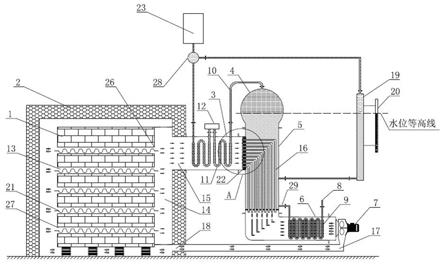
1.本实用新型涉及一种过热蒸汽换热技术领域,具体地说是一种通过电蓄热进行热交换的过热蒸汽换热系统。
背景技术:
2.众所周知,在能源领域的应用上,热能是最主要的形式之一。其中蒸汽又是工业用热能形式里占主要的特出理形态,蒸汽主要分为饱和蒸汽和过热蒸汽,同时又存在着不同的温度和压力。目前,蒸汽的获取方式通常还是以传统的燃煤锅炉为主,也有少量的采取燃气等热源形式,但是随着国家2030年实现碳达峰、2060年实现碳中和的环保目标,以及化石能源的不可再生性,因此,燃煤、燃气等采取化石能源的热源产生方式将逐步减少,但是随着工业的发展,工业蒸汽的需求反而会逐步加大,与逐步减少的以化石能源为主的热源市场出现供需矛盾的现象。随着国家环保目标的实现,电能将是未来的主要能源形式,风电、光电、核电等清洁可再生能源将在电能生产中占比逐渐加大,成为主要发电方式。利用电能生产蒸汽,既能满足工业及民用的生产生活,又可以实现环保目标,以电制热也将成为一种趋势。如何既能生产稳定的蒸汽又能降低生产成本,研制一种过热蒸汽装置系统成为一种必须。
技术实现要素:
3.本实用新型的目的是提供一种通过电蓄热进行热交换的过热蒸汽换热系统。
4.本实用新型目的是通过如下技术方案来实现的:一种过热蒸汽换热系统,它包括有保温壳体,在保温壳体内设置有带绝缘支撑结构的固体蓄热体,在固体蓄热体内阵列分布有蓄热体风道,在蓄热体风道内设置有高压电发热体,其特征在于:所述保温壳体的外壁上设置有高温出风通道口和低温回风通道口,蓄热体风道出口通过高温封闭区与所对应的高温出风通道口连通,该高温出风通道口依次连接有过热蒸气换热器、蒸发器中的放热管组、预热换热器、循环风机,该循环风机出端口通过回风道连接低温回风通道口后,再与保温壳体内的蓄热体风道进口相连通构成热风循环回路;在预热换热器内接有蛇形结构的预热管组,该预热管组低温端连接有补水管,高温端与蒸发器输入口相连通,在蒸发器顶部的球冠形汽包处设置有饱和蒸气输出管,该饱和蒸气输出管与设置在过热蒸气换热器内的过热管组相连通,该过热管组的出口通过过热蒸汽输出管道与过热蒸气用户相连通;在过热管组上还串联有过热蒸汽减温器,该过热蒸汽减温器设置在过热蒸气换热器的外侧;在过热蒸汽输出管道上还设置有水位系统。
5.本实用新型根据用户过热蒸气的需要量,则设置在保温壳体侧壁上的高温出风通道口和低温回风通道口为一条、二条或二条以上的多条所组成。
6.本实用新型所述的预热管组是预热管的阵列式排列结构,由耐热无缝钢管翅片管焊接而成。
7.本实用新型所述的过热管组是过热管的阵列式排列结构,由耐热无缝钢管翅片管
焊接而成。
8.本实用新型所述的水位系统是连通管的构造结构,包括水位柱、水位计及相联通的管道;水位柱上端与过热蒸汽输出管道联通,下端与蒸发器外壳下端联通;水位计安装在水位柱上,水位计半量程读数刻度高度安装位置,与水位柱内工作水平面高度位置同高度。
9.本实用新型所述的安装放热管组的管板外平面设置有绝热层,所述的绝热层是由能耐受大于1000℃工作的硅酸铝板、毡、棉类隔热材料制成。
10.本实用新型所述放热管组的进出两个端口设置有喇叭口形扩风口,该喇叭口是与放热管组两端口连接的用耐热金属板制成的圆台管状体。
11.本实用新型所述的过热蒸汽减温器是能测量过热蒸汽参数,并能控制适量的冷却水以雾状喷入过热蒸汽管道中,使过热蒸汽温度降低的装置。
12.本实用新型所述的高温封闭区是在蓄热体风道出口与高温出风通道口之间建立的高温空间,是用耐热绝缘的云母板围成的腔体。
13.本实用新型的优点是:热源采用电能制热,区别于传统化石能源,利于环保;系统结构简单紧凑,区别于传统锅炉需要的大量附属部件,本系统外围部件少,便利于采用高电压工作,杜绝了电气安全隐患;系统过热器、蒸发器、预热器串联在一起,由一台循环风机动力驱动,调节过热器、蒸发器、预热器各自的受热面、系统稳定,便于制取满足用户需求的稳定的过热蒸汽;蒸发器区别于传统的管程水壳程风的结构,采用管程风壳程水的新式结构,避免了水程因结垢造成水堵爆管的故障现象发生;本系统结构简单,现场整体吊装施工,施工工艺简单,这样便于出厂前做整部件的压力检测,适合生产10mpa、550℃的过热蒸汽。
附图说明
14.图1为本实用新型一种过热蒸汽装置系统的结构示意简图;
15.图2 为图1中的a向放大结构示意简图。
16.附图中主要部件说明如下:1、固体蓄热体,2、保温壳体,3、热过蒸汽换热器,4、球冠形汽包,5、蒸发器,6、预热换热器,7、循环风机,8、补水管,9、预热管组,10、饱和蒸汽输出管,11、过热管组,12、过热蒸汽减温器,13、蓄热体风道,14、高温封闭区,15、高温出风通道口,16、放热管组,17、回风道,18、低温回风通道口,19、水位柱,20、水位计,21、高压电发热体,22、绝热层,23、过热蒸汽用户,24喇叭口,25管板,26、蓄热体风道出口,27、蓄热体风道进口,28、过热蒸汽输出管道,29、蒸发器输入口。
17.本实用新型附图仅仅是发明的一个实施案例的示意图,对于本领域普通技术人员来讲,在不付出创造性劳动的前提下,可根据这一附图获得其他的附图。
具体实施方式
18.下面结合附图对本实用新型具体实施方式作详细说明, 以下说明仅作为示范和解释,并不对本实用新型作任何形式上的限制。
19.如图1、2所示,图中的1为固体蓄热体,2为保温壳体,在保温壳体2内设置有带绝缘支撑结构的固体蓄热体1,在固体蓄热体内阵列分布有蓄热体风道13,在蓄热体风道13内设置有高压电发热体21;所述保温壳体2的外壁上设置有高温出风通道口15和低温回风通道口18,蓄热体风道出口13通过高温封闭区与所对应的高温出风通道口15连通,该高温出风
通道口15依次连接有过热蒸气换热器3、蒸发器5内的放热管组16、预热换热器6、循环风机7,该循环风机7出端口通过回风道17连接低温回风通道口18后,再与保温壳体内的蓄热体风道进口相连通构成热风循环回路;在预热换热器6内接有蛇形结构的预热管组9,该预热管组9低温端连接有补水管8,高温端与蒸发器5的蒸发器输入口29相连通,在蒸发器5顶部的球冠形汽包4处设置有饱和蒸气输出管10,该饱和蒸气输出管10与设置在过热蒸气换热器3内的过热管组11相连通,该过热管组11的出口通过过热蒸汽输出管道28与过热蒸气用户23相连通;在过热管组11上还串联有过热蒸汽减温器12,该过热蒸汽减温器12设置在过热蒸气换热器3的外侧;在过热蒸汽输出管道28上还设置有水位系统19。
20.在保温壳体2内部建设有固体蓄热体1,固体蓄热体1中阵列分布水平蓄热体风道13,既是热能载体空气的循环通道,又是安装连接高压电源发热的高压电发热体21的安装通道;过热蒸汽换热器3内部分布有过热管组11,连接有可以调节过热蒸汽温度的过热蒸汽减温器12,蒸发器5内部分布有放热管组16,预热换热器6内部分布有预热管组9,循环风机7与预热换热器6相连,并通过回风道17与低温回风通道18连接。低温空气流通蓄热体风道13形成高温热空气汇集到高温封闭区14,由各个高温进风通道口15依次流经过热蒸汽换热器3、蒸发器5内部的放热管组16、预热换热器6,与其各自内部的饱和蒸汽、高温水、低温水进行热能交换,最后在循环风机7的动力驱动下,经回风道17、低温回风通道18回到保温壳体2内部,再次经过固体蓄热体风道13加温、形成高温热空气,汇集到高温封闭区14,重复上述循环路径。低温水从补水管8,依次流经预热换热器6内,通过预热管组9与热空气换热形成高温水,进入蒸发器5内,通过放热管组16吸收的热能在球冠形汽包4中形成饱和蒸气,由饱和蒸汽输出管10输入到过热蒸汽换热器3内,通过过热管组11再次吸收高温热能形成的过热蒸汽并入过热蒸汽输出管道28后输送到热用户23使用。过热蒸汽输出管道28连接有多个过热蒸汽换热器3,过热蒸汽输出管道28上还连接一个或多个水位系统。过热蒸汽换热器3连接的过热蒸汽减温器12,可以调节过热蒸汽温度。
21.由于需要产生的是过热蒸汽,因此热源保温结构内部的空气温度会达到700℃左右。在极端条件下,经过过热器辐射到蒸发器的空气温度与蓄热体内的温度几乎一致,高温会对焊接放热管组16的管板25产生破坏力,因此,如图2中22所示,在管板外部设计有一层绝热层,可以有效降低高温空气对管板25的热辐射,提高蒸发器5的使用寿命。
22.蒸发器5分布有放热管组16,高温风经过过热蒸汽换热器3进入放热管组16内,在放热管组16每只放热管两端口设置有喇叭口24,用于消除气体流动的湍流等不利现象。
23.本系统中设置有水位系统,完成本装置的集中补水控制采样过程。水位系统连接成连通管结构,以连通管内各水平面等高传递的原理为依据设置多蒸发器5和多水位柱19的组合结构,用水位计20测量水位柱19的水平面标定球冠形汽包4的水位。
24.高温封闭区14是在蓄热体风道出口26与高温出风通道口15之间建立的高温空间,是用耐受1000℃热风和能耐受110kv工作电压绝缘要求的云母板围成的腔体。
25.预热管组9是安装在预热换热器6中,采用耐热钢无缝管制成的翅片热管,经水平蛇形多组排列构成、焊接而成,高温端为迎风面。
26.过热管组11是安装在过热蒸汽换热器3中,采用耐热钢无缝管制成的翅片热管,经水平蛇形多组排列构成、焊接而成,高温端为迎风面。
27.根据过热蒸汽的需求量,本过热蒸汽换热系统可以采取多组并联使用,来满足热
用户的需求。
28.最后所应说明的是,以上具体实施方式仅用以说明本实用新型的技术方案而非限制,尽管参照实例对本实用新型进行了详细说明,本领域的普通技术人员应当理解,可以对本实用新型的技术方案进行修改或者等同替换,而不脱离本实用新型技术方案的精神和范围,其均应涵盖在本实用新型的权利要求范围中。