056]
为了使本发明所要解决的技术问题、技术方案及有益效果更加清楚明白,以下结合附图及实施例,对本发明进行进一步详细说明。应当理解,此处所描述的具体实施例仅仅用以解释本发明,并不用于限定本发明。
[0057]
实施例一
[0058]
请一并参阅图1至2,现对本发明实施例一提供的雾化芯进行说明。本发明实施例一提供的雾化芯用于雾化器,其可在气溶胶发生装置的电源装置的电驱动下发热,将雾化器的储液腔中的气溶胶形成基质加热雾化形成烟雾,以供用户吸食而达到模拟吸烟的效果。
[0059]
请结合参阅图2,本发明实施例一提供的雾化芯包括多孔基底1和发热层3。多孔基底1的至少部分外表面形成有雾化面11。多孔基底1内部具有毛细吸附作用的微孔结构,多孔基底1可通过微孔结构吸附、存储气溶胶形成基质,且吸附、存储的气溶胶形成基质可经由微孔结构持续传输至雾化面11。至少部分雾化面11上形成有发热层3。则雾化芯在使用时,通过气溶胶发生装置的电源装置向雾化芯供电,发热层3在通电后产生热量,加热传输至雾化面11上气溶胶形成基质,以使气溶胶形成基质雾化形成可供用户吸食的烟雾。
[0060]
在其中一些实施方式中,多孔基底1还可以是多孔陶瓷、多孔金属等具备液体吸附能力的多孔材料。在其中一些具体实施例中,多孔基底1为多孔陶瓷;进一步地,在其中一些更具体实施例中,多孔基底1的孔隙率为30%~80%,多孔基底1的孔径为10~30μm。
[0061]
在其中一些实施方式中,发热层3为化学性能稳定、导电导热性能良好的金属层或合金层,发热层3为铜层、铁层、镍层、铬层、金层、银层、铂层、钯层、钼层等金属层以及金银合金层、金铂合金层、金银铂合金层、银钯合金层、银铂合金层、钯铜合金层、钯银合金层、镍铬合金层中的至少任一种。在其中一些具体实施例中,发热层3为镍铬合金层。镍铬合金层热性能良好,镍铬合金层价格相对于金层、银层、铂层、钯层等贵金属层或者金银合金层、金铂合金层、金银铂合金层、银钯合金层、银铂合金层、钯铜合金层、钯银合金层等贵金属合金层便宜。在其中一些更具体实施例中,发热层3为镍铬合金层,其ni/(ni+cr)质量比例为0.2~0.9。根据电阻计算公式可知,发热层3的厚度决定了发热层3的电阻值大小,发热层3的厚度越薄时电阻值越大,发热层3的厚度越厚时电阻值越小,故可通过调节与控制发热层3的厚度以达到调节发热层3电阻值的目的。同时,在研发过程中,通过大量的实验,发明人发
现:当发热层3的厚度太薄的话,薄层结构的发热层3比较疏松且连续性不好,影响发热层3电阻值的稳定性,发热层3比较容易被高温氧化或碳化;发热层3的厚度越厚,薄层结构的发热层3的连续性与致密性也会随之增加,使得发热层3的抗氧化或抗碳化的能力大幅度增强,从而增强发热层3电阻的稳定性。然而,当发热层3的厚度太厚的话,一方面,发热层3所需形成时间较长,从而大幅降低生产效率;另一方面,发热层3的应力越大,发热层3在通电使用过程中微观结构遭到破坏,影响发热层3电阻值的稳定性。以及考虑到发热层3的电阻太低存在发热层3短路过载的安全隐患,而发热层3的电阻太高存在达不到所需发热功率的问题,因此发热层3的常用电阻为0.8~2ω。考虑发热层3的厚度对发热层3电阻的稳定性的影响,以及考虑发热层3的厚度与形成时长的正向关联,并结合发热层3的常用电阻为0.8~2ω,综合上述考虑,发热层3的厚度设置为1~5μm。在其中一些具体实施例中,发热层3为镍铬合金层,镍铬合金层的厚度设置为1~5μm,以使得发热层3的电阻稳定性提高,发热层3的电阻处于常用电阻范围内,且发热层3的形成时间适中,进而使得雾化芯的电阻稳定性提高,雾化芯的发热功率较大,雾化芯的雾化效果好,雾化芯的制造成本可控。
[0062]
在其中一些实施方式中,薄膜沉积工艺可以是但不限于薄膜沉积工艺中的磁控溅射工艺。由于雾化芯的发热面积更大,发热更均匀,不会出现局部温度过高现象,有利于提高气溶胶形成基质受热的均匀性,从而提高雾化效果。在其中一些具体实施例中,通过磁控溅射工艺沉积形成发热层3,发热层3为镍铬合金层,磁控溅射工艺的靶材功率密度为5~15w/cm2,溅射气压为0.1~0.3pa,溅射时间为30~90min。这样,通过磁控溅射工艺,在多孔基底1的至少部分雾化面11上,沉积形成厚度为1~5μm的镍铬合金层,镍铬合金层形成发热层3。
[0063]
在通过薄膜沉积工艺沉积形成发热层3的过程中,发热层3形成的过程大致包括:1、岛初步形成:气态靶材达到多孔基底1的表面,附着并凝聚,形成一些均匀细小、而且可以运动的原子团,原地团被称为“岛”;2、岛数目饱和:“岛”不断接受新的沉积原子,并与其他小“岛”合并而逐渐长大,岛的数目快速达到饱和;3、岛长大形核:小“岛”合并不断进行的同时,空出来的多孔基底1的表面又会形成新的小“岛”;4、合并长大填充:小“岛”的形成与合并不断进行,尺寸较大的“岛”不断吞并附近尺寸较小的“岛”;5、填充孔隙成膜:孤立的小“岛”随着合并的进行相互连接成片,最后只留下一些孤立的孔洞和沟道,这些孔洞和沟道又不断被填充,形成形貌连续、覆盖完整的膜层。
[0064]
请结合参阅图1和图2,在其中一些实施方式中,雾化芯还包括形成在发热层3与多孔基底1之间的过渡层2。在一具体实施方式中,通过薄膜沉积工艺在多孔基底1的至少部分雾化面11上沉积形成厚度为0.1~1μm的过渡层2,过渡层2背离多孔基底1的一面上形成有发热层3。由于多孔基底1的表面上凹点的势能最低,过渡层2形成的过程与上述发热层3形成的过程相同,因此过渡层2降低多孔基底1表面的粗糙度,使得发热层3具有良好的连续性,便于调节控制发热层3的厚度。而且过渡层2还可以阻隔多孔基底1的钠、钾离子在电场作用下扩散进入发热层3,增强发热层3电阻的稳定性。此外,过渡层2能够起到调节发热层3与多孔基底1表面的应力匹配,增强发热层3与多孔基底1之间的附着力,使得发热层3牢固地结合于多孔基底1上,提高发热层3工作性能的稳定可靠性,延长雾化芯的使用寿命。在其中一些实施方式中,薄膜沉积工艺可以是但不限于薄膜沉积工艺中的磁控溅射工艺。
[0065]
在其中一些具体实施例中,通过磁控溅射工艺沉积形成过渡层2,磁控溅射工艺的
靶材功率密度为3~12w/cm2,溅射气压为0.1~0.5pa,溅射时间为20~100min,过渡层2的厚度为0.1~1μm。当过渡层2的厚度太薄时,过渡层2起不到上述降低多孔基底1表面的粗糙度以及阻隔多孔基底1的钠、钾离子在电场作用下扩散进入发热层3的作用;随着过渡层2厚度的增加,过渡层2能逐渐降低多孔基底1表面的粗糙度,逐渐阻隔多孔基底1的钠、钾离子在电场作用下扩散进入发热层3,逐渐调节发热层3与多孔基底1表面的应力匹配;然而,当过渡层2的厚度太厚的话,过渡层2应力会出现大幅增加,造成过渡层2在雾化芯通电使用过程中微观结构遭到破坏,过渡层2无法阻隔多孔基底1的钠、钾离子在电场作用下扩散进入发热层3,影响发热层3电阻值的稳定性。因此,将过渡层2的厚度设置为0.1~1μm,使得过渡层2降低多孔基底1表面的粗糙度,使得过渡层2阻隔多孔基底1的钠、钾离子在电场作用下扩散进入发热层3,使得过渡层2调节发热层3与多孔基底1表面的应力匹配。优选地,将过渡层2的厚度设置为0.3~0.8μm,在便于降低多孔基底1表面的粗糙度的同时,有利于阻隔多孔基底1的钠、钾离子在电场作用下扩散进入发热层3。
[0066]
在其中一些实施方式中,过渡层2与多孔基底1的应力值接近,使得过渡层2与多孔基底1的应力匹配较好。在其中一些具体实施例中,多孔基底1为多孔陶瓷,过渡层2为氮化铝层、氮化硅层、氮化铬层、碳化铬层或其他陶瓷层中的至少任一种。
[0067]
请结合参阅图1和图2,在其中一些实施方式中,雾化芯还包括形成在发热层3上保护层4。在一具体实施方式中,通过薄膜沉积工艺,在发热层3背离多孔基底1的一面上,沉积形成厚度为0.5~3μm的保护层4。保护层4阻隔气溶胶形成基质及外界空气进入发热层3,从而避免发热层3通电使用过程中发生氧化或碳化,增强发热层3的抗氧化性和抗碳化性,增强发热层3电阻的稳定性,提高雾化芯的循环使用寿命。在其中一些实施方式中,薄膜沉积工艺可以是但不限于薄膜沉积工艺中的磁控溅射工艺。在其中一些具体实施例中,通过磁控溅射工艺沉积形成保护层4,磁控溅射工艺的靶材功率密度为3~12w/cm2,溅射气压为0.1~0.5pa,溅射时间为40~150min。当保护层4的厚度太薄时,保护层4起不到阻隔气溶胶形成基质及外界空气进入发热层3的作用;随着保护层4厚度的增加,保护层4能逐渐阻隔气溶胶形成基质及外界空气进入发热层3;然而,当保护层4的厚度太厚的话,保护层4应力会出现大幅增加,造成保护层4在雾化芯通电使用过程中微观结构遭到破坏,保护层4无法阻隔气溶胶形成基质及外界空气进入发热层3,使得发热层3的抗氧化性和抗碳化性减弱,影响发热层3电阻的稳定性,缩短雾化芯的循环使用寿命。综合上述考虑,将保护层4的厚度设置为0.5~3μm,使得保护层4阻隔气溶胶形成基质及外界空气进入发热层3。优选地,将保护层4的厚度设置为0.8~1.5μm,能良好地阻隔气溶胶形成基质及外界空气进入发热层3。
[0068]
在其中一些实施方式中,保护层4的化学性能稳定且结构致密。在其中一些具体实施例中,保护层4为氧化铝层、氧化硅层、氮化铝层、氮化硅层、氧化钛层、氮化钛层中的至少任一种。
[0069]
请结合参阅图2,在其中一些实施方式中,发热层3上设有未沉积形成保护层4的成对设置的两个裸露部41,裸露部41用于实现电源装置与发热层3的电连接。
[0070]
本发明实施例一还提供一种雾化器,雾化器包括上述任一实施例提供的雾化芯。因雾化器具有上述任一实施例提供的雾化芯的全部技术特征,故其具有雾化芯相同的技术效果。
[0071]
本发明实施例一还提供一种气溶胶发生装置,气溶胶发生装置包括上述任一实施
例提供的雾化芯或上述任一实施例提供的的雾化器。因气溶胶发生装置具有上述任一实施例提供的雾化芯或雾化器的全部技术特征,故其具有雾化芯相同的技术效果。
[0072]
本发明实施例一还提供一种上述雾化芯的雾化芯制备方法,本发明实施例一中的雾化芯制备方法包括如下步骤:
[0073]
步骤s1:沉积过渡层:通过薄膜沉积工艺,在多孔基底1的至少部分雾化面11上沉积形成过渡层2;
[0074]
步骤s2:沉积发热层:通过薄膜沉积工艺,在过渡层2背离多孔基底1的一面上沉积形成发热层3;
[0075]
步骤s3:沉积保护层:通过薄膜沉积工艺,在发热层3背离过渡层2的一面上沉积形成保护层4。
[0076]
上述沉积过渡层步骤s1中,通过薄膜沉积工艺在多孔基底1的至少部分雾化面11上沉积形成厚度为0.1~1μm的过渡层2,过渡层2与多孔基底1的应力值接近。过渡层2降低多孔基底1表面的粗糙度,使得发热层3具有良好的连续性,便于调节控制发热层3的厚度。而且过渡层2还可以阻隔多孔基底1的钠、钾离子在电场作用下扩散进入发热层3,增强发热层3电阻的稳定性。此外,过渡层2能够起到调节发热层3与多孔基底1表面的应力匹配,增强发热层3与多孔基底1之间的附着力,使得发热层3牢固地结合于多孔基底1上,提高发热层3工作性能的稳定可靠性,延长雾化芯的使用寿命。具体地,薄膜沉积工艺可以是但不限于薄膜沉积工艺中的磁控溅射工艺。当通过磁控溅射工艺沉积形成过渡层2时,磁控溅射工艺的靶材功率密度为3~12w/cm2,溅射气压为0.1~0.5pa,溅射时间为20~100min,过渡层2的厚度为0.1~1μm。当过渡层2的厚度太薄时,过渡层2起不到上述降低多孔基底1表面的粗糙度以及阻隔多孔基底1的钠、钾离子在电场作用下扩散进入发热层3的作用;而当过渡层2的厚度太厚的话,过渡层2应力会出现大幅增加,造成过渡层2在雾化芯通电使用过程中微观结构遭到破坏,过渡层2无法阻隔多孔基底1的钠、钾离子在电场作用下扩散进入发热层3,影响发热层3电阻值的稳定性。因此,将过渡层2的厚度设置为0.1~1μm,使得过渡层2降低多孔基底1表面的粗糙度,使得过渡层2阻隔多孔基底1的钠、钾离子在电场作用下扩散进入发热层3,使得过渡层2调节发热层3与多孔基底1表面的应力匹配。优选地,将过渡层2的厚度设置为0.3~0.8μm,在便于降低多孔基底1表面的粗糙度的同时,有利于阻隔多孔基底1的钠、钾离子在电场作用下扩散进入发热层3。具体地,多孔基底1为多孔陶瓷,通过薄膜沉积工艺在多孔陶瓷的至少部分雾化面11上沉积形成过渡层2,过渡层2为氮化铝层、氮化硅层、氮化铬层、碳化铬层或其他陶瓷层中的至少任一种。
[0077]
上述沉积发热层步骤s2中,通过薄膜沉积工艺在过渡层2背离多孔基底1的一面上沉积形成发热层3。具体地,发热层3为镍铬合金层,镍铬合金层的厚度设置为1~5μm。镍铬合金层热性能良好,镍铬合金层价格相对于金层、银层、铂层、钯层等贵金属层或者金银合金层、金铂合金层、金银铂合金层、银钯合金层、银铂合金层、钯铜合金层、钯银合金层等贵金属合金层便宜。在其中一些更具体实施例中,发热层3为镍铬合金层,其ni/(ni+cr)质量比例为0.2~0.9。根据电阻计算公式可知,发热层3的厚度决定了发热层3的电阻值大小,发热层3的厚度越薄时电阻值越大,发热层3的厚度越厚时电阻值越小,故可通过调节与控制发热层3的厚度以达到调节发热层3电阻值的目的。同时,在研发过程中,通过大量的实验,发明人发现:当发热层3的厚度太薄的话,薄层结构的发热层3比较疏松且连续性不好,影响
发热层3电阻值的稳定性,发热层3比较容易被高温氧化或碳化;发热层3的厚度越厚,薄层结构的发热层3的连续性与致密性也会随之增加,使得发热层3的抗氧化或抗碳化的能力大幅度增强,从而增强发热层3电阻的稳定性。然而,当发热层3的厚度太厚的话,一方面,发热层3所需形成时间较长,从而大幅降低生产效率;另一方面,发热层3的应力越大,发热层3在通电使用过程中微观结构遭到破坏,影响发热层3电阻值的稳定性。以及考虑到发热层3的电阻太低存在发热层3短路过载的安全隐患,而发热层3的电阻太高存在达不到所需发热功率的问题,因此发热层3的常用电阻为0.8~2ω。考虑发热层3的厚度对发热层3电阻的稳定性的影响,以及考虑发热层3的厚度与形成时长的正向关联,并结合发热层3的常用电阻为0.8~2ω,综合上述考虑,发热层3为镍铬合金层,镍铬合金层的厚度设置为1~5μm,以使得发热层3的电阻稳定性提高,发热层3的电阻处于常用电阻范围内,且发热层3的形成时间适中,进而使得雾化芯的电阻稳定性提高,雾化芯的发热功率较大,雾化芯的雾化效果好,雾化芯的制造成本可控。具体地,薄膜沉积工艺可以是但不限于薄膜沉积工艺中的磁控溅射工艺。当通过磁控溅射工艺沉积形成发热层3,发热层3为镍铬合金层,磁控溅射工艺的靶材功率密度为5~15w/cm2,溅射气压为0.1~0.3pa,溅射时间为30~90min。这样,通过磁控溅射工艺,在多孔基底1的至少部分雾化面11上,沉积形成厚度为1~5μm的镍铬合金层,镍铬合金层为发热层3。
[0078]
上述沉积保护层步骤s3中,通过薄膜沉积工艺,在发热层3背离多孔基底1的一面上,沉积形成厚度为0.5~3μm的化学性能稳定且结构致密的保护层4。保护层4阻隔气溶胶形成基质及外界空气进入发热层3,从而避免发热层3通电使用过程中发生氧化或碳化,增强发热层3的抗氧化性和抗碳化性,增强发热层3电阻的稳定性,提高雾化芯的循环使用寿命。在其中一些实施方式中,薄膜沉积工艺可以是但不限于薄膜沉积工艺中的磁控溅射工艺。在其中一些具体实施例中,通过磁控溅射工艺沉积形成保护层4,磁控溅射工艺的靶材功率密度为3~12w/cm2,溅射气压为0.1~0.5pa,溅射时间为40~150min。当保护层4的厚度太薄时,保护层4起不到阻隔气溶胶形成基质及外界空气进入发热层3的作用;随着保护层4厚度的增加,保护层4能逐渐阻隔气溶胶形成基质及外界空气进入发热层3;然而,当保护层4的厚度太厚的话,保护层4应力会出现大幅增加,造成保护层4在雾化芯通电使用过程中微观结构遭到破坏,保护层4无法阻隔气溶胶形成基质及外界空气进入发热层3,使得发热层3的抗氧化性和抗碳化性减弱,影响发热层3电阻的稳定性,缩短雾化芯的循环使用寿命。综合上述考虑,将保护层4的厚度设置为0.5~3μm,使得保护层4阻隔气溶胶形成基质及外界空气进入发热层3。优选地,将保护层4的厚度设置为0.8~1.5μm,能良好地阻隔气溶胶形成基质及外界空气进入发热层3。具体地,保护层4为氧化铝层、氧化硅层、氮化铝层、氮化硅层、氧化钛层、氮化钛层中的至少任一种。
[0079]
可以理解的,上述雾化芯制备方法,主要包括采用薄膜沉积工艺将导电材料沉积在多孔陶瓷基底的至少部分外表面上,以在所述多孔陶瓷基底上形成发热层,获得表面具有发热层的雾化芯。在某些实施方式中,当不包括过渡层2和/或保护层4时,对应的膜层形成步骤s1、s3可以进行相应的省略。
[0080]
在其中另一些实施方式中,上述雾化芯的雾化芯制备方法还包括:
[0081]
步骤s4:采用退火老化工艺,对雾化芯进行退火热处理。
[0082]
在其中一些实施方式中,上述雾化芯的雾化芯制备方法还包括:
[0083]
步骤s5:采用通电老化工艺,对退火热处理后的雾化芯进行供电,退火热处理后的雾化芯通电后发热,以对发热层3的微观结构进行老化处理。
[0084]
上述步骤s4中,采用退火老化工艺,对带有发热层3的雾化芯进行退火热处理。退火热处理目的是消除发热层3的微观缺陷,促使发热层3的微观结构中的晶粒长大,使得发热层3更加致密,从而提高雾化芯在循环使用过程中电阻值的稳定性,进而使得雾化芯发热功率稳定,加热均匀,雾化效果好。结合上述发热层3形成的过程,从热力学条件来看,在一定体积的发热层3中,发热层3内晶粒越粗,总的晶界表面积就越小,总的表面能越低。由于晶粒粗化可以减小表面能,使发热层3处于较稳定的、自由能较低的状态,要实现向稳定的、自由能较低方向的变化趋势,需要导电材料原子有较强的扩散能力,以完成晶粒长大时晶界的迁移运动,而高温的退火热处理正使其具备了这一条件。因此,将带有发热层3的雾化芯的进行退火热处理,可促使发热层3的微观结构中的晶粒长大,使得发热层3更加致密,提高发热层3在通电使用过程中电阻的稳定性,从而提高雾化芯在通电使用过程中电阻的稳定性。
[0085]
在其中一些具体实施例中,对雾化芯的发热层3进行退火热处理的温度为500~800℃,退火热处理的时间为5~60min。上述步骤s4中,雾化芯退火热处理过程,是在保护气体氛围中进行的。具体地,将雾化芯置于管式炉中进行退火热处理,在雾化芯退火热处理过程中,不断向管式炉中充入保护气体,以防止雾化芯退火热处理过程中发热层3发生氧化。保护气体可以是但不限于氮气。
[0086]
可以理解地,上述过渡层2以及保护层4,在退火热处理过程中的变化趋势与发热层3相同。具体地,从热力学条件来看,在一定体积的过渡层2或保护层4中,过渡层2或保护层4内晶粒越粗,总的晶界表面积就越小,总的表面能越低。由于晶粒粗化可以减小表面能,使过渡层2或保护层4处于较稳定的、自由能较低的状态,要实现向稳定的、自由能较低方向的变化趋势,需要导电材料原子有较强的扩散能力,以完成晶粒长大时晶界的迁移运动,而高温的退火热处理正使其具备了这一条件。因此,将雾化芯的过渡层2或保护层4进行退火热处理,可促使过渡层2或保护层4的微观结构中的晶粒长大,使得过渡层2或保护层4更加致密,从而提高雾化芯在循环使用过程中电阻值的稳定性。
[0087]
在上述步骤s5中,通过将退火热处理后的雾化芯进行通电老化处理:对退火热处理后的雾化芯进行供电,退火热处理后的雾化芯通电后发热,对发热层3的微观结构进行老化处理,以增强发热层3的电学稳定性。在其中一些具体实施例中,在在大气氛围下,采用直流稳压电源对雾化芯的发热层3进行供电,通电功率为6~8w,通电时间为1~20min。上述将雾化芯进行通电老化处理的目的是,提高雾化芯通电使用过程中电阻的稳定性。
[0088]
本发明实施例一中的雾化芯制备方法,与现有技术相比,采用退火老化工艺,对雾化芯的发热层3进行退火热处理,使发热层3微观结构中的晶粒长大,促使发热层3更加致密,减少发热层3的微观缺陷;然后,对退火热处理后的雾化芯进行通电发热处理,以对发热层3的微观结构进行进一步的老化处理。这样,雾化芯在经过退火热处理及通电老化处理后,能够改善并提高发热层3电阻的稳定性,增强了发热层3的电学稳定性,进而使得发热层3发热更均匀,防止雾化芯出现局部温度过高的现象,可对气溶胶形成基质具有良好的雾化效果。
[0089]
另外,值得注意的是,本发明实施例一中是先对具有发热层3的雾化芯进行退火热
处理,而后对退火热处理的雾化芯进行通电老化处理。上述加工处理的次序不能发生调换的,这是为了模拟雾化芯真实的使用氛围,由于通电老化处理一般是在大气氛围下进行的,而退火热处理通常是在保护气体氛围下进行的,如果先对雾化芯进行通电老化处理,会导致保护层4的稳定性较差,且造成发热层3会在大气氛围下发生氧化或碳化,进而影响发热层3的使用寿命。因此,先在保护气体氛围下对具有发热层3的雾化芯进行退火热处理,使得发热层3内部结构的晶粒粗化以减小表面能,从而使雾化芯上的过渡层2、发热层3以及保护层4处于较稳定的、自由能较低的状态,进而使过渡层2、发热层3以及保护层4更加致密,减少过渡层2、发热层3以及保护层4的微观缺陷,提高过渡层2、发热层3以及保护层4的稳定性。一方面,经退火热处理后,稳定且致密的过渡层2可以阻隔多孔陶瓷基底1的钠、钾离子在电场作用下扩散进入发热层3,进一步提高发热层3的电阻稳定性;另一方面,经退火热处理后,稳定且致密的发热层3可以增强发热层3的电阻稳定性;再一方面,经退火热处理后,稳定且致密的保护层4可使发热层3与气溶胶形成基质及空气中的氧隔离,提高发热层3的抗氧化性能和抗碳化性能,从而提高发热层3的电阻稳定性。而后,在大气氛围下对具有发热层3的雾化芯进行通电老化处理:对过渡层2、发热层3以及保护层4的微观结构进行老化处理,更进一步提高发热层3的电阻稳定性。
[0090]
实施例二
[0091]
实施例二中的雾化芯与实施例一中的雾化芯区别在于:
[0092]
雾化芯还包括用于将发热层3与电源装置进行电连接的两个电极5。请结合参阅图4和图5,在一具体实施例方式中,电极5通过厚膜沉积工艺形成于多孔基底1的雾化面11上,电极5的厚度为20~60μm。一方面,使电极5牢固地结合在多孔基底1上,防止电极5在高温高速气溶胶形成基质流体冲击下发生脱落,另一方面,使得电极5在与金属弹针电连接时有足够强度支撑其承受来自于金属弹针的抵压作用力,再一方面,使得电极5有足够的接触面积与金属弹针电连接,则可方便通过金属弹针与电源装置实现电连接,进而便于发热层3通过电极5与电源装置实现电连接。
[0093]
在其中一些实施方式中,电极5为金层、银层、铂层、钯层、铝层、铜层、金银合金层、银铂合金层、银钯合金层中的至少任一种。在其中一些具体实施例中,采用丝网印刷工艺在多孔基底1上丝印金属浆料,烘干、烧结后形成电极5。金属浆料为由金、银、铂、钯、铝、铜、金银合金、银铂合金、银钯合金中的至少任一种,以在多孔基底1上形成电极5。
[0094]
请结合参阅图3和图4,在其中一些实施方式中,电极5成对并间隔布置于雾化面11上的第一区域11a,发热层3至少覆设于雾化面11上的第二区域11b,第二区域11b为雾化面11上于第一区域11a之外的区域,以使第一区域11a与第二区域11b在雾化面11上为连续区域,发热层3包括形成于多孔基底1的雾化面11上的第二区域11b的发热部31、形成在其中一个电极5至少部分表面的第一连接部32,形成在另一个电极5至少部分表面的第二连接部33,第一连接部32、第二连接部33分别与发热部31连接。通过面与面的接触形式将发热层3与相应电极5电性相连,避免电极5与发热层3出现接触不良,从而提高向发热层3供电的稳定可靠性。
[0095]
请结合参阅图3和图4,在其中一些实施方式中,电极5成对并间隔布置于雾化面11上的第一区域11a,过渡层2形成于雾化面11上的第二区域11b,发热层3覆设于过渡层2背离多孔基底1的一面上。可以理解地,该实施方式中,第二区域11b同样为雾化面11上于第一区
域11a之外的区域,以使第一区域11a与第二区域11b在雾化面11上为连续区域。发热层3包括形成于过渡层2背离多孔基底1的一面上的发热部31、形成在其中一个电极5至少部分表面的第一连接部32,形成在另一个电极5至少部分表面的第二连接部33,第一连接部32、第二连接部33分别与发热部31连接。通过面与面的接触形式将发热层3与相应电极5电性相连,避免电极5与发热层3出现接触不良,从而提高向发热层3供电的稳定可靠性。
[0096]
请结合参阅图4和图5,在其中一些实施方式中,电极5的厚度大于过渡层2、发热部31以及保护层4的厚度之和,两个电极5之间可以形成凹槽6,凹槽6内由凹槽6的内底面自下往上依次层叠设置有过渡层2、发热部31和保护层4,将过渡层2、发热部31与保护层4容置并定位于两个电极5之间的凹槽6中,有利于增强过渡层2、发热部31与保护层4结合于多孔基底1上的稳固性。
[0097]
请结合参阅图4,在一具体实施方式中,发热层3还至少部分形成在电极5上。
[0098]
请结合参阅图4,在其中一些具体实施例中,第一连接部32包括由发热部31靠近其中一个电极5的一侧并沿该电极5的厚度方向弯折延伸的第一侧部321,第二连接部33包括由发热部31靠近另一个电极5的一侧并沿该电极5的厚度方向弯折延伸的第二侧部331,第一侧部321与第二侧部331分别结合于相应电极5的对应侧面上。可通过第一侧部321与第二侧部331分别与相应电极5的对应侧面结合,通过面与面的接触形式将发热层3与相应电极5电性相连,避免电极5与发热层3出现接触不良,从而提高向发热层3供电的稳定可靠性。
[0099]
请结合参阅图4,在其中一些更具体实施例中,第一连接部32还包括形成于其中一个电极5背离多孔基底1的一面上的第一结合部322,第二连接部33还包括形成于另一个电极5背离多孔基底1的一面上的第二结合部332,第一结合部322的对应侧边与第一侧部321的对应侧边相连,第二结合部332的对应侧边与第二侧部331的对应侧边相连。一方面增大了电极5与发热层3的接触面积,有利于提高电极5向发热层3供电的稳定性;另一方面增大了电极5与发热层3的接触面积,从而减小了发热层3与电极5的接触电阻,有利于将发热区域集中在发热部31;再一方面可增强发热层3的附着力,使得发热层3更加牢固地结合于多孔基底1及电极5上。具体地,上述实施例中的雾化面11为一平面。
[0100]
可以理解地,发热部31、第一连接部32以及第二连接部33是形成发热层3时一次形成的,在第一连接部32不包括第一结合部322,第二连接部33不包括第二结合部332的情况下,只需要在通过薄膜沉积工艺形成发热层3时,对电极5背离多孔基底1的一面进行掩膜处理,使发热层3无法沉积形成在电极5背离多孔基底1的一面。
[0101]
本发明实施例二还提供一种雾化器,雾化器包括上述任一实施例提供的雾化芯。因雾化器具有上述任一实施例提供的雾化芯的全部技术特征,故其具有雾化芯相同的技术效果。
[0102]
本发明实施例二还提供一种气溶胶发生装置,气溶胶发生装置包括上述任一实施例提供的雾化芯或上述任一实施例提供的的雾化器。因气溶胶发生装置具有上述任一实施例提供的雾化芯或雾化器的全部技术特征,故其具有雾化芯相同的技术效果。
[0103]
本发明实施例二还提供一种上述雾化芯的雾化芯制备方法,本发明实施例二中的雾化芯制备方法与实施例一中的雾化芯制备方法区别在于:
[0104]
上述雾化芯的雾化芯制备方法还包括:
[0105]
步骤s0:电极制作:采用丝网印刷的方式在多孔基底1上丝印金属浆料,烘干、烧结
后形成电极5。可以理解的,在其他实施方式中,电极5也可以通过其他方式形成。
[0106]
在其中一些实施方式中,在沉积过渡层步骤之前,将丝网印刷有电极5的多孔基底1放入真空室中,抽真空至0.003pa,采用考夫曼型离子源对对多孔基底1进行离子清洗2~10min。
[0107]
实施例三
[0108]
实施例三中的雾化芯与实施例二中的雾化芯区别在于:雾化面11不是一个平面。具体地,请结合参阅图6和图7,多孔基体1的一表面上分别凹陷形成有第一凹陷部13和第二凹陷部14,第一凹陷部13与第二凹陷部14间隔设置,以使第一凹陷部13与第二凹陷部14之间的部分形成凸起部12,雾化面11包括凸起部12背离多孔基体1的第一表面11c、第一凹陷部13背离多孔基体1的第二表面11d、第二凹陷部14背离多孔基体1的第三表面11e、连接第一表面11c与第二表面11d的第一过渡面11f,以及连接第一表面11c与第三表面11e的第二过渡面11g。其中一个电极5沉积形成在第一凹陷部13中,另一个电极5沉积形成在第二凹陷部14中,发热部31沉积形成在凸起部12的第一表面11c上,两个电极5的上端面高于发热部31的上端面。
[0109]
实施例四
[0110]
实施例四中的雾化芯与实施例三中的雾化芯区别在于:两个电极5的上端面与发热层3的下端面齐平,发热层3为形成在多孔基底1和电极5上的一层连续的板片状结构层。具体地,请结合参阅图8,发热层3包括形成于多孔基底1的雾化面11上的第二区域11b的发热部31、形成在其中一个电极5至少部分表面的第一连接部32,形成在另一个电极5至少部分表面的第二连接部33,第一连接部32、第二连接部33分别与发热部31连接。第一连接部32包括形成于其中一个电极5背离多孔基底1的一面上的第一结合部322,第二连接部33包括形成于另一个电极5背离多孔基底1的一面上的第二结合部332。第一结合部322的对应侧边与发热部31的对应侧边相连,第二结合部332的对应侧边与发热部31的对应侧边相连。也就是说,第一连接部32可以不包括第一侧部321,第二连接部33可以不包括第二侧部331,第一连接部32的第一结合部322分别连接其中一个电极5和发热部31,第二连接部33的第二结合部332分别连接另一个电极5和发热部31。一方面增大了电极5与发热层3的接触面积,有利于提高电极5向发热层3供电的稳定性;另一方面增大了电极5与发热层3的接触面积,从而减小了发热层3与电极5的接触电阻,有利于将发热区域集中在发热部31;再一方面可增强发热层3的附着力,使得发热层3更加牢固地结合于多孔基底1及电极5上。具体地,上述实施例中的雾化面11为一平面。
[0111]
实验例
[0112]
为使本发明上述实施细节和操作能清楚地被本领域技术人员理解,以及本发明雾化芯制备方法的进步性能显著地体现,以下通过具体实验例对本发明的雾化芯制备方法的具体实施过程进行举例说明。
[0113]
实验例1
[0114]
1)采用丝网印刷工艺在多孔基底1上丝印银钯金属浆料,烘干、烧结后形成电极5。其中,电极5烘干的温度为80,电极5烘干的时间20min,烧结的条件为在910℃温度环境保温20min;
[0115]
2)将丝网印刷有银钯金属电极5的多孔基底1放入磁控溅射真空室中,抽真空至
0.003pa,采用考夫曼型离子源对基底进行离子清洗5min,离子源功率为200w;
[0116]
3)采用磁控溅射工艺,在离子清洗后的多孔基底1的外表面直接沉积发热层3。其中,所使用的镍铬合金靶材中ni/(ni+cr)的质量比为80%,镍铬合金靶材溅射功率密度为10w/cm2,溅射气压为0.3pa,溅射时间为30min。
[0117]
采用台阶仪,对实验例1中沉积于多孔基底1上的发热层3进行厚度测试,测得发热层3的厚度为1μm。将实验例1制备的雾化芯标记为s
‑
1,将此雾化芯s
‑
1与电池、烟弹组装成电子烟在电子烟抽烟机上进行模拟抽吸测试。测试结束后将雾化芯s
‑
1取出测量其电阻值的变化。从图9中可以明显看出在前3000次循环,雾化芯s
‑
1的阻值在测试初期变化非常明显,而后续电阻值变化幅度明显降低。雾化芯s
‑
1电阻值循环测试初期明显变化的原因:一方面是由于在高温条件下,多孔基底1中的钠、钾离子电场作用下渗入到发热层3中,使得发热层3的微观结构发生了变化;另一方面是由于在高温条件下,发热层3与气溶胶形成基质或空气中的氧发生了碳化或氧化。
[0118]
实验例2
[0119]
实验例2与实验例1的区别在于:磁控溅射发热层3的时间不同,实验例2中的溅射时间为60min,以增加多孔基底1上沉积发热层3的厚度。采用台阶仪,测得实验例2中发热层3的厚度为3μm,并将实验例2制备的雾化芯标记为s
‑
2。与实验例1一样组装成电子烟在电子烟抽烟机上进行模拟抽吸测试,测试结束后测量雾化芯电阻值变化。
[0120]
实验例3
[0121]
实验例3与实验例1的区别在于:磁控溅射发热层3的时间不同,实验例3中的溅射时间为90min,以增加多孔基底1上沉积发热层3的厚度。采用台阶仪,测得实验例3中发热层3的厚度为5μm,并将实验例3制备的雾化芯标记为s
‑
3。与实验例1一样组装成电子烟在电子烟抽烟机上进行模拟抽吸测试,测试结束后测量雾化芯电阻值变化。
[0122]
实验例4
[0123]
此实验例与实验例2的区别在于:在沉积发热层3之前,先采用掩膜将丝网印刷于多孔基底1上的银钯金属电极5遮蔽,再在多孔基底1的至少部分外表面上沉积氮化铝过渡层2,防止氮化铝沉积在银钯金属电极5上。具体地,采用磁控溅射工艺,在多孔基底1上沉积氮化铝。其中,反应气体为氮气,氩气为工作气体,氮气/氩气气体流量比为1.2,溅射气压为0.35pa,金属铝靶材溅射功率密度为8w/cm2,溅射时间为20min。采用台阶仪,测得实验例4中氮化铝过渡层2的厚度为0.1μm。沉积完氮化铝过渡层2后,采用与实验例1相同的工艺步骤,继续在氮化铝过渡层2背离多孔基底1的一面上沉积发热层3。同时采用与实验例1相同的仪器及测试方法,测得实验例4中的发热层3厚度为3μm。并且,将实验例4制备的雾化芯标记为s
‑
4,采用同实验例1一样的方法,对雾化芯s
‑
4进行循环可靠性测试,并测量其电阻值。
[0124]
实验例5
[0125]
实验例5与实验例4的区别在于:磁控溅射氮化铝过渡层2的时间不同,溅射时间为50min。采用台阶仪,测得实验例5中的氮化铝过渡层2的厚度为0.5μm,并将实验例5制备的雾化芯标记为s
‑
5。采用同实验例1一样的方法,对雾化芯s
‑
5进行循环可靠性测试,并测量其电阻值。
[0126]
实验例6
[0127]
实验例6与实验例4的区别在于:磁控溅射氮化铝过渡层2的时间不同,溅射时间为
100min。采用台阶仪,测得实验例6中的氮化铝过渡层2的厚度为1μm,并将实验例6制备的雾化芯标记为s
‑
6。采用同实验例1一样的方法,对雾化芯s
‑
6进行循环可靠性测试,并测量其电阻值。
[0128]
实验例7
[0129]
实验例7与实验例5的区别在于:在发热层3上沉积氧化铝保护层,即在实验例5中沉积完发热层3后,采用磁控溅射工艺继续在发热层3背离多孔基底1的一面上沉积氧化铝保护层。磁控溅射氧化铝保护层之前,采用掩膜将丝网印刷于多孔基底1上的银钯金属电极5遮蔽,防止氧化铝沉积在银钯金属电极5上。具体地,沉积氧化铝保护层采用磁控溅射工艺,磁控溅射的反应气体为氧气,氩气为工作气体,氧气/氩气气体流量比为1.5,溅射气压为0.4pa,金属铝靶材溅射功率密度为9w/cm2,溅射时间为40min。采用台阶仪,测得实验例7中的氧化铝保护层厚度为0.5μm,并将实验例7制备的雾化芯标记为s
‑
7。采用同实验例1一样的方法,对雾化芯s
‑
7进行循环可靠性测试,并测量其电阻值。
[0130]
实验例8
[0131]
实验例8与实验例7的区别在于:磁控溅射氧化铝保护层的时间不同,溅射时间为90min。采用台阶仪,测得实验例8中的氧化铝保护层厚度为1.5μm,并将实验例8制备的雾化芯标记为s
‑
8。采用同实验例1一样的方法,对雾化芯s
‑
8进行循环可靠性测试,并测量其电阻值。
[0132]
实验例9
[0133]
实验例9与实验例7的区别在于:磁控溅射氧化铝保护层的时间不同,溅射时间为150min。采用台阶仪,测得实验例9中的氧化铝保护层厚度为3μm,并将实验例9制备的雾化芯标记为s
‑
9。采用同实验例1一样的方法,对雾化芯s
‑
9进行循环可靠性测试,并测量其电阻值。
[0134]
实验例10
[0135]
实验例10与实验例8的区别在于:将实验例8中制备的雾化芯,置于管式炉中进行退火热处理。其中,管式炉内的保护气体为氮气,退火温度为500℃,退火时间为10min。将实验例10中退火处理后的雾化芯标记为s
‑
10,采用同实验例1一样的方法,对雾化芯s
‑
10进行循环可靠性测试,并测量其电阻值。
[0136]
实验例11
[0137]
实验例11与实验例10的区别在于:退火温度温度不同,退火温度为700℃。将实验例11中退火处理后的雾化芯标记为s
‑
11,采用同实验例1一样的方法,对雾化芯s
‑
11进行循环可靠性测试,并测量其电阻值。
[0138]
实验例12
[0139]
实验例12与实验例10的区别在于:退火温度温度不同,退火温度为800℃。将实验例12中退火处理后的雾化芯标记为s
‑
12,采用同实验例1一样的方法,对雾化芯s
‑
12进行循环可靠性测试,并测量其电阻值。
[0140]
实验例13
[0141]
实验例13与实验例11的区别在于:将实验例11中制备的雾化芯,进行通电发热老化处理。其中,通电发热老化处理所使用的电源为直流稳压电源,通电功率为5w,通电2s后停5s然后继续通电2s停5s,一共进行100个循环。将实验例13中通电发热老化处理后的雾化
芯标记为s
‑
13,采用同实验例1一样的方法,对雾化芯s
‑
13进行循环可靠性测试,并测量其电阻值。
[0142]
实验例14
[0143]
实验例14与实验例13的区别在于:通电功率为7w。将实验例14中通电发热老化处理后的雾化芯标记为s
‑
14,采用同实验例1一样的方法,对雾化芯s
‑
14进行循环可靠性测试,并测量其电阻值。
[0144]
实验例15
[0145]
实验例15与实验例13的区别在于:通电功率为9w。将实验例15中通电发热老化处理后的雾化芯标记为s
‑
15,采用同实验例1一样的方法,对雾化芯s
‑
15进行循环可靠性测试,并测量其电阻值。
[0146]
雾化芯相关性能测试:
[0147]
将上述实验例1至实验例15中的雾化芯,分别进行循环可靠性测试,并测量其电阻值。测试结果如下述表1。
[0148]
表1实验例1至实验例15中的雾化芯循环测试电阻值数据表
[0149][0150]
需要说明的,表1中总循环的变化电阻值是指第3000次循环测试后测试样品的电阻值与测试样品的初始电阻值之间的差值,表1中总循环的变化电阻率是指测试样品的上
述变化电阻值与测试样品的初始电阻值得出的比率。可以理解的,总循环的变化电阻值越小和/或总循环的变化电阻率越小,可以判断为循环测试后的电阻值变化减小,测试样品在循环测试中的电阻稳定性越高。
[0151]
需要说明的,表1中雾化芯s
‑
1至雾化芯s
‑
15的循环测试数据均为一件测试样品通过测试得出的数据。除去雾化芯s
‑
1至雾化芯s
‑
3因分别具有不同厚度的发热层3所以初始电阻值不同。在其余雾化芯中,在循环测试前,控制单一变化量的对比例会从同一批次多个测试样品中挑选初始电阻值较为接近的测试样品,例如:雾化芯s
‑
4至雾化芯s
‑
6控制为过渡层2厚度不同的单一变化量,从同一批次的发热层3的厚度为3μm的雾化芯s
‑
2的多个测试样品中挑选初始电阻值较为接近的测试样品。
[0152]
结合图9、图11及表1可以看出,在前3000次循环,实验例1中的雾化芯s
‑
1的阻值变化非常明显,其循环测试的变化电阻值达到1.21ω,变化电阻率达到77.6%。实验例1中的雾化芯s
‑
1在循环测试中电阻值明显变化的原因:一方面是由于在高温条件下,多孔基底1中的钠、钾离子电场作用下渗入到发热层3中,使得发热层3的微观结构发生了变化,以及多孔基底1中的钠、钾离子电场作用下渗入到发热层3中;另一方面是由于在高温条件下,发热层3与气溶胶形成基质或空气中的氧发生了碳化或氧化。
[0153]
结合图9、图11及表1可以看出,实验例1中的雾化芯s
‑
1,其发热层3的厚度为1μm,其初始电阻值为1.56ω,实验例2中的雾化芯s
‑
2,其发热层3的厚度为3μm,其初始电阻值为1.25ω,以及实验例3中的雾化芯s
‑
3,其发热层3的厚度为5μm,其初始电阻值为1.07ω,因实验例1至实验例3中的发热层3厚度分别不同,其对应的初始电阻值也会随之不同:发热层3厚度越大,其初始电阻值越低。这样,就可以通过改变发热层3厚度来调整雾化芯的初始电阻值。
[0154]
结合图11及表1还可以看出,实验例1中的雾化芯s
‑
1,其发热层3的厚度为1μm,其循环测试的变化电阻值为1.21ω,变化电阻率为77.6%,实验例2中的雾化芯s
‑
2,其发热层3的厚度为3μm,其循环测试的变化电阻值为0.67ω,变化电阻率为53.6%,及实验例3中的雾化芯s
‑
3,其发热层3的厚度为5μm,其循环测试的变化电阻值为0.54ω,变化电阻率为50.5%,因分别具有不同厚度的发热层3,发热层3厚度越大,其循环测试后阻值变化减小。这是由于发热层3是通过薄膜沉积方式形成于多孔基底1上,如果多孔基底1表面粗糙度较大,而发热层3比较薄的话,发热层3呈不连续、疏松状分布,使用过程中发热层3容易被氧化或碳化,影响其电阻值的稳定性。发热层3越厚,发热层3呈连续性、致密状分布,提高抗氧化或碳化能力,从而使得电阻值越稳定。
[0155]
结合图9、图12及表1中测试数据可以看出,以实验例2中的雾化芯s
‑
2为对比例,其循环测试的变化电阻值为0.67ω,变化电阻率为53.6%,实验例4中的雾化芯s
‑
4循环测试的变化电阻值为0.53ω,变化电阻率为42.7%,实验例5中的雾化芯s
‑
5循环测试的变化电阻值为0.4ω,变化电阻率为32.5%,及实验例6中的雾化芯s
‑
6循环测试的变化电阻值为0.47ω,变化电阻率为37.9%,雾化芯在前3000次循环测试中,其电阻值的变化均要小于实验例2中的雾化芯s
‑
2雾化芯的电阻值,说明氮化铝过渡层2的设置,提高了雾化芯的发热层3的电阻稳定性。这是由于氮化铝过渡层2能降低多孔基底1表面的粗糙度,提高发热层3的连续性,同时氮化铝过渡层2也能够阻隔多孔基底1中钠钾离子渗入发热层3中,达到改善和提高雾化芯的发热层3电阻稳定性的目的。
[0156]
结合图12及表1可以看出,以实验例2中的雾化芯s
‑
2为对比例,其循环测试的变化电阻值为0.67ω,变化电阻率为53.6%,实验例4至实验例6中的雾化芯s
‑
4、雾化芯s
‑
5和雾化芯s
‑
6中,实验例4中的雾化芯s
‑
4的氮化铝过渡层2厚度为0.1μm,其循环测试的变化电阻值为0.53ω,变化电阻率为42.7%,电阻值稳定性有所提高;实验例5中的雾化芯s
‑
5的氮化铝过渡层2厚度为0.5μm,其循环测试的变化电阻值为0.4ω,变化电阻率为32.5%,电阻值稳定性进一步提高。实验例6中的雾化芯s
‑
6的氮化铝过渡层2厚度为1μm,其循环测试的变化电阻值为0.47ω,变化电阻率为37.9%,电阻值稳定性反而出现下降。这是由于氮化铝过渡层2能阻隔多孔基底1中的钠钾离子在电场下渗入发热层3,氮化铝过渡层2在一定厚度范围内,其厚度越厚其阻隔效果越好。但随着氮化铝过渡层2厚度提高到1μm,氮化铝过渡层应力会出现大幅度增加,造成发热层3在循环测试过程中微观结构遭到破坏,致使雾化芯循环测试的电阻值稳定性反而出现下降。
[0157]
结合图9、图13及表1中测试数据可以看出,以实验例5中的雾化芯s
‑
5为对比例,其循环测试的变化电阻值为0.4ω,变化电阻率为32.5%,实验例7中的雾化芯s
‑
7,在3000次循环测试后,其循环测试的变化电阻值为0.34ω,变化电阻率为27%,实验例8中的雾化芯s
‑
8,在3000次循环测试后,其循环测试的变化电阻值为0.24ω,变化电阻率为18.9%,实验例9中的雾化芯s
‑
9,在3000次循环测试后,其循环测试的变化电阻值为0.29ω,变化电阻率为22.7%,实验例7至实验例9中的雾化芯s
‑
7、雾化芯s
‑
8和雾化芯s
‑
9的电阻值变化明显要小于实验例5中的雾化芯s
‑
5,这是由于氧化铝保护层的设置,使发热层3与气溶胶形成基质及空气中的氧隔离,避免长期使用过程中发热层3被高温碳化和氧化而影响电阻值的稳定性,从而改善雾化芯的发热层3的电阻稳定性,且提高雾化芯的循环使用寿命。
[0158]
结合图13及表1可以看出,以实验例5中的雾化芯s
‑
5为对比例,其循环测试的变化电阻值为0.4ω,变化电阻率为32.5%,实验例7至实验例9中的雾化芯s
‑
7、雾化芯s
‑
8和雾化芯s
‑
9中,实验例7中的雾化芯s
‑
7的氧化铝保护层厚度为0.5μm,其循环测试的变化电阻值为0.34ω,变化电阻率为27%,其循环测试的电阻值稳定性有所提高,实验例8中的雾化芯s
‑
8的氧化铝保护层厚度为1.5μm,其循环测试的变化电阻值为0.24ω,变化电阻率为18.9%,其循环测试的电阻值稳定性进一步提高。实验例9中的雾化芯s
‑
9的氧化铝保护层厚度为3μm,其循环测试的变化电阻值为0.29ω,变化电阻率为22.7%,其循环测试的电阻值稳定性反而出现下降。这是由于氧化铝保护层在一定厚度范围内,其厚度越厚其氧化铝保护层的致密性越高,能够更好地将发热层3与气溶胶形成基质及空气中的氧隔离。但随着氧化铝保护层厚度提高到3μm,氧化铝保护层应力会出现大幅度增加,造成氧化铝保护层在循环测试过程中微观结构遭到破坏,致使雾化芯循环测试的电阻值稳定性反而出现下降。
[0159]
结合图9、图14及表1中测试数据可以看出,以实验例8中的雾化芯s
‑
8为对比例,其循环测试的变化电阻值为0.24ω,变化电阻率为18.9%,实验例10中的雾化芯s
‑
10,在3000次循环测试后,其循环测试的变化电阻值为0.18ω,变化电阻率为13.5%,实验例11中的雾化芯s
‑
11,在3000次循环测试后,其循环测试的变化电阻值为0.13ω,变化电阻率为9.7%,实验例12中的雾化芯s
‑
12,在3000次循环测试后,其循环测试的变化电阻值为0.21ω,变化电阻率为15.4%,实验例10至实验例12中的雾化芯s
‑
10、雾化芯s
‑
11和雾化芯s
‑
12的电阻值变化明显要小于实验例8中的雾化芯s
‑
8,这是由于退火热处理能减少过渡层2、发热层3和保护层4的微观缺陷,使发热层3的微观结构中的晶粒长大,促使发热层3更加致密,从而
提高雾化芯的发热层3循环测试电阻的稳定性。
[0160]
结合图14及表1中测试数据可以看出,以实验例8中的雾化芯s
‑
8为对比例,其循环测试的变化电阻值为0.24ω,变化电阻率为18.9%,实验例10至实验例12中的雾化芯s
‑
10、雾化芯s
‑
11和雾化芯s
‑
12中,实验例10中的雾化芯s
‑
10,其循环测试的变化电阻值为0.18ω,变化电阻率为13.5%,实验例10中的雾化芯s
‑
10的循环测试的电阻值稳定性,相对于实验例8中未退火热处理的雾化芯s
‑
8的循环测试的电阻值稳定性,没有明显的提高,这是由于500℃的温度过低,没有达到发热层3微观结构中的晶粒长大需要的能量。实验例11中将退火温度提高至700℃,实验例11中的雾化芯s
‑
11,其循环测试的变化电阻值为0.13ω,变化电阻率为9.7%,实验例11中的雾化芯s
‑
11循环测试的电阻稳定性明显提高。但随着实验例12中将退火温度进一步提高至800℃,实验例12中的雾化芯s
‑
12,其循环测试的变化电阻值为0.21ω,变化电阻率为15.4%,实验例12中的雾化芯s
‑
12循环测试电阻稳定性反而降低,这是因为过高的温度会破坏过渡层2、发热层3或保护层4的微观结构,影响发热层3循环测试电阻的稳定性。
[0161]
结合图9、图15及表1中测试数据可以看出,以实验例11中的雾化芯s
‑
11为对比例,其循环测试的变化电阻值为0.13ω,变化电阻率为9.7%,实验例13中的雾化芯s
‑
13,在3000次循环测试后,其循环测试的变化电阻值为0.1ω,变化电阻率为6.8%,实验例14中的雾化芯s
‑
14,在3000次循环测试后,其循环测试的变化电阻值为0.07ω,变化电阻率为4.8%,实验例13至实验例14中的雾化芯s
‑
13和雾化芯s
‑
14的电阻值变化明显要小于实验例11中的雾化芯s
‑
11,这是通电发热老化处理能提高发热层3电学稳定性,达到改善和提高高发热层3循环测试电阻的稳定性的目的。
[0162]
结合图10、图15及表1中测试数据可以看出,以实验例11中的雾化芯s
‑
11为对比例,其循环测试的变化电阻值为0.13ω,变化电阻率为9.7%,实验例13中的雾化芯s
‑
13中,其通电发热老化处理的功率为5w,其循环测试的变化电阻值为0.1ω,变化电阻率为6.8%,实验例13中的雾化芯s
‑
13的循环测试的电阻值稳定性,相对于实验例11中未退火热处理的雾化芯s
‑
11的循环测试的电阻值稳定性,没有明显的提高。这是由于通电发热老化处理的功率过低,发热层3的发热量较小,发热层3的微观结构改善较小,从而发热层3电阻的稳定性提高幅度小。实验例14中的雾化芯s
‑
14中,其通电发热老化处理的功率为7w,其循环测试的变化电阻值为0.07ω,变化电阻率为4.8%,能够明显提高雾化芯的发热层3循环电阻的稳定性。而在实验例15中的雾化芯s
‑
15中,通电发热老化处理的功率增加至9w,其循环测试的变化电阻值为0.41ω,变化电阻率为27.7%,雾化芯的发热层3循环电阻的稳定性反而出现下降。这是由于通电发热老化处理的功率过高,发热层3的发热量越大,过大的发热量会破坏发热层3的微观结构,从而降低发热层3电阻的稳定性。
[0163]
以上所述仅为本发明的较佳实施例而已,并不用以限制本发明,凡在本发明的精神和原则之内所作的任何修改、等同替换和改进等,均应包含在本发明的保护范围之内。