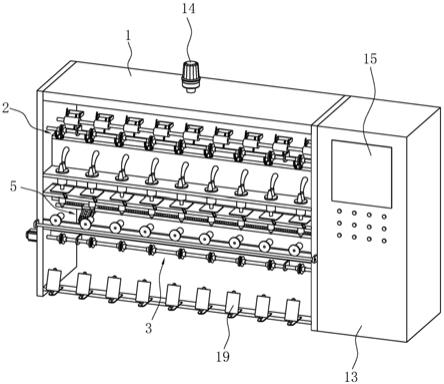
1.本技术涉及织造设备的领域,尤其是涉及一种磨毛机的断纱检测系统。
背景技术:
2.磨毛机是纺织业进行磨毛工艺时所使用的设备,用于摩擦纱线表面,使纱线表面形成一层短绒毛层。
3.进行纱线的磨毛过程中,由于一个车间内设置有数十甚至数百台磨毛机,每台磨毛机上都会对大量的纱线进行磨毛。会专门安排巡检人员对车间的磨毛机进行断纱巡检。当磨毛机出现断纱的情况时,巡检人员发现后,重新进行纱线的穿设,使纱线重新投入磨毛生产中。
4.由于同时进行磨毛的纱线数量庞大,人工巡检过程花费时间很长,且巡检的同时需要保持精神高度集中,人工成本非常高。
技术实现要素:
5.为了方便对磨毛机进行断纱检测,本技术提供一种磨毛机的断纱检测系统。
6.本技术提供一种磨毛机的断纱检测系统,采用如下的技术方案:一种磨毛机的断纱检测系统,包括机架,所述机架的底端设有间隔设置多个纱筒,所述机架的顶端设有安装板,所述安装板对应纱筒间隔设置有多块,每块所述安装板上均设有用于检测断纱的检测组件,所述机架的底端设有超喂组件,所述纱筒与超喂组件之间设有安装架,所述安装架上设有剪断组件。
7.通过采用上述技术方案,检测组件对磨毛机上的纱线进行检测,当出现断纱时,进行报警,方便巡检人员能够快速了解到磨毛机上是否存在断纱,省去人工集中精神对磨毛机上每根纱线进行检测的过程,方便对断纱进行检测。超喂组件对纱筒的纱线进行拉扯,减少出现纱线输送不平滑导致的断纱的情况,减少断纱的情况出现。出现断纱的情况后,纱线在重力的作用下,存在缠绕在超喂组件或磨毛机内输送结构上的情况,剪断组件将纱线剪断,减少纱线的缠绕,减少纱线的损失。
8.可选的,所述检测组件包括安装套、滚轮和开关件,所述滚轮设置在安装套一端,所述开关件设置在安装套内,所述开关件与滚轮连接,所述安装套设置在安装板上,所述安装套的侧壁上设有警示灯,所述警示灯与开关件电连接。
9.通过采用上述技术方案,纱线正常输送时,纱线带动滚轮转动,警示灯保持熄灭。当出现断纱的情况时,纱线无法带动滚轮转动,通过滚轮的转动进行磨毛机断纱的检测。开关件运转促使警示灯运转,利用警示灯光提醒巡检人员磨毛机存在断纱情况。
10.可选的,每块所述安装板上均开设有调节孔,每个安装套朝向安装板的一面上设有连接杆,所述连接杆贯穿调节孔,所述连接杆上螺纹连接有锁紧螺母。
11.通过采用上述技术方案,利用调节孔对安装套在安装板上位置进行调节,方便保持纱线与滚轮的贴合,保证纱线能够顺利带动滚轮转动,减少出现误报的情况。
12.可选的,所述机架一端设有控制主机,所述控制主机上设有显示器,每个所述警示灯均与所述控制主机电连接。
13.通过采用上述技术方案,控制主机将磨毛机的运行情况反映在显示器上,巡检人员通过显示器上显示的信息能够快速了解到每根纱线的磨毛情况。
14.可选的,所述机架上设有提示灯,所述提示灯与所述控制主机电连接。
15.通过采用上述技术方案,控制主机接收到警示灯亮起的开关信息后,向提示灯发送打开的控制命令,提示灯亮起,方便巡检人员快速定位存在断纱的磨毛机。
16.可选的,还包括服务器和若干个移动端,若干个所述移动端与服务器通信连接,所述服务器与控制主机通信连接。
17.通过采用上述技术方案,控制主机将磨毛机的运行情况发送至服务器内,巡检人员能够通过在移动端调取存储在服务器内的数据信息,方便地了解到磨毛机的断纱情况。
18.可选的,所述超喂组件包括传动轴和多个超喂罗拉,所述传动轴的两端分别设置在机架两端,多个所述超喂罗拉均设置在传动轴上,所述超喂罗拉与所述纱筒一一对应设置,所述机架的侧壁上设有用于驱动传动轴转动的第一驱动电机。
19.通过采用上述技术方案,超喂罗拉拉动纱线向磨毛机内输送,通过改变对纱线的张拉方式,减少出现纱线由于张紧力过大导致的断纱。
20.可选的,所述超喂罗拉包括套筒、多块挡板和多个从动轮,多块所述挡板间隔设置在套筒上,所述从动轮设置在相邻挡板之间,多个所述从动轮分两组沿套筒圆周方向间隔排布在套筒上,两组所述从动轮间隔交错排布在套筒两端。
21.通过采用上述技术方案,当纱线的张紧力较小时,超喂罗拉转动时,从动轮与纱线贴合较松,超喂罗拉与纱线能够保持相对运动的状态,超喂罗拉转动不影响纱线的输送。当纱线由于输送不平滑导致张紧力增大时,纱线与滚轮的表面贴合更紧密,从动轮拉扯纱线,超喂罗拉能够带动纱线进行输送。
22.可选的,所述剪断组件包括夹指气缸和刀片,所述刀片设置在夹指气缸的滑块上,所述安装架上设有推拉气缸,所述夹指气缸设置在推拉气缸的活塞杆上。
23.通过采用上述技术方案,夹指气缸的滑块相互靠近带动刀片相互靠近,将纱线剪断。推拉气缸调整刀片的位置,使刀片从纱线的输送路径上脱离,避免刀片将纱线割断的情况出现。
24.可选的,所述机架内设有导向杆,所述导向杆贯穿安装架,所述机架内设有与导向杆平行的传动丝杠,所述安装架螺纹连接在传动丝杠上,所述机架的侧壁上设有用于驱动传动丝杠的第二驱动电机,所述安装架上设有位置传感器。
25.通过采用上述技术方案,通过对安装架在机架内位置的调节,使刀片在不同的纱线之间移动,方便对同一磨毛机上的多根纱线剪断。
26.综上所述,本技术包括以下至少一种有益技术效果:1. 检测组件对磨毛机上的纱线进行检测,当出现断纱时,进行报警,方便巡检人员能够快速了解到磨毛机上是否存在断纱,省去人工集中精神对磨毛机上每根纱线进行检测的过程,方便对断纱进行检测;2.设置控制主机和提示灯,对出现断纱的磨毛机进行提示,方便巡检人员快速了解磨毛机是否存在断纱情况。
附图说明
27.图1是本技术实施例的整体结构示意图。
28.图2是体现超喂组件结构的示意图。
29.图3是体现检测组件结构的爆炸图。
30.图4是体现超喂罗拉结构的示意图。
31.图5是体现剪断组件结构的示意图。
32.图6是体现检测系统的框图。
33.附图标记说明:1、机架;2、检测组件;21、安装套;22、滚轮;23、开关件;231、磁块;232、控制器;233、霍尔元件;24、警示灯;25、连接杆;26、锁紧螺母;3、超喂组件;31、传动轴;32、第一驱动电机;4、超喂罗拉;41、套筒;42、挡板;43、从动轮;5、剪断组件;51、夹指气缸;52、刀片;6、安装板;7、安装架;8、传动丝杠;9、导向杆;10、位置传感器;11、推拉气缸;12、第二驱动电机;13、控制主机;14、提示灯;15、显示器;16、服务器;17、移动端;18、调节孔;19、纱筒。
具体实施方式
34.以下结合附图1-6对本技术作进一步详细说明。
35.本技术实施例公开一种磨毛机的断纱检测系统。参照图1和图2,磨毛机的断纱检测系统包括机架1,机架1的底端间隔设置有多个纱筒19,机架1的顶端间隔设置有多块安装板6,每块安装板6上均设有用于检测断纱的检测组件2。
36.参照图2和图3,检测组件2包括安装套21、滚轮22和开关件23,安装套21设置在安装板6上,开关件23设置在安装套21内,滚轮22设置在安装套21远离安装板6的一端。开关件23包括磁块231、控制器232和霍尔元件233,磁块231偏心固定在滚轮朝向控制器232的一面上,霍尔元件233偏心设置在控制器232朝向磁块231的一面上,控制器232与警示灯24电连接,控制器232在本实施例中具体为单片机,在其他实施例中也可以为plc控制器等。
37.参照图3,滚轮22带动磁块231快速转动,磁块231每次接近霍尔元件233时,增大通过霍尔元件233的磁通量,触发霍尔元件233向控制器232发送脉冲,控制器232检测到霍尔元件233发送的脉冲后进行记录,检测最近两次脉冲之间的时间间隔t1,并将该时间间隔t1与工作人员预设的时间间隔阈值t0进行比对。若时间间隔t1小于时间间隔阈值t0,则说明磨毛机正常运转,控制器232控制电路保持断开状态;若时间间隔t1大于或等于时间间隔阈值t0,则说明磨毛机出现断纱的情况,此时,控制器232运作,控制电路导通,警示灯24亮起。
38.巡检人员通过观察警示灯24是否亮起就能够快速判断纱线是否断裂。省去巡检人员人工对每一条纱线进行检查的过程,方便巡检人员快速了解到磨毛机的断纱情况。
39.参照图2和图3,每块安装板6上均开设有弧形的调节孔18,安装套21朝向安装板6的一面上固定有连接杆25,连接杆25上螺纹连接有锁紧螺母26。旋松锁紧螺母26,方便调整安装套21在安装板6上的位置,进而对滚轮22的位置进行调节,完成调节后,旋紧锁紧螺母26,将安装套21固定在安装板6上,方便保持纱线与滚轮22表面的贴合,提升对纱线的检测精度。
40.纱线输送时由于摩擦力等原因而停滞,输送不平滑时,此时磨毛机对纱线的张紧力急剧增大,对纱线磨毛时,容易出现纱线断裂的情况。
41.参照图2和图4,机架1的顶端和底端各设有一组超喂组件3,用于缓解上述的情况。超喂组件3包括传动轴31和多个超喂罗拉4,传动轴31的两端均设置在机架1两端的内侧壁上,超喂罗拉4同轴间隔排布在传动轴31上,超喂罗拉4与纱筒19一一对应设置,机架1的侧壁上固定有第一驱动电机32,第一驱动电机32的输出轴与传动轴31同轴连接。驱动电机运转带动传动轴31转动,传动轴31带动超喂罗拉4转动,超喂罗拉4拉拽纱线,使纱线从纱筒19上脱出,进行纱线的输送,缓解纱线难以从纱筒19上脱出导致的纱线断裂的问题。
42.参照图4,超喂罗拉4包括套筒41、两块挡板42和多个从动轮43,套筒41套设在传动轴31上,挡板42沿套筒41轴线方向竖直间隔排布,多个从动轮43均设置在两块挡板42之间,从动轮43设置在套筒41上,多个从动轮43沿套筒41的圆周方向间隔排布,多个从动轮43分为两组间隔交错排布在套筒41轴线方向两端。纱线从纱筒19上脱出后,缠绕在滚轮22上,挡板42使纱线保持在滚轮22上的稳定。正常进行纱线的输送时,纱线的张紧力较小,套筒41转动时仅能够使滚轮22与纱线发生相对摩擦,使滚轮22转动,并不影响纱线的正常输送。当纱线停滞在纱筒19上无法继续输送时,此时纱线的张紧力增大,纱线与滚轮22贴合更紧密,纱线与滚轮22之间的摩擦增大。套筒41转动带动滚轮22转动,此时滚轮22在摩擦力的作用下对纱线进行拉扯,拉动纱线从纱筒19上脱出,继续进行纱线的输送。
43.一旦出现纱线断裂,断裂的纱线失去磨毛机的牵引而向下坠落,存在纱线坠落在超喂罗拉4上的情况,此时超喂罗拉4在第一驱动电机32的带动下将纱线卷绕,导致大量的纱线缠绕在超喂罗拉4上,后期清理非常繁琐。
44.参照图2和图5,纱筒19与传动轴31之间设有安装架7,安装架7上固定有推拉气缸11,推拉气缸11上设有用于将纱线剪断的剪断组件5。在检测到纱线断裂后,推拉气缸11推动剪断组件5向纱线移动,剪断组件5将超喂罗拉4与纱筒19之间的纱线剪断,减少缠绕在超喂罗拉4上的纱线,减少纱线损失。完成纱线的剪断后,推拉气缸11的活塞杆缩回,剪断组件5离开纱线的输送路径,方便剪断组件5在纱线间移动。
45.参照图5,剪断组件5包括夹指气缸51和两块刀片52,刀片52设置在夹指气缸51的滑块上,夹指气缸51固定在推顶气缸的活塞杆上。需要剪断纱线时,夹指气缸51运转带动刀片52相互靠近,将纱线剪断。将纱线剪断后,夹指气缸51的滑块带动刀片52相互远离,方便进行下一次裁剪作业。
46.参照图2,机架1内壁上设有导向杆9,导向杆9贯穿安装架7,机架1内设有与导向杆9平行的传动丝杠8,安装架7螺纹连接在传动丝杠8上。机架1的侧壁上固定有第二驱动电机12,第二驱动电机12的输出轴与传动轴31同轴固定连接。第二驱动电机12运转带动安装架7沿导向杆9在线筒之间移动,方便对多根纱线进行剪断。
47.参照图1和图2,机架1一端设有控制主机13,控制主机13上设有显示器15,控制主机13的显示器15上显示有磨毛机上每根纱线的输送情况。安装架7上固定有位置传感器10,传感器与控制主机13电连接,控制主机13与第二驱动电机12电连接,每个警示灯24均与控制主机13电连接。
48.参照图1和图2,出现断纱的情况后,开关件23控制警示灯24亮起,警示灯24将开关信号发送给控制主机13,控制主机13接收到警示灯24发送的开关信号后,记录打开的警示灯24的位置信息,并将该信息反映在预设的显示器15上,供巡检人员查看,同时生成运转信息并将运转信息发送给第二驱动电机12。第二驱动电机12接收到运转信息后,自动运转带
动安装架7在纱线间移动,位置传感器10不断将安装架7的位置信息向控制主机13发送。当位置传感器10发送的位置信息与记录的警示灯24的位置信息相同时,控制主机13向第二驱动电机12发送停止命令,并向推顶气缸发送运转命令,推顶气缸的活塞杆伸出。控制主机13再向夹指气缸51发送运转命令,夹指气缸51将纱线剪断。控制主机13再向夹指气缸51和推顶气缸发送复位命令,夹指气缸51和推顶气缸接收到复位命令后自动复位。
49.参照图1,机架1的顶面上固定有提示灯14,提示灯14与控制主机13电连接。当检测到出现断纱的情况后,警示灯24亮起并将开关信息发送至控制主机13,控制主机13接收到警示灯24的亮起的开关信息后,控制提示灯14亮起。通过机架1顶端的警示灯24,巡检人员能够快速了解到磨毛机是否存在断纱的情况,并结合亮起的警示灯24,快速定位到断纱的磨毛机,大大提升磨毛机的断纱检测效率。
50.参照图6,磨毛机的断纱检测系统还包括服务器16和若干移动端17,服务器16和控制主机13通信连接,移动端17与服务器16通信连接,本实施例中移动端17优选为手机。控制主机13接收到警示灯24的开关信息后,读取预设的计时器上的时间信息,并将开关信息和时间信息一同上传至服务器16,并存储在服务器16内,巡检人员能够通过手机调取服务器16内的数据信息,方便巡检人员快速了解断纱情况和断纱时间。
51.本技术实施例的实施原理为:利用开关件23对磨毛机是否断纱进行检测,当出现断纱的情况时,安装套21上警示灯24亮起,控制主机13将机架1顶端的提示灯14打开并将信息上传至服务器16内。第二驱动电机12运转带动安装架7向断纱的纱筒19移动,将纱筒19与超喂罗拉4之间的纱线剪断。
52.当出现纱线难以平滑地进行输送时,超喂罗拉4在第一驱动电机32的带动下,拉拽纱线,拉动纱线进行稳定的输送,减少出现纱线由于输送不平滑导致断纱的情况。
53.巡检人员能够观察机架1顶端的提示灯14以及警示灯24快速定位断纱的磨毛机,对磨毛机的断纱检测更加方便。巡检人员还能够通过调取服务器16内的数据信息,了解磨毛机的断纱情况和断纱时间,对大量磨毛机进行实施监测。
54.以上均为本技术的较佳实施例,并非依此限制本技术的保护范围,故:凡依本技术的结构、形状、原理所做的等效变化,均应涵盖于本技术的保护范围之内。